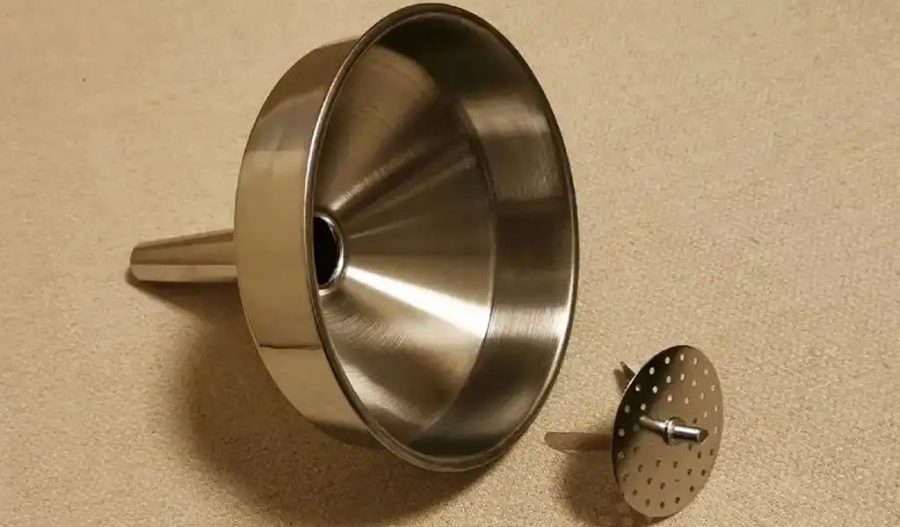
Custom round stainless steel hoppers are specialized industrial containers designed to store, transport, and dispense bulk materials such as powders, granules, liquids, or irregularly shaped solids. These hoppers are widely utilized across industries including pharmaceuticals, food processing, chemical manufacturing, agriculture, and materials handling due to their durability, corrosion resistance, and hygienic properties. The process of customizing a round stainless steel hopper involves a multidisciplinary approach, integrating materials science, mechanical engineering, and fabrication techniques to meet specific operational requirements. This article explores the comprehensive methodology for designing and fabricating custom round stainless steel hoppers, delving into material selection, design considerations, manufacturing processes, finishing techniques, and performance optimization, with detailed comparative tables to elucidate key variables.
Stainless steel, an alloy primarily composed of iron, chromium (minimum 10.5% by mass), and often nickel, molybdenum, or other elements, is the material of choice for hoppers due to its exceptional properties. The chromium content forms a passive layer of chromium oxide (Cr₂O₃) on the surface, which protects against rust and corrosion, making it ideal for environments involving moisture, acidic substances, or hygienic standards. Round hoppers, as opposed to square or rectangular designs, offer advantages such as improved material flow, reduced dead zones where material may accumulate, and enhanced structural integrity under pressure. Customization allows these hoppers to be tailored to specific applications, such as integrating with existing machinery, handling unique material properties, or adhering to regulatory standards like those set by the Food and Drug Administration (FDA) or the American Society of Mechanical Engineers (ASME).
The process of creating a custom round stainless steel hopper begins with defining the operational requirements. Engineers must consider the type of material to be handled—its particle size, density, flowability, abrasiveness, and corrosiveness—as well as the hopper’s intended function, whether it is storage, feeding into a conveyor, or dispensing into a mixing vessel. For instance, fine powders like pharmaceutical excipients require smooth, polished surfaces to prevent adhesion, while abrasive materials like sand necessitate thicker walls and wear-resistant grades of stainless steel. Volume capacity, typically ranging from a few liters to several cubic meters, is another critical parameter, as is the hopper’s discharge mechanism, which may involve gravity flow, pneumatic assistance, or mechanical agitation.
Material selection is a foundational step in hopper customization. Stainless steel Grades 304 and 316 are the most commonly employed due to their balance of cost, availability, and performance. Grade 304, containing 18% chromium and 8% nickel (18/8 stainless), is suitable for general-purpose applications with moderate corrosion resistance. Grade 316, with an additional 2-3% molybdenum, offers superior resistance to pitting and crevice corrosion, making it preferable for acidic or chloride-rich environments, such as those encountered in chemical processing or marine applications. For highly abrasive conditions, martensitic stainless steels like Grade 410, which can be heat-treated for increased hardness, may be considered, though they sacrifice some corrosion resistance. The choice of grade impacts not only durability but also fabrication complexity and cost, as detailed in Table 1 below.
