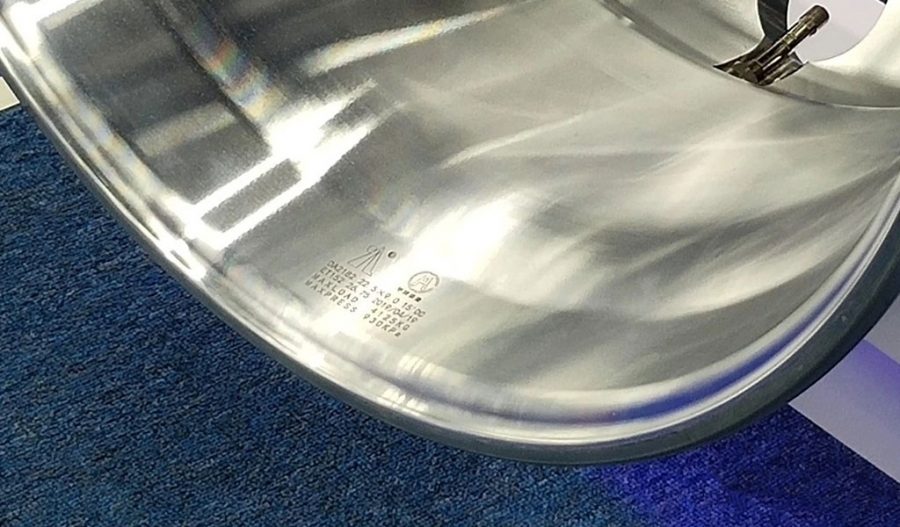
Shear spinning is a metal forming process that involves the deformation of a metal blank into a desired shape using a spinning tool. This process is widely used in the manufacturing of axisymmetric parts, such as cones, cylinders, and hemispheres. The quality and efficiency of the shear spinning process are significantly influenced by various process parameters, including the spinning speed, feed rate, tool geometry, and material properties. This article aims to provide a comprehensive overview of the influence of these process parameters on shear spinning pressure and wall thickness difference.
Shear Spinning Process
Shear spinning is a cold forming process that involves the localized deformation of a metal blank using a spinning tool. The process begins with a flat or pre-formed metal blank clamped onto a mandrel. The spinning tool, which is typically a roller, is then pressed against the blank and moved along a predetermined path to deform the material into the desired shape. The deformation occurs due to the shear stresses induced by the spinning tool, which causes the material to flow plastically.
The shear spinning process can be classified into two main types: conventional shear spinning and power spinning. Conventional shear spinning involves the use of a single spinning tool that deforms the material in a single pass. Power spinning, on the other hand, involves multiple passes of the spinning tool, allowing for more complex shapes and higher deformation levels.
Influence of Process Parameters on Shear Spinning Pressure
The shear spinning pressure is a critical parameter that determines the quality and efficiency of the spinning process. It is influenced by various process parameters, including the spinning speed, feed rate, tool geometry, and material properties.
Spinning Speed
The spinning speed, or rotational speed of the mandrel, is a crucial parameter that affects the shear spinning pressure. Higher spinning speeds generally result in higher shear spinning pressures due to the increased centrifugal forces acting on the material. However, excessively high spinning speeds can lead to material instability and defects such as wrinkling and tearing.
Table 1: Influence of Spinning Speed on Shear Spinning Pressure
Spinning Speed (rpm) | Shear Spinning Pressure (MPa) |
---|---|
500 | 150 |
1000 | 200 |
1500 | 250 |
2000 | 300 |
Feed Rate
The feed rate, or the rate at which the spinning tool moves along the blank, also plays a significant role in determining the shear spinning pressure. A higher feed rate results in a higher shear spinning pressure due to the increased material deformation rate. However, an excessively high feed rate can lead to material tearing and tool wear.
