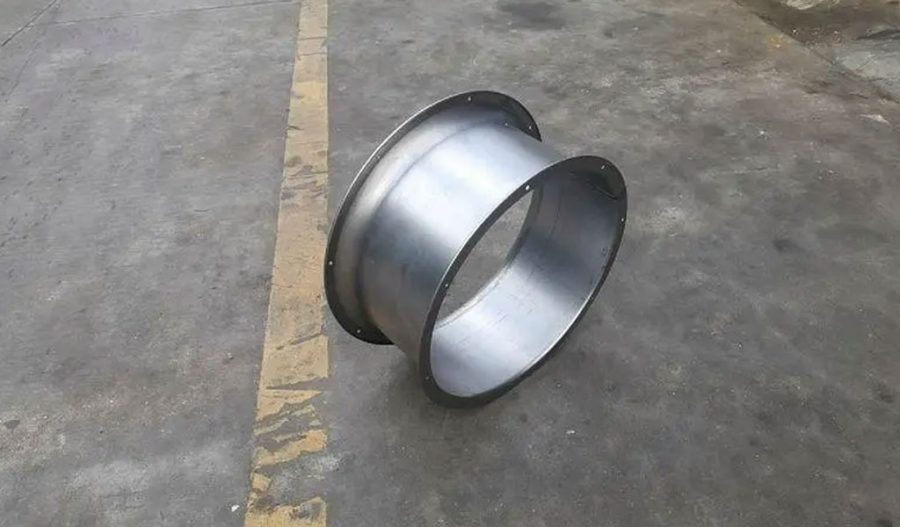
Spinning, a fundamental process in the textile and metalworking industries, involves the manipulation of materials to create fibers or shapes through rotation. There are several variations of spinning, with power spinning and normal spinning being two primary techniques. This article elucidates the differences between power spinning and normal spinning, highlighting their unique applications, advantages, and processes.
Normal Spinning
Normal spinning, also known as conventional spinning or hand spinning in the context of textiles, is a traditional method employed for centuries. In metalworking, normal spinning refers to a technique where a metal disc is rotated at high speed and formed into an axially symmetric part.
Process
- Textile Spinning:
- Material Preparation: Raw fibers, such as cotton or wool, are cleaned and carded to align the fibers.
- Spinning: The fibers are drawn out and twisted together to form yarn using a spindle or spinning wheel.
- Metal Spinning:
- Material Preparation: A metal blank (usually a disc) is secured on a lathe.
- Forming: As the blank rotates, a tool (usually a roller or hand-held tool) applies pressure to shape the metal over a form or mandrel.
Applications
- Textile Industry: Production of yarn for weaving and knitting.
- Metalworking: Fabrication of components like lampshades, kitchen utensils, and musical instruments.
Advantages
- Textile:
- Simple and cost-effective.
- Suitable for small-scale production and custom yarns.
- Metal:
- High precision and excellent surface finish.
- Ideal for producing symmetrical shapes.
Power Spinning
Power spinning, often referred to as CNC spinning or shear spinning, is an advanced, automated form of spinning that utilizes computer numerical control (CNC) machinery to achieve high precision and efficiency. It is predominantly used in metalworking.
Process
- Setup: A metal blank is mounted on a CNC lathe.
- Forming: The CNC machine controls the movement of the spinning tool, which exerts pressure on the rotating blank to shape it according to a pre-programmed design. This process can include shear spinning, where the thickness of the metal is reduced as it is formed.
Applications
- Aerospace Industry: Manufacturing of high-precision components like rocket cones and jet engine parts.
- Automotive Industry: Production of wheels and other critical parts.
- Industrial Equipment: Fabrication of robust, durable components for machinery.
Advantages
- Precision: High accuracy due to computerized control.
- Efficiency: Faster production times and lower labor costs.
- Versatility: Capable of producing complex shapes and large-scale components.
