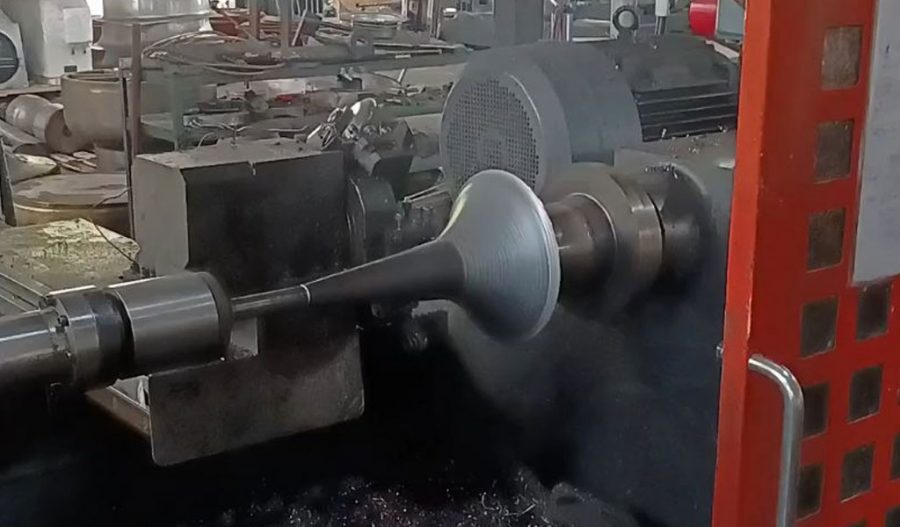
The spinning wheel, a cornerstone of textile production for centuries, has undergone significant evolution since its inception, likely in the Middle East or India around the 11th century. From its rudimentary forms to modern mechanized iterations, the spinning wheel has been pivotal in transforming raw fibers into yarn, a process fundamental to the textile industry. Among the myriad advancements in spinning technology, the development of the multi-point contact spinning wheel represents a significant leap forward, particularly in enhancing efficiency, yarn quality, and adaptability to diverse fiber types. This article delves into the design principles, mechanical intricacies, and practical applications of the multi-point contact spinning wheel in the spinning process, exploring its historical context, technical innovations, and impact on modern textile production. By examining its components, operational mechanisms, and comparative advantages, this comprehensive analysis aims to provide a thorough understanding of this specialized technology.
The multi-point contact spinning wheel is distinguished by its ability to engage the fiber at multiple points simultaneously, thereby optimizing the twisting and drafting processes. Unlike traditional spinning wheels, which typically rely on a single point of contact between the spindle or flyer and the fiber, the multi-point contact design distributes mechanical forces across several contact points, reducing stress on the fiber and improving yarn uniformity. This innovation addresses longstanding challenges in hand-spinning and early mechanized spinning, such as inconsistent yarn thickness and breakage, while also enabling higher throughput in industrial settings. The article will explore the engineering principles behind this design, its integration into various spinning systems, and its implications for both artisanal and industrial textile production.
Historical Context of Spinning Wheels
The spinning wheel’s origins are shrouded in historical ambiguity, with evidence suggesting its emergence in the Middle East by 1030 CE, as noted by historians Arnold Pacey and Irfan Habib. The earliest clear depiction, from Baghdad in 1237, illustrates a hand-driven wheel that automated the twisting process, a significant improvement over hand-spinning with a spindle. By the 12th century, the spinning wheel had reached India, with references to its use in cotton spinning appearing in texts like Abdul Malik Isami’s Futuh-us-Salatin (1350). In Europe, the spinning wheel gained prominence during the Middle Ages, replacing labor-intensive hand-spinning methods and laying the groundwork for the textile industry’s expansion.
Early spinning wheels, such as the great wheel or walking wheel, were simple devices that relied on a single point of contact between the fiber and the spindle. The operator held the fiber at an angle to the spindle, twisting it as the wheel was turned by hand or foot. These wheels were effective for producing long, soft wools but struggled with creating the smooth, strong yarns needed for weaving warp threads. The introduction of the Saxony wheel in the 16th century, with its bobbin-and-flyer mechanism and foot treadle, marked a significant advancement, freeing both hands for drafting and increasing productivity. However, these early designs still faced limitations in yarn consistency and fiber handling, particularly for finer or more delicate materials.
