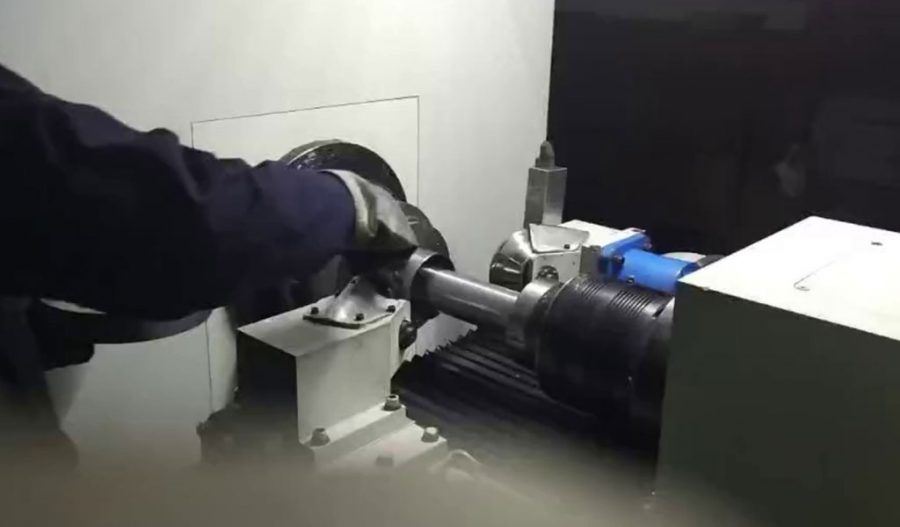
Iron is one of the most important metals used in human history, forming the backbone of the modern industrial world. It is the fourth most abundant element in the Earth’s crust, making up approximately 5% by weight. Iron is essential in numerous industries, ranging from construction to transportation, and from energy production to medical applications. The metal’s versatility is largely due to its various forms, each possessing unique properties that make it suitable for different purposes. The types of iron can be categorized based on their composition, structure, and specific uses. These categories include cast iron, wrought iron, steel, and various alloys of iron that exhibit specific characteristics for industrial and commercial applications.
What Is Iron
Iron is a chemical element with the symbol Fe and atomic number 26. It has been known to humanity for thousands of years and has played a central role in the development of civilizations, particularly in the production of tools, weapons, and infrastructure. In its pure form, iron is soft and brittle, which limits its use. However, through various processes of alloying and manipulation, iron can be made into stronger and more durable materials suited for a wide range of applications.
The properties of iron vary depending on the amount and type of impurities present, as well as the specific methods used to process it. By combining iron with carbon and other elements, different types of iron and steel with distinct properties can be created. The most significant difference among these types is their carbon content, which directly affects hardness, tensile strength, ductility, and resistance to corrosion.
Properties of Iron
Iron, in its purest form, has a silvery-gray appearance and is relatively soft compared to other metals such as steel or titanium. It is magnetic, which means it is attracted to magnets and can be magnetized itself. The metal has a high melting point of 1,538°C (2,800°F), making it suitable for use in high-temperature applications. When alloyed with other metals, iron’s physical properties can be significantly enhanced, leading to the creation of stronger and more durable materials.
Some of the key properties of iron include:
- High Density: Iron has a high density, which contributes to its weight and stability. This property is particularly useful in construction and manufacturing, where the material’s mass provides structural integrity.
- Magnetic Properties: Pure iron is ferromagnetic, meaning it can be magnetized. This property is crucial in the production of electrical components, transformers, and other devices requiring magnetism.
- Malleability and Ductility: Pure iron is relatively malleable and ductile. It can be shaped or stretched into thin sheets or wires, making it useful in the production of various metal products.
- Corrosion Resistance: Although iron is susceptible to rusting when exposed to moisture and oxygen, its corrosion resistance can be improved through alloying, coatings, or other treatments.
- Tensile Strength: The tensile strength of iron increases when it is alloyed with other elements such as carbon, manganese, or chromium. This enhanced strength is crucial for structural applications, such as in the construction of bridges, buildings, and vehicles.
- Thermal Conductivity: Iron is an excellent conductor of heat, making it useful in applications where heat transfer is required, such as in heat exchangers and cooking appliances.
Types of Iron
Iron is primarily classified into four main categories based on its carbon content and the type of processing used to refine it. These categories include cast iron, wrought iron, steel, and various iron alloys.
1. Cast Iron
Cast iron is one of the oldest and most widely used forms of iron. It is made by melting iron and adding a significant amount of carbon, typically between 2% and 4%. This high carbon content makes cast iron brittle, but it also imparts several desirable properties, such as excellent castability, wear resistance, and a high level of fluidity when molten.
Cast iron is commonly produced by pouring the molten iron into molds, which harden as they cool. The resulting cast iron products can be further machined, but the material itself is generally not amenable to significant shaping once it has solidified. Cast iron is often used in the manufacturing of pipes, engine blocks, cookware, and construction components due to its ability to withstand high temperatures and its good corrosion resistance.
