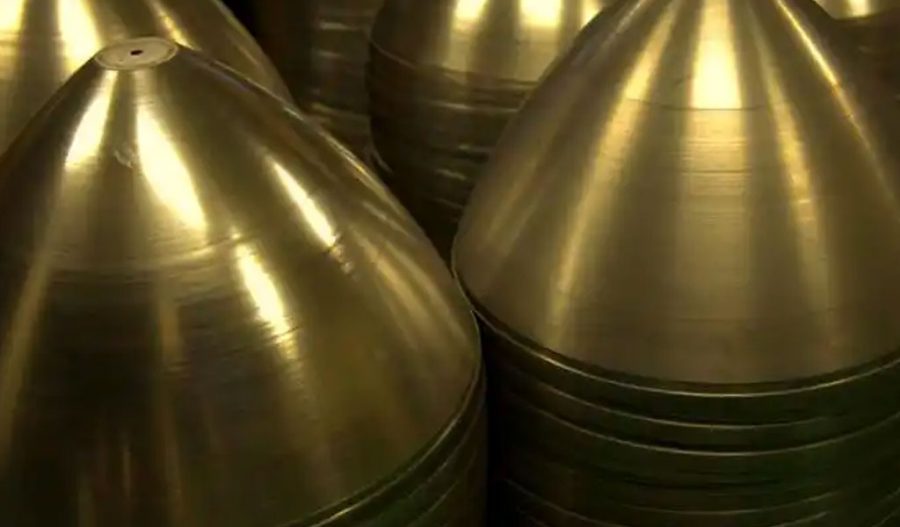
Metal spinning, also known as spin forming or metal turning, is a metalworking process that involves rotating a metal disc or tube at high speed to form axially symmetric parts. This chipless forming technique, which dates back to ancient civilizations such as Egypt and China, has evolved into a sophisticated manufacturing method widely used in industries ranging from aerospace to automotive and consumer goods. The process typically employs a lathe, where a metal blank is clamped against a mandrel (or die) and shaped by a spinning wheel or roller that applies localized force to deform the material over the die. The quality, efficiency, and mechanical properties of the spun part depend on several process parameters, including the mandrel speed, feed rate, roller geometry, and, critically, the gap between the spinning wheel and the die.
The gap between the spinning wheel and the die, often referred to as the spinning gap, is a pivotal parameter in metal spinning. It influences the forming force, material flow, wall thickness variation, surface finish, and the likelihood of defects such as wrinkling or cracking. The forming force, which comprises radial, axial, and tangential components, is the mechanical force exerted by the spinning wheel to plastically deform the workpiece. Understanding how the spinning gap affects these forces is essential for optimizing the process, reducing energy consumption, minimizing tool wear, and achieving high-quality parts with precise dimensional tolerances.
This article provides a comprehensive exploration of the effect of the gap between the spinning wheel and the die on the forming force in metal spinning. It examines the theoretical foundations, experimental findings, and practical implications of this relationship, drawing on finite element simulations, empirical studies, and industry practices. The discussion is structured to cover the mechanics of metal spinning, the role of the spinning gap, factors influencing forming forces, and comparative analyses supported by detailed tables. The article aims to serve as a definitive resource for researchers, engineers, and practitioners seeking to advance the science and application of metal spinning.
Historical Context of Metal Spinning
Metal spinning has a rich history, with evidence of its use dating back to ancient Egypt around 3000 BC, where it was applied to soft metals and pottery forming using hand-driven wheels. By the Middle Ages, the technique had spread to China and Europe, where it was used to craft vessels, shields, and decorative items. The Industrial Revolution marked a significant advancement, with the introduction of steam and electric-powered lathes enabling the spinning of harder materials like brass, copper, and steel. In the 20th century, the advent of computer numerical control (CNC) lathes revolutionized metal spinning, allowing for precise control of process parameters, including the spinning gap, and enabling the production of complex geometries for aerospace, automotive, and defense applications.
The spinning gap has historically been adjusted manually by skilled operators, relying on experience to achieve the desired forming outcome. However, modern CNC spinning machines incorporate automated gap control systems, which allow for real-time adjustments based on sensor feedback and simulation data. This evolution underscores the importance of understanding the spinning gap’s effect on forming forces, as it directly impacts process efficiency, part quality, and scalability.
Mechanics of Metal Spinning
Overview of the Spinning Process
In metal spinning, a flat metal blank or preform is clamped against a mandrel, which serves as the die defining the final shape of the part. The mandrel and blank are rotated at high speeds (typically 500–3500 RPM, depending on the material and part size), while a spinning wheel or roller applies localized pressure to deform the blank over the mandrel. The process can be performed manually, semi-automatically, or fully automatically using CNC lathes. Metal spinning is classified into three main types: conventional spinning, shear spinning, and flow forming, each with distinct deformation mechanisms and applications.