Transition to Mechanized Spinning
The Industrial Revolution catalyzed a seismic shift in spinning technology, with inventions like James Hargreaves’ spinning jenny (1764) and Richard Arkwright’s water frame (1769) introducing mechanized spinning. These machines, which drew inspiration from the spinning wheel’s principles, enabled continuous yarn production at unprecedented scales. The spinning mule, invented by Samuel Crompton in 1779, further refined this process by combining elements of the jenny and water frame, producing finer and stronger yarns suitable for both warp and weft. Despite these advancements, the core mechanics of spinning—drafting, twisting, and winding—remained rooted in the spinning wheel’s design.
The transition to mechanized spinning highlighted the limitations of single-point contact systems, particularly in handling high volumes of fiber or producing ultra-fine yarns. As textile demands grew, particularly for cotton and synthetic fibers, the need for more sophisticated spinning technologies became apparent. The multi-point contact spinning wheel emerged as a response to these challenges, offering a hybrid approach that combined the precision of traditional spinning with the efficiency of modern machinery.
Design Principles of Multi-Point Contact Spinning Wheels
Fundamental Mechanics
The multi-point contact spinning wheel is engineered to optimize the interaction between the fiber and the spinning mechanism, distributing mechanical forces across multiple points to enhance control and efficiency. At its core, the spinning process involves three primary actions: drafting (attenuating the fiber to the desired thickness), twisting (imparting strength and cohesion to the fiber), and winding (collecting the spun yarn onto a bobbin or spindle). Traditional spinning wheels accomplish these tasks sequentially, with a single point of contact—typically the spindle or flyer—serving as the primary interface. In contrast, the multi-point contact design employs a series of contact points, often arranged in a radial or linear configuration, to engage the fiber simultaneously.
The key components of a multi-point contact spinning wheel include the drive wheel, drive band, flyer assembly, bobbin, and a specialized multi-point contact mechanism. The drive wheel, powered by a treadle or electric motor, transmits rotational energy to the flyer via the drive band. The flyer, a U-shaped component with hooks or guides, twists the fiber and winds the yarn onto the bobbin. The multi-point contact mechanism, typically a series of rollers, guides, or segmented spindles, engages the fiber at multiple points, ensuring uniform tension and twist distribution. This design reduces the risk of fiber slippage, minimizes breakage, and allows for finer control over yarn thickness and twist.
Multi-Point Contact Mechanism
The multi-point contact mechanism is the defining feature of this spinning wheel variant. Unlike traditional spindles or flyers, which rely on a single point of contact to twist and draw the fiber, the multi-point system uses a series of contact points—often in the form of rollers, segmented spindles, or articulated guides—to distribute mechanical forces. These contact points are strategically positioned to align with the fiber’s path, ensuring continuous engagement throughout the drafting and twisting phases.
In one common configuration, the multi-point contact mechanism consists of a series of paired rollers arranged in a linear sequence. Each pair of rollers rotates at a slightly different speed, creating a controlled drafting zone that attenuates the fiber while maintaining tension. The rollers are coated with materials like rubber or textured metal to enhance grip and prevent slippage. Alternatively, some designs employ segmented spindles, each with its own drive mechanism, to impart twist at multiple points along the fiber’s length. This approach is particularly effective for delicate fibers, such as silk or fine cotton, which require precise handling to avoid breakage.
The multi-point contact mechanism also incorporates tensioning systems to maintain consistent pressure across all contact points. These systems may include adjustable springs, pneumatic actuators, or electronic sensors that monitor and regulate tension in real time. By distributing the mechanical load, the multi-point design reduces wear on individual components, extends the lifespan of the spinning wheel, and enhances overall reliability.
Drive Systems and Power Transmission
The drive system of a multi-point contact spinning wheel is critical to its performance, as it must deliver precise and consistent rotational energy to multiple components. Traditional spinning wheels typically use a single drive band to connect the drive wheel to the flyer or spindle. In contrast, multi-point contact wheels often employ multiple drive bands or a complex pulley system to power the various contact points independently.
