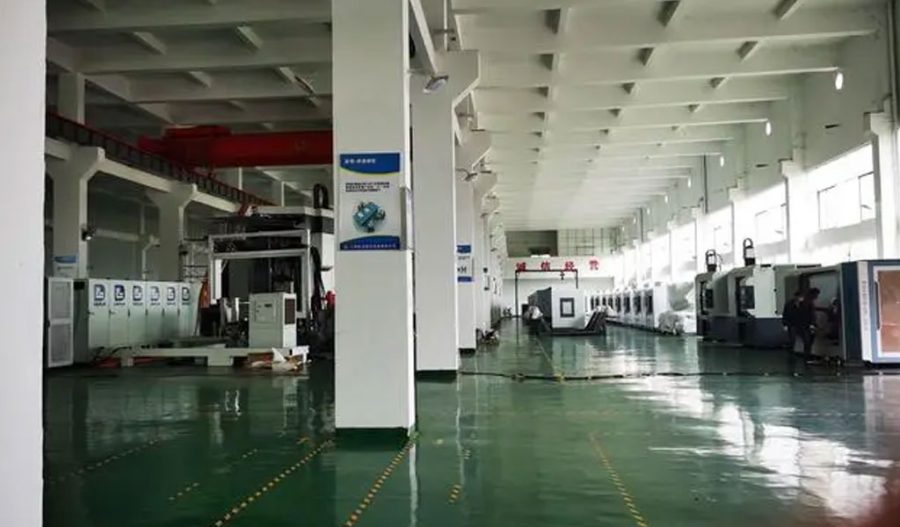
The escalating cost of raw materials has become a pressing concern for businesses across industries. Whether it’s steel, lumber, or precious metals, these expenses directly impact a company’s bottom line. While global economic factors and market demand play significant roles in these rising costs, understanding the intricacies of the supply chain can offer businesses valuable insights to mitigate expenses. This article delves into the high cost of raw materials and offers strategies to save by comprehending the supply chain better.
Understanding the Raw Material Supply Chain
The raw material supply chain is a complex network of processes and entities that starts with extraction or cultivation and ends with the delivery of the finished product to consumers. Key components of this chain include:
- Extraction or Cultivation: This involves mining ores, harvesting crops, or sourcing natural resources.
- Processing: Raw materials undergo various processes like refining, milling, or smelting to become usable.
- Distribution: Processed materials are transported to manufacturers or distributors.
- Manufacturing: Manufacturers transform these materials into finished products.
- Retail and Consumption: Finished products are then sold to retailers and consumed by end-users.
Factors Driving High Costs
Several factors contribute to the high cost of raw materials:
- Global Demand and Supply: Increased global demand and limited supply can lead to higher prices.
- Geopolitical Factors: Political instability, trade disputes, or sanctions can disrupt supply chains, affecting prices.
- Transportation Costs: Rising fuel prices and logistical challenges can inflate the costs of distribution.
- Environmental Regulations: Stricter environmental standards may require costly modifications in extraction or processing methods.
- Currency Fluctuations: Changes in currency values can impact the cost of imported raw materials.
Strategies to Save on Raw Materials
Understanding the supply chain can empower businesses to adopt cost-saving strategies:
- Supplier Diversification: Work with multiple suppliers to reduce reliance on a single source. This can help mitigate risks associated with supply chain disruptions.
- Long-term Contracts: Negotiate long-term contracts with suppliers to lock in prices and secure a steady supply of raw materials.
- Inventory Management: Implement efficient inventory management practices to minimize holding costs and reduce wastage.
- Value Engineering: Explore alternative materials or processes that offer similar performance but at a lower cost.
- Collaborative Planning: Collaborate closely with suppliers, distributors, and other stakeholders to streamline operations and reduce inefficiencies.
- Invest in Technology: Adopt advanced technologies like AI, IoT, and blockchain to track and optimize supply chain processes, improving transparency and efficiency.
- Sustainable Practices: Embrace sustainable sourcing and recycling initiatives to reduce costs and appeal to eco-conscious consumers.
Conclusion
The high cost of raw materials is a complex issue influenced by various global, economic, and logistical factors. However, businesses can navigate these challenges effectively by gaining a deeper understanding of the supply chain and adopting strategic approaches to save on costs. By diversifying suppliers, negotiating contracts, optimizing inventory, and leveraging technology, companies can not only mitigate the impact of rising raw material costs but also enhance their overall competitiveness in the market. Embracing sustainable practices not only helps in cost reduction but also positions businesses as responsible and forward-thinking entities in today’s eco-conscious landscape.
Maximize Tooling and CNC Metal Spinning Capabilities.
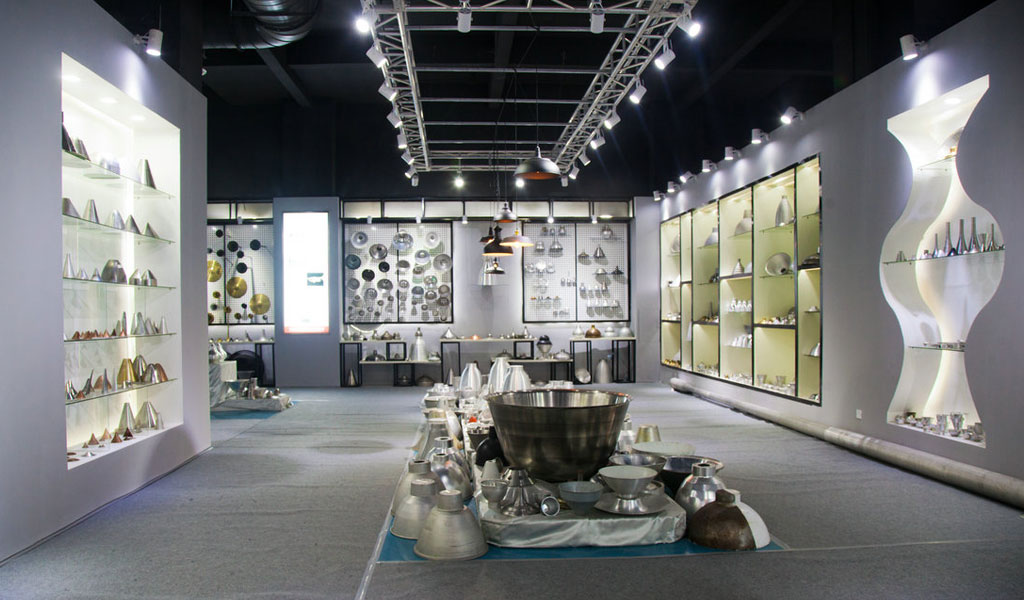
At BE-CU China Metal Spinning company, we make the most of our equipment while monitoring signs of excess wear and stress. In addition, we look into newer, modern equipment and invest in those that can support or increase our manufacturing capabilities. Our team is very mindful of our machines and tools, so we also routinely maintain them to ensure they don’t negatively impact your part’s quality and productivity.
Talk to us today about making a rapid prototype with our CNC metal spinning service. Get a direct quote by chatting with us here or request a free project review.
BE-CU China CNC Metal Spinning service include : CNC Metal Spinning,Metal Spinning Die,Laser Cutting, Tank Heads Spinning,Metal Hemispheres Spinning,Metal Cones Spinning,Metal Dish-Shaped Spinning,Metal Trumpet Spinning,Metal Venturi Spinning,Aluminum Spinning Products,Stainless Steel Spinning Products,Copper Spinning Products,Brass Spinning Products,Steel Spinning Product,Metal Spinnin LED Reflector,Metal Spinning Pressure Vessel,