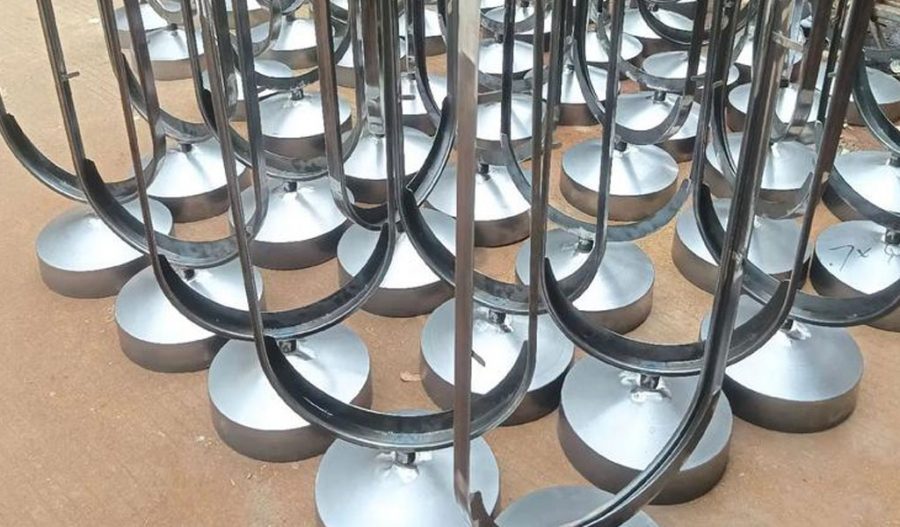
Heat pipes are thermal management devices that utilize phase change and capillary action to transfer heat efficiently. They are widely used in various applications, including electronics cooling, spacecraft thermal control, and energy recovery systems. Copper heat pipes, in particular, are favored for their excellent thermal conductivity and mechanical properties. One of the critical factors influencing the performance of heat pipes is the structure of the inner wall, specifically the presence of micro-grooves. These micro-grooves enhance the capillary action, facilitating the return of the working fluid from the condenser to the evaporator section.
High-speed liquid-filled spinning is an advanced manufacturing technique used to create micro-grooves on the inner wall of copper heat pipes. This process involves the use of a high-speed rotating mandrel and a liquid medium to form precise, uniform grooves. The technique offers several advantages over traditional methods, including improved surface finish, reduced manufacturing time, and enhanced groove uniformity. This article delves into the principles, methodologies, and applications of high-speed liquid-filled spinning for micro-groove formation in copper heat pipes.
Principles of High-Speed Liquid-Filled Spinning
High-speed liquid-filled spinning is a hybrid manufacturing process that combines the principles of spinning and liquid-assisted machining. The process begins with the preparation of a copper tube, which is mounted onto a high-speed rotating mandrel. The mandrel is designed to hold the tube securely while allowing for precise control over the rotational speed and axial movement.
The key component of this process is the liquid medium, which serves multiple functions. Firstly, it acts as a lubricant, reducing friction between the cutting tool and the copper surface. This minimizes tool wear and ensures a smooth, consistent cutting action. Secondly, the liquid medium helps to dissipate heat generated during the spinning process, preventing thermal deformation of the copper tube. Lastly, the liquid medium aids in the removal of swarf (small chips or fragments of material), maintaining a clean cutting environment.
The cutting tool, typically a diamond-tipped or carbide-tipped tool, is positioned at a precise angle and depth relative to the rotating tube. As the tube spins at high speeds, the tool is moved axially along the length of the tube, creating helical or spiral grooves on the inner wall. The depth, width, and pitch of the grooves can be precisely controlled by adjusting the tool’s position and the rotational speed of the mandrel.
Methodologies and Techniques
The success of high-speed liquid-filled spinning relies on several critical parameters, including the rotational speed of the mandrel, the feed rate of the cutting tool, the composition and properties of the liquid medium, and the geometry of the cutting tool. Each of these parameters must be optimized to achieve the desired groove characteristics and surface finish.
Rotational Speed and Feed Rate
The rotational speed of the mandrel is a crucial factor in determining the quality and uniformity of the micro-grooves. Higher rotational speeds generally result in smoother surfaces and more uniform grooves. However, excessively high speeds can lead to vibrations and instability, compromising the precision of the grooves. The feed rate, which is the speed at which the cutting tool moves axially along the tube, must be carefully controlled to ensure consistent groove depth and pitch.
