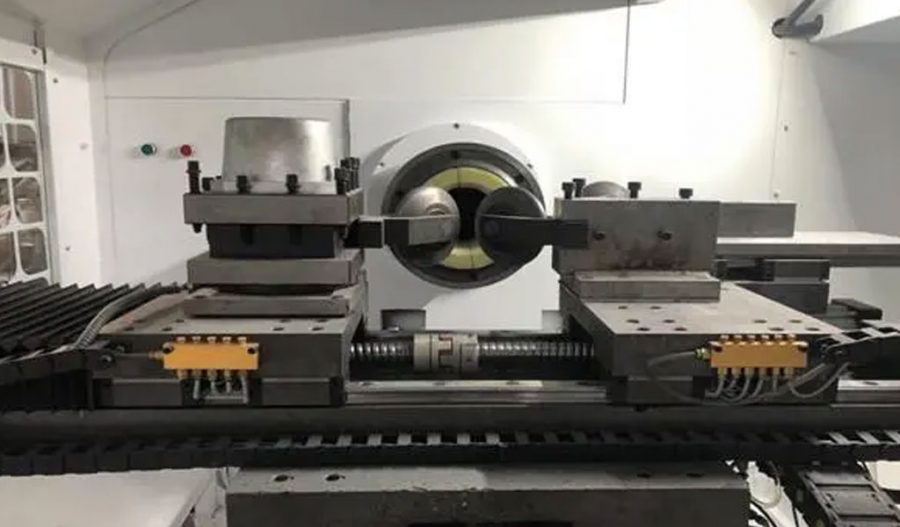
Die-less spinning, also known as CNC (Computer Numerical Control) spinning or freeform spinning, is an advanced metalworking process that involves the forming of asymmetric workpieces without the use of a fixed die. This technique is particularly valuable for producing complex, irregularly shaped parts with high precision and efficiency. As manufacturing industries evolve to meet the demands of customized and intricate designs, die-less spinning has emerged as a pivotal technology in achieving these objectives.
Historical Background Of Die-less spinning
Die-less spinning traces its roots to traditional metal spinning, which has been practiced for centuries. Traditional spinning involves the manual manipulation of metal over a mandrel using a fixed die, allowing for the creation of symmetrical, axisymmetric parts such as bowls, cones, and cylinders. However, the limitations of fixed dies in producing non-symmetrical and complex shapes led to the development of die-less spinning techniques.
With the advent of computer numerical control (CNC) technology in the late 20th century, the metalworking industry saw a significant transformation. CNC spinning machines, equipped with sophisticated software and control systems, enabled precise and automated control over the spinning process. This development marked the beginning of die-less spinning, allowing for greater flexibility and precision in shaping asymmetric workpieces.
Die-less Spinning Process Overview
Die-less spinning involves several key steps:
- Material Preparation: A metal blank, typically in the form of a flat disc or sheet, is prepared. Common materials include aluminum, steel, and various alloys, chosen for their malleability and strength.
- CNC Programming: Detailed CAD (Computer-Aided Design) models of the desired workpiece are created. These models are translated into CNC programs, which guide the spinning machine’s movements and operations.
- Mounting and Centering: The metal blank is mounted onto a rotating spindle or chuck. Precise centering is crucial to ensure uniformity and accuracy during the spinning process.
- Tooling and Forming: Instead of a fixed die, a series of CNC-controlled rollers and tools are used to gradually shape the metal blank. These tools move along predetermined paths, applying pressure and force to deform the metal into the desired shape. The absence of a fixed die allows for greater flexibility in creating asymmetric and complex geometries.
- Finishing: After the initial shaping, additional processes such as trimming, polishing, and heat treatment may be applied to achieve the final specifications and surface finish of the workpiece.
Advantages of Die-Less Spinning
- Flexibility and Customization: Die-less spinning excels in producing customized and low-volume parts. The absence of fixed dies means that manufacturers can quickly switch between different designs without the need for extensive tooling changes.
- Cost-Effectiveness: Traditional spinning methods require the fabrication of dedicated dies for each specific part, which can be expensive and time-consuming. Die-less spinning eliminates this need, reducing overall production costs, especially for small batch sizes.
- Precision and Quality: CNC control ensures high precision and repeatability, resulting in consistent and high-quality parts. The ability to precisely control the spinning process minimizes defects and variations in the final products.
- Complex Geometries: Die-less spinning is particularly advantageous for creating complex, non-symmetrical shapes that are challenging or impossible to achieve with traditional methods. This capability is critical for industries such as aerospace, automotive, and medical devices, where intricate designs are often required.
Applications Of Die-less Spinning
Die-less spinning finds applications across various industries:
- Aerospace: The aerospace industry demands lightweight, high-strength components with intricate shapes. Die-less spinning is used to manufacture components such as turbine blades, cones, and other aerodynamic structures.
