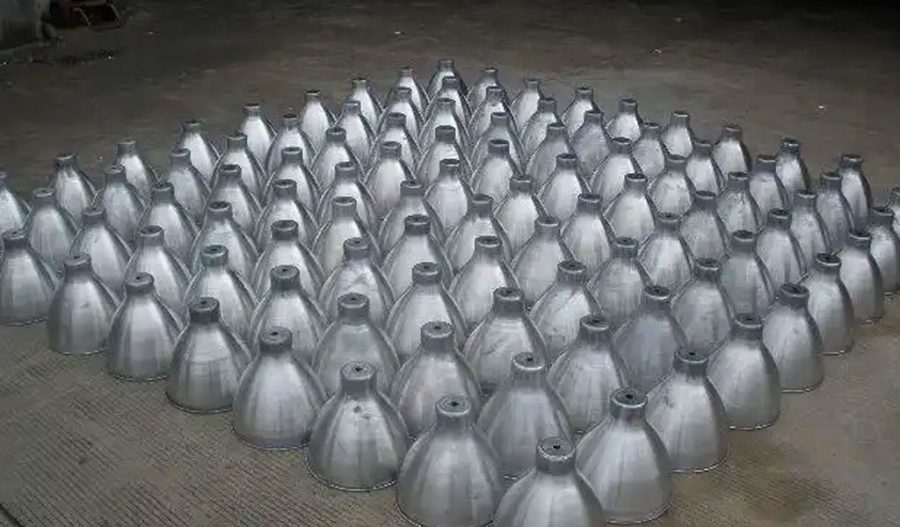
The hot spinning forming method is a critical process in the manufacturing of heterogeneous titanium alloy thin-walled tubes, particularly in cross-phase regions. This method leverages the unique properties of titanium alloys, which exhibit exceptional strength-to-weight ratios, corrosion resistance, and biocompatibility. The cross-phase regions refer to the transition zones between different microstructural phases within the alloy, such as the alpha (α) and beta (β) phases. These regions are crucial for achieving optimal mechanical properties and performance characteristics in the final product.
Titanium alloys are widely used in aerospace, chemical processing, marine applications, and medical implants due to their superior properties. The hot spinning process involves heating the titanium alloy to a specific temperature range where the material becomes more ductile, allowing it to be formed into thin-walled tubes through a spinning mandrel. This article delves into the intricacies of the hot spinning forming method, focusing on the cross-phase regions of heterogeneous titanium alloys.
Material Properties and Phase Transformations
Titanium alloys can be broadly classified into alpha (α), beta (β), and alpha-beta (α-β) alloys based on their microstructural phases. The alpha phase is characterized by a hexagonal close-packed (HCP) crystal structure, while the beta phase has a body-centered cubic (BCC) structure. Alpha-beta alloys contain a mixture of both phases, providing a balance of strength, ductility, and toughness.
The phase transformations in titanium alloys are temperature-dependent. At room temperature, pure titanium exists in the alpha phase. As the temperature increases, the alpha phase transforms into the beta phase at around 882°C (1620°F), known as the beta transus temperature. In alpha-beta alloys, the beta transus temperature varies depending on the alloying elements. The cross-phase regions are the intermediate temperature ranges where both alpha and beta phases coexist, and these regions are critical for hot spinning forming.
Hot Spinning Forming Process
The hot spinning forming process involves several key steps:
- Preheating: The titanium alloy blank is preheated to a temperature within the cross-phase region. This temperature range is carefully controlled to ensure the material is in a ductile state, facilitating the forming process.
- Spinning: The preheated blank is placed on a spinning mandrel, which rotates at high speeds. The mandrel applies pressure to the blank, gradually forming it into a thin-walled tube. The spinning process is controlled by parameters such as mandrel speed, feed rate, and applied pressure.
- Cooling: After the spinning process, the formed tube is cooled to room temperature. The cooling rate is critical as it affects the final microstructure and mechanical properties of the tube.
- Annealing: In some cases, annealing is performed to relieve residual stresses and improve the mechanical properties of the tube. Annealing involves heating the tube to a specific temperature and holding it for a certain period before cooling.
Microstructural Evolution
The microstructural evolution during the hot spinning forming process is complex and depends on various factors, including temperature, strain rate, and cooling rate. In the cross-phase regions, the alpha and beta phases undergo dynamic recrystallization and phase transformations, leading to a refined microstructure.
