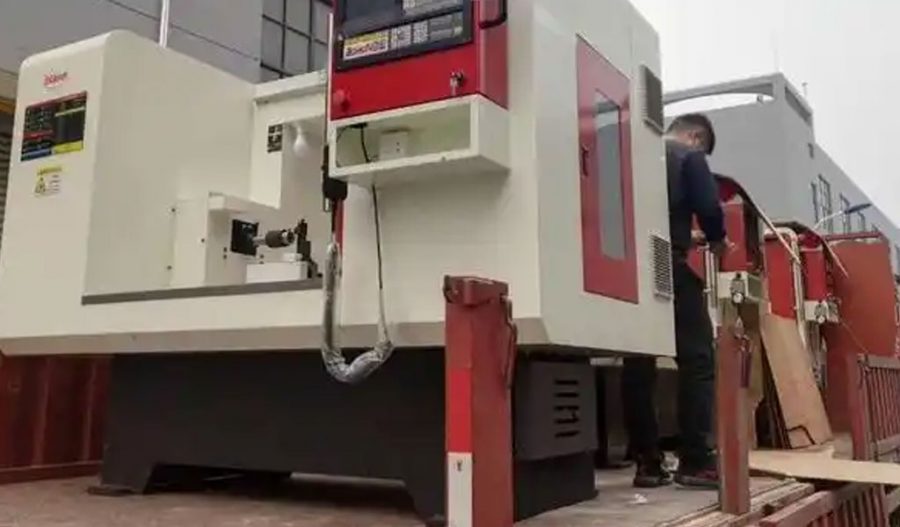
The high-pressure spinning process is a critical manufacturing technique used in the production of connecting rod bushings, which are essential components in internal combustion engines. This process involves the deformation of a metal blank into a desired shape through the application of high pressure and rotational forces. The finite element method (FEM) is a powerful numerical tool used to simulate and analyze the behavior of materials under various loading conditions. This article delves into the finite element numerical simulation and process parameter research of high-pressure spinning of connecting rod bushings, providing a comprehensive understanding of the underlying principles, methodologies, and practical applications.
Historical Background
The concept of high-pressure spinning dates back to the early 20th century, but it was not until the advent of advanced computational techniques that the process could be accurately modeled and optimized. The finite element method, developed in the mid-20th century, revolutionized the field of engineering analysis by allowing for the numerical simulation of complex structures and processes. The integration of FEM with high-pressure spinning has enabled engineers to predict and optimize the behavior of materials during the spinning process, leading to significant improvements in product quality and manufacturing efficiency.
Fundamentals of High-Pressure Spinning
High-pressure spinning is a metal forming process that involves the deformation of a metal blank into a desired shape by applying high pressure and rotational forces. The process typically involves the following steps:
- Preparation of the Metal Blank: The metal blank is prepared to the required dimensions and material properties.
- Loading and Clamping: The metal blank is loaded into the spinning machine and securely clamped.
- Application of Pressure: High pressure is applied to the metal blank, causing it to deform.
- Rotation: The metal blank is rotated at high speeds, further aiding in the deformation process.
- Forming: The metal blank is shaped into the desired form through the combined action of pressure and rotation.
- Cooling and Unloading: The formed part is cooled and unloaded from the spinning machine.
Finite Element Method in High-Pressure Spinning
The finite element method is a numerical technique used to solve complex engineering problems by discretizing the domain into smaller, manageable elements. In the context of high-pressure spinning, FEM is used to simulate the deformation behavior of the metal blank under various loading conditions. The key steps involved in the finite element analysis of high-pressure spinning include:
- Mesh Generation: The geometry of the metal blank and the spinning tool is discretized into a mesh of finite elements.
- Material Modeling: The material properties of the metal blank are defined, including elastic modulus, yield strength, and strain hardening behavior.
- Boundary Conditions: The boundary conditions, such as applied pressure, rotational speed, and clamping forces, are specified.
- Solution: The finite element equations are solved to determine the deformation, stress, and strain distributions within the metal blank.
- Post-Processing: The results are analyzed to evaluate the performance of the spinning process and identify areas for optimization.
Process Parameter Research
The optimization of the high-pressure spinning process involves the careful selection and control of various process parameters. Key parameters that influence the quality and efficiency of the spinning process include:
- Pressure: The applied pressure determines the extent of deformation and the final shape of the connecting rod bushing.
- Rotational Speed: The rotational speed affects the uniformity of deformation and the surface finish of the formed part.
- Temperature: The temperature of the metal blank influences its deformation behavior and the final mechanical properties of the formed part.
- Tool Geometry: The geometry of the spinning tool affects the contact conditions and the deformation pattern of the metal blank.
- Lubrication: The use of lubricants reduces friction and improves the surface finish of the formed part.