There are several types of cast iron, each with distinct properties and uses:
- Gray Cast Iron: This is the most common type of cast iron, characterized by its gray color when fractured. It contains graphite flakes, which act as lubricants, reducing friction and improving machinability. Gray cast iron is often used in engine blocks, pipes, and structural components because of its excellent castability and wear resistance.
- White Cast Iron: White cast iron is hard and brittle due to the lack of graphite and the presence of cementite, an iron-carbon compound. It is often used for high-wear applications, such as in the production of grinding media and crushers.
- Ductile Iron: Also known as nodular cast iron or spheroidal graphite iron, ductile iron is produced by adding small amounts of magnesium to the molten iron. This results in the formation of graphite in the form of spheres rather than flakes, improving the material’s ductility and strength. Ductile iron is used in the manufacturing of automotive components, pipes, and heavy machinery parts.
- Malleable Iron: Malleable iron is produced by heat treating white cast iron to convert the cementite into graphite. It is more ductile than white cast iron and is used for applications requiring higher strength and impact resistance, such as in automotive components and industrial machinery.
2. Wrought Iron
Wrought iron is a type of iron that is worked by hand or machine, typically at elevated temperatures, to create a solid, malleable material. It is low in carbon, usually containing less than 0.08% carbon, making it highly ductile and resistant to corrosion. Wrought iron is forged by hammering or rolling to shape it into various forms, and it has a fibrous texture that imparts additional strength and flexibility.
Historically, wrought iron was used for a wide range of products, including structural components, tools, and decorative elements such as gates and railings. It is still used in specialized applications today, such as in the creation of ornamental designs and architectural details.
Due to its high ductility and resistance to corrosion, wrought iron is ideal for applications where strength and flexibility are needed. It was widely used in the construction of buildings, bridges, and ships, especially in the 18th and 19th centuries.
3. Steel
Steel is an alloy of iron and carbon, with carbon content typically ranging from 0.02% to 2%. It is one of the most important materials in modern industry due to its strength, durability, and versatility. Steel is produced by refining pig iron (which is made by reducing iron ore in a blast furnace) and removing impurities such as sulfur, phosphorus, and carbon.
There are many different types of steel, each designed for specific applications. The most common types of steel include:
- Carbon Steel: Carbon steel is a broad category of steel that includes low-carbon, medium-carbon, and high-carbon steels. Low-carbon steel is easy to form and is used in applications such as automotive body panels, structural beams, and pipes. High-carbon steel is harder and stronger, making it suitable for tools, knives, and industrial machinery.
- Alloy Steel: Alloy steel is made by adding elements such as chromium, nickel, molybdenum, or vanadium to improve specific properties like corrosion resistance, strength, or hardness. Stainless steel, for example, is a type of alloy steel that contains at least 10.5% chromium, making it resistant to rust and corrosion. Alloy steels are widely used in the aerospace, automotive, and manufacturing industries.
- Tool Steel: Tool steel is a group of high-carbon steels specifically designed for making tools, dies, and other precision machinery components. These steels are known for their hardness, wear resistance, and ability to retain a sharp edge, making them ideal for cutting, drilling, and shaping metals.
- Stainless Steel: Stainless steel is a special type of alloy steel that contains a minimum of 10.5% chromium, which helps prevent rust and corrosion. It is used in a variety of industries, including food processing, pharmaceuticals, architecture, and medical devices, due to its resistance to corrosion, stain, and rust.
- High-Speed Steel (HSS): High-speed steel is a form of tool steel that retains its hardness and strength even at elevated temperatures. It is used primarily in the manufacturing of cutting tools, such as drills and lathe tools, where high heat and stress are present.
4. Iron Alloys
In addition to the basic forms of cast iron, wrought iron, and steel, there are numerous specialized iron alloys designed to enhance particular properties. These alloys typically contain iron combined with other metals or non-metals to create materials with unique characteristics.
Some common iron alloys include:
- Nickel-Iron Alloys: These alloys are made by combining iron with nickel to create materials with enhanced strength, corrosion resistance, and thermal stability. Nickel-iron alloys are used in applications such as electrical components and heat exchangers.
- Cobalt-Iron Alloys: Cobalt-iron alloys are known for their high magnetic properties, making them useful in the production of electrical and magnetic components. These alloys are commonly used in the aerospace and electronics industries.
- Manganese-Iron Alloys: Manganese is often added to iron to improve its strength and wear resistance. Manganese steel is used in high-impact and heavy-duty applications, such as in railroad tracks, mining equipment, and crushers.
- Aluminum-Iron Alloys: By adding aluminum to iron, alloys with improved corrosion resistance and lightweight properties can be created. These alloys are used in the automotive and aerospace industries for making lightweight structural components.
