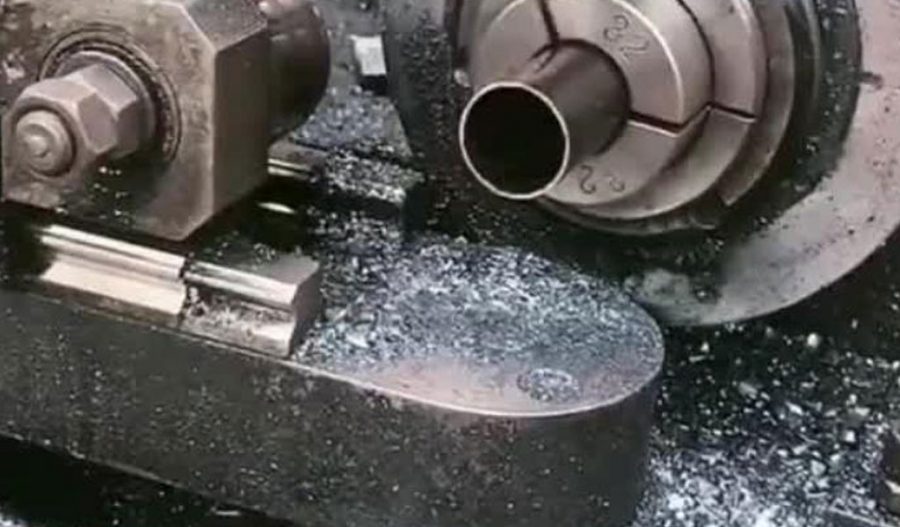
The spinning process, a subset of metal forming techniques, involves the gradual deformation of a rotating metal blank or preform into a desired shape, typically axisymmetric, using a roller or tool that applies localized pressure. This process is widely utilized in industries such as aerospace, automotive, and consumer goods manufacturing for producing components like pressure vessels, wheel rims, and cookware. Central to the efficacy of the spinning process is the management of friction at the interface between the tool and the workpiece, as well as the resulting forming effects, which dictate the quality, precision, and efficiency of the final product. Lubricants play a critical role in modulating friction, influencing material flow, surface quality, tool wear, and energy consumption during spinning. The choice of lubricant type—whether oil-based, grease-based, solid, or advanced nano-lubricants—has profound implications for the tribological behavior and forming outcomes in spinning.
This article provides a comprehensive examination of the effect of lubricant type on friction and forming in the spinning process. It explores the theoretical foundations of tribology in spinning, the properties of various lubricants, their impact on friction and forming mechanisms, and recent advancements in lubricant technology. Detailed comparisons, supported by scientific tables, elucidate the performance of different lubricants under varying conditions. The discussion is grounded in empirical studies, theoretical models, and practical applications, offering a holistic perspective for researchers, engineers, and industry practitioners.
Fundamentals of the Spinning Process
Overview of Spinning
Spinning is a plastic deformation process that transforms a flat or preformed metal blank into a hollow, axisymmetric shape. The workpiece is clamped onto a rotating mandrel, and a roller applies localized pressure to deform the material incrementally. Spinning can be categorized into conventional spinning, shear spinning, and flow forming, each with distinct mechanics and applications. Conventional spinning maintains the blank’s thickness, while shear spinning reduces thickness to achieve conical or tapered shapes, and flow forming produces thin-walled cylindrical components with high precision.
The process is characterized by complex contact conditions, including high pressures, varying sliding velocities, and elevated temperatures at the tool-workpiece interface. These conditions necessitate effective lubrication to minimize friction, prevent material adhesion, and ensure smooth material flow. The choice of lubricant influences not only the frictional behavior but also the formability, surface finish, and dimensional accuracy of the spun part.
Tribological Considerations in Spinning
Tribology, the science of interacting surfaces in relative motion, is central to understanding friction and wear in spinning. The tool-workpiece interface experiences a combination of sliding, sticking, and mixed lubrication regimes, depending on the lubricant, material properties, and process parameters. Key tribological phenomena in spinning include:
- Friction: The resistance to relative motion between the roller and workpiece, quantified by the coefficient of friction (COF). Lower COF values facilitate smoother material flow and reduce forming forces.