Liquid Medium
The choice of liquid medium is critical for the success of the spinning process. Commonly used liquids include water-based coolants, oil-based lubricants, and specialized cutting fluids. The viscosity, thermal conductivity, and lubricating properties of the liquid medium must be carefully considered. Water-based coolants are often preferred for their excellent heat dissipation properties, while oil-based lubricants provide superior friction reduction.
Cutting Tool Geometry
The geometry of the cutting tool plays a significant role in determining the shape and dimensions of the micro-grooves. Diamond-tipped tools are favored for their durability and precision, while carbide-tipped tools offer a balance between cost and performance. The tool’s rake angle, clearance angle, and nose radius must be optimized to achieve the desired groove profile and surface finish.
Process Control and Automation
High-speed liquid-filled spinning is typically performed using computer numerical control (CNC) machines, which offer precise control over the rotational speed, feed rate, and tool position. CNC machines can be programmed to create complex groove patterns, including variable pitch and depth, to meet specific performance requirements. Automation also ensures consistency and repeatability, reducing the likelihood of human error.
Advantages of High-Speed Liquid-Filled Spinning
High-speed liquid-filled spinning offers several advantages over traditional methods for creating micro-grooves on the inner wall of copper heat pipes. These advantages include:
Improved Surface Finish
The use of a liquid medium and high-speed rotation results in a smoother surface finish compared to traditional machining methods. The reduced friction and efficient heat dissipation minimize tool marks and surface defects, enhancing the overall quality of the micro-grooves.
Enhanced Groove Uniformity
The precise control offered by CNC machines ensures consistent groove depth, width, and pitch along the entire length of the tube. This uniformity is critical for maintaining optimal capillary action and heat transfer performance in the heat pipe.
Reduced Manufacturing Time
High-speed liquid-filled spinning is a highly efficient process, capable of creating micro-grooves in a fraction of the time required by traditional methods. The combination of high rotational speeds and automated control significantly reduces manufacturing time, increasing productivity and reducing costs.
Versatility
The process can be adapted to create a wide range of groove patterns and dimensions, making it suitable for various applications and performance requirements. The ability to create complex groove patterns, including variable pitch and depth, allows for customization to meet specific thermal management needs.
Cost-Effectiveness
The reduced manufacturing time and improved surface finish translate into lower production costs. Additionally, the use of durable cutting tools and efficient liquid media minimizes tool wear and maintenance requirements, further reducing costs.
Applications of High-Speed Liquid-Filled Spinning
High-speed liquid-filled spinning is widely used in the manufacture of copper heat pipes for various applications, including:
Electronics Cooling
In the electronics industry, heat pipes are used to dissipate heat from high-performance components such as CPUs, GPUs, and power electronics. The micro-grooves created by high-speed liquid-filled spinning enhance the capillary action, ensuring efficient heat transfer and preventing thermal throttling.
Spacecraft Thermal Control
Heat pipes are essential for thermal management in spacecraft, where they are used to transfer heat from electronic components and other heat sources to radiators. The precise and uniform micro-grooves created by high-speed liquid-filled spinning ensure reliable and efficient heat transfer, even in the harsh conditions of space.
Energy Recovery Systems
In industrial applications, heat pipes are used in energy recovery systems to capture and reuse waste heat. The enhanced capillary action provided by micro-grooves improves the efficiency of heat transfer, reducing energy consumption and operating costs.
Automotive Cooling
In the automotive industry, heat pipes are used to cool engine components and electronic systems. The precise control and versatility of high-speed liquid-filled spinning make it an ideal process for creating customized heat pipes that meet the specific cooling requirements of different vehicle models.
Medical Devices
Heat pipes are used in medical devices to maintain optimal operating temperatures. The high-precision micro-grooves created by high-speed liquid-filled spinning ensure reliable and efficient heat transfer, enhancing the performance and longevity of medical equipment.
Challenges and Future Directions
While high-speed liquid-filled spinning offers numerous advantages, it also presents several challenges that need to be addressed. One of the primary challenges is the optimization of process parameters to achieve the desired groove characteristics and surface finish. This requires a deep understanding of the interactions between the rotational speed, feed rate, liquid medium, and cutting tool geometry.
Another challenge is the development of advanced cutting tools that can withstand the high speeds and forces involved in the spinning process. The use of diamond-tipped tools has shown promise, but further research is needed to develop more durable and cost-effective tool materials.