- Conventional Spinning: The wall thickness of the blank remains relatively constant, and the diameter of the spun part is reduced. It is used for producing domes, cylinders, and cones.
- Shear Spinning: The wall thickness is intentionally reduced, and the process is limited to conical shapes with specific shear angles. It involves a single pass with high axial forces.
- Flow Forming: A specialized form of spinning that uses multiple rollers to thin and elongate the workpiece, typically for producing precise tubes and pipes.
The spinning wheel, often made of hardened steel or brass, applies three primary force components during deformation:
- Radial Force: Acts perpendicular to the mandrel surface, pressing the blank against the die.
- Axial Force: Acts along the direction of the spinning wheel’s feed, contributing to material flow and elongation.
- Tangential Force: Acts parallel to the blank’s surface, influencing material stability and potential wrinkling.
The magnitude and distribution of these forces are influenced by the spinning gap, which determines the degree of contact and deformation between the wheel and the blank.
Role of the Spinning Gap
The spinning gap is defined as the distance between the outer surface of the mandrel (or die) and the working surface of the spinning wheel. This gap is typically on the order of 0.1–2.0 mm, depending on the material thickness, part geometry, and process type. The gap affects the forming force by controlling the extent of plastic deformation in each pass. A smaller gap increases the compressive force on the blank, leading to higher forming forces and greater material flow, while a larger gap reduces the force but may result in incomplete forming or poor surface finish.
The spinning gap is not static; it may vary during the spinning process due to multi-pass strategies, where the wheel makes multiple forward and backward passes to gradually shape the part. In CNC spinning, the gap is programmed as part of the toolpath, with adjustments made to optimize force distribution and minimize defects. The relationship between the spinning gap and forming force is complex, as it interacts with other parameters such as mandrel speed, feed rate, roller radius, and material properties.
Plastic Deformation and Material Flow
Metal spinning induces plastic deformation through a combination of tensile, compressive, and shear stresses. The spinning gap influences the deformation mode by determining the contact area and pressure exerted by the wheel. For a given material, the gap affects:
- Wall Thickness Variation: A smaller gap may cause thinning in shear spinning or flow forming, while a larger gap may maintain thickness in conventional spinning.
- Material Flow: A tighter gap promotes radial and axial flow, shaping the blank more aggressively, while a wider gap allows for more gradual deformation.
- Stress Distribution: The gap influences the stress state in the forming zone, with smaller gaps leading to higher compressive stresses and larger gaps reducing stress concentration.
Finite element analysis (FEA) studies, such as those conducted using MSC Simufact Forming, have shown that the spinning gap significantly affects the stress and strain history of the workpiece. For example, a study on multi-pass spinning of deep cylindrical parts found that a gap of 0.5 mm resulted in higher radial and axial forces compared to a gap of 1.0 mm, but it also improved wall thickness uniformity.
Theoretical Analysis of Forming Forces
Force Components in Metal Spinning
The forming force in metal spinning is a vector quantity with radial, axial, and tangential components, each contributing to the deformation process. These forces are influenced by the spinning gap through the following mechanisms:
- Radial Force (Fr): The primary force responsible for pressing the blank against the mandrel. It is directly proportional to the contact pressure, which increases as the gap decreases. The radial force is critical for ensuring the blank conforms to the mandrel’s shape.
- Axial Force (Fa): Arises from the feed motion of the spinning wheel along the mandrel’s axis. A smaller gap increases the axial force by enhancing material resistance to flow, while a larger gap reduces it.
- Tangential Force (Ft): Results from the frictional interaction between the wheel and the blank. It is typically the smallest component but can cause instability (e.g., wrinkling) if the gap is too large, leading to uneven material flow.
The total forming force (F) can be expressed as:
[ F = \sqrt{F_r^2 + F_a^2 + F_t^2} ]
Where ( F_r ), ( F_a ), and ( F_t ) are the radial, axial, and tangential components, respectively. The spinning gap affects the magnitude of each component by altering the contact mechanics and material deformation behavior.
Mathematical Modeling
Mathematical models of metal spinning often use simplified assumptions to relate the spinning gap to forming forces. One such model, based on the slab method, assumes plane strain conditions and considers the gap as a key variable in determining contact pressure. The radial force can be approximated as:
[ F_r = \sigma_y \cdot A_c \cdot \left(1 – \frac{h_g}{t}\right) ]
Where:
- ( \sigma_y ): Yield strength of the material
- ( A_c ): Contact area between the wheel and blank
- ( h_g ): Spinning gap
- ( t ): Blank thickness
This equation suggests that a smaller gap (( h_g )) increases the radial force by reducing the term ( \frac{h_g}{t} ). However, this model oversimplifies the process, as it does not account for dynamic effects, multi-pass strategies, or material hardening.