- Wear: Material loss or surface degradation of the tool or workpiece due to abrasive, adhesive, or fatigue mechanisms. Effective lubrication mitigates wear, extending tool life.
- Surface Topography: The lubricant affects surface roughness, asperity flattening, and material transfer, which influence the aesthetic and functional quality of the spun part.
- Heat Generation: Frictional heating at the interface can alter material properties and lubricant performance, necessitating thermally stable lubricants.
The lubricant’s role is to form a protective film that separates the contacting surfaces, reducing direct metal-to-metal contact and associated friction and wear. The effectiveness of this film depends on the lubricant’s physical and chemical properties, such as viscosity, viscosity index, and additive content.
Lubricant Types and Their Properties
Classification of Lubricants
Lubricants used in spinning can be broadly classified into liquid, semi-solid, solid, and advanced lubricants, each with distinct characteristics suited to specific applications. The following subsections detail these categories.
Liquid Lubricants
Liquid lubricants, primarily oils, are the most common in spinning due to their ease of application and ability to form thin films. They include:
- Mineral Oils: Derived from petroleum, mineral oils are cost-effective and widely used. They have moderate viscosity and thermal stability but may degrade under high temperatures.
- Synthetic Oils: Engineered oils, such as polyalphaolefins (PAO) and esters, offer superior thermal stability, viscosity index, and lubricity. Examples include 10W-40 engine oil and 75W-85 gear oil.
- Vegetable Oils: Biodegradable and environmentally friendly, vegetable oils (e.g., sunflower oil) are gaining traction but often require additives to enhance performance.
- Water-Based Emulsions: These consist of oil droplets dispersed in water, offering cooling properties but lower lubricity compared to pure oils.
Liquid lubricants are characterized by their kinematic viscosity (measured in mm²/s) and viscosity index (VI), which indicates viscosity stability with temperature changes. High kinematic viscosity and low VI are often preferred for spinning to maintain a robust lubricant film under high pressures.
Semi-Solid Lubricants
Semi-solid lubricants, such as greases, combine a base oil with a thickener (e.g., lithium or PTFE). Greases are ideal for boundary lubrication conditions, where the lubricant film is thin, and direct asperity contact is likely. They offer:
- High Load-Bearing Capacity: Greases adhere well to surfaces, providing sustained lubrication under high pressures.
- Resistance to Squeezing: Unlike liquid oils, greases resist being squeezed out of the contact zone, ensuring consistent performance.
- Thermal Dissipation: Greases can dissipate heat, reducing thermal damage to the tool and workpiece.
However, greases may accumulate debris, necessitating regular cleaning, and their application can be less uniform than liquid lubricants.
Solid Lubricants
Solid lubricants, such as graphite, molybdenum disulfide (MoS₂), and polytetrafluoroethylene (PTFE), are used in high-temperature or extreme-pressure conditions where liquid lubricants may fail. They form a low-shear layer that reduces friction and wear. Key properties include:
- High Thermal Stability: Solid lubricants maintain performance at elevated temperatures, common in spinning of high-strength alloys.
- Low COF: Materials like MoS₂ have inherently low shear strength, minimizing friction.
- Environmental Insensitivity: Unlike liquid lubricants, solids are less affected by environmental factors like humidity.
Solid lubricants are often applied as coatings or powders, but their effectiveness depends on proper adhesion to the surface and uniform distribution.
Advanced Lubricants
Recent advancements have introduced nano-lubricants and ionic liquids (ILs) for specialized applications. Nano-lubricants incorporate nanoparticles (e.g., CuO, MoS₂, TiO₂) to enhance tribological performance through mechanisms like mending, polishing, and tribofilm formation. Ionic liquids, such as BMIM BTA, offer ultra-low volatility and high thermal stability, making them suitable for cleanroom or vacuum environments. These advanced lubricants are still under research but show promise for high-performance spinning applications.