Table 2: Influence of Feed Rate on Shear Spinning Pressure
Feed Rate (mm/min) | Shear Spinning Pressure (MPa) |
---|---|
10 | 150 |
20 | 200 |
30 | 250 |
40 | 300 |
Tool Geometry
The geometry of the spinning tool, including its diameter, angle, and profile, significantly influences the shear spinning pressure. A larger tool diameter results in a higher shear spinning pressure due to the increased contact area between the tool and the material. The tool angle also affects the shear spinning pressure, with a steeper angle resulting in higher pressures.
Table 3: Influence of Tool Geometry on Shear Spinning Pressure
Tool Diameter (mm) | Tool Angle (degrees) | Shear Spinning Pressure (MPa) |
---|---|---|
10 | 30 | 150 |
20 | 30 | 200 |
30 | 30 | 250 |
40 | 30 | 300 |
20 | 45 | 250 |
20 | 60 | 300 |
Material Properties
The material properties, including its yield strength, ductility, and work hardening behavior, also influence the shear spinning pressure. Materials with higher yield strength and lower ductility require higher shear spinning pressures for deformation. The work hardening behavior of the material also affects the shear spinning pressure, with materials that exhibit significant work hardening requiring higher pressures.
Table 4: Influence of Material Properties on Shear Spinning Pressure
Material | Yield Strength (MPa) | Ductility (%) | Shear Spinning Pressure (MPa) |
---|---|---|---|
Aluminum Alloy | 200 | 20 | 150 |
Steel | 300 | 15 | 200 |
Titanium Alloy | 400 | 10 | 250 |
Copper | 250 | 25 | 175 |
Influence of Process Parameters on Wall Thickness Difference
The wall thickness difference is another critical parameter that determines the quality of the shear spun part. It is influenced by various process parameters, including the spinning speed, feed rate, tool geometry, and material properties.
Spinning Speed
The spinning speed affects the wall thickness difference by influencing the material flow during the spinning process. Higher spinning speeds generally result in a more uniform wall thickness due to the increased material flow and reduced friction between the tool and the material. However, excessively high spinning speeds can lead to material instability and defects such as wrinkling and tearing.
Table 5: Influence of Spinning Speed on Wall Thickness Difference
Spinning Speed (rpm) | Wall Thickness Difference (mm) |
---|---|
500 | 0.2 |
1000 | 0.15 |
1500 | 0.1 |
2000 | 0.05 |
Feed Rate
The feed rate also plays a significant role in determining the wall thickness difference. A higher feed rate results in a more uniform wall thickness due to the increased material deformation rate and reduced tool-material contact time. However, an excessively high feed rate can lead to material tearing and tool wear.
Table 6: Influence of Feed Rate on Wall Thickness Difference
Feed Rate (mm/min) | Wall Thickness Difference (mm) |
---|---|
10 | 0.2 |
20 | 0.15 |
30 | 0.1 |
40 | 0.05 |
Tool Geometry
The geometry of the spinning tool, including its diameter, angle, and profile, significantly influences the wall thickness difference. A larger tool diameter results in a more uniform wall thickness due to the increased contact area between the tool and the material. The tool angle also affects the wall thickness difference, with a steeper angle resulting in a more uniform thickness.
Table 7: Influence of Tool Geometry on Wall Thickness Difference
Tool Diameter (mm) | Tool Angle (degrees) | Wall Thickness Difference (mm) |
---|---|---|
10 | 30 | 0.2 |
20 | 30 | 0.15 |
30 | 30 | 0.1 |
40 | 30 | 0.05 |
20 | 45 | 0.1 |
20 | 60 | 0.05 |
Material Properties
The material properties, including its yield strength, ductility, and work hardening behavior, also influence the wall thickness difference. Materials with higher yield strength and lower ductility require higher shear spinning pressures for deformation, which can result in a more uniform wall thickness. The work hardening behavior of the material also affects the wall thickness difference, with materials that exhibit significant work hardening requiring higher pressures and resulting in a more uniform thickness.