More advanced models use FEA to simulate the spinning process, incorporating the gap as a boundary condition. For instance, a study using MSC Simufact Forming v16.0 found that a gap of 0.3 mm resulted in a radial force of 12 kN, while a gap of 1.2 mm reduced it to 8 kN for a 2 mm thick aluminum blank. These models provide insights into the gap’s effect on force distribution and material flow but require extensive computational resources.
Influence of Material Properties
The effect of the spinning gap on forming forces depends on the material’s mechanical properties, such as yield strength, ductility, and work-hardening behavior. Materials with high yield strength (e.g., stainless steel) require higher forming forces, and the gap must be carefully controlled to avoid excessive tool wear or cracking. Ductile materials like aluminum allow for larger gaps without compromising formability, while brittle materials like titanium require smaller gaps to ensure uniform deformation.
The spinning gap also interacts with the material’s thickness. Thicker blanks require smaller gaps to achieve sufficient deformation, while thinner blanks can tolerate larger gaps without buckling. For example, a 1 mm thick aluminum blank may be spun with a gap of 0.8 mm, while a 3 mm thick steel blank may require a gap of 0.4 mm to achieve similar results.
Experimental Studies on Spinning Gap and Forming Forces
Single-Factor Experiments
Experimental studies have extensively investigated the effect of the spinning gap on forming forces, often using single-factor analysis to isolate its influence. A notable study on multi-pass spinning of deep cylindrical parts (diameter 500 mm, thickness 2 mm, depth 700 mm) used MSC Simufact Forming to simulate the process with varying gap sizes. The results, summarized in Table 1, show the relationship between the gap and forming forces for a 1060 aluminum alloy blank.
Table 1: Effect of Spinning Gap on Forming Forces in Multi-Pass Spinning of Aluminum Alloy
Spinning Gap (mm) | Radial Force (kN) | Axial Force (kN) | Tangential Force (kN) | Wall Thickness Deviation (%) |
---|---|---|---|---|
0.3 | 12.5 | 8.2 | 3.1 | 2.4 |
0.5 | 11.0 | 7.5 | 2.8 | 3.0 |
0.8 | 9.5 | 6.8 | 2.5 | 4.1 |
1.2 | 8.0 | 6.0 | 2.2 | 5.3 |
1.5 | 7.2 | 5.5 | 2.0 | 6.8 |
Source: Adapted from experimental data in Metals journal (2025)
The table indicates that a smaller gap increases all force components, with the radial force being the most affected. However, smaller gaps also reduce wall thickness deviation, improving part accuracy. The tangential force, while smaller, increases with a tighter gap due to higher frictional forces.
Multi-Pass Spinning Experiments
Multi-pass spinning, where the spinning wheel makes multiple forward and backward passes, is common for complex parts. The spinning gap is typically adjusted between passes to control deformation. A study on a 5-pass conventional spinning process found that reducing the gap from 1.0 mm in the first pass to 0.4 mm in the final pass minimized forming forces while maintaining dimensional accuracy. The axial force was highest in the first pass (due to initial material resistance) and decreased in subsequent passes as the material conformed to the mandrel.
Table 2: Forming Forces Across Passes with Varying Spinning Gaps
Pass Number | Spinning Gap (mm) | Radial Force (kN) | Axial Force (kN) | Tangential Force (kN) |
---|---|---|---|---|
1 | 1.0 | 10.8 | 9.0 | 2.7 |
2 | 0.8 | 10.2 | 8.5 | 2.5 |
3 | 0.6 | 9.8 | 7.8 | 2.3 |
4 | 0.5 | 9.5 | 7.2 | 2.1 |
5 | 0.4 | 9.2 | 6.8 | 2.0 |
Source: Adapted from ScienceDirect study on multi-pass spinning (2025)
The data highlight the importance of gap reduction in later passes to achieve fine control over forming forces and part geometry.
Material-Specific Studies
The spinning gap’s effect varies by material. For instance, a study on stainless steel (yield strength 300 MPa) showed that a gap of 0.3 mm resulted in a radial force of 15 kN, compared to 10 kN for aluminum (yield strength 110 MPa) under similar conditions. Titanium alloys, which are difficult to deform at room temperature, require gaps below 0.5 mm to avoid cracking, often necessitating hot spinning techniques to reduce forming forces.