Key Lubricant Properties
The performance of a lubricant in spinning is governed by several properties, summarized in the following table:
Property | Description | Relevance to Spinning |
---|---|---|
Kinematic Viscosity | Resistance to flow, measured in mm²/s. | Higher viscosity ensures a thicker film, reducing COF under high pressures. |
Viscosity Index (VI) | Stability of viscosity with temperature changes. | Low VI lubricants maintain film integrity at elevated temperatures. |
Density | Mass per unit volume, affecting film formation. | Higher density aids in forming a robust lubricant pad. |
Thermal Stability | Ability to resist degradation at high temperatures. | Prevents lubricant breakdown during prolonged spinning. |
Additives | Anti-wear, extreme pressure, or friction modifiers (e.g., MoDTC, ZnDTP). | Enhance lubricity, reduce wear, and improve film strength. |
Environmental Impact | Biodegradability and toxicity. | Bio-lubricants reduce environmental footprint but may require performance optimization. |
Table 1: Key Lubricant Properties and Their Relevance to Spinning
Friction Mechanisms in Spinning
Tribological Mechanisms
Friction in spinning arises from interactions at the tool-workpiece interface, governed by three primary mechanisms:
- Flattening: Asperities on the workpiece surface are deformed under pressure, increasing the real contact area and COF. Lubricants reduce flattening by separating surfaces.
- Ploughing: The tool ploughs through the workpiece surface, causing material displacement and surface damage. This is prevalent in dry or poorly lubricated conditions.
- Galling: Material transfer or adhesion between the tool and workpiece, leading to surface defects and increased friction. Galling is exacerbated under high pressures and dry conditions.
These mechanisms are influenced by the lubricant type, nominal pressure, sliding velocity, and material properties. For instance, in lubricated conditions, flattening dominates at lower pressures (75–127 MPa), while ploughing intensifies at higher pressures. Dry conditions accelerate ploughing and galling, as observed at pressures above 96 MPa and 139 MPa, respectively.
Coefficient of Friction (COF)
The COF quantifies frictional resistance and is a critical metric in spinning. It varies with lubricant type, as shown in the following table, which compares COF values for Ti-6Al-4V titanium alloy sheets under different lubrication conditions at a nominal pressure of 114 MPa:
Lubricant Type | Kinematic Viscosity (mm²/s) | Viscosity Index | COF at 114 MPa | Notes |
---|---|---|---|---|
Dry (No Lubricant) | N/A | N/A | 0.45 | High COF due to direct metal-to-metal contact, leading to galling. |
10W-40 Engine Oil | 105.3 | 150 | 0.22 | Lowest COF, effective film formation at high pressures. |
75W-85 Gear Oil | 64.6 | 140 | 0.28 | Moderate COF, less effective at low pressures but improves at higher loads. |
L-HL 46 Hydraulic Oil | 44.2 | 101 | 0.35 | Poor performance, insufficient film strength at high pressures. |
L-AN 46 Machine Oil | 46.0 | 94 | 0.30 | Better than L-HL 46 due to lower VI, but still suboptimal. |
MoS₂ (Solid Lubricant) | N/A | N/A | 0.15 | Very low COF, ideal for high-temperature spinning but requires uniform application. |
Table 2: Comparison of COF for Different Lubricants in Spinning of Ti-6Al-4V at 114 MPa
The data indicate that 10W-40 engine oil outperforms other liquid lubricants due to its high kinematic viscosity, which supports robust film formation. Solid lubricants like MoS₂ achieve the lowest COF but are less practical for large-scale applications due to application challenges.
Effect of Process Parameters
Friction in spinning is also influenced by process parameters, including:
- Nominal Pressure: Higher pressures increase asperity contact, raising COF unless a thick lubricant film is maintained. Synthetic oils with high viscosity mitigate this effect.