Dynamic recrystallization occurs when the material is deformed at elevated temperatures, resulting in the formation of new, strain-free grains. This process enhances the ductility and toughness of the material. Phase transformations, such as the alpha to beta transformation, also occur during heating and cooling, affecting the final microstructure.
Mechanical Properties
The mechanical properties of heterogeneous titanium alloy thin-walled tubes formed by hot spinning are influenced by the microstructural evolution during the process. Key mechanical properties include:
- Tensile Strength: The tensile strength of the tube is a measure of its resistance to fracture under tensile loading. Hot spinning in the cross-phase regions results in a refined microstructure, leading to enhanced tensile strength.
- Yield Strength: The yield strength is the stress at which the material begins to deform plastically. The hot spinning process improves the yield strength by refining the grain structure and reducing defects.
- Ductility: Ductility is the ability of the material to deform plastically without fracturing. The dynamic recrystallization during hot spinning enhances ductility, making the tubes more resistant to cracking.
- Toughness: Toughness is the material’s ability to absorb energy and deform plastically before fracturing. The refined microstructure and reduced defects in hot-spun tubes improve toughness.
- Fatigue Strength: Fatigue strength is the material’s resistance to fracture under cyclic loading. The hot spinning process enhances fatigue strength by reducing residual stresses and refining the microstructure.
Comparative Analysis
To understand the effectiveness of the hot spinning forming method, a comparative analysis with other forming methods is essential. The following table compares the hot spinning forming method with cold drawing and hydroforming methods for titanium alloy thin-walled tubes:
Property | Hot Spinning Forming | Cold Drawing | Hydroforming |
---|---|---|---|
Temperature Range | Cross-phase regions | Room temperature | Elevated temperature |
Microstructure | Refined, dynamic recrystallization | Elongated grains | Coarse grains |
Tensile Strength | High | Moderate | Moderate |
Yield Strength | High | Moderate | Moderate |
Ductility | High | Low | Moderate |
Toughness | High | Moderate | Moderate |
Fatigue Strength | High | Moderate | Moderate |
Residual Stresses | Low | High | Moderate |
Forming Complexity | Moderate | Low | High |
Cost | Moderate | Low | High |
Advantages and Limitations
The hot spinning forming method offers several advantages:
- Improved Mechanical Properties: The refined microstructure and reduced defects result in enhanced mechanical properties, including tensile strength, yield strength, ductility, toughness, and fatigue strength.
- Reduced Residual Stresses: The dynamic recrystallization and annealing processes relieve residual stresses, improving the dimensional stability and performance of the tubes.
- Versatility: The hot spinning process can be applied to various titanium alloys and tube geometries, making it a versatile forming method.
However, the method also has some limitations:
- Complexity: The hot spinning process requires precise control of temperature, strain rate, and cooling rate, making it more complex than other forming methods.
- Cost: The need for specialized equipment and precise control increases the cost of the hot spinning process compared to simpler methods like cold drawing.
Applications
The hot spinning forming method is widely used in various industries due to its ability to produce high-quality titanium alloy thin-walled tubes. Some key applications include:
- Aerospace: Titanium alloy tubes are used in aircraft structures, engines, and landing gear due to their high strength-to-weight ratio and corrosion resistance.
- Chemical Processing: The excellent corrosion resistance of titanium alloys makes them ideal for chemical processing equipment, such as heat exchangers and piping systems.
- Marine: Titanium alloy tubes are used in marine applications, including shipbuilding and offshore structures, due to their resistance to seawater corrosion.
- Medical Implants: The biocompatibility and corrosion resistance of titanium alloys make them suitable for medical implants, such as orthopedic devices and dental implants.
Future Directions
The hot spinning forming method of heterogeneous titanium alloy thin-walled tubes in cross-phase regions is a rapidly evolving field. Future research and development efforts are likely to focus on the following areas:
- Advanced Alloys: Developing new titanium alloys with enhanced mechanical properties and improved formability in the cross-phase regions.
- Process Optimization: Optimizing the hot spinning process parameters, such as temperature, strain rate, and cooling rate, to achieve even better mechanical properties and reduce residual stresses.
- Automation: Implementing automated control systems to improve the precision and consistency of the hot spinning process.