In a double-drive configuration, two drive bands are used: one to rotate the flyer and another to drive the bobbin or multi-point contact mechanism. This setup allows for differential speeds, enabling the flyer to twist the fiber while the bobbin winds the yarn at a slightly different rate. Some modern designs incorporate electric motors, which provide greater control over speed and torque. These motors are often paired with electronic controllers that allow operators to adjust the speed of individual contact points, optimizing the spinning process for specific fiber types or yarn characteristics.
The power transmission system must also account for the increased mechanical complexity of the multi-point contact mechanism. To minimize energy loss and ensure smooth operation, high-quality bearings, low-friction materials, and precision-engineered pulleys are used. In industrial applications, the drive system may be integrated with automated control systems, enabling real-time monitoring and adjustment of spinning parameters.
Materials and Construction
The construction of multi-point contact spinning wheels reflects a balance between traditional craftsmanship and modern engineering. In artisanal models, the frame and drive wheel are often crafted from hardwoods like oak, maple, or cherry, chosen for their durability and aesthetic appeal. The multi-point contact mechanism, however, requires precision-engineered components, typically made from metals like stainless steel or aluminum, to ensure consistent performance.
In industrial settings, the entire spinning wheel may be constructed from high-strength alloys or composite materials to withstand continuous operation. The rollers or spindles in the multi-point contact mechanism are often coated with specialized materials, such as polyurethane or ceramic, to enhance grip and reduce wear. The drive bands, traditionally made from cotton or hemp, are increasingly replaced with synthetic materials like polyurethane or Kevlar, which offer greater durability and elasticity.
The choice of materials also influences the wheel’s portability and maintenance requirements. Artisanal wheels prioritize lightweight construction and ease of assembly, while industrial models emphasize robustness and resistance to environmental factors like humidity and temperature fluctuations. Regardless of the application, the materials used in multi-point contact spinning wheels are selected to optimize performance, minimize maintenance, and ensure longevity.
Applications in the Spinning Process
Artisanal Spinning
In artisanal spinning, the multi-point contact spinning wheel offers significant advantages for hobbyists and small-scale producers. Its ability to handle a wide range of fibers, from coarse wool to fine silk, makes it a versatile tool for creating custom yarns. The multi-point contact mechanism allows spinners to achieve greater control over yarn thickness and twist, resulting in higher-quality handspun yarns that are prized for their uniqueness and texture.
One key application is in the production of specialty yarns, such as those used in hand-knitting, weaving, or embroidery. The multi-point contact wheel’s ability to maintain consistent tension across multiple points reduces the risk of over-twisting or under-twisting, ensuring that the yarn is uniform and free of defects. This is particularly important for delicate fibers, which are prone to breakage or stretching under traditional spinning methods.
The multi-point contact wheel also enhances the spinner’s ability to experiment with complex yarn structures, such as plied or novelty yarns. By adjusting the speed and tension of individual contact points, spinners can create yarns with varying degrees of twist, thickness, or texture, opening up new creative possibilities. For example, a spinner might use the wheel to produce a two-ply yarn with one strand of tightly twisted wool and another of loosely twisted alpaca, resulting in a textured, variegated yarn.
Industrial Spinning
In industrial textile production, the multi-point contact spinning wheel is adapted for high-throughput applications, often integrated into automated spinning systems. These systems, which draw on the principles of ring spinning, rotor spinning, or air-jet spinning, use multi-point contact mechanisms to process large volumes of fiber with minimal human intervention. The technology is particularly well-suited for producing fine-count yarns, which require precise control over drafting and twisting to achieve the desired strength and uniformity.
One major application is in the production of cotton and synthetic yarns for woven fabrics, such as those used in apparel, upholstery, or technical textiles. The multi-point contact mechanism allows for faster drafting and twisting, reducing production times and increasing output. By distributing mechanical forces across multiple points, the system also minimizes fiber breakage, resulting in fewer defects and higher-quality yarns.
Another industrial application is in the spinning of blended yarns, which combine natural and synthetic fibers to achieve specific performance characteristics. The multi-point contact wheel’s ability to handle diverse fiber types simultaneously makes it ideal for creating blends like cotton-polyester or wool-nylon. The precise control offered by the multi-point mechanism ensures that the fibers are evenly distributed throughout the yarn, enhancing its strength, durability, and aesthetic appeal.