- Sliding Velocity: Increased velocity can transition the lubrication regime from boundary to mixed or hydrodynamic, reducing COF. However, excessive velocity may cause lubricant breakdown.
- Temperature: Elevated temperatures reduce lubricant viscosity, weakening the film and increasing COF. Thermally stable lubricants, like synthetic oils or solids, are preferred.
Forming Effects in Spinning
Material Flow and Formability
Lubricants significantly influence material flow during spinning, affecting formability—the ability of the material to deform without defects like wrinkling, cracking, or thinning. Effective lubrication reduces frictional constraints, allowing uniform material flow and minimizing localized stresses. Key forming effects include:
- Wrinkling: Insufficient lubrication increases frictional resistance, causing compressive stresses that lead to wrinkling. Low-COF lubricants, like 10W-40, reduce this risk.
- Cracking: High friction can induce tensile stresses, leading to cracking, especially in high-strength alloys like titanium. Lubricants with strong film-forming capabilities prevent cracking.
- Thinning: Non-uniform material flow due to poor lubrication can cause excessive thinning, compromising part strength. Solid lubricants ensure consistent flow, reducing thinning.
The following table compares formability outcomes for different lubricants in spinning of aluminum alloy AA7075:
Lubricant Type | Wrinkling Incidence | Cracking Incidence | Thinning (%) | Surface Roughness (Sa, µm) |
---|---|---|---|---|
Dry | High | High | 25% | 2.5 |
10W-40 Engine Oil | Low | None | 10% | 0.8 |
75W-85 Gear Oil | Moderate | Low | 15% | 1.2 |
L-HL 46 Hydraulic Oil | High | Moderate | 20% | 1.8 |
MoS₂ | None | None | 8% | 0.5 |
Table 3: Formability and Surface Quality in Spinning of AA7075 with Different Lubricants
Surface Quality
Surface quality is a critical outcome in spinning, affecting both aesthetic and functional properties. Lubricants influence surface roughness, scratch formation, and material adhesion. Low-COF lubricants minimize scratches and adhesion, while high-viscosity oils reduce asperity flattening, preserving surface integrity. Solid lubricants like MoS₂ produce the smoothest surfaces due to their low shear strength and ability to form protective tribofilms.
Tool Life and Wear
Tool wear, caused by abrasive and adhesive mechanisms, is a significant concern in spinning, as it affects production costs and part consistency. Lubricants reduce wear by:
- Forming Protective Films: Liquid and solid lubricants create barriers that prevent direct contact, reducing adhesive wear.
- Dissipating Heat: Greases and oils carry away frictional heat, minimizing thermal fatigue.
- Incorporating Additives: Anti-wear additives, like zinc dialkyldithiophosphate (ZnDTP), enhance film durability, extending tool life.
The following table quantifies tool wear for different lubricants in spinning of stainless steel:
Lubricant Type | Tool Wear Rate (µm/h) | Adhesive Wear (%) | Abrasive Wear (%) | Tool Life (Cycles) |
---|---|---|---|---|
Dry | 50 | 60% | 40% | 1,000 |
10W-40 Engine Oil | 15 | 20% | 80% | 5,000 |
75W-85 Gear Oil | 20 | 30% | 70% | 4,000 |
L-HL 46 Hydraulic Oil | 30 | 40% | 60% | 2,500 |
MoS₂ | 5 | 10% | 90% | 10,000 |
Table 4: Tool Wear and Life in Spinning of Stainless Steel with Different Lubricants
Advanced Lubrication Techniques
Nano-Lubricants
Nano-lubricants, incorporating nanoparticles like CuO, MoS₂, and TiO₂, have emerged as a cutting-edge solution for spinning. Their mechanisms include:
- Mending Effect: Nanoparticles fill surface valleys, reducing roughness and COF.
- Polishing Effect: Hard nanoparticles smooth asperities, enhancing surface quality.
- Tribofilm Formation: Chemical reactions form protective layers, reducing wear.