Uses of Iron
Iron and its alloys have a wide range of uses in numerous industries. The specific properties of each type of iron determine its suitability for particular applications.
- Construction: Iron and steel are fundamental materials in construction, used in everything from structural beams and columns to reinforcing bars and concrete. Steel is used in the construction of buildings, bridges, and other infrastructure due to its strength, durability, and versatility.
- Transportation: Iron and steel are used extensively in the manufacture of vehicles, including cars, trucks, trains, and ships. Steel is also used to produce rail tracks, airplane components, and automotive engines.
- Manufacturing: Iron alloys are used in a variety of manufacturing processes, including the production of machinery, tools, and industrial equipment. Steel is particularly important in the manufacturing of heavy machinery, including presses, turbines, and construction equipment.
- Cookware: Cast iron, especially in the form of cookware, is prized for its heat retention and even cooking properties. Cast iron skillets, Dutch ovens, and griddles are popular items in kitchens worldwide.
- Medical Devices: Steel, particularly stainless steel, is widely used in medical devices, including surgical instruments, implants, and prosthetics, due to its corrosion resistance and biocompatibility.
- Energy Production: Iron and steel are used in the production of energy infrastructure, such as pipelines, wind turbines, and boilers. The materials’ strength and durability make them ideal for use in environments subject to high pressures and temperatures.
Conclusion
Iron is an incredibly versatile and important material that has shaped human civilization for millennia. Through its various forms, such as cast iron, wrought iron, steel, and iron alloys, it has contributed to countless technological advancements in industries ranging from construction to aerospace. The wide range of properties exhibited by different types of iron, including strength, flexibility, corrosion resistance, and magnetic characteristics, make it an indispensable resource. Understanding the different types of iron and their unique properties is essential for selecting the right material for any application, ensuring both performance and durability across various industries.
Maximize Tooling and CNC Metal Spinning Capabilities.
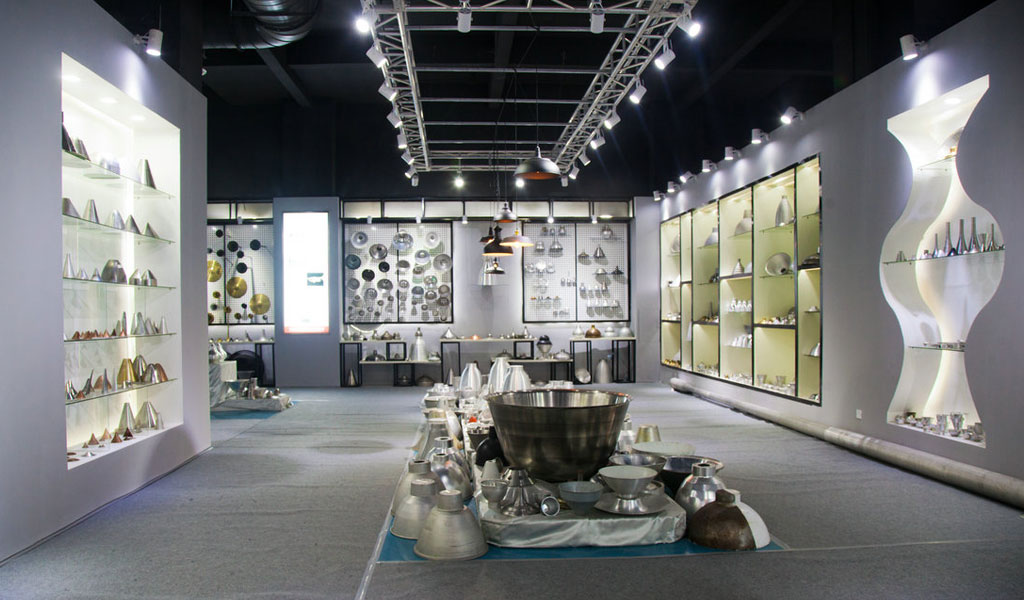
At BE-CU China Metal Spinning company, we make the most of our equipment while monitoring signs of excess wear and stress. In addition, we look into newer, modern equipment and invest in those that can support or increase our manufacturing capabilities. Our team is very mindful of our machines and tools, so we also routinely maintain them to ensure they don’t negatively impact your part’s quality and productivity.
Talk to us today about making a rapid prototype with our CNC metal spinning service. Get a direct quote by chatting with us here or request a free project review.
BE-CU China CNC Metal Spinning service include : CNC Metal Spinning,Metal Spinning Die,Laser Cutting, Tank Heads Spinning,Metal Hemispheres Spinning,Metal Cones Spinning,Metal Dish-Shaped Spinning,Metal Trumpet Spinning,Metal Venturi Spinning,Aluminum Spinning Products,Stainless Steel Spinning Products,Copper Spinning Products,Brass Spinning Products,Steel Spinning Product,Metal Spinnin LED Reflector,Metal Spinning Pressure Vessel,