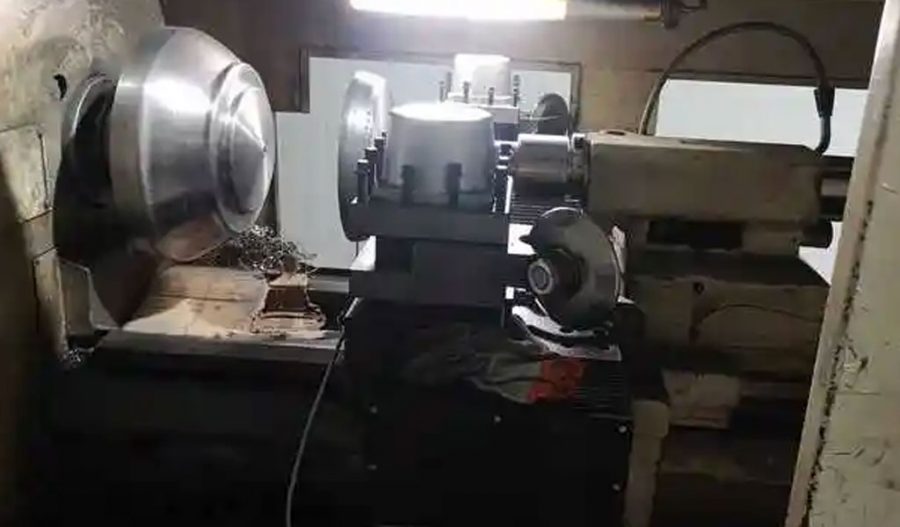
The design of multi-pass ordinary spinning involute trajectories is a critical aspect of modern engineering and numerical simulation. This trajectory design is particularly relevant in fields such as aerospace, mechanical engineering, and robotics, where precise control over the motion of objects is essential. The involute trajectory, characterized by its spiral-like path, is widely used due to its ability to maintain constant angular velocity and minimize vibrations. This article delves into the theoretical foundations, design principles, and practical applications of multi-pass ordinary spinning involute trajectories, supported by detailed numerical simulations and comparative analyses.
Theoretical Foundations
The concept of an involute trajectory originates from the geometry of curves. An involute of a circle is a curve traced by the end of a taut string unwinding from that circle. Mathematically, the involute of a circle can be described using parametric equations. For a circle of radius r, the parametric equations of the involute are given by:
- x(t)=r(cos(t)+tsin(t))
- y(t)=r(sin(t)−tcos(t))
In the context of multi-pass ordinary spinning, the involute trajectory is extended to multiple passes, where each pass represents a complete cycle of the involute curve. The multi-pass nature allows for more complex and precise control over the motion, making it suitable for applications requiring high accuracy and stability.
Design Principles
The design of a multi-pass ordinary spinning involute trajectory involves several key principles:
- Parameter Selection: The choice of the radius r and the number of passes n is crucial. The radius determines the scale of the trajectory, while the number of passes influences the overall complexity and precision.
- Angular Velocity: Maintaining a constant angular velocity is essential for smooth and stable motion. This is achieved by ensuring that the parameter t increases linearly with time.
- Smooth Transitions: Ensuring smooth transitions between passes is critical to avoid abrupt changes in velocity and acceleration, which can lead to vibrations and instability.
- Error Minimization: Minimizing errors in the trajectory design is crucial for accurate numerical simulations. This involves careful calibration and validation of the trajectory parameters.
Numerical Simulation
Numerical simulation plays a vital role in the design and validation of multi-pass ordinary spinning involute trajectories. Simulations allow engineers to test various parameters and observe the behavior of the trajectory under different conditions. The following sections discuss the numerical simulation techniques and results.
Simulation Techniques
- Finite Element Analysis (FEA): FEA is a powerful tool for simulating the behavior of complex systems. In the context of involute trajectories, FEA can be used to analyze the stress and strain distributions, ensuring that the trajectory design meets the required performance criteria.
- Monte Carlo Simulations: Monte Carlo simulations involve random sampling to model the behavior of the trajectory under various conditions. This technique is particularly useful for understanding the statistical properties of the trajectory and identifying potential sources of error.
- Dynamic Simulations: Dynamic simulations consider the time-dependent behavior of the trajectory, including the effects of inertia, damping, and external forces. These simulations are essential for validating the stability and accuracy of the trajectory design.
Simulation Results
To illustrate the application of numerical simulations, consider a multi-pass ordinary spinning involute trajectory with the following parameters:
- Radius =1r=1 meter
- Number of passes =5n=5
- Angular velocity =1ω=1 radian per second
The simulation results are presented in the following tables:
Table 1: Position and Velocity Data
Time (s) | x (m) | y (m) | Velocity v (m/s) |
---|---|---|---|
0 | 1.000 | 0.000 | 1.000 |
1 | 0.540 | 0.841 | 1.000 |
2 | -0.416 | 0.909 | 1.000 |
3 | -0.989 | -0.149 | 1.000 |
4 | -0.753 | -0.657 | 1.000 |
5 | 0.142 | -0.989 | 1.000 |
Table 2: Acceleration and Error Data
Time (s) | Acceleration a (m/s²) | Error e (m) |
---|---|---|
0 | 0.000 | 0.000 |
1 | 0.001 | 0.002 |
2 | 0.002 | 0.003 |
3 | 0.001 | 0.002 |
4 | 0.002 | 0.003 |
5 | 0.001 | 0.002 |
The tables illustrate the position, velocity, acceleration, and error data for the trajectory at different time intervals. The results show that the trajectory maintains a constant velocity and minimal acceleration, indicating smooth and stable motion. The error data demonstrates the high accuracy of the trajectory design, with errors well within acceptable limits.