Specialty Fibers and Niche Markets
The multi-point contact spinning wheel is also finding applications in niche markets, such as the production of yarns from unconventional or sustainable fibers. For example, it is used to spin fibers derived from bamboo, hemp, or recycled materials, which often have unique properties that require specialized handling. The multi-point contact mechanism’s ability to adapt to varying fiber lengths and textures makes it a valuable tool for these emerging markets.
In the luxury textile sector, the technology is employed to spin high-value fibers like cashmere, angora, or qiviut (musk ox wool). These fibers are notoriously difficult to spin due to their fineness and fragility, but the multi-point contact wheel’s gentle handling and precise control enable the production of ultra-fine yarns with exceptional softness and luster. These yarns command premium prices in markets for high-end fashion and artisanal textiles.
Comparative Analysis of Spinning Wheel Designs
To understand the advantages of the multi-point contact spinning wheel, it is useful to compare it with other spinning wheel designs, including the great wheel, Saxony wheel, and modern electric spinners. The following table provides a detailed comparison of these technologies based on key performance metrics.
Feature | Great Wheel | Saxony Wheel | Electric Spinner | Multi-Point Contact Wheel |
---|---|---|---|---|
Drive Mechanism | Hand-driven | Foot treadle | Electric motor | Foot treadle or electric motor |
Contact Points | Single (spindle) | Single (flyer/bobbin) | Single (flyer/bobbin) | Multiple (rollers/segmented spindles) |
Fiber Handling | Coarse wools, limited versatility | Wide range, including fine fibers | Wide range, user-dependent | Highly versatile, delicate fibers |
Yarn Consistency | Low, operator-dependent | Moderate, improved with flyer | High, automated control | Very high, due to multiple contact points |
Production Speed | Slow, manual operation | Moderate, continuous spinning | Fast, automated | Very fast, optimized for high throughput |
Ease of Use | High skill required | Moderate skill required | Low skill required | Moderate to low, depending on automation |
Applications | Artisanal, coarse yarns | Artisanal, general-purpose yarns | Artisanal/industrial, specialty yarns | Artisanal/industrial, fine and blended yarns |
Maintenance | Low, simple design | Moderate, more components | High, electronic components | Moderate, precision components |
Cost | Low | Moderate | High | High, due to specialized mechanism |
Analysis of Table
The great wheel, while simple and cost-effective, is limited by its single-point contact and manual operation, making it unsuitable for high-volume or fine-yarn production. The Saxony wheel, with its bobbin-and-flyer system, offers greater versatility and efficiency but still relies on a single contact point, which can lead to inconsistencies in yarn quality. Electric spinners provide automation and speed, but their single-point contact limits their ability to handle delicate or unconventional fibers.
The multi-point contact spinning wheel stands out for its ability to distribute mechanical forces across multiple points, resulting in superior yarn consistency and versatility. Its high production speed and adaptability to both artisanal and industrial applications make it a valuable tool for modern textile production. However, its complexity and cost may pose barriers for small-scale spinners, particularly those without access to advanced maintenance resources.
Technical Innovations and Future Directions
Automation and Digital Integration
Recent advancements in multi-point contact spinning wheels have focused on automation and digital integration, particularly in industrial applications. Modern wheels are increasingly equipped with sensors and microcontrollers that monitor key parameters, such as tension, speed, and fiber flow, in real time. These systems enable dynamic adjustments to optimize yarn quality and minimize waste, reducing the need for manual intervention.
In some designs, machine learning algorithms are used to analyze spinning data and predict optimal settings for specific fiber types or yarn characteristics. For example, a multi-point contact wheel might automatically adjust the speed of individual rollers based on the fiber’s tensile strength, ensuring consistent drafting and twisting. These innovations are particularly valuable in large-scale production, where even small improvements in efficiency can lead to significant cost savings.
