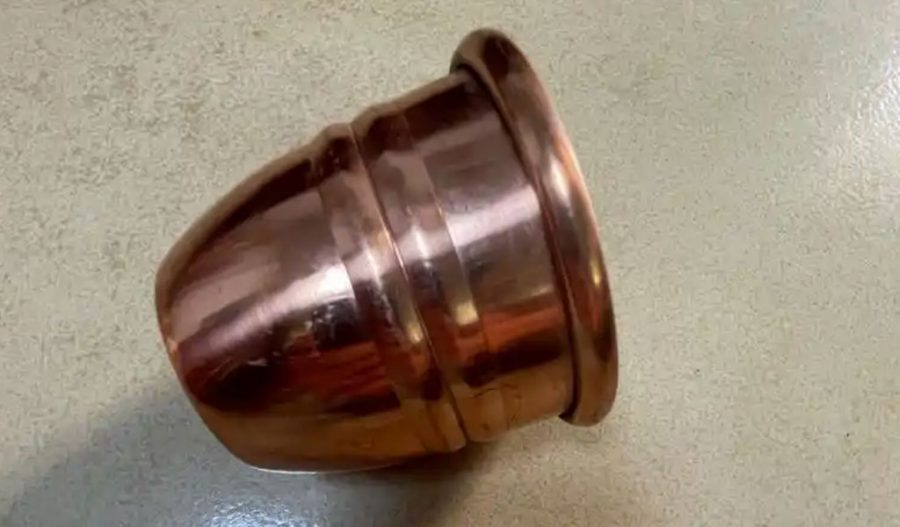
The design of spinning die and the pressing method of cast aluminum alloy wheel hubs are critical aspects of modern automotive manufacturing. These processes involve a combination of material science, mechanical engineering, and advanced manufacturing techniques to produce high-quality, lightweight, and durable wheel hubs. This article delves into the intricacies of these processes, providing a comprehensive overview that includes detailed tables for comparison.
Introduction to Cast Aluminum Alloy Wheel Hubs
Cast aluminum alloy wheel hubs are widely used in the automotive industry due to their superior strength-to-weight ratio, excellent corrosion resistance, and aesthetic appeal. The manufacturing process involves several stages, including die design, casting, and pressing. Each stage requires precise control to ensure the final product meets the required specifications.
Design of Spinning Die
The spinning die is a crucial component in the manufacturing of cast aluminum alloy wheel hubs. The design of the spinning die involves several key considerations, including material selection, geometric design, and thermal management.
Material Selection
The choice of material for the spinning die is critical as it directly affects the die’s durability and the quality of the cast wheel hub. Common materials used for spinning dies include:
- Tool Steel: Known for its high hardness and wear resistance, tool steel is often used in high-volume production.
- High-Speed Steel (HSS): Offers excellent heat resistance and is suitable for high-speed spinning operations.
- Carbide: Provides superior wear resistance and is ideal for applications requiring precise dimensional control.
Geometric Design
The geometric design of the spinning die involves creating a mold that accurately reflects the desired shape and dimensions of the wheel hub. Key geometric considerations include:
- Cavity Design: The cavity must be designed to accommodate the molten aluminum alloy and ensure uniform distribution.
- Runner and Gate System: Properly designed runners and gates are essential for efficient molten metal flow and to prevent defects such as porosity and shrinkage.
- Venting: Adequate venting is necessary to allow gases to escape during the casting process, preventing the formation of voids and inclusions.
Thermal Management
Effective thermal management is crucial for maintaining the die’s temperature within an optimal range. This involves:
- Cooling Channels: Incorporating cooling channels within the die to dissipate heat efficiently.
- Insulation: Using insulating materials to control heat transfer and maintain uniform temperature distribution.
- Temperature Monitoring: Implementing sensors to monitor the die’s temperature in real-time and make necessary adjustments.
Pressing Method of Cast Aluminum Alloy Wheel Hub
The pressing method involves applying pressure to the cast aluminum alloy to shape it into the desired form. This process is critical for achieving the final dimensions and mechanical properties of the wheel hub.
Types of Pressing Methods
Several pressing methods are employed in the manufacturing of cast aluminum alloy wheel hubs, including:
- Hot Pressing: Involves heating the aluminum alloy to a high temperature before applying pressure. This method enhances formability and reduces the risk of cracking.
- Cold Pressing: Performed at room temperature, this method is suitable for alloys with good formability and is often used for finishing operations.
- Warm Pressing: Conducted at intermediate temperatures, this method balances formability and strength, making it suitable for a wide range of alloys.
Pressing Parameters
Optimizing pressing parameters is essential for achieving high-quality wheel hubs. Key parameters include:
- Pressure: The applied pressure must be sufficient to deform the material without causing defects such as cracking or excessive thinning.
- Temperature: The pressing temperature must be carefully controlled to ensure optimal material flow and prevent thermal degradation.
- Speed: The pressing speed affects the material’s flow behavior and the final microstructure. Slow speeds allow for better control but may increase cycle time.
Defect Analysis
Common defects encountered during the pressing of cast aluminum alloy wheel hubs include:
- Cracking: Often results from excessive pressure or inadequate temperature control.
- Wrinkling: Caused by insufficient pressure or poor material flow.
