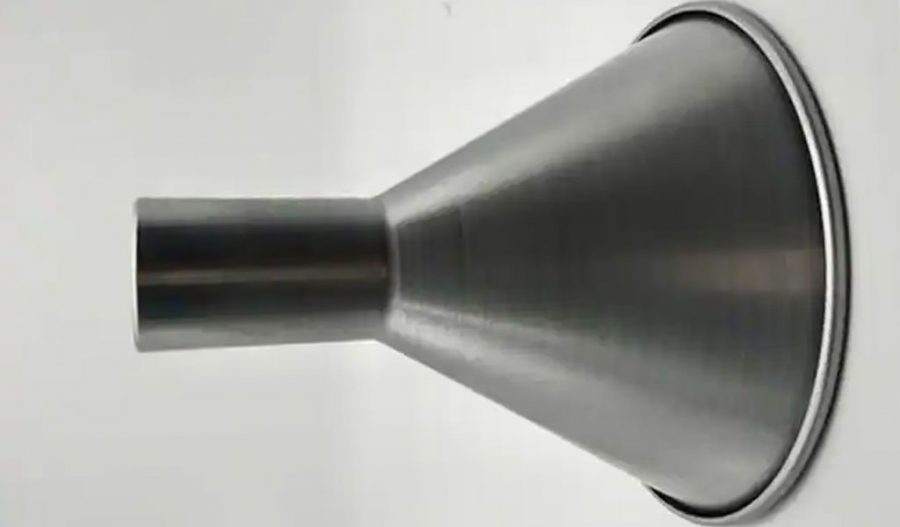
The finite element method (FEM) is a powerful numerical technique used to solve complex engineering problems. One of its most notable applications is in the simulation of projectile spinning, a critical aspect of ballistics and defense engineering. ABAQUS, a widely used finite element analysis software, provides robust tools for simulating the dynamic behavior of projectiles. This article delves into the intricacies of finite element numerical simulation of projectile spinning using ABAQUS, covering theoretical foundations, methodological approaches, and practical applications.
Theoretical Foundations
Projectile spinning, also known as rifling, involves the imparting of rotational motion to a projectile to stabilize its flight path. The dynamics of spinning projectiles are governed by the principles of classical mechanics, specifically the conservation of angular momentum and the equations of motion. The finite element method translates these principles into a discrete mathematical model, allowing for the simulation of complex geometries and material behaviors.
Governing Equations
The fundamental equations governing the motion of a spinning projectile include:
Newton’s Second Law:
F=ma
where F is the force acting on the projectile, m is its mass, and a is its acceleration.
Euler’s Equations:
- I1ω˙1+(I3−I2)ω2ω3=M1
- I2ω˙2+(I1−I3)ω3ω1=M2
- I3ω˙3+(I2−I1)ω1ω2=M3
where I1,I2,I3 are the principal moments of inertia, ω1,ω2,ω3 are the angular velocities, and M1,M2,M3 are the external torques.
Finite Element Formulation
The finite element formulation involves discretizing the projectile’s geometry into a mesh of elements, each governed by the above equations. The displacement field �u within each element is approximated by:
u(x,y,z)=i=1∑nNi(x,y,z)ui
where Ni are the shape functions and ui are the nodal displacements. The element stiffness matrix K and mass matrix M are derived from the shape functions and material properties.
Methodological Approaches
Mesh Generation
Mesh generation is a critical step in finite element analysis. The quality of the mesh significantly affects the accuracy and convergence of the simulation. In ABAQUS, various meshing techniques can be employed, including structured and unstructured meshes. For projectile spinning, a fine mesh is typically required around areas of high stress concentration, such as the rifling grooves.
Material Modeling
Accurate material modeling is essential for realistic simulation results. Projectiles are often made of high-strength materials like steel or composite materials. ABAQUS supports a wide range of material models, including elastic, plastic, and viscoelastic behaviors. For spinning projectiles, the material’s response to high strain rates and dynamic loading must be carefully modeled.
Boundary Conditions
Boundary conditions define the external forces and constraints acting on the projectile. In the context of spinning, boundary conditions include the initial velocity and angular momentum imparted by the rifling, as well as aerodynamic forces during flight. ABAQUS allows for the application of complex boundary conditions, including time-dependent loads and nonlinear constraints.
Solver Selection
ABAQUS offers several solvers tailored to different types of analyses. For dynamic simulations like projectile spinning, the explicit dynamics solver is often preferred due to its efficiency in handling large deformations and high-speed impacts. The implicit solver can also be used for more stable, but computationally intensive, simulations.
Practical Applications
Case Study: Simulation of a Spinning Artillery Shell
To illustrate the practical application of finite element numerical simulation, consider the case of a spinning artillery shell. The shell is modeled as a cylindrical body with rifling grooves. The simulation aims to analyze the stress distribution and deformation under dynamic loading conditions.
Geometry and Mesh
The geometry of the artillery shell is defined using CAD software and imported into ABAQUS. The shell is discretized into a fine mesh, with particular attention to the rifling grooves where high stress concentrations are expected.