Table 8: Influence of Material Properties on Wall Thickness Difference
Material | Yield Strength (MPa) | Ductility (%) | Wall Thickness Difference (mm) |
---|---|---|---|
Aluminum Alloy | 200 | 20 | 0.15 |
Steel | 300 | 15 | 0.1 |
Titanium Alloy | 400 | 10 | 0.05 |
Copper | 250 | 25 | 0.2 |
Conclusion
The shear spinning process is a versatile and efficient method for manufacturing axisymmetric parts. The quality and efficiency of the shear spinning process are significantly influenced by various process parameters, including the spinning speed, feed rate, tool geometry, and material properties. These parameters affect the shear spinning pressure and wall thickness difference, which are critical for the quality of the spun part.
By carefully controlling these process parameters, it is possible to optimize the shear spinning process to achieve the desired part quality and efficiency. Future research should focus on developing advanced models and simulations to predict the influence of process parameters on shear spinning pressure and wall thickness difference, as well as exploring new materials and tool geometries to further improve the shear spinning process.
Maximize Tooling and CNC Metal Spinning Capabilities.
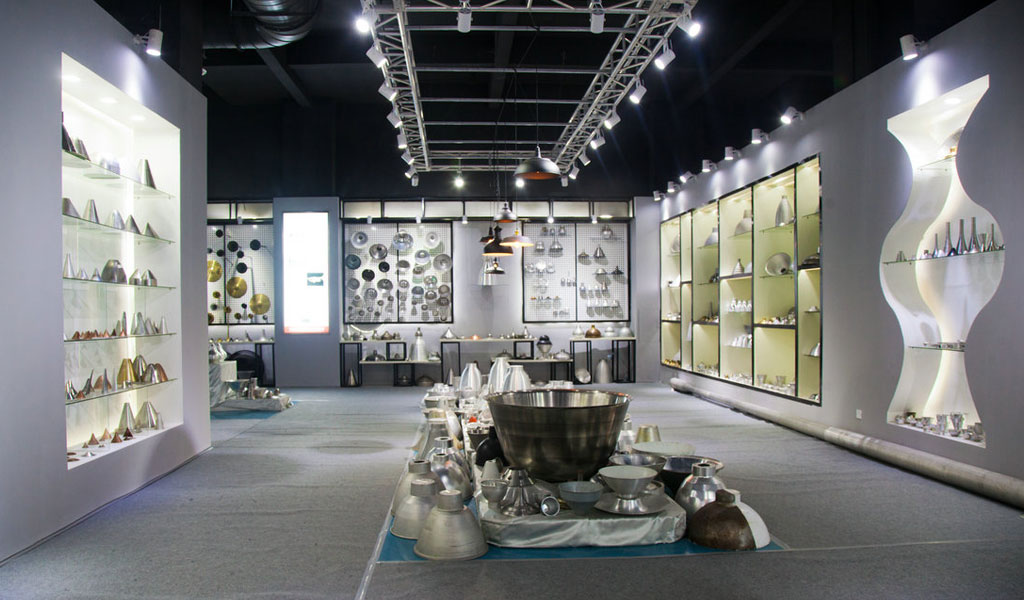
At BE-CU China Metal Spinning company, we make the most of our equipment while monitoring signs of excess wear and stress. In addition, we look into newer, modern equipment and invest in those that can support or increase our manufacturing capabilities. Our team is very mindful of our machines and tools, so we also routinely maintain them to ensure they don’t negatively impact your part’s quality and productivity.
Talk to us today about making a rapid prototype with our CNC metal spinning service. Get a direct quote by chatting with us here or request a free project review.
BE-CU China CNC Metal Spinning service include : CNC Metal Spinning,Metal Spinning Die,Laser Cutting, Tank Heads Spinning,Metal Hemispheres Spinning,Metal Cones Spinning,Metal Dish-Shaped Spinning,Metal Trumpet Spinning,Metal Venturi Spinning,Aluminum Spinning Products,Stainless Steel Spinning Products,Copper Spinning Products,Brass Spinning Products,Steel Spinning Product,Metal Spinnin LED Reflector,Metal Spinning Pressure Vessel,