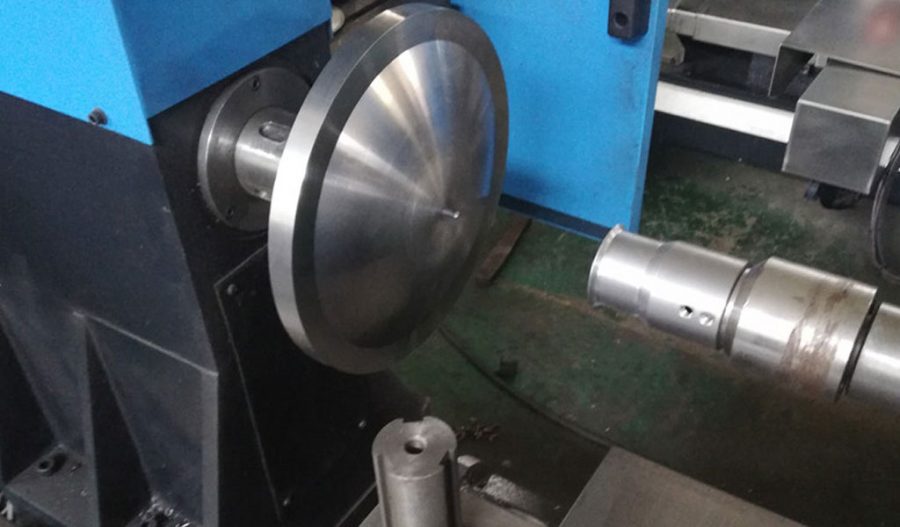
Deep spinning of sheet metals is a highly specialized metal-forming process rooted in the broader domain of spin forming or metal spinning, a technique that has been employed for centuries to shape ductile metals into axially symmetric components. This process, often conducted on a lathe or a dedicated spinning machine, involves the incremental deformation of a flat metal sheet or blank into a desired three-dimensional geometry, typically using a combination of rotational motion and controlled pressure from a forming tool. Unlike conventional spinning, which is generally limited to shallow or moderately deep parts, deep spinning refers to the production of components with significant depth-to-diameter ratios, often exceeding 1:1, where the final shape requires substantial material flow and deformation. This article provides an exhaustive exploration of deep spinning of sheet metals, delving into its historical evolution, fundamental principles, material considerations, process mechanics, tooling, applications, advantages, limitations, and comparative analyses with other forming techniques, supported by detailed tables to elucidate key parameters.
The origins of metal spinning can be traced back to ancient civilizations, with evidence of rudimentary spinning techniques found in Egyptian and Chinese artifacts dating as early as 1400 BCE. Artisans of these eras used manual tools to shape metals like copper and bronze into vessels, decorative items, and utilitarian objects, relying on the inherent ductility of these materials. The industrial revolution of the 18th and 19th centuries marked a pivotal turning point, as mechanized lathes and the advent of steam power enabled more precise and repeatable forming operations. By the 20th century, the development of modern alloys and advanced machinery paved the way for deep spinning, a process that emerged as a response to the growing demand for complex, lightweight, and high-strength components in industries such as aerospace, automotive, and energy. Today, deep spinning stands as a cornerstone of advanced manufacturing, blending traditional craftsmanship with cutting-edge engineering principles.
At its core, deep spinning operates on the principle of plastic deformation, wherein a flat metal blank, typically circular, is clamped against a rotating mandrel—a pre-shaped form that defines the internal geometry of the final part. The mandrel spins at a controlled speed, often ranging from 100 to 1,000 revolutions per minute (RPM), depending on the material, thickness, and desired precision. A forming tool, which may be a roller, spoon-shaped implement, or a CNC-controlled stylus, applies localized pressure to the blank, gradually forcing it to conform to the mandrel’s contours. In deep spinning, this process occurs in multiple passes or stages, as the depth of the part increases incrementally with each cycle. The tool’s motion may be manual, as in traditional spinning, or automated via computer numerical control (CNC) systems, which offer superior repeatability and the ability to execute complex tool paths for intricate geometries.