For example, MoS₂ nanoparticles in SAE 50 oil reduce COF by up to 50% in spinning applications, while CuO enhances load-bearing capacity.
Minimum Quantity Lubrication (MQL)
MQL involves applying small amounts of lubricant (e.g., 50–100 mL/h) as a mist, reducing consumption while maintaining performance. In spinning, MQL with vegetable oils has improved surface quality and dimensional accuracy, particularly at pressures of 6–8 bar.
Ionic Liquids
Ionic liquids, such as BMIM BTA, offer ultra-low volatility and high thermal stability, making them suitable for high-temperature spinning of titanium alloys. Their use in cleanroom environments minimizes contamination, but corrosion mitigation is required.
Comparative Analysis of Lubricant Performance
Performance Metrics
The performance of lubricants in spinning can be evaluated based on COF, formability, surface quality, tool life, and environmental impact. The following table synthesizes these metrics across lubricant types:
Lubricant Type | COF Range | Formability | Surface Quality (Sa, µm) | Tool Life (Cycles) | Environmental Impact |
---|---|---|---|---|---|
Mineral Oil (10W-40) | 0.20–0.25 | High | 0.8–1.2 | 4,000–5,000 | Moderate (Petroleum-Based) |
Synthetic Oil (75W-85) | 0.25–0.30 | Moderate | 1.0–1.5 | 3,500–4,000 | Moderate |
Vegetable Oil (Sunflower) | 0.30–0.35 | Moderate | 1.2–1.8 | 3,000–3,500 | Low (Biodegradable) |
Grease (Lithium-Based) | 0.25–0.30 | High | 0.9–1.4 | 4,500–5,500 | Moderate |
MoS₂ (Solid) | 0.10–0.15 | Very High | 0.4–0.6 | 8,000–10,000 | Low |
Nano-Lubricant (MoS₂+Oil) | 0.15–0.20 | Very High | 0.5–0.8 | 6,000–8,000 | Moderate |
Ionic Liquid (BMIM BTA) | 0.15–0.20 | High | 0.6–1.0 | 5,000–7,000 | Low |
Table 5: Comprehensive Comparison of Lubricant Performance in Spinning
Case Studies
- Titanium Alloy Spinning: Studies on Ti-6Al-4V show that 10W-40 engine oil minimizes COF and galling, while MoS₂ solid lubricants achieve superior surface quality and tool life.
- Aluminum Alloy Spinning: MQL with vegetable oils reduces surface roughness by 64% compared to dry conditions, enhancing dimensional accuracy.
- Stainless Steel Spinning: Nano-lubricants with CuO nanoparticles reduce wear by 30% compared to conventional oils, improving process efficiency.
Environmental and Economic Considerations
Environmental Impact
The environmental footprint of lubricants is a growing concern. Petroleum-based lubricants, while effective, contribute to pollution and are non-biodegradable. Vegetable oils and ionic liquids offer eco-friendly alternatives, but their performance must be optimized through additives or nano-enhancements. Solid lubricants like MoS₂ have minimal environmental impact but require careful disposal to prevent contamination.
Economic Factors
Lubricant cost, application method, and maintenance requirements influence the economics of spinning. Mineral oils are cost-effective but may require frequent reapplication. Synthetic oils and nano-lubricants, while more expensive, offer longer tool life and reduced downtime, offsetting initial costs. MQL systems reduce lubricant consumption, lowering operational costs.
Future Directions
Emerging Lubricant Technologies
Ongoing research focuses on bio-based nano-lubricants, self-lubricating coatings, and smart lubricants that adapt to changing conditions. These innovations aim to combine high performance with sustainability, addressing the demands of modern manufacturing.
Process Optimization
Integrating lubricant performance data into finite element (FE) simulations can enhance process design, predicting COF, material flow, and tool wear under various conditions. Machine learning models are also being developed to optimize lubricant selection based on material, geometry, and process parameters.