Comparison
Aspect | Normal Spinning | Power Spinning |
---|---|---|
Technology | Manual or semi-manual | Automated (CNC-controlled) |
Precision | Moderate | High |
Speed | Slower | Faster |
Cost | Lower initial investment | Higher initial investment |
Production | Small to medium scale | Medium to large scale |
Complexity | Suitable for simpler designs | Capable of complex designs |
Conclusion
While normal spinning and power spinning share the fundamental principle of shaping materials through rotation, they diverge significantly in their methods, applications, and advantages. Normal spinning is valued for its simplicity and suitability for small-scale, artisanal production, whereas power spinning excels in precision, efficiency, and the ability to handle complex, large-scale manufacturing tasks. Understanding the distinctions between these techniques allows industries to select the most appropriate method for their specific production needs.
Maximize Tooling and CNC Metal Spinning Capabilities.
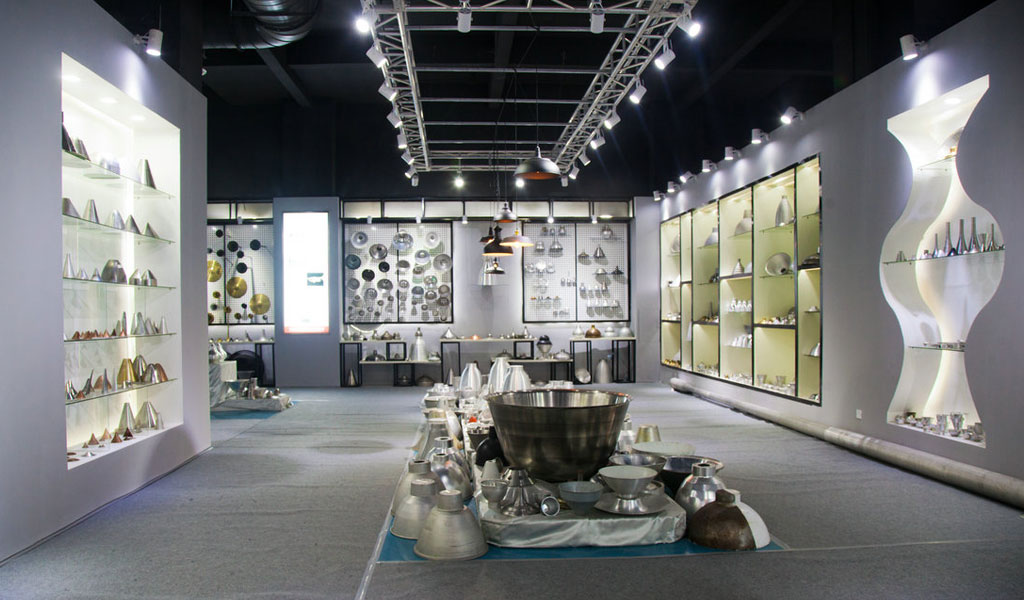
At BE-CU China Metal Spinning company, we make the most of our equipment while monitoring signs of excess wear and stress. In addition, we look into newer, modern equipment and invest in those that can support or increase our manufacturing capabilities. Our team is very mindful of our machines and tools, so we also routinely maintain them to ensure they don’t negatively impact your part’s quality and productivity.
Talk to us today about making a rapid prototype with our CNC metal spinning service. Get a direct quote by chatting with us here or request a free project review.
BE-CU China CNC Metal Spinning service include : CNC Metal Spinning,Metal Spinning Die,Laser Cutting, Tank Heads Spinning,Metal Hemispheres Spinning,Metal Cones Spinning,Metal Dish-Shaped Spinning,Metal Trumpet Spinning,Metal Venturi Spinning,Aluminum Spinning Products,Stainless Steel Spinning Products,Copper Spinning Products,Brass Spinning Products,Steel Spinning Product,Metal Spinnin LED Reflector,Metal Spinning Pressure Vessel,