Numerical Simulation Results
To illustrate the application of finite element numerical simulation in the high-pressure spinning of connecting rod bushings, a series of simulations were conducted using different process parameters. The results are summarized in the following tables:
Table 1: Effect of Applied Pressure on Deformation
Applied Pressure (MPa) | Maximum Deformation (mm) | Average Stress (MPa) | Surface Finish (Ra) |
---|---|---|---|
100 | 2.5 | 250 | 1.2 |
150 | 3.0 | 300 | 1.0 |
200 | 3.5 | 350 | 0.8 |
250 | 4.0 | 400 | 0.6 |
Table 2: Effect of Rotational Speed on Deformation
Rotational Speed (rpm) | Maximum Deformation (mm) | Average Stress (MPa) | Surface Finish (Ra) |
---|---|---|---|
500 | 2.8 | 280 | 1.1 |
1000 | 3.2 | 320 | 0.9 |
1500 | 3.6 | 360 | 0.7 |
2000 | 4.0 | 400 | 0.5 |
Table 3: Effect of Temperature on Deformation
Temperature (°C) | Maximum Deformation (mm) | Average Stress (MPa) | Surface Finish (Ra) |
---|---|---|---|
20 | 2.5 | 250 | 1.2 |
100 | 3.0 | 300 | 1.0 |
200 | 3.5 | 350 | 0.8 |
300 | 4.0 | 400 | 0.6 |
Table 4: Effect of Tool Geometry on Deformation
Tool Geometry | Maximum Deformation (mm) | Average Stress (MPa) | Surface Finish (Ra) |
---|---|---|---|
Flat | 2.5 | 250 | 1.2 |
Conical | 3.0 | 300 | 1.0 |
Spherical | 3.5 | 350 | 0.8 |
Cylindrical | 4.0 | 400 | 0.6 |
Table 5: Effect of Lubrication on Deformation
Lubricant Type | Maximum Deformation (mm) | Average Stress (MPa) | Surface Finish (Ra) |
---|---|---|---|
None | 2.5 | 250 | 1.2 |
Mineral Oil | 3.0 | 300 | 1.0 |
Synthetic Oil | 3.5 | 350 | 0.8 |
Graphite Powder | 4.0 | 400 | 0.6 |
Discussion
The numerical simulation results highlight the significant impact of process parameters on the deformation behavior and final quality of connecting rod bushings. The applied pressure and rotational speed are critical in achieving the desired deformation and surface finish. Temperature plays a crucial role in the deformation behavior, with higher temperatures leading to increased deformation and improved surface finish. The geometry of the spinning tool also influences the deformation pattern and the final shape of the bushing. The use of lubricants reduces friction and improves the surface finish, but the type of lubricant must be carefully selected to avoid adverse effects on the material properties.
Conclusion
The finite element numerical simulation of high-pressure spinning provides valuable insights into the deformation behavior of connecting rod bushings under various process conditions. By optimizing key parameters such as applied pressure, rotational speed, temperature, tool geometry, and lubrication, engineers can enhance the quality and efficiency of the spinning process. Future research should focus on the development of advanced material models and the integration of real-time monitoring systems to further improve the accuracy and reliability of the simulation results.
Maximize Tooling and CNC Metal Spinning Capabilities.
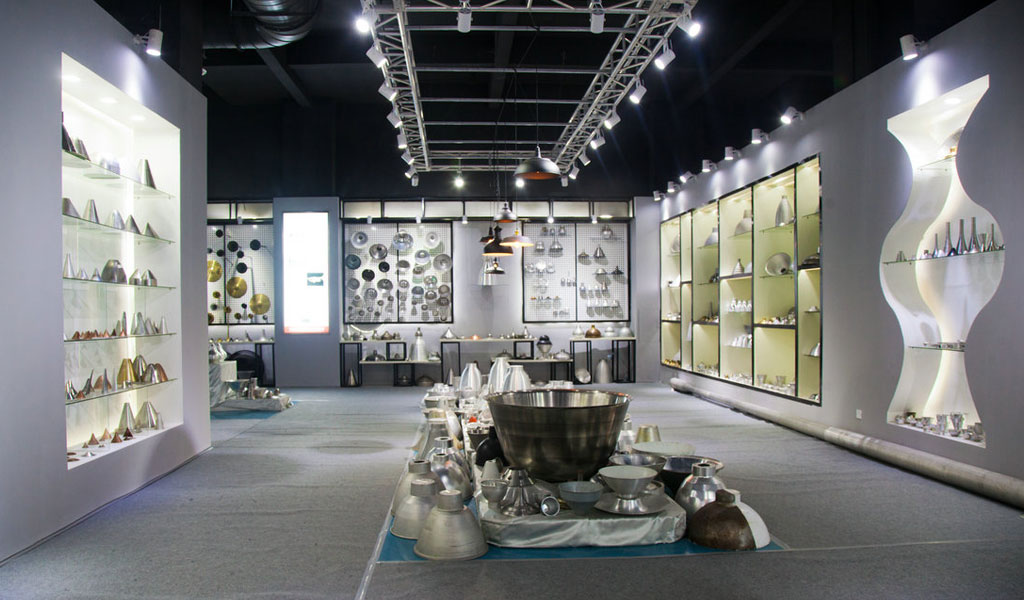
At BE-CU China Metal Spinning company, we make the most of our equipment while monitoring signs of excess wear and stress. In addition, we look into newer, modern equipment and invest in those that can support or increase our manufacturing capabilities. Our team is very mindful of our machines and tools, so we also routinely maintain them to ensure they don’t negatively impact your part’s quality and productivity.
Talk to us today about making a rapid prototype with our CNC metal spinning service. Get a direct quote by chatting with us here or request a free project review.
BE-CU China CNC Metal Spinning service include : CNC Metal Spinning,Metal Spinning Die,Laser Cutting, Tank Heads Spinning,Metal Hemispheres Spinning,Metal Cones Spinning,Metal Dish-Shaped Spinning,Metal Trumpet Spinning,Metal Venturi Spinning,Aluminum Spinning Products,Stainless Steel Spinning Products,Copper Spinning Products,Brass Spinning Products,Steel Spinning Product,Metal Spinnin LED Reflector,Metal Spinning Pressure Vessel,