- Orange Peel: A surface defect characterized by a rough, uneven texture, typically due to improper pressing parameters.
Comparative Analysis
The following tables provide a comparative analysis of different materials, geometric designs, and pressing methods used in the manufacturing of cast aluminum alloy wheel hubs.
Table 1: Comparison of Spinning Die Materials
Material | Hardness (HRC) | Wear Resistance | Heat Resistance | Cost |
---|---|---|---|---|
Tool Steel | 55-60 | High | Moderate | Moderate |
High-Speed Steel (HSS) | 60-65 | High | High | High |
Carbide | 70-75 | Very High | Moderate | Very High |
Table 2: Comparison of Geometric Designs
Design Feature | Cavity Design | Runner and Gate System | Venting |
---|---|---|---|
Purpose | Accommodate molten metal | Efficient metal flow | Gas escape |
Key Considerations | Uniform distribution | Prevent porosity and shrinkage | Prevent voids and inclusions |
Example | Complex shapes with uniform wall thickness | Well-designed runners and gates | Adequate venting channels |
Table 3: Comparison of Pressing Methods
Pressing Method | Temperature Range (°C) | Formability | Strength | Cost |
---|---|---|---|---|
Hot Pressing | 400-500 | High | Moderate | High |
Cold Pressing | Room Temperature | Moderate | High | Moderate |
Warm Pressing | 200-300 | High | High | High |
Conclusion
The design of spinning die and the pressing method of cast aluminum alloy wheel hubs are complex processes that require a deep understanding of material science, mechanical engineering, and advanced manufacturing techniques. By carefully selecting materials, optimizing geometric designs, and controlling pressing parameters, manufacturers can produce high-quality, durable, and aesthetically pleasing wheel hubs. Continuous innovation and research in these areas will further enhance the efficiency and sustainability of the automotive industry.
Future Directions
As the automotive industry continues to evolve, there is a growing emphasis on sustainability and efficiency. Future research should focus on developing more environmentally friendly materials and processes, as well as integrating advanced technologies such as additive manufacturing and artificial intelligence to optimize the design and production of cast aluminum alloy wheel hubs.
Maximize Tooling and CNC Metal Spinning Capabilities.
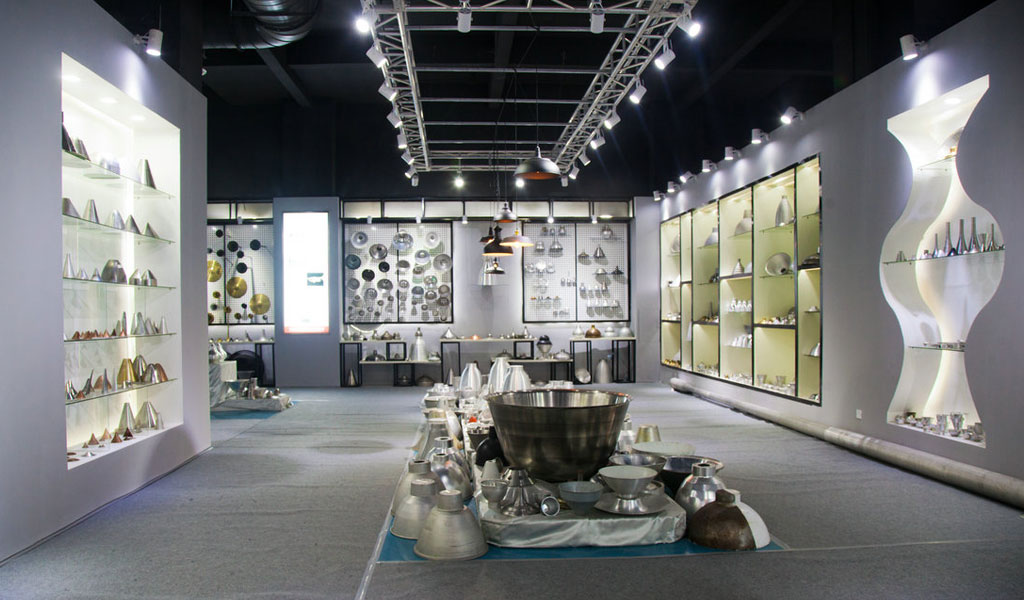
At BE-CU China Metal Spinning company, we make the most of our equipment while monitoring signs of excess wear and stress. In addition, we look into newer, modern equipment and invest in those that can support or increase our manufacturing capabilities. Our team is very mindful of our machines and tools, so we also routinely maintain them to ensure they don’t negatively impact your part’s quality and productivity.
Talk to us today about making a rapid prototype with our CNC metal spinning service. Get a direct quote by chatting with us here or request a free project review.
BE-CU China CNC Metal Spinning service include : CNC Metal Spinning,Metal Spinning Die,Laser Cutting, Tank Heads Spinning,Metal Hemispheres Spinning,Metal Cones Spinning,Metal Dish-Shaped Spinning,Metal Trumpet Spinning,Metal Venturi Spinning,Aluminum Spinning Products,Stainless Steel Spinning Products,Copper Spinning Products,Brass Spinning Products,Steel Spinning Product,Metal Spinnin LED Reflector,Metal Spinning Pressure Vessel,