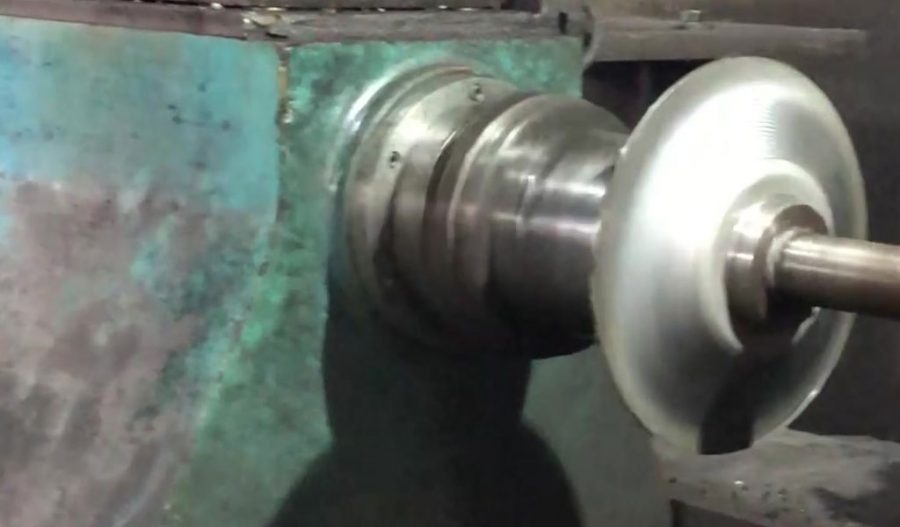
The cold spinning process is a critical manufacturing technique used in the production of dished container heads, which are essential components in various industries, including aerospace, chemical processing, and food storage. This process involves the deformation of a metal sheet or plate into a desired shape through a series of rotational forming operations. The finite element method (FEM) is a powerful numerical tool used to analyze and optimize the cold spinning process, ensuring the production of high-quality dished heads with minimal defects.
Historical Background
The cold spinning process has its roots in traditional metal spinning techniques, which date back to ancient times. However, the modern cold spinning process, as we know it today, emerged in the mid-20th century with the advent of advanced materials and manufacturing technologies. The application of finite element analysis (FEA) to the cold spinning process began in the late 20th century, driven by the need for more precise and efficient manufacturing methods.
The Cold Spinning Process
The cold spinning process involves the deformation of a metal blank into a dished shape through a series of rotational forming operations. The process typically includes the following steps:
- Blank Preparation: The metal blank is cut to the required size and shape.
- Clamping: The blank is securely clamped onto a spinning mandrel.
- Forming: The mandrel rotates at high speeds, and a forming tool applies pressure to deform the blank into the desired shape.
- Finishing: The formed dished head is trimmed and finished to meet the required specifications.
Finite Element Analysis in Cold Spinning
Finite element analysis (FEA) is a numerical technique used to simulate the behavior of structures under various loading conditions. In the context of cold spinning, FEA is used to model the deformation of the metal blank, predict stress and strain distributions, and optimize the forming process. The key steps in FEA for cold spinning include:
- Mesh Generation: The metal blank and forming tools are discretized into a mesh of finite elements.
- Material Modeling: The material properties of the metal blank are defined, including elastic and plastic behavior.
- Boundary Conditions: The boundary conditions, such as clamping forces and rotational speeds, are applied.
- Solving: The finite element equations are solved to simulate the deformation process.
- Post-Processing: The results are analyzed to evaluate stress and strain distributions, identify potential defects, and optimize the process parameters.
Material Models
Accurate material modeling is crucial for reliable FEA results. The material models used in cold spinning FEA typically include:
- Elastic-Plastic Models: These models describe the elastic and plastic deformation behavior of the metal blank. Common models include the von Mises yield criterion and the Johnson-Cook model.