- Sustainability: Exploring sustainable manufacturing practices, such as energy-efficient heating methods and recycling of titanium alloys, to reduce the environmental impact of the hot spinning process.
Conclusion
The hot spinning forming method is a critical process for manufacturing heterogeneous titanium alloy thin-walled tubes in cross-phase regions. This method leverages the unique properties of titanium alloys, including their strength, ductility, and corrosion resistance, to produce high-quality tubes with superior mechanical properties. The dynamic recrystallization and phase transformations during the hot spinning process result in a refined microstructure, enhancing the tensile strength, yield strength, ductility, toughness, and fatigue strength of the tubes.
While the hot spinning forming method offers several advantages, such as improved mechanical properties and reduced residual stresses, it also has limitations, including complexity and cost. Future research and development efforts are likely to focus on advanced alloys, process optimization, automation, and sustainability to address these challenges and further enhance the hot spinning forming method.
In summary, the hot spinning forming method of heterogeneous titanium alloy thin-walled tubes in cross-phase regions is a vital technology for various industries, including aerospace, chemical processing, marine applications, and medical implants. Continued advancements in this field will drive innovation and improve the performance and sustainability of titanium alloy products.
Maximize Tooling and CNC Metal Spinning Capabilities.
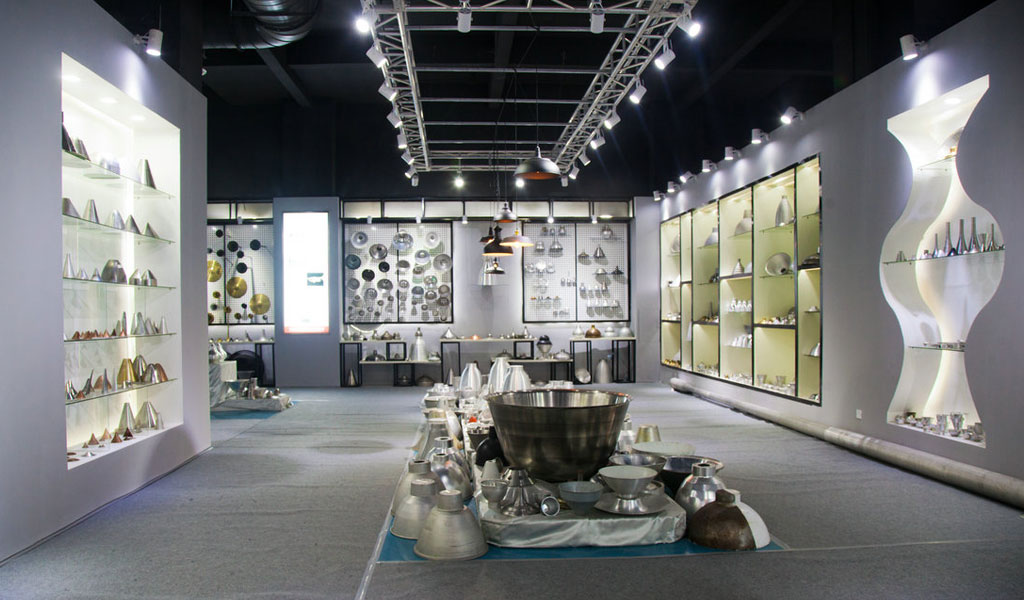
At BE-CU China Metal Spinning company, we make the most of our equipment while monitoring signs of excess wear and stress. In addition, we look into newer, modern equipment and invest in those that can support or increase our manufacturing capabilities. Our team is very mindful of our machines and tools, so we also routinely maintain them to ensure they don’t negatively impact your part’s quality and productivity.
Talk to us today about making a rapid prototype with our CNC metal spinning service. Get a direct quote by chatting with us here or request a free project review.
BE-CU China CNC Metal Spinning service include : CNC Metal Spinning,Metal Spinning Die,Laser Cutting, Tank Heads Spinning,Metal Hemispheres Spinning,Metal Cones Spinning,Metal Dish-Shaped Spinning,Metal Trumpet Spinning,Metal Venturi Spinning,Aluminum Spinning Products,Stainless Steel Spinning Products,Copper Spinning Products,Brass Spinning Products,Steel Spinning Product,Metal Spinnin LED Reflector,Metal Spinning Pressure Vessel,