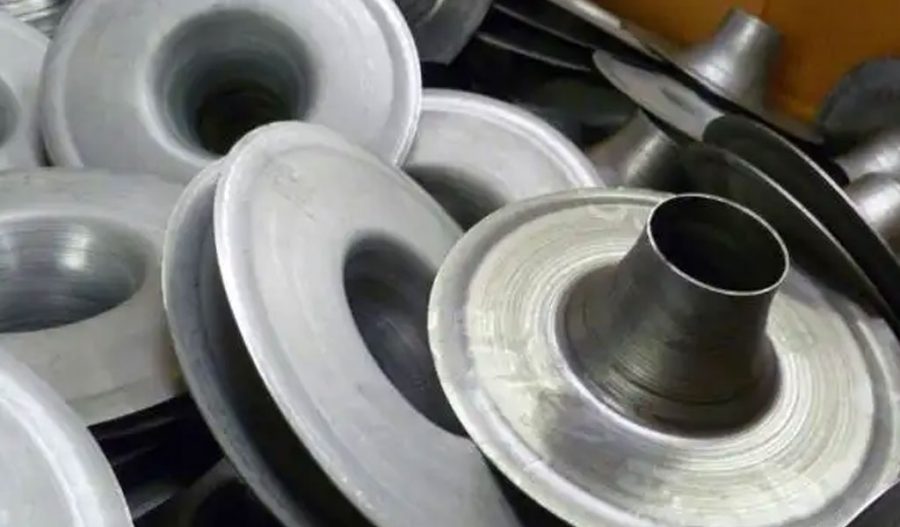
A metal lathe is a fundamental machine tool utilized in various manufacturing processes to shape and finish metal workpieces. The speed at which a metal lathe spins—commonly referred to as spindle speed—is a critical parameter that significantly influences machining operations. This article explores the factors affecting spindle speed, typical speed ranges, and their implications for different machining tasks.
Spindle Speed: Definition and Importance
Spindle speed is defined as the rotational speed of the lathe’s spindle, typically measured in revolutions per minute (RPM). It is an essential variable in turning operations, as it affects cutting efficiency, surface finish quality, and tool wear. The optimal spindle speed for a specific operation depends on several factors, including the material being machined, the type of cutting tool used, and the diameter of the workpiece.
Factors Affecting Spindle Speed
- Material of the Workpiece: Different metals exhibit varying machinability characteristics. For example, softer materials such as aluminum can be machined at higher speeds, whereas harder materials like stainless steel require lower speeds to prevent tool wear and overheating.
- Diameter of the Workpiece: The diameter of the workpiece directly impacts the cutting speed. As the diameter increases, the linear speed at the outer edge of the workpiece increases, necessitating a reduction in spindle speed to maintain an appropriate cutting speed.
- Type of Cutting Tool: The material and geometry of the cutting tool play a significant role in determining the suitable spindle speed. High-speed steel (HSS) tools may require different speeds compared to carbide tools, which are designed for higher cutting speeds due to their hardness and heat resistance.
- Cutting Conditions: Factors such as depth of cut, feed rate, and lubrication also influence the choice of spindle speed. Increased depth of cut or feed rate may necessitate a reduction in spindle speed to maintain the integrity of the tool and workpiece.
Typical Spindle Speed Ranges
The spindle speed of a metal lathe can vary widely depending on the machine’s design and intended application. Most lathes offer a range of speeds, commonly from 50 RPM to over 3000 RPM.
- Low-Speed Operations (50 – 500 RPM): These speeds are typically used for larger workpieces or harder materials. At lower speeds, the cutting forces are manageable, allowing for deeper cuts without compromising tool integrity.
- Medium-Speed Operations (500 – 1500 RPM): These speeds are suitable for a broad range of materials, including mild steels and aluminum. Medium speeds allow for a balance between cutting efficiency and tool longevity.
- High-Speed Operations (1500 – 3000+ RPM): High speeds are often used for machining softer materials and smaller diameters, such as brass or aluminum. At these speeds, the cutting process can be efficient, producing finer surface finishes.
