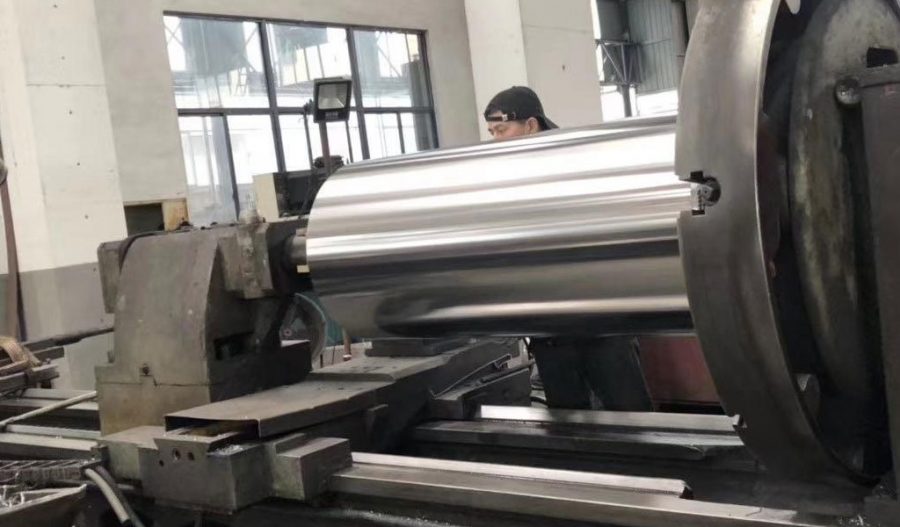
High-power spinning, also known as shear forming or flow forming, is a metalworking process used to produce axisymmetric parts with high precision and strength. This process is particularly advantageous for manufacturing components from niobium alloys, which are known for their exceptional mechanical properties and resistance to corrosion. Niobium alloys are widely used in aerospace, nuclear, and chemical industries due to their unique combination of strength, ductility, and resistance to high temperatures and corrosive environments.
The high-power spinning process involves the use of a rotating mandrel and a set of rollers that apply pressure to the workpiece, causing it to flow and conform to the shape of the mandrel. This method allows for the production of complex shapes with high dimensional accuracy and excellent surface finish. The process is particularly suited for niobium alloys due to their high formability and ability to withstand the high forces and temperatures involved in spinning.
Historical Background
The origins of metal spinning can be traced back to ancient times, where it was used for shaping metals into various forms. However, the modern high-power spinning process emerged in the mid-20th century with the advent of advanced machinery and materials. The development of niobium alloys, particularly in the aerospace industry, drove the need for more precise and efficient manufacturing techniques. High-power spinning provided a solution by enabling the production of high-strength, lightweight components with complex geometries.
Material Properties of Niobium Alloys
Niobium, also known as columbium, is a refractory metal with a melting point of approximately 2477°C. Its alloys exhibit a range of desirable properties, including high strength-to-weight ratio, excellent corrosion resistance, and good weldability. The most commonly used niobium alloys include Nb-1Zr, Nb-10Hf-1Ti, and Nb-10W-2.5Zr. These alloys are characterized by their high strength at elevated temperatures, making them ideal for applications in extreme environments.
Property | Nb-1Zr | Nb-10Hf-1Ti | Nb-10W-2.5Zr |
---|---|---|---|
Density (g/cm³) | 8.57 | 9.25 | 10.8 |
Melting Point (°C) | 2477 | 2450 | 2400 |
Yield Strength (MPa) | 275 | 350 | 400 |
Tensile Strength (MPa) | 380 | 450 | 500 |
Elongation (%) | 25 | 20 | 15 |
Thermal Conductivity (W/mK) | 53.7 | 51.2 | 49.5 |
Corrosion Resistance | Excellent | Excellent | Excellent |
High-Power Spinning Process
The high-power spinning process involves several key steps:
- Preparation of the Workpiece: The niobium alloy blank is prepared to the required dimensions and preheated to the desired temperature to enhance formability.