The mechanics of deep spinning are governed by several interdependent variables, including material properties, blank thickness, mandrel design, tool geometry, spinning speed, feed rate, and lubrication. Ductility—the ability of a metal to undergo plastic deformation without fracturing—is the most critical material property for successful deep spinning. Common materials include aluminum alloys (e.g., 6061, 1100), stainless steels (e.g., 304, 316), titanium alloys (e.g., Ti-6Al-4V), and copper, each selected based on the application’s requirements for strength, corrosion resistance, and formability. Aluminum, for instance, is favored in aerospace applications due to its low density and excellent workability, while stainless steel is prevalent in chemical processing equipment for its durability and resistance to harsh environments. The blank thickness, typically ranging from 0.5 mm to 6 mm, influences the force required and the number of passes needed, with thinner sheets requiring less force but greater care to avoid wrinkling or tearing.
The deformation process in deep spinning can be broadly categorized into two modes: shear spinning and flow forming. Shear spinning, sometimes referred to as power spinning, involves a reduction in blank thickness as the material is stretched and thinned over the mandrel, maintaining a constant volume. This mode is less common in deep spinning due to its limitation in achieving significant depth without excessive thinning. Flow forming, by contrast, dominates deep spinning applications, as it allows the material to flow plastically along the mandrel without substantial thickness reduction, preserving structural integrity. The flow forming mode relies heavily on compressive and tensile stresses induced by the forming tool, which must be carefully balanced to prevent defects such as cracking, buckling, or springback—the elastic recovery of the material after deformation.
Tooling plays a pivotal role in deep spinning, with the mandrel and forming tool being the primary components. The mandrel, typically machined from hardened steel or aluminum, must withstand the high forces and frictional wear encountered during spinning. Its surface finish, often polished to a mirror-like quality, directly affects the final part’s surface quality, as imperfections can transfer to the workpiece. Mandrels may be solid for smaller parts or segmented for larger, deeper components, allowing disassembly and part removal. The forming tool, meanwhile, varies in design depending on the process stage. Early passes often employ broad, rounded rollers to distribute force evenly and initiate deformation, while finishing passes may use pointed tools for precision shaping. Tool materials range from hardened steel to ceramics or carbides, selected for their wear resistance and thermal stability, especially when spinning high-strength alloys like titanium.
Lubrication is another critical factor, reducing friction between the blank, mandrel, and tool, thereby minimizing heat buildup and tool wear. Common lubricants include mineral oils, synthetic emulsions, and solid lubricants like graphite or molybdenum disulfide, with the choice depending on the material and spinning conditions. For instance, aluminum benefits from oil-based lubricants to prevent galling—a form of adhesive wear—while titanium may require high-temperature lubricants to accommodate its elevated forming temperatures, often exceeding 300°C in hot spinning applications.
The deep spinning process unfolds in a series of meticulously orchestrated steps. First, the blank is prepared, typically by cutting a circular disc from a sheet using shearing, laser cutting, or waterjet methods, ensuring dimensional accuracy and a burr-free edge. The blank is then centered and clamped onto the mandrel, often with a tailstock or follower block to maintain alignment during rotation. Initial spinning begins with coarse deformation, where the tool presses the blank against the mandrel’s base, gradually working outward and downward in subsequent passes. For deep parts, intermediate annealing—heat treatment to relieve stresses and restore ductility—may be required between stages, particularly for strain-hardening materials like stainless steel. Final passes refine the shape, achieving tight tolerances (e.g., ±0.1 mm) and a smooth surface finish, often eliminating the need for secondary machining.
One of the defining characteristics of deep spinning is its ability to produce seamless, monolithic components with exceptional structural integrity. This is particularly advantageous in applications requiring pressure vessels, rocket nose cones, or automotive wheel rims, where welds or joints could introduce weak points. The process also excels in material efficiency, as it generates minimal waste compared to subtractive methods like milling. However, deep spinning is not without challenges. The high degree of deformation can lead to work hardening, where the material becomes progressively stiffer and less ductile, necessitating careful process planning. Wrinkling, a common defect, occurs when compressive stresses cause the blank to buckle, particularly in thin-walled sections, while tearing results from excessive tensile stresses exceeding the material’s ultimate strength.
To mitigate these issues, modern deep spinning often incorporates advanced technologies. CNC spinning machines, equipped with real-time force and position sensors, enable precise control over tool paths and deformation rates, reducing defects and improving consistency. Finite element analysis (FEA) simulations are increasingly used to model material flow, predict stress distributions, and optimize process parameters before physical trials, saving time and resources. Hot spinning, where the blank is heated to enhance ductility, is another innovation, particularly for high-strength alloys. Temperatures typically range from 200°C to 600°C, depending on the material, with induction heating or flame torches providing localized or uniform heat.