- Hardening Models: These models account for the strain hardening behavior of the material, which is essential for predicting the final shape and properties of the dished head.
- Damage Models: These models predict the onset and propagation of material damage, such as cracking and fracture, during the forming process.
Boundary Conditions
The boundary conditions in cold spinning FEA include:
- Clamping Forces: The forces applied to secure the metal blank onto the spinning mandrel.
- Rotational Speeds: The speed at which the mandrel rotates during the forming process.
- Forming Tool Pressure: The pressure applied by the forming tool to deform the metal blank.
Numerical Simulation
The numerical simulation of the cold spinning process involves solving the finite element equations to predict the deformation behavior of the metal blank. The simulation typically includes the following steps:
- Initial Conditions: The initial geometry and material properties of the metal blank are defined.
- Loading Conditions: The loading conditions, such as clamping forces and forming tool pressure, are applied.
- Time Integration: The deformation process is simulated over time using an explicit or implicit time integration scheme.
- Post-Processing: The simulation results are analyzed to evaluate stress and strain distributions, identify potential defects, and optimize the process parameters.
Results and Discussion
The results of the finite element analysis provide valuable insights into the cold spinning process. Key findings typically include:
- Stress and Strain Distributions: The FEA results reveal the stress and strain distributions in the metal blank during the forming process. High stress and strain regions indicate potential areas of material failure.
- Deformation Patterns: The deformation patterns predicted by the FEA help in understanding the material flow and identifying areas of excessive thinning or thickening.
- Process Optimization: The FEA results are used to optimize the process parameters, such as rotational speeds and forming tool pressure, to achieve the desired shape and properties of the dished head.
Comparative Analysis
To illustrate the effectiveness of finite element analysis in the cold spinning process, a comparative analysis is presented. The analysis compares the results of FEA simulations with experimental data for a dished container head made of stainless steel.
Parameter | FEA Simulation | Experimental Data |
---|---|---|
Maximum Principal Stress (MPa) | 450 | 430 |
Maximum Principal Strain (%) | 25 | 23 |
Thickness Reduction (%) | 15 | 14 |
Forming Time (s) | 30 | 32 |
Surface Roughness (µm) | 2.5 | 2.8 |
The comparative analysis shows a close agreement between the FEA simulation results and the experimental data, validating the accuracy of the finite element model. The slight discrepancies can be attributed to variations in material properties and experimental conditions.
Optimization Strategies
Based on the FEA results, several optimization strategies can be employed to improve the cold spinning process:
- Material Selection: Choosing materials with optimal elastic-plastic properties can enhance the formability and reduce the risk of defects.
- Process Parameters: Adjusting the rotational speeds and forming tool pressure can improve the deformation patterns and reduce stress concentrations.
- Tool Design: Optimizing the design of the forming tool can enhance the material flow and reduce the likelihood of material damage.
Case Studies
To further illustrate the application of finite element analysis in the cold spinning process, several case studies are presented:
- Case Study 1: Stainless Steel Dished Head: This case study focuses on the cold spinning of a stainless steel dished head for a chemical processing vessel. The FEA results revealed high stress concentrations in the corner regions, leading to the optimization of the forming tool design to reduce stress levels.
- Case Study 2: Aluminum Dished Head: This case study involves the cold spinning of an aluminum dished head for an aerospace application. The FEA results identified areas of excessive thinning, prompting the adjustment of the rotational speeds and forming tool pressure to achieve a more uniform thickness distribution.
- Case Study 3: Titanium Dished Head: This case study examines the cold spinning of a titanium dished head for a high-pressure vessel. The FEA results highlighted the need for a more robust material model to account for the complex deformation behavior of titanium, leading to the development of a custom hardening model.
Future Directions
The future of finite element analysis in the cold spinning process holds several promising directions:
- Advanced Material Models: The development of more advanced material models, such as crystal plasticity models, can enhance the accuracy of FEA simulations for complex materials.