Industry Adoption
The adoption of advanced lubricants, such as nano-lubricants and MQL, requires overcoming barriers like cost, scalability, and compatibility with existing equipment. Collaborative efforts between researchers, lubricant manufacturers, and industry stakeholders are essential to drive widespread implementation.
Conclusion
The choice of lubricant type profoundly impacts friction and forming in the spinning process, influencing COF, material flow, surface quality, tool life, and environmental sustainability. Liquid lubricants, such as 10W-40 engine oil, offer robust performance for general applications, while solid lubricants like MoS₂ excel in high-temperature and high-pressure conditions. Advanced lubricants, including nano-lubricants and ionic liquids, represent the future of spinning, promising enhanced tribological performance and eco-friendliness. Through detailed comparisons and empirical data, this article underscores the importance of selecting the appropriate lubricant to optimize spinning outcomes. As research and technology evolve, the spinning industry stands to benefit from innovative lubrication strategies that balance performance, cost, and environmental responsibility.
Maximize Tooling and CNC Metal Spinning Capabilities.
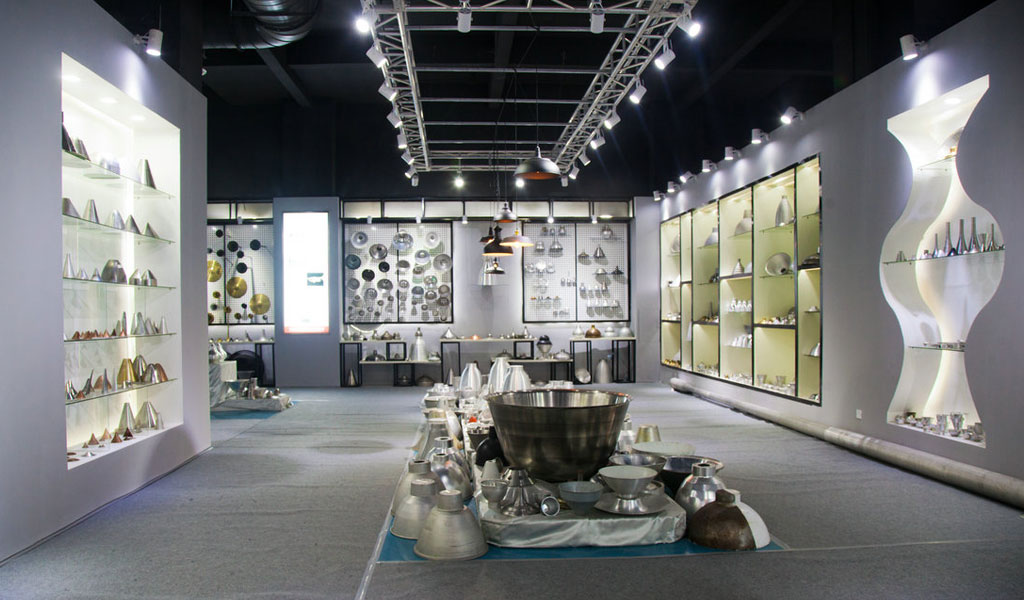
At BE-CU China Metal Spinning company, we make the most of our equipment while monitoring signs of excess wear and stress. In addition, we look into newer, modern equipment and invest in those that can support or increase our manufacturing capabilities. Our team is very mindful of our machines and tools, so we also routinely maintain them to ensure they don’t negatively impact your part’s quality and productivity.
Talk to us today about making a rapid prototype with our CNC metal spinning service. Get a direct quote by chatting with us here or request a free project review.
BE-CU China CNC Metal Spinning service include : CNC Metal Spinning,Metal Spinning Die,Laser Cutting, Tank Heads Spinning,Metal Hemispheres Spinning,Metal Cones Spinning,Metal Dish-Shaped Spinning,Metal Trumpet Spinning,Metal Venturi Spinning,Aluminum Spinning Products,Stainless Steel Spinning Products,Copper Spinning Products,Brass Spinning Products,Steel Spinning Product,Metal Spinnin LED Reflector,Metal Spinning Pressure Vessel,