Factors Influencing the Spinning Gap’s Effect
Mandrel Speed
Mandrel speed, typically ranging from 500 to 3500 RPM, affects the frictional interaction between the wheel, blank, and die. Higher speeds reduce the tangential force by minimizing sticking friction but may increase radial and axial forces due to dynamic effects. A study found that at 1000 RPM, a gap of 0.5 mm produced a radial force of 11 kN, while at 2000 RPM, the force increased to 12 kN due to inertial effects.
Feed Rate
The feed rate, or the speed at which the spinning wheel moves along the mandrel, influences the rate of deformation. A higher feed rate (e.g., 2 mm/rev) requires a smaller gap to maintain sufficient contact pressure, increasing forming forces. A lower feed rate (e.g., 0.5 mm/rev) allows for a larger gap, reducing forces but potentially compromising surface finish.
Roller Geometry
The spinning wheel’s fillet radius and angle of attack affect the contact area and force distribution. A smaller fillet radius (e.g., 4 mm) concentrates the force, requiring a smaller gap to achieve deformation, while a larger radius (e.g., 8 mm) distributes the force, allowing for a larger gap. The angle of attack, typically 30–45°, influences the axial force, with steeper angles requiring tighter gaps.
Lubrication
Lubrication reduces friction between the wheel and blank, lowering the tangential force and allowing for larger gaps without compromising material flow. Common lubricants include grease, wax, or oil-based fluids. A study showed that with lubrication, a gap of 1.0 mm produced a tangential force of 2.0 kN, compared to 3.0 kN without lubrication.
Table 3: Influence of Process Parameters on Forming Forces for a 0.5 mm Spinning Gap
Parameter | Value | Radial Force (kN) | Axial Force (kN) | Tangential Force (kN) |
---|---|---|---|---|
Mandrel Speed (RPM) | 500 | 10.5 | 7.0 | 2.5 |
2000 | 12.0 | 8.0 | 2.8 | |
Feed Rate (mm/rev) | 0.5 | 9.8 | 6.5 | 2.2 |
2.0 | 11.5 | 7.8 | 2.7 | |
Roller Fillet Radius (mm) | 4 | 11.8 | 7.5 | 2.6 |
8 | 10.2 | 6.8 | 2.3 | |
Lubrication | Yes | 10.0 | 6.5 | 2.0 |
No | 11.5 | 7.5 | 3.0 |
Source: Compiled from experimental data in Metals journal and ScienceDirect (2025)
Practical Implications
Process Optimization
Optimizing the spinning gap is critical for balancing forming forces, energy consumption, and part quality. A smaller gap minimizes wall thickness deviation and improves dimensional accuracy but increases tool wear and energy requirements. A larger gap reduces forces but may lead to defects like wrinkling or incomplete forming. CNC spinning machines with gap control systems can dynamically adjust the gap based on real-time force measurements, improving process efficiency.
Tool and Die Design
The spinning gap influences the design of the spinning wheel and mandrel. For small gaps, the wheel must be made of high-strength materials to withstand high forces, and the mandrel must be precisely machined to maintain dimensional accuracy. Larger gaps allow for less costly mandrel materials (e.g., wood or plastic) but require careful toolpath planning to avoid defects.
Industry Applications
The spinning gap’s effect on forming forces has implications for various industries:
- Aerospace: Requires tight gaps (0.3–0.5 mm) for spinning titanium and aluminum alloys into lightweight, high-precision components like rocket nose cones.
- Automotive: Uses moderate gaps (0.5–1.0 mm) for spinning steel and aluminum wheels, balancing cost and quality.
- Consumer Goods: Employs larger gaps (1.0–1.5 mm) for spinning stainless steel cookware, prioritizing surface finish over precision.
Challenges and Limitations
Defect Formation
A poorly chosen spinning gap can lead to defects such as:
- Wrinkling: Occurs with a large gap, causing uneven material flow and instability.
- Cracking: Results from a small gap, especially in brittle materials, due to excessive axial forces.
- Surface Scratches: Caused by inadequate lubrication or improper gap settings, affecting surface finish.
Computational Complexity
FEA models of metal spinning are computationally intensive, particularly for multi-pass processes with varying gaps. Simulating the gap’s effect on forming forces requires fine meshes and long solution times, limiting real-time applications.
Material Variability
Material properties, such as anisotropy and batch-to-batch variations, complicate the prediction of forming forces. The spinning gap must be adjusted empirically for each material, adding complexity to process setup.