- Automotive: In the automotive sector, die-less spinning is employed to produce parts like exhaust components, wheels, and structural elements that require precise shaping and high strength.
- Medical Devices: The medical industry benefits from die-less spinning in the production of customized implants, prosthetics, and other medical instruments that require unique and patient-specific geometries.
- Consumer Goods: Die-less spinning is also used in the production of household items, lighting fixtures, and decorative pieces where unique and artistic designs are desired.
Challenges and Future Directions
Despite its numerous advantages, die-less spinning faces certain challenges:
- Material Limitations: Not all materials are suitable for die-less spinning due to their inherent properties such as brittleness or work-hardening tendencies. Research and development efforts are ongoing to expand the range of materials that can be effectively spun using this method.
- Complexity and Skill Requirements: While CNC technology automates much of the process, the setup and programming of CNC machines for die-less spinning require specialized knowledge and expertise. Skilled operators and programmers are essential to ensure successful outcomes.
- Surface Finish and Accuracy: Achieving the desired surface finish and dimensional accuracy can be challenging, especially for highly complex shapes. Advanced toolpath planning and real-time monitoring systems are being developed to address these issues.
The future of die-less spinning holds promise with continued advancements in CNC technology, materials science, and process optimization. The integration of artificial intelligence and machine learning algorithms is expected to further enhance the precision and efficiency of die-less spinning processes. Additionally, ongoing research into hybrid manufacturing techniques, combining die-less spinning with other processes such as additive manufacturing, could open new avenues for producing even more complex and innovative components.
In conclusion, die-less spinning represents a significant evolution in metalworking, offering unparalleled flexibility, precision, and cost-effectiveness for the production of asymmetric workpieces. As industries continue to demand more customized and intricate designs, the role of die-less spinning in modern manufacturing is set to expand, driving innovation and enabling the creation of next-generation components.
Maximize Tooling and CNC Metal Spinning Capabilities.
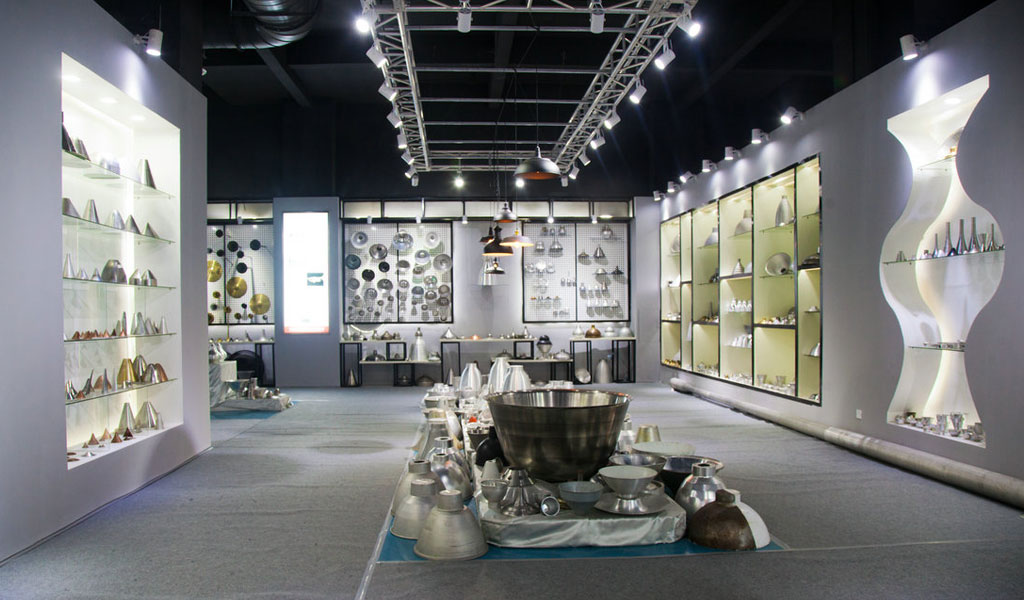
At BE-CU China Metal Spinning company, we make the most of our equipment while monitoring signs of excess wear and stress. In addition, we look into newer, modern equipment and invest in those that can support or increase our manufacturing capabilities. Our team is very mindful of our machines and tools, so we also routinely maintain them to ensure they don’t negatively impact your part’s quality and productivity.
Talk to us today about making a rapid prototype with our CNC metal spinning service. Get a direct quote by chatting with us here or request a free project review.
BE-CU China CNC Metal Spinning service include : CNC Metal Spinning,Metal Spinning Die,Laser Cutting, Tank Heads Spinning,Metal Hemispheres Spinning,Metal Cones Spinning,Metal Dish-Shaped Spinning,Metal Trumpet Spinning,Metal Venturi Spinning,Aluminum Spinning Products,Stainless Steel Spinning Products,Copper Spinning Products,Brass Spinning Products,Steel Spinning Product,Metal Spinnin LED Reflector,Metal Spinning Pressure Vessel,