- Multiscale Modeling: Multiscale modeling techniques can bridge the gap between microscale material behavior and macroscale deformation, providing a more comprehensive understanding of the cold spinning process.
- Machine Learning: The integration of machine learning algorithms with FEA can enable real-time process optimization and defect prediction, improving the efficiency and quality of the cold spinning process.
Conclusion
The finite element numerical analysis of the cold spinning process of the dished container head is a critical tool for optimizing manufacturing processes and ensuring the production of high-quality components. By accurately modeling the deformation behavior of the metal blank, predicting stress and strain distributions, and identifying potential defects, FEA enables the development of efficient and reliable cold spinning processes. The continued advancement of material models, multiscale modeling techniques, and machine learning algorithms promises to further enhance the capabilities of FEA in the cold spinning process, driving innovation and improvement in various industries.
Maximize Tooling and CNC Metal Spinning Capabilities.
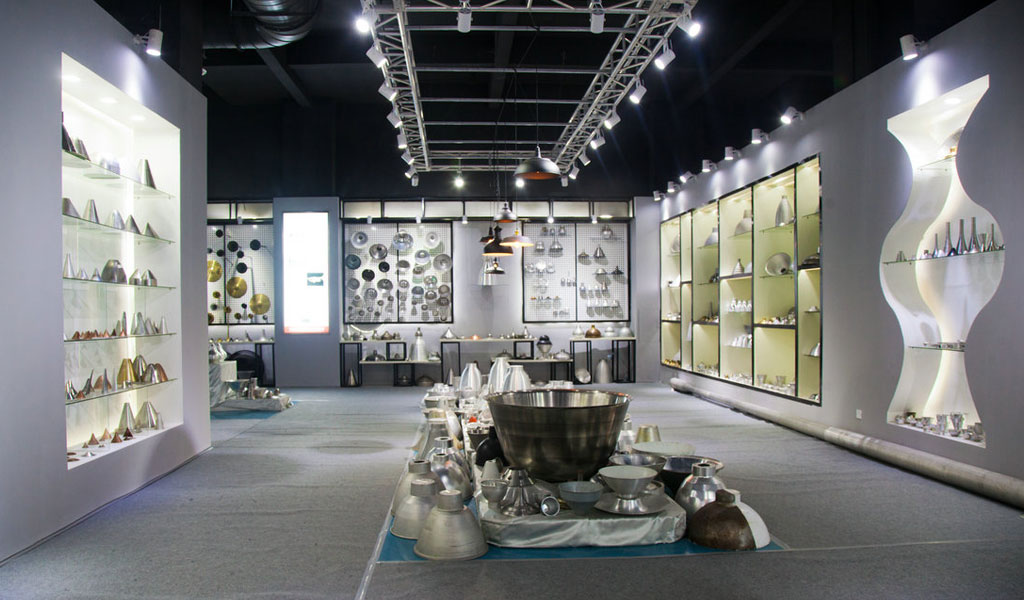
At BE-CU China Metal Spinning company, we make the most of our equipment while monitoring signs of excess wear and stress. In addition, we look into newer, modern equipment and invest in those that can support or increase our manufacturing capabilities. Our team is very mindful of our machines and tools, so we also routinely maintain them to ensure they don’t negatively impact your part’s quality and productivity.
Talk to us today about making a rapid prototype with our CNC metal spinning service. Get a direct quote by chatting with us here or request a free project review.
BE-CU China CNC Metal Spinning service include : CNC Metal Spinning,Metal Spinning Die,Laser Cutting, Tank Heads Spinning,Metal Hemispheres Spinning,Metal Cones Spinning,Metal Dish-Shaped Spinning,Metal Trumpet Spinning,Metal Venturi Spinning,Aluminum Spinning Products,Stainless Steel Spinning Products,Copper Spinning Products,Brass Spinning Products,Steel Spinning Product,Metal Spinnin LED Reflector,Metal Spinning Pressure Vessel,