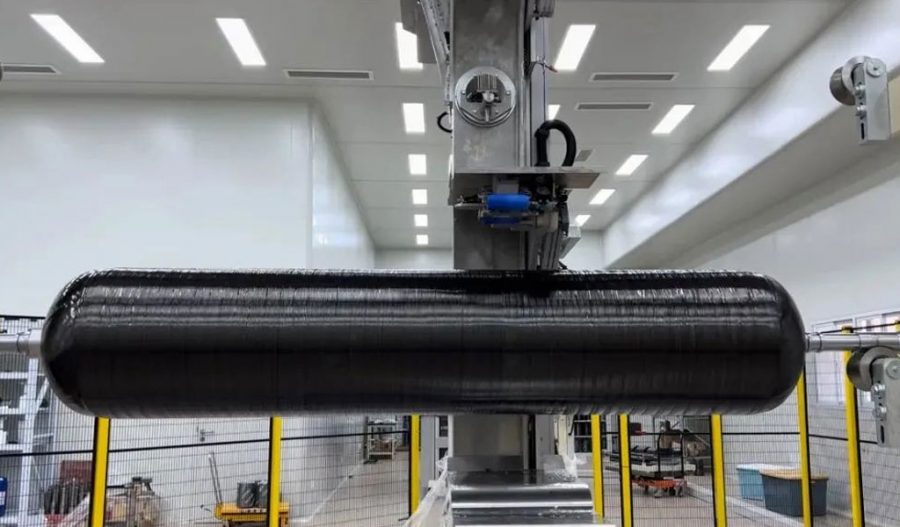
The transition towards a sustainable future is heavily reliant on clean energy sources, with hydrogen emerging as a promising alternative to fossil fuels. However, one of the significant challenges hindering the widespread adoption of hydrogen technology is efficient and safe storage. Traditional methods of hydrogen storage often fall short in terms of safety, weight, and efficiency. In recent years, aluminum forming centers have garnered attention for their pivotal role in producing robust hydrogen tanks. This article delves into the process of aluminum forming and its transformative impact on hydrogen storage technology.
Understanding the Need for Robust Hydrogen Tanks:
Hydrogen, touted as the clean energy carrier of the future, possesses immense potential in decarbonizing various sectors, including transportation, industry, and energy production. However, unlike conventional fuels, hydrogen has unique storage requirements. It is highly volatile and tends to leak easily, posing safety hazards. Moreover, to be viable for transportation applications, hydrogen storage systems must be lightweight, durable, and cost-effective.
Conventional storage methods such as compressed gas and liquid hydrogen entail significant drawbacks. Compressed gas tanks require high-pressure vessels, making them bulky and impractical for many applications. Liquid hydrogen, on the other hand, necessitates cryogenic temperatures, adding complexity and cost to the storage infrastructure. These limitations underscore the urgent need for innovative storage solutions that can address safety concerns while maximizing efficiency.
Enter Aluminum Forming Centers:
Aluminum forming centers represent a cutting-edge approach to manufacturing lightweight yet robust hydrogen tanks. These facilities leverage advanced forming techniques and materials to produce tanks that meet stringent performance standards. At the heart of this technology lies aluminum, a versatile metal known for its strength-to-weight ratio, corrosion resistance, and recyclability.
The process of aluminum forming involves shaping aluminum alloys into intricate geometries through various techniques such as hydroforming, stamping, and extrusion. These methods allow for the creation of complex tank designs tailored to specific applications. By optimizing the geometry and thickness of tank components, aluminum forming centers can enhance structural integrity while minimizing weight.
Hydrogen Tank Forming Process
Key Advantages of Aluminum Forming in Hydrogen Tank Production
- Strength and Durability: Aluminum alloys offer exceptional mechanical properties, allowing hydrogen tanks to withstand high pressures and environmental stresses. By employing advanced forming techniques, aluminum forming centers can enhance the structural integrity of tank components, reducing the risk of leaks or ruptures.
- Weight Reduction: The lightweight nature of aluminum translates to significant weight savings in hydrogen tank construction. This is particularly crucial for applications such as fuel cell vehicles, where reducing vehicle mass can improve efficiency and performance. Aluminum forming allows for the creation of lightweight yet durable tank structures, enabling greater energy density and extended driving range.
- Corrosion Resistance: Hydrogen storage environments can be corrosive, particularly in the presence of impurities or moisture. Aluminum alloys exhibit excellent corrosion resistance, ensuring long-term reliability and safety of hydrogen tanks. Through proper surface treatment and alloy selection, aluminum forming centers can further enhance corrosion resistance, prolonging the service life of hydrogen storage systems.
- Cost-Effectiveness: While initial investments in aluminum forming technology may be substantial, the long-term benefits outweigh the costs. Aluminum’s abundance and recyclability contribute to cost-effective manufacturing processes, reducing reliance on expensive raw materials. Moreover, the durability and longevity of aluminum-based hydrogen tanks result in lower maintenance and replacement expenses over their operational lifespan.
- Design Flexibility: Aluminum forming techniques offer unparalleled design flexibility, allowing engineers to create custom tank shapes and configurations to suit specific application requirements. Whether it’s optimizing internal volume, integrating mounting points, or enhancing thermal management, aluminum forming enables tailored solutions that maximize storage efficiency and usability.