The future of high-speed liquid-filled spinning lies in the integration of advanced technologies such as artificial intelligence (AI) and machine learning (ML). These technologies can be used to optimize process parameters in real-time, ensuring consistent and high-quality micro-grooves. Additionally, the development of new liquid media with enhanced lubricating and heat dissipation properties can further improve the efficiency and effectiveness of the spinning process.
Conclusion
High-speed liquid-filled spinning is a cutting-edge manufacturing technique that offers significant advantages for creating micro-grooves on the inner wall of copper heat pipes. The combination of high-speed rotation, liquid-assisted machining, and precise control ensures improved surface finish, enhanced groove uniformity, reduced manufacturing time, and cost-effectiveness. The technique is widely used in various applications, including electronics cooling, spacecraft thermal control, energy recovery systems, automotive cooling, and medical devices.
As the demand for efficient thermal management solutions continues to grow, the importance of high-speed liquid-filled spinning is expected to increase. Ongoing research and development efforts are focused on addressing the challenges associated with this process and exploring new opportunities for innovation. The integration of advanced technologies such as AI and ML, along with the development of new cutting tools and liquid media, will drive the future of high-speed liquid-filled spinning, ensuring its continued relevance and effectiveness in the manufacturing of copper heat pipes.
Maximize Tooling and CNC Metal Spinning Capabilities.
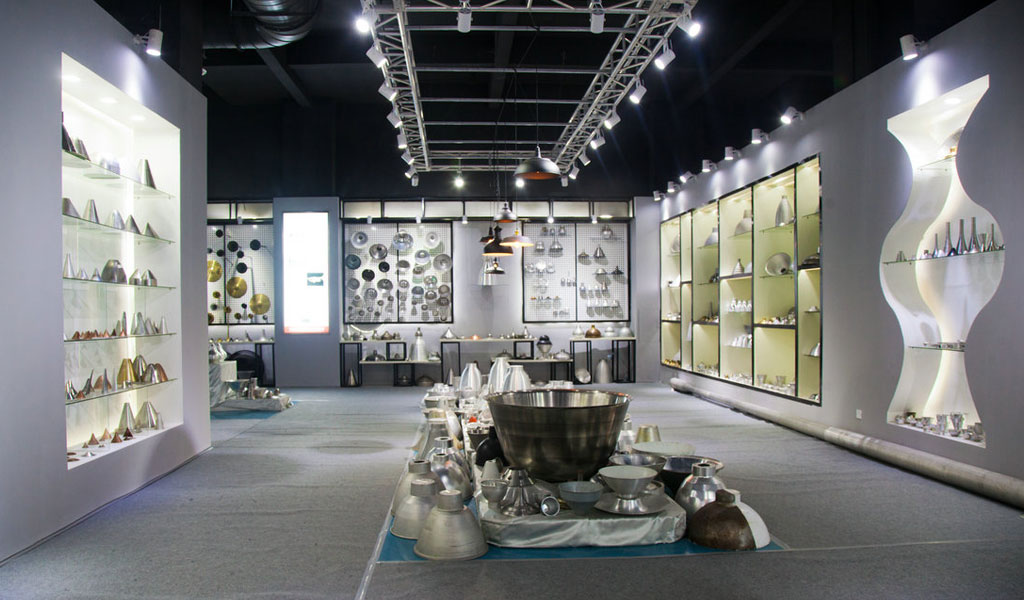
At BE-CU China Metal Spinning company, we make the most of our equipment while monitoring signs of excess wear and stress. In addition, we look into newer, modern equipment and invest in those that can support or increase our manufacturing capabilities. Our team is very mindful of our machines and tools, so we also routinely maintain them to ensure they don’t negatively impact your part’s quality and productivity.
Talk to us today about making a rapid prototype with our CNC metal spinning service. Get a direct quote by chatting with us here or request a free project review.
BE-CU China CNC Metal Spinning service include : CNC Metal Spinning,Metal Spinning Die,Laser Cutting, Tank Heads Spinning,Metal Hemispheres Spinning,Metal Cones Spinning,Metal Dish-Shaped Spinning,Metal Trumpet Spinning,Metal Venturi Spinning,Aluminum Spinning Products,Stainless Steel Spinning Products,Copper Spinning Products,Brass Spinning Products,Steel Spinning Product,Metal Spinnin LED Reflector,Metal Spinning Pressure Vessel,