Calculating Optimal Spindle Speed
The optimal spindle speed for a given machining operation can be calculated using the following formula:
RPM=CS×12/π×D
Where:
- RPM = Revolutions per minute
- CS = Cutting speed (typically in feet per minute)
- D = Diameter of the workpiece (in inches)
Cutting speed values vary based on the material; for instance, the cutting speed for aluminum might be around 600 to 1200 feet per minute, while for stainless steel, it could range from 50 to 150 feet per minute.
Conclusion
Understanding spindle speed is crucial for effective metal lathe operations. The relationship between spindle speed, material properties, and machining parameters determines the success of turning operations. By carefully considering these factors and calculating optimal speeds, machinists can enhance efficiency, ensure high-quality finishes, and prolong the life of cutting tools. The proper selection and adjustment of spindle speed ultimately contribute to the overall productivity and cost-effectiveness of metalworking processes.
Maximize Tooling and CNC Metal Spinning Capabilities.
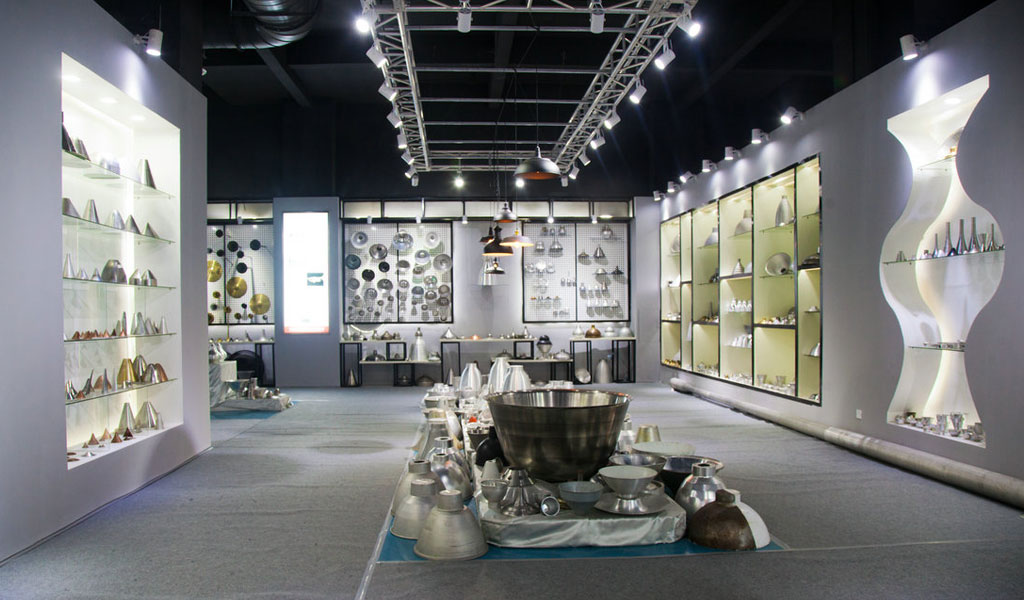
At BE-CU China Metal Spinning company, we make the most of our equipment while monitoring signs of excess wear and stress. In addition, we look into newer, modern equipment and invest in those that can support or increase our manufacturing capabilities. Our team is very mindful of our machines and tools, so we also routinely maintain them to ensure they don’t negatively impact your part’s quality and productivity.
Talk to us today about making a rapid prototype with our CNC metal spinning service. Get a direct quote by chatting with us here or request a free project review.
BE-CU China CNC Metal Spinning service include : CNC Metal Spinning,Metal Spinning Die,Laser Cutting, Tank Heads Spinning,Metal Hemispheres Spinning,Metal Cones Spinning,Metal Dish-Shaped Spinning,Metal Trumpet Spinning,Metal Venturi Spinning,Aluminum Spinning Products,Stainless Steel Spinning Products,Copper Spinning Products,Brass Spinning Products,Steel Spinning Product,Metal Spinnin LED Reflector,Metal Spinning Pressure Vessel,