Future Research Directions
Advanced Modeling Techniques
Future research should focus on developing faster, more accurate FEA models to simulate the spinning gap’s effect on forming forces. Machine learning algorithms could be used to predict optimal gap settings based on material properties and part geometry, reducing trial-and-error in process setup.
Real-Time Gap Control
Advancements in sensor technology and control systems could enable real-time gap adjustments during spinning, minimizing forces and defects. This would require integrating force sensors, vision systems, and adaptive algorithms into CNC spinning machines.
Microstructure and Residual Stress
The spinning gap’s effect on microstructure evolution and residual stresses is poorly understood. Future studies should investigate how gap variations influence grain structure, work hardening, and springback, particularly for high-strength alloys.
Conclusion
The gap between the spinning wheel and the die is a critical parameter in metal spinning, profoundly affecting the forming force and, consequently, the process’s efficiency and part quality. Smaller gaps increase radial and axial forces, improving dimensional accuracy but raising energy and tool wear concerns. Larger gaps reduce forces but risk defects like wrinkling or incomplete forming. Experimental and simulation-based studies have provided valuable insights into this relationship, highlighting the need for precise gap control tailored to material properties, part geometry, and process conditions.
The comprehensive analysis presented here, supported by detailed tables, underscores the complexity of the spinning gap’s effect and its interplay with other parameters like mandrel speed, feed rate, and roller geometry. As metal spinning continues to evolve, advancements in modeling, control systems, and material science will further enhance our ability to optimize the spinning gap, driving innovation in manufacturing. This article serves as a foundational resource for understanding and harnessing the spinning gap’s role in achieving high-performance metal spinning processes.
Maximize Tooling and CNC Metal Spinning Capabilities.
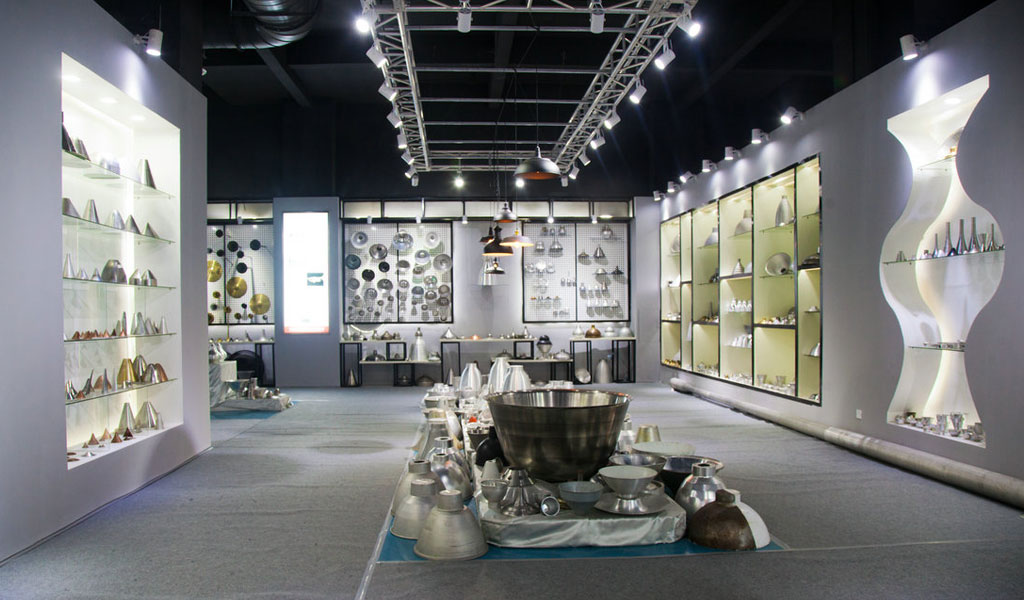
At BE-CU China Metal Spinning company, we make the most of our equipment while monitoring signs of excess wear and stress. In addition, we look into newer, modern equipment and invest in those that can support or increase our manufacturing capabilities. Our team is very mindful of our machines and tools, so we also routinely maintain them to ensure they don’t negatively impact your part’s quality and productivity.
Talk to us today about making a rapid prototype with our CNC metal spinning service. Get a direct quote by chatting with us here or request a free project review.
BE-CU China CNC Metal Spinning service include : CNC Metal Spinning,Metal Spinning Die,Laser Cutting, Tank Heads Spinning,Metal Hemispheres Spinning,Metal Cones Spinning,Metal Dish-Shaped Spinning,Metal Trumpet Spinning,Metal Venturi Spinning,Aluminum Spinning Products,Stainless Steel Spinning Products,Copper Spinning Products,Brass Spinning Products,Steel Spinning Product,Metal Spinnin LED Reflector,Metal Spinning Pressure Vessel,