The applications of deep spinning span a wide range of industries, reflecting its versatility and adaptability. In aerospace, it is used to fabricate components such as missile casings, satellite dishes, and jet engine housings, where lightweight, high-strength parts are paramount. The automotive sector employs deep spinning for manufacturing wheel rims, exhaust cones, and fuel tank components, leveraging its ability to produce complex shapes from lightweight materials like aluminum. In the energy sector, deep spinning produces turbine housings, pressure vessels, and nuclear reactor components, often from stainless steel or titanium for their corrosion resistance and durability. Consumer goods, such as cookware and lighting reflectors, also benefit from the process, where aesthetic appeal and cost-effectiveness are key drivers.
Comparatively, deep spinning offers distinct advantages over alternative forming methods like deep drawing, forging, and hydroforming. Deep drawing, a press-based process, excels in high-volume production of shallow to moderately deep parts but struggles with extreme depth-to-diameter ratios due to punch and die constraints. Forging, while ideal for high-strength, thick-walled components, lacks the flexibility to produce thin-walled, seamless shapes. Hydroforming, which uses fluid pressure to shape metal, offers excellent precision for complex geometries but requires expensive tooling and is less suited to small-batch production. Deep spinning, by contrast, balances cost, flexibility, and capability, making it ideal for low- to medium-volume runs of deep, symmetric parts.
To illustrate these differences, Table 1 provides a detailed comparison of deep spinning with deep drawing, forging, and hydroforming across key parameters:
Parameter | Deep Spinning | Deep Drawing | Forging | Hydroforming |
---|---|---|---|---|
Depth-to-Diameter Ratio | High (>1:1) | Moderate (≤1:1) | Low (<0.5:1) | High (>1:1) |
Material Thickness | 0.5–6 mm | 0.2–3 mm | 5–50 mm | 0.5–5 mm |
Tooling Cost | Moderate (mandrel + tool) | High (punch + die) | High (dies) | Very High (dies + fluid system) |
Production Volume | Low to Medium | High | Medium to High | Low to Medium |
Material Waste | Low | Moderate (trimming) | High (flash) | Low |
Seamlessness | Yes | No (if multi-piece) | Yes | Yes |
Surface Finish | Good (post-finishing optional) | Excellent | Fair (requires machining) | Excellent |
Typical Materials | Al, SS, Ti, Cu | Al, SS, mild steel | Steel, Al, Ti | Al, SS, Ti |
Cycle Time | Moderate (multi-pass) | Fast (single stroke) | Slow (multi-step) | Moderate (pressure application) |
This table underscores deep spinning’s niche as a process for deep, seamless parts with moderate tooling costs and material efficiency, though it sacrifices some speed and scalability compared to deep drawing.
Material selection further refines the process’s applicability, as shown in Table 2, which compares common metals used in deep spinning:
Material | Density (g/cm³) | Yield Strength (MPa) | Ductility (% Elongation) | Forming Temperature (°C) | Applications |
---|---|---|---|---|---|
Aluminum 6061 | 2.7 | 276 | 17 | 20–300 | Aerospace, automotive |
Stainless Steel 304 | 8.0 | 215 | 40 | 20–600 | Pressure vessels, cookware |
Titanium Ti-6Al-4V | 4.43 | 880 | 10 | 300–600 | Aerospace, medical implants |
Copper | 8.96 | 70 | 50 | 20–200 | Decorative items, electrical |
These properties dictate process adjustments, such as higher temperatures for titanium or additional annealing for stainless steel, highlighting the need for tailored approaches in deep spinning.
In practice, deep spinning’s success hinges on optimizing process parameters, a task increasingly aided by computational tools. For instance, the spinning ratio—defined as the ratio of blank diameter to final part diameter—typically ranges from 1.5:1 to 3:1 for deep parts, influencing material flow and tool force. Feed rates, expressed as millimeters per revolution (mm/rev), vary from 0.1 to 1.0 mm/rev, balancing speed and surface quality. Spindle speed, material thickness, and tool radius further interact, requiring empirical testing or simulation to refine. Table 3 summarizes typical parameter ranges:
Parameter | Range | Effect |
---|---|---|
Spinning Ratio | 1.5:1–3:1 | Higher ratios increase material flow |
Feed Rate (mm/rev) | 0.1–1.0 | Lower rates improve finish, raise time |
Spindle Speed (RPM) | 100–1,000 | Higher speeds reduce cycle time, risk heat |
Tool Radius (mm) | 5–20 | Larger radii reduce stress concentration |
The scientific underpinnings of deep spinning draw from solid mechanics, plasticity theory, and tribology. The von Mises yield criterion often models the onset of plastic deformation, while the flow rule describes material behavior under multi-axial stresses. Friction coefficients, typically 0.05–0.2 with lubrication, govern tool-workpiece interactions, influencing heat generation and wear. These principles inform process design, ensuring that stresses remain below the material’s fracture limit while achieving the desired shape.