Table 1: Comparison of Stainless Steel Grades for Hopper Fabrication
Grade | Composition | Corrosion Resistance | Hardness | Cost (Relative) | Typical Applications |
---|---|---|---|---|---|
304 | 18% Cr, 8% Ni | Moderate | Low-Moderate | Low | Food processing, general storage |
316 | 16-18% Cr, 10-14% Ni, 2-3% Mo | High | Moderate | Medium-High | Pharmaceuticals, chemicals |
410 | 11.5-13.5% Cr | Low-Moderate | High | Low-Medium | Abrasive materials, dry solids |
317 | 18-20% Cr, 11-15% Ni, 3-4% Mo | Very High | Moderate | High | Highly acidic environments |
Once the material is selected, the design phase involves determining the hopper’s geometry. A round hopper typically features a cylindrical upper section transitioning to a conical lower section, with the cone angle tailored to the material’s angle of repose—the steepest angle at which a pile of loose material remains stable without slumping. For free-flowing materials like grains (angle of repose ~25-35°), a cone angle of 45-60° ensures smooth discharge, while cohesive powders like flour (angle of repose ~45-55°) may require steeper angles (60-70°) or additional flow aids like vibrators. The diameter of the cylindrical section and the outlet size are calculated using mass flow principles, ensuring the hopper avoids arching (where material forms a stable bridge over the outlet) or ratholing (where material flows only from the center, leaving stagnant zones). Computational fluid dynamics (CFD) simulations or empirical flowability tests, such as those using a Jenike shear cell, can refine these parameters.
The wall thickness of the hopper is another critical design consideration, balancing structural integrity with weight and cost. For a 1-meter diameter hopper holding 1 cubic meter of material with a density of 1000 kg/m³, the hoop stress (σ) in the cylindrical section can be approximated using the formula σ = (P × r) / t, where P is the internal pressure, r is the radius, and t is the thickness. Assuming a static load equivalent to atmospheric pressure plus material weight (approximately 10 kPa), a 500 mm radius, and a safety factor of 2, a Grade 304 stainless steel hopper (yield strength ~205 MPa) requires a minimum thickness of 0.5 mm. However, practical designs often use 1.5-3 mm thicknesses to account for dynamic loads, fabrication tolerances, and wear over time.
Manufacturing a custom round stainless steel hopper involves several fabrication techniques, each chosen based on precision, scalability, and cost. Sheet metal forming is the primary method, where flat stainless steel sheets are cut, rolled, and welded into the desired shape. Laser cutting or water jet cutting ensures precise dimensions for the cylindrical and conical sections, with tolerances as tight as ±0.1 mm for high-end applications. The rolling process uses a three-roll bending machine to curve the sheet into a cylinder, with the radius controlled by adjusting the roller positions. For the conical section, a flat sheet is cut into a sector of a circle, rolled into a cone, and seam-welded along the joint. Gas tungsten arc welding (GTAW), commonly known as TIG welding, is preferred for its clean, high-quality welds, using a filler rod compatible with the base material (e.g., 308L for 304 stainless).
Seam welding introduces potential weak points, so non-destructive testing (NDT) methods like dye penetrant inspection or X-ray radiography are employed to detect cracks or inclusions. For seamless designs, particularly smaller hoppers, metal spinning—a cold-forming process where a flat disc is rotated and shaped over a mandrel—offers an alternative. This technique, while limited to thinner materials (typically <2 mm), eliminates welds, enhancing hygiene and strength. Larger hoppers may require segmented construction, where multiple rolled sections are welded together, followed by grinding and polishing to smooth the interior.
Surface finishing is a pivotal step in hopper customization, particularly for sanitary applications. Stainless steel’s as-rolled surface (No. 1 finish) is rough and unsuitable for most uses, so mechanical polishing or electropolishing is applied. A 2B finish (cold-rolled, annealed, and pickled) provides a smooth, moderately reflective surface, while a No. 4 finish (brushed) offers a finer texture suitable for food-grade hoppers. Electropolishing, an electrochemical process, removes a thin layer of material (10-40 µm), enhancing smoothness (Ra < 0.8 µm) and passivating the surface for maximum corrosion resistance. Table 2 compares these finishes based on roughness, cost, and application.
Table 2: Comparison of Stainless Steel Surface Finishes
Finish | Roughness (Ra, µm) | Process | Cost (Relative) | Applications |
---|---|---|---|---|
No. 1 | 3.2-12.5 | Hot-rolled, annealed | Low | Structural, non-hygienic |
2B | 0.1-0.5 | Cold-rolled, pickled | Medium | General-purpose, moderate hygiene |
No. 4 | 0.2-0.8 | Brushed | Medium-High | Food processing, decorative |
Electropolished | <0.8 | Electrochemical | High | Pharmaceuticals, ultra-hygienic |
Customization extends to integrating auxiliary features. Discharge valves (e.g., butterfly, slide, or rotary) are selected based on material flow control needs, with stainless steel construction ensuring compatibility. For sticky or cohesive materials, vibrators or air cannons can be mounted to the hopper walls, dislodging buildup without compromising structural integrity. Lifting lugs, caster wheels, or forklift channels enhance mobility, while sight glasses or level sensors provide operational monitoring. These features must be designed to withstand the hopper’s operating conditions, such as temperature extremes (-20°C to 200°C for standard stainless grades) or pressure fluctuations.
Quality assurance is integral to the customization process. Beyond NDT, pressure testing (e.g., hydrostatic testing at 1.5 times the design pressure) verifies structural integrity, while flow testing ensures the hopper meets discharge rate specifications. Compliance with standards like ASME Section VIII (for pressure vessels) or FDA 21 CFR Part 177 (for food contact) may be required, necessitating documentation of material traceability and fabrication processes. For instance, a hopper destined for pharmaceutical use might undergo a riboflavin test, where a fluorescent dye is applied and rinsed to confirm no residual contaminants remain in crevices.
The performance of a custom round stainless steel hopper is ultimately validated in its operational context. A hopper designed for a flour mill, for example, must maintain a consistent discharge rate of 500 kg/h into a pneumatic conveyor, while one for a chemical plant handling sodium hydroxide pellets must resist caustic corrosion over a 10-year lifespan. Iterative feedback from end-users—such as adjustments to cone angle or outlet diameter—refines the design, ensuring alignment with real-world demands. Table 3 summarizes key performance metrics across industries.
Table 3: Performance Metrics for Custom Hoppers by Industry
Industry | Material Example | Cone Angle (°) | Discharge Rate | Lifespan (Years) | Key Requirement |
---|---|---|---|---|---|
Food Processing | Flour | 60-70 | 300-1000 kg/h | 10-15 | Hygiene, smooth flow |
Pharmaceuticals | Lactose Powder | 55-65 | 50-200 kg/h | 15-20 | Contamination prevention |
Chemical | NaOH Pellets | 45-60 | 1000-5000 kg/h | 8-12 | Corrosion resistance |
Agriculture | Grain | 40-50 | 2000-10,000 kg/h | 15-25 | High capacity, durability |
Maximize Tooling and CNC Metal Spinning Capabilities.
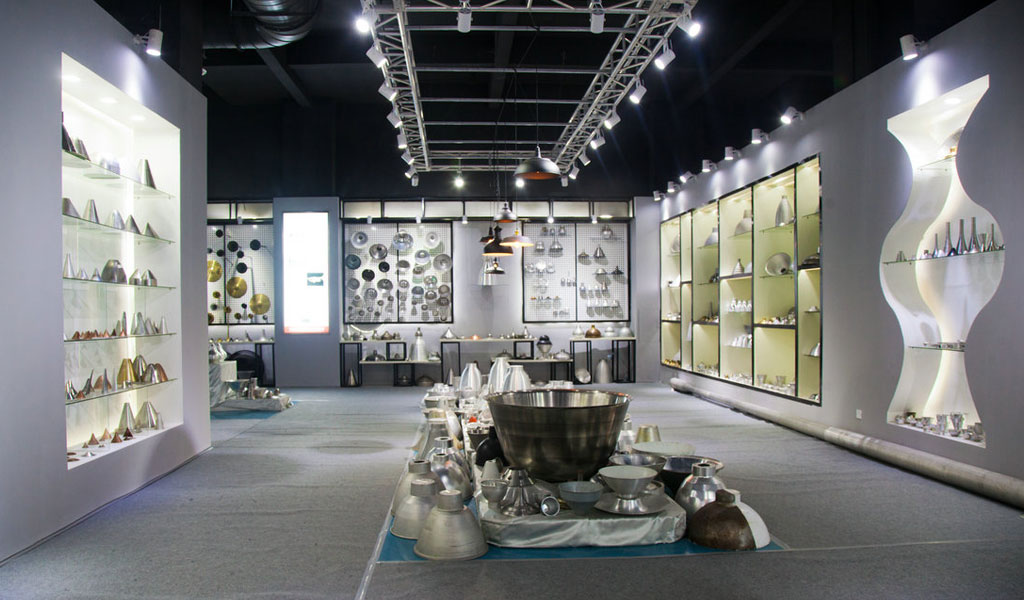
At BE-CU China Metal Spinning company, we make the most of our equipment while monitoring signs of excess wear and stress. In addition, we look into newer, modern equipment and invest in those that can support or increase our manufacturing capabilities. Our team is very mindful of our machines and tools, so we also routinely maintain them to ensure they don’t negatively impact your part’s quality and productivity.
Talk to us today about making a rapid prototype with our CNC metal spinning service. Get a direct quote by chatting with us here or request a free project review.
BE-CU China CNC Metal Spinning service include : CNC Metal Spinning,Metal Spinning Die,Laser Cutting, Tank Heads Spinning,Metal Hemispheres Spinning,Metal Cones Spinning,Metal Dish-Shaped Spinning,Metal Trumpet Spinning,Metal Venturi Spinning,Aluminum Spinning Products,Stainless Steel Spinning Products,Copper Spinning Products,Brass Spinning Products,Steel Spinning Product,Metal Spinnin LED Reflector,Metal Spinning Pressure Vessel,