- Mandrel Setup: The mandrel, which serves as the mold for the final shape, is securely mounted on the spinning machine. The mandrel is typically made from a high-strength, wear-resistant material to withstand the forces applied during the spinning process.
- Roller Application: The rollers, which are made from hardened tool steel, are positioned against the workpiece. The rollers apply pressure to the workpiece, causing it to flow and conform to the shape of the mandrel.
- Spinning Operation: The mandrel and workpiece are rotated at high speeds, typically ranging from 500 to 2000 RPM, depending on the size and complexity of the part. The rollers traverse the workpiece, applying controlled pressure to achieve the desired thickness and shape.
- Cooling and Finishing: After the spinning operation, the part is cooled to room temperature. Additional finishing operations, such as machining or polishing, may be performed to achieve the final dimensions and surface finish.
Advantages of High-Power Spinning
High-power spinning offers several advantages over traditional manufacturing methods, such as forging and machining:
- High Precision: The process allows for the production of parts with high dimensional accuracy and excellent surface finish, reducing the need for additional finishing operations.
- Material Efficiency: High-power spinning minimizes material waste, as the workpiece is formed directly into the final shape without the need for extensive machining.
- Cost-Effective: The process is relatively fast and requires less energy compared to other manufacturing methods, making it a cost-effective solution for producing complex parts.
- Versatility: High-power spinning can be used to produce a wide range of axisymmetric parts, including cones, cylinders, and hemispheres, with various wall thicknesses and diameters.
Applications of Niobium Alloy Parts
Niobium alloy parts manufactured through high-power spinning are used in various industries due to their unique properties:
- Aerospace Industry: Niobium alloys are used in the production of rocket nozzles, combustion chambers, and other high-temperature components. The high strength-to-weight ratio and excellent corrosion resistance make them ideal for aerospace applications.
- Nuclear Industry: Niobium alloys are used in nuclear reactors for control rods, fuel cladding, and other components that require high strength and resistance to corrosion and radiation.
- Chemical Industry: Niobium alloys are used in chemical processing equipment, such as reactors, heat exchangers, and piping, due to their excellent corrosion resistance and ability to withstand high temperatures and pressures.
- Electronics Industry: Niobium alloys are used in the production of superconducting magnets and other electronic components that require high electrical conductivity and resistance to magnetic fields.
Challenges and Limitations
Despite its advantages, high-power spinning of niobium alloys presents several challenges:
- High Tooling Costs: The mandrels and rollers used in the spinning process are typically made from high-strength, wear-resistant materials, which can be expensive to manufacture and maintain.
- Complex Setup: The spinning process requires precise control of various parameters, including rotation speed, roller pressure, and temperature, which can be challenging to achieve and maintain.
- Limited Geometries: High-power spinning is primarily suited for axisymmetric parts. Producing parts with complex, non-axisymmetric geometries may require additional manufacturing steps or alternative processes.
- Material Limitations: While niobium alloys are highly formable, their high strength and resistance to deformation can make them challenging to spin, particularly for parts with thin walls or complex shapes.
Future Directions
The high-power spinning of niobium alloy parts is a continually evolving field, with ongoing research and development aimed at addressing its challenges and expanding its applications. Key areas of focus include:
- Advanced Tooling Materials: Developing new tooling materials with improved wear resistance and strength to reduce tooling costs and extend tool life.
- Process Optimization: Optimizing the spinning process parameters, such as rotation speed, roller pressure, and temperature, to improve part quality and reduce production time.
- Hybrid Manufacturing: Combining high-power spinning with other manufacturing techniques, such as additive manufacturing or machining, to produce parts with complex geometries and enhanced properties.
- New Alloy Developments: Exploring new niobium alloys with improved formability, strength, and corrosion resistance to expand the range of applications for spun parts.