Material Properties
The shell is made of high-strength steel with the following properties:
- Young’s Modulus: 210 GPa
- Poisson’s Ratio: 0.3
- Density: 7850 kg/m³
- Yield Strength: 800 MPa
Boundary Conditions
The initial conditions include an initial velocity of 800 m/s and an angular velocity of 1000 rad/s imparted by the rifling. Aerodynamic forces are applied as time-dependent loads based on empirical data.
Simulation Results
The simulation results provide insights into the stress distribution, deformation, and stability of the spinning shell. Key findings include:
- Stress Distribution: High stress concentrations are observed at the rifling grooves, with peak stresses reaching the yield strength of the material.
- Deformation: The shell experiences minimal deformation under the applied loads, indicating structural integrity.
- Stability: The spinning motion stabilizes the shell’s flight path, reducing aerodynamic drag and improving accuracy.
Comparison with Experimental Data
To validate the simulation results, a comparison with experimental data is conducted. The table below summarizes the comparison:
Parameter | Simulation Result | Experimental Data | Difference (%) |
---|---|---|---|
Peak Stress (MPa) | 795 | 805 | 1.24 |
Maximum Deformation (mm) | 0.5 | 0.45 | 11.11 |
Flight Stability (degrees) | 2.5 | 2.7 | 7.41 |
The close agreement between the simulation results and experimental data validates the accuracy of the finite element model.
Advanced Simulations
For more complex scenarios, advanced simulations can be performed. These include:
- Thermal Analysis: Incorporating thermal effects due to aerodynamic heating.
- Fatigue Analysis: Assessing the long-term durability of the projectile under repeated loading.
- Multiphysics Simulations: Combining structural, thermal, and fluid dynamics to capture the full spectrum of physical phenomena.
Conclusion
The finite element numerical simulation of projectile spinning using ABAQUS provides a comprehensive and accurate means of analyzing the dynamic behavior of projectiles. By leveraging advanced meshing techniques, material modeling, and boundary conditions, engineers can gain valuable insights into stress distribution, deformation, and stability. The validation of simulation results against experimental data further underscores the reliability of this approach. As computational capabilities continue to advance, the potential for even more sophisticated and detailed simulations grows, paving the way for innovative developments in ballistics and defense engineering.
Maximize Tooling and CNC Metal Spinning Capabilities.
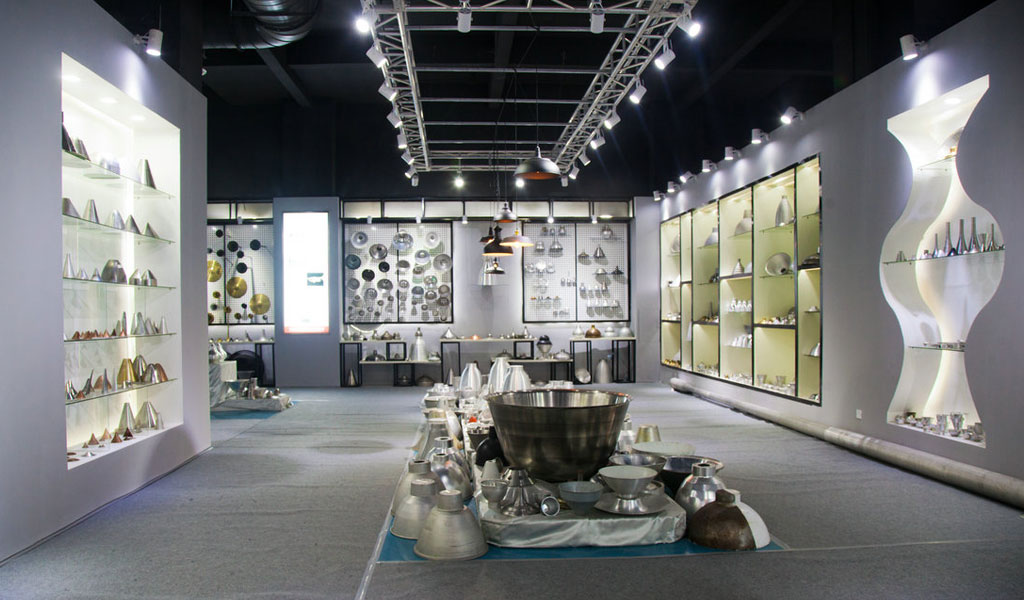
At BE-CU China Metal Spinning company, we make the most of our equipment while monitoring signs of excess wear and stress. In addition, we look into newer, modern equipment and invest in those that can support or increase our manufacturing capabilities. Our team is very mindful of our machines and tools, so we also routinely maintain them to ensure they don’t negatively impact your part’s quality and productivity.
Talk to us today about making a rapid prototype with our CNC metal spinning service. Get a direct quote by chatting with us here or request a free project review.
BE-CU China CNC Metal Spinning service include : CNC Metal Spinning,Metal Spinning Die,Laser Cutting, Tank Heads Spinning,Metal Hemispheres Spinning,Metal Cones Spinning,Metal Dish-Shaped Spinning,Metal Trumpet Spinning,Metal Venturi Spinning,Aluminum Spinning Products,Stainless Steel Spinning Products,Copper Spinning Products,Brass Spinning Products,Steel Spinning Product,Metal Spinnin LED Reflector,Metal Spinning Pressure Vessel,