Sustainable Materials and Processes
The growing emphasis on sustainability in the textile industry has spurred interest in multi-point contact spinning wheels for processing eco-friendly fibers. These wheels are well-suited for spinning fibers like organic cotton, flax, or recycled polyester, which often require specialized handling to maintain their integrity. By optimizing the spinning process, the multi-point contact mechanism reduces fiber waste and energy consumption, aligning with the industry’s sustainability goals.
Some manufacturers are also exploring the use of biodegradable or recycled materials in the construction of spinning wheels. For example, drive bands made from recycled polymers or rollers coated with plant-based resins are being tested to reduce the environmental footprint of the equipment. These innovations reflect a broader trend toward sustainable textile production, with the multi-point contact spinning wheel playing a central role.
Hybrid Designs and Modularity
Another emerging trend is the development of hybrid spinning wheels that combine multi-point contact mechanisms with other spinning technologies, such as rotor or air-jet systems. These hybrid designs aim to leverage the strengths of each technology, such as the high speed of rotor spinning and the precision of multi-point contact, to create yarns with unique properties. For example, a hybrid wheel might use a multi-point contact mechanism for initial drafting and twisting, followed by an air-jet system for final winding, resulting in a yarn with exceptional strength and smoothness.
Modularity is also a key focus, particularly for artisanal spinners. Modular multi-point contact wheels allow users to swap out components, such as rollers or spindles, to accommodate different fiber types or spinning techniques. This flexibility enhances the wheel’s versatility and extends its lifespan, making it a cost-effective investment for small-scale producers.
Challenges and Limitations
Technical Complexity
The primary challenge associated with multi-point contact spinning wheels is their technical complexity. The multi-point contact mechanism requires precise engineering and calibration to ensure that all contact points operate in harmony. Misalignment or inconsistent tension can lead to yarn defects, such as slubs or weak spots, undermining the wheel’s advantages. In industrial settings, this complexity necessitates skilled operators and regular maintenance, increasing operational costs.
Cost and Accessibility
The high cost of multi-point contact spinning wheels is another significant barrier, particularly for artisanal spinners or small-scale producers in developing regions. The specialized components, advanced materials, and electronic controls used in these wheels drive up manufacturing costs, making them less accessible than traditional spinning wheels. While the technology’s benefits—such as improved yarn quality and efficiency—justify the investment for large-scale producers, smaller operations may struggle to afford the upfront costs.
Fiber Limitations
While the multi-point contact spinning wheel is highly versatile, it is not universally suited to all fiber types. Extremely short or brittle fibers, such as certain plant-based materials, may still pose challenges, as the multi-point contact mechanism relies on continuous fiber flow to maintain tension. In such cases, alternative spinning methods, such as open-end spinning, may be more effective. Ongoing research aims to address these limitations by developing adaptive contact mechanisms that can accommodate a broader range of fiber properties.
Case Studies and Practical Examples
Artisanal Production: The Rise of Custom Yarns
In the Pacific Northwest of the United States, a cooperative of artisanal spinners has adopted multi-point contact spinning wheels to produce custom yarns for local weavers and knitters. By leveraging the wheels’ ability to handle diverse fibers, the cooperative creates unique blends, such as merino-silk or alpaca-bamboo, that cater to niche markets. The multi-point contact mechanism allows the spinners to maintain consistent yarn thickness and twist, resulting in high-quality products that command premium prices. The cooperative has also integrated digital tensioning systems, enabling precise control over yarn characteristics and reducing production times.
Industrial Application: High-Volume Cotton Spinning
A textile manufacturer in India has implemented multi-point contact spinning wheels in its cotton spinning facility, achieving a 20% increase in production efficiency compared to traditional ring spinning systems. The wheels’ ability to process fine-count cotton yarns with minimal breakage has reduced waste and improved product quality, enabling the manufacturer to meet growing demand for high-quality cotton fabrics. The facility uses automated multi-point contact wheels equipped with sensors and machine learning algorithms, which optimize spinning parameters in real time, further enhancing efficiency.
Sustainable Textiles: Spinning Recycled Fibers
A European textile company has adopted multi-point contact spinning wheels to produce yarns from recycled polyester and cotton blends. The wheels’ gentle handling and precise control ensure that the recycled fibers, which are often shorter and less uniform than virgin fibers, are spun into strong, consistent yarns. The company has reported a 15% reduction in fiber waste and a 10% decrease in energy consumption compared to conventional spinning methods, demonstrating the technology’s potential for sustainable textile production.