Conclusion
High-power spinning is a versatile and efficient manufacturing process for producing niobium alloy parts with high precision and strength. The unique properties of niobium alloys, including their high strength-to-weight ratio, excellent corrosion resistance, and good formability, make them ideal for a wide range of applications in aerospace, nuclear, chemical, and electronics industries. While the process presents several challenges, ongoing research and development are addressing these issues and expanding the potential of high-power spinning for niobium alloys.
As the demand for high-performance materials continues to grow, the high-power spinning of niobium alloy parts will play an increasingly important role in manufacturing advanced components for various industries. The continued advancement of tooling materials, process optimization, hybrid manufacturing techniques, and new alloy developments will further enhance the capabilities and applications of this innovative manufacturing process.
Maximize Tooling and CNC Metal Spinning Capabilities.
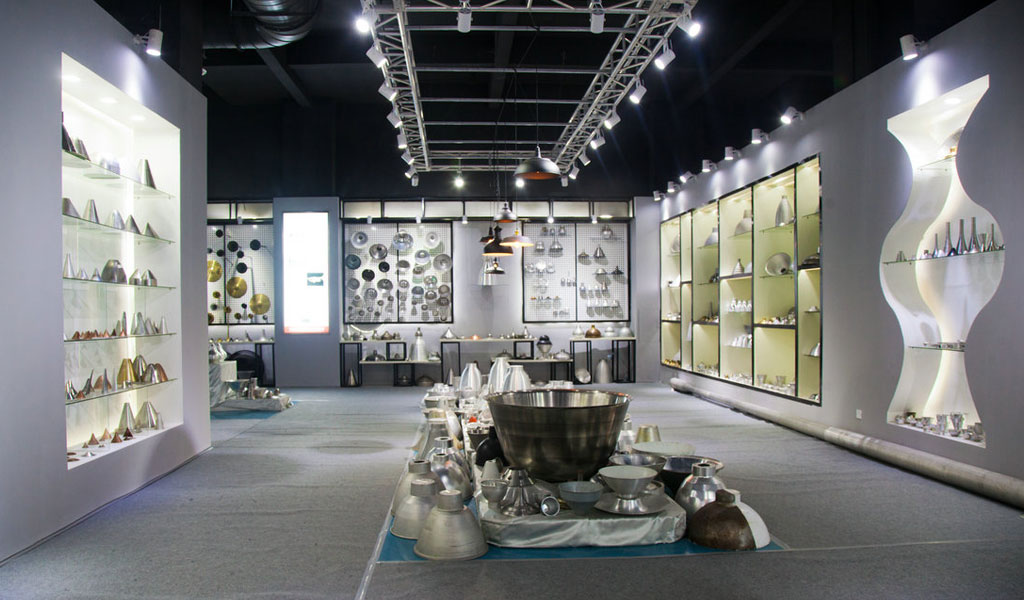
At BE-CU China Metal Spinning company, we make the most of our equipment while monitoring signs of excess wear and stress. In addition, we look into newer, modern equipment and invest in those that can support or increase our manufacturing capabilities. Our team is very mindful of our machines and tools, so we also routinely maintain them to ensure they don’t negatively impact your part’s quality and productivity.
Talk to us today about making a rapid prototype with our CNC metal spinning service. Get a direct quote by chatting with us here or request a free project review.
BE-CU China CNC Metal Spinning service include : CNC Metal Spinning,Metal Spinning Die,Laser Cutting, Tank Heads Spinning,Metal Hemispheres Spinning,Metal Cones Spinning,Metal Dish-Shaped Spinning,Metal Trumpet Spinning,Metal Venturi Spinning,Aluminum Spinning Products,Stainless Steel Spinning Products,Copper Spinning Products,Brass Spinning Products,Steel Spinning Product,Metal Spinnin LED Reflector,Metal Spinning Pressure Vessel,