Looking ahead, deep spinning continues to evolve with advancements in automation, materials science, and hybrid processes. The integration of robotics promises greater precision and reduced labor costs, while the development of high-entropy alloys and composites expands the material palette. Hybrid techniques, such as combining spinning with additive manufacturing, offer new possibilities for customized, multi-material components. As industries demand ever-lighter, stronger, and more complex parts, deep spinning’s role in manufacturing is poised to grow, bridging the gap between art and engineering with unparalleled finesse.
In conclusion, deep spinning of sheet metals represents a sophisticated fusion of tradition and technology, capable of producing deep, seamless components with remarkable efficiency and precision. Its reliance on material ductility, incremental deformation, and advanced tooling distinguishes it from other forming methods, offering a unique blend of flexibility and performance. Supported by rigorous scientific principles and enhanced by modern innovations, deep spinning remains a vital process in the pantheon of manufacturing techniques, with applications that continue to shape the modern world.
Maximize Tooling and CNC Metal Spinning Capabilities.
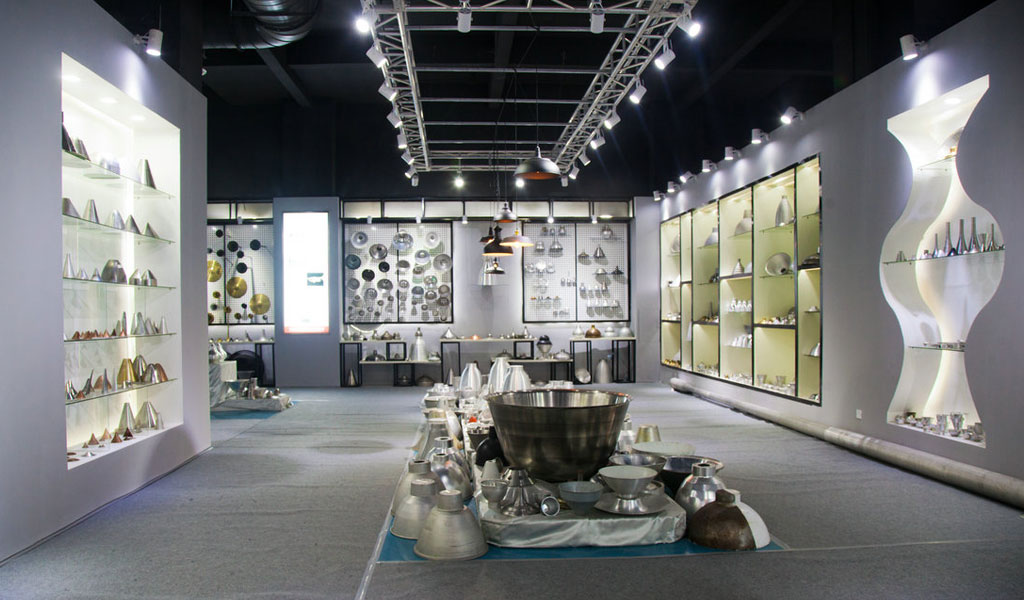
At BE-CU China Metal Spinning company, we make the most of our equipment while monitoring signs of excess wear and stress. In addition, we look into newer, modern equipment and invest in those that can support or increase our manufacturing capabilities. Our team is very mindful of our machines and tools, so we also routinely maintain them to ensure they don’t negatively impact your part’s quality and productivity.
Talk to us today about making a rapid prototype with our CNC metal spinning service. Get a direct quote by chatting with us here or request a free project review.
BE-CU China CNC Metal Spinning service include : CNC Metal Spinning,Metal Spinning Die,Laser Cutting, Tank Heads Spinning,Metal Hemispheres Spinning,Metal Cones Spinning,Metal Dish-Shaped Spinning,Metal Trumpet Spinning,Metal Venturi Spinning,Aluminum Spinning Products,Stainless Steel Spinning Products,Copper Spinning Products,Brass Spinning Products,Steel Spinning Product,Metal Spinnin LED Reflector,Metal Spinning Pressure Vessel,