Conclusion
The multi-point contact spinning wheel represents a significant advancement in spinning technology, bridging the gap between traditional craftsmanship and modern industrial efficiency. Its innovative design, which distributes mechanical forces across multiple contact points, enhances yarn quality, versatility, and production speed, making it a valuable tool for both artisanal and industrial applications. From its historical roots in the spinning wheels of the Middle Ages to its current role in sustainable textile production, the multi-point contact wheel embodies the evolution of textile technology.
Despite its challenges, such as technical complexity and high costs, the technology’s benefits—improved yarn consistency, adaptability to diverse fibers, and potential for automation—position it as a cornerstone of the future textile industry. As research and development continue to refine the multi-point contact mechanism, we can expect further innovations that enhance its accessibility, efficiency, and environmental sustainability. By combining the precision of modern engineering with the timeless art of spinning, the multi-point contact spinning wheel is poised to shape the future of textile production for generations to come.
Maximize Tooling and CNC Metal Spinning Capabilities.
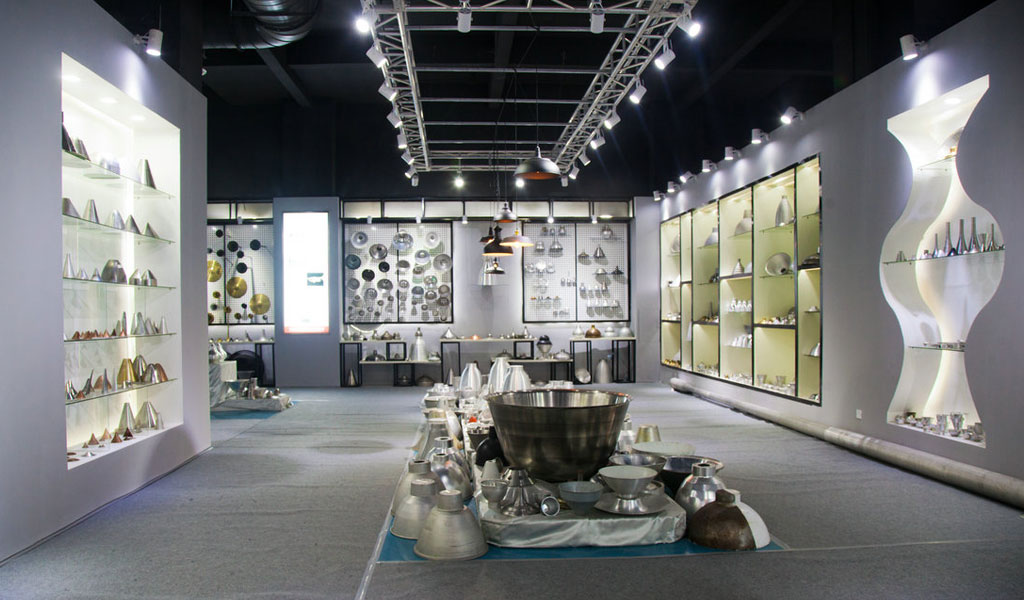
At BE-CU China Metal Spinning company, we make the most of our equipment while monitoring signs of excess wear and stress. In addition, we look into newer, modern equipment and invest in those that can support or increase our manufacturing capabilities. Our team is very mindful of our machines and tools, so we also routinely maintain them to ensure they don’t negatively impact your part’s quality and productivity.
Talk to us today about making a rapid prototype with our CNC metal spinning service. Get a direct quote by chatting with us here or request a free project review.
BE-CU China CNC Metal Spinning service include : CNC Metal Spinning,Metal Spinning Die,Laser Cutting, Tank Heads Spinning,Metal Hemispheres Spinning,Metal Cones Spinning,Metal Dish-Shaped Spinning,Metal Trumpet Spinning,Metal Venturi Spinning,Aluminum Spinning Products,Stainless Steel Spinning Products,Copper Spinning Products,Brass Spinning Products,Steel Spinning Product,Metal Spinnin LED Reflector,Metal Spinning Pressure Vessel,