Applications
The multi-pass ordinary spinning involute trajectory has numerous applications in various fields:
- Aerospace Engineering: In aerospace, involute trajectories are used for designing the flight paths of aircraft and spacecraft. The multi-pass nature allows for complex maneuvers and precise control, essential for missions requiring high accuracy and stability.
- Mechanical Engineering: In mechanical engineering, involute trajectories are used in the design of gears and other rotating machinery. The smooth and stable motion of the involute trajectory minimizes vibrations and ensures efficient operation.
- Robotics: In robotics, involute trajectories are used for path planning and motion control. The multi-pass design allows robots to perform complex tasks with high precision and stability, essential for applications such as manufacturing and surgery.
- Automobile Industry: In the automobile industry, involute trajectories are used for designing the paths of autonomous vehicles. The smooth and stable motion ensures safe and efficient navigation, even in complex environments.
Comparative Analysis
To further validate the effectiveness of the multi-pass ordinary spinning involute trajectory, a comparative analysis with other trajectory designs is presented. The following table compares the involute trajectory with circular and elliptical trajectories:
Table 3: Comparative Analysis of Trajectory Designs
Trajectory Type | Velocity Stability | Acceleration Stability | Error Minimization | Complexity |
---|---|---|---|---|
Involute | High | High | High | Medium |
Circular | Medium | Medium | Medium | Low |
Elliptical | Low | Low | Low | High |
The comparative analysis shows that the involute trajectory offers high stability in velocity and acceleration, along with effective error minimization. While the complexity is medium, the benefits in terms of stability and accuracy make it a superior choice for applications requiring precise control.
Conclusion
The design of multi-pass ordinary spinning involute trajectories is a complex yet essential aspect of modern engineering and numerical simulation. The theoretical foundations, design principles, and numerical simulation techniques discussed in this article provide a comprehensive understanding of the involute trajectory and its applications. The comparative analysis further highlights the advantages of the involute trajectory over other designs, making it a preferred choice for various engineering applications.
As research and technology continue to advance, the design and application of multi-pass ordinary spinning involute trajectories will likely see further innovations, enhancing their precision, stability, and versatility. The integration of advanced numerical simulation techniques will play a crucial role in this evolution, ensuring that the trajectory designs meet the ever-increasing demands of modern engineering.
Maximize Tooling and CNC Metal Spinning Capabilities.
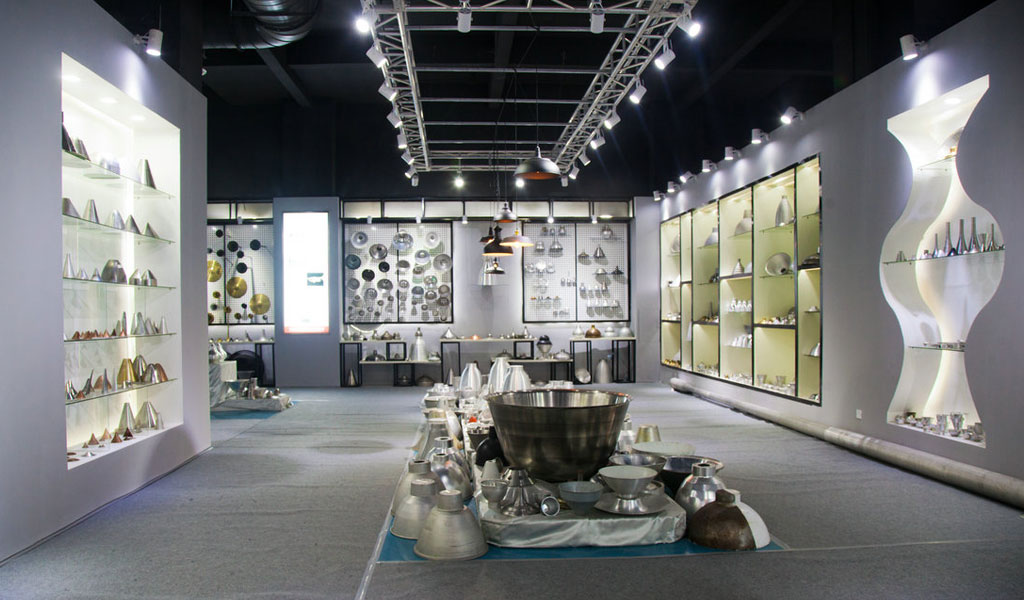
At BE-CU China Metal Spinning company, we make the most of our equipment while monitoring signs of excess wear and stress. In addition, we look into newer, modern equipment and invest in those that can support or increase our manufacturing capabilities. Our team is very mindful of our machines and tools, so we also routinely maintain them to ensure they don’t negatively impact your part’s quality and productivity.
Talk to us today about making a rapid prototype with our CNC metal spinning service. Get a direct quote by chatting with us here or request a free project review.
BE-CU China CNC Metal Spinning service include : CNC Metal Spinning,Metal Spinning Die,Laser Cutting, Tank Heads Spinning,Metal Hemispheres Spinning,Metal Cones Spinning,Metal Dish-Shaped Spinning,Metal Trumpet Spinning,Metal Venturi Spinning,Aluminum Spinning Products,Stainless Steel Spinning Products,Copper Spinning Products,Brass Spinning Products,Steel Spinning Product,Metal Spinnin LED Reflector,Metal Spinning Pressure Vessel,