Case Studies: Implementing Aluminum Formed Hydrogen Tanks
- Automotive Sector: Several automotive manufacturers have embraced aluminum formed hydrogen tanks as a viable solution for fuel cell vehicles. By leveraging lightweight materials and innovative tank designs, these vehicles achieve competitive driving ranges and performance metrics. Additionally, aluminum’s recyclability aligns with the automotive industry’s sustainability goals, further driving adoption.
- Aerospace Applications: Aluminum forming technology has found applications in the aerospace sector, where lightweight yet robust storage solutions are critical. By partnering with aluminum forming centers, aerospace companies can develop hydrogen storage systems that meet stringent safety and performance standards for space exploration missions and satellite propulsion.
- Renewable Energy Infrastructure: In the realm of renewable energy, aluminum formed hydrogen tanks play a vital role in storing excess energy generated from sources such as wind and solar power. These tanks enable efficient hydrogen production through electrolysis, facilitating energy storage and grid stabilization. Moreover, the scalability of aluminum forming technology makes it suitable for large-scale storage applications in renewable energy installations.
Future Directions and Challenges:
While aluminum forming holds tremendous potential for advancing hydrogen storage technology, several challenges remain to be addressed. These include optimizing manufacturing processes for scalability and cost-efficiency, ensuring compatibility with emerging hydrogen production methods, and enhancing safety standards to meet regulatory requirements. Collaboration between industry stakeholders, research institutions, and government agencies will be crucial in overcoming these challenges and accelerating the adoption of aluminum formed hydrogen tanks on a global scale.
Conclusion:
Aluminum forming centers represent a cornerstone in the quest for efficient and safe hydrogen storage solutions. By harnessing the inherent properties of aluminum alloys and leveraging advanced forming techniques, these facilities enable the production of lightweight, durable, and cost-effective hydrogen tanks. From automotive to aerospace applications, aluminum formed hydrogen tanks are driving innovation across various sectors, paving the way for a sustainable energy future. As the demand for clean energy continues to grow, the role of aluminum forming in hydrogen storage is poised to become even more significant, ushering in a new era of renewable energy utilization and environmental stewardship.
Maximize Tooling and CNC Metal Spinning Capabilities.
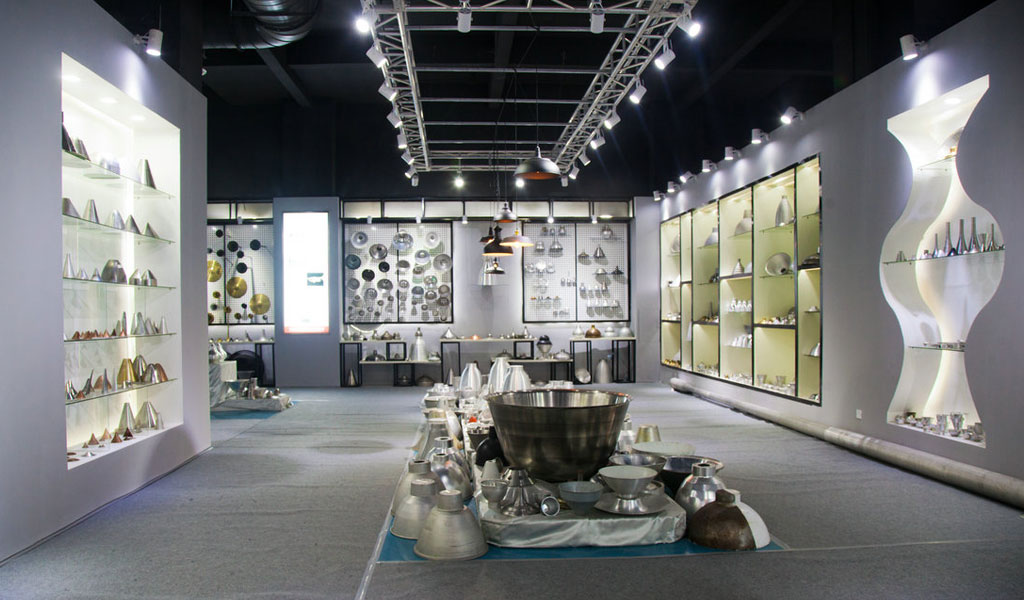
At BE-CU China Metal Spinning company, we make the most of our equipment while monitoring signs of excess wear and stress. In addition, we look into newer, modern equipment and invest in those that can support or increase our manufacturing capabilities. Our team is very mindful of our machines and tools, so we also routinely maintain them to ensure they don’t negatively impact your part’s quality and productivity.
Talk to us today about making a rapid prototype with our CNC metal spinning service. Get a direct quote by chatting with us here or request a free project review.
BE-CU China CNC Metal Spinning service include : CNC Metal Spinning,Metal Spinning Die,Laser Cutting, Tank Heads Spinning,Metal Hemispheres Spinning,Metal Cones Spinning,Metal Dish-Shaped Spinning,Metal Trumpet Spinning,Metal Venturi Spinning,Aluminum Spinning Products,Stainless Steel Spinning Products,Copper Spinning Products,Brass Spinning Products,Steel Spinning Product,Metal Spinnin LED Reflector,Metal Spinning Pressure Vessel,