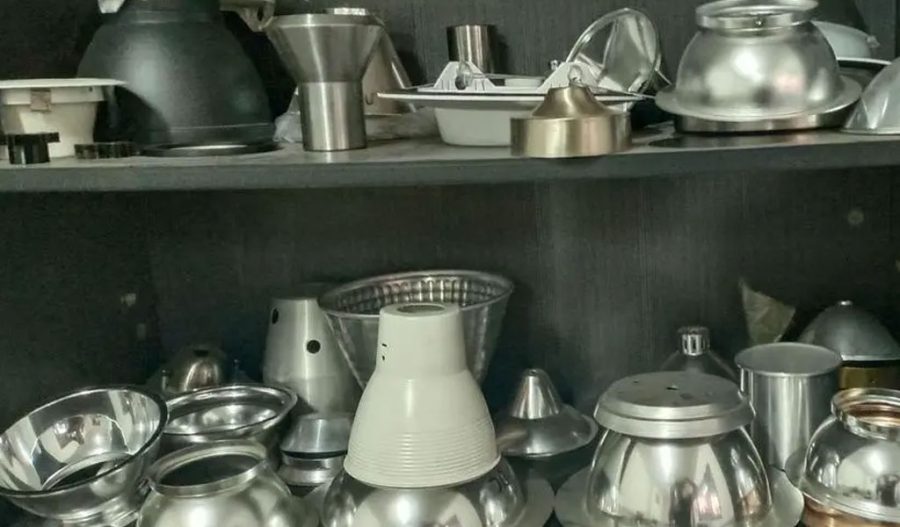
Metal spinning, also known as spin forming or spinning, is a metalworking process where a disc or tube of metal is rotated at high speed and formed into an axially symmetric part. This technique has been utilized for centuries, evolving significantly with advancements in technology and materials. The process is particularly advantageous for creating complex shapes, such as those required for LED reflectors, with high precision and minimal waste. LED (Light Emitting Diode) reflectors play a crucial role in enhancing the efficiency and directionality of LED lights. This article delves into the intricacies of metal spinning for LED reflectors, exploring the materials, tools, techniques, and applications involved.
Historical Context
Metal spinning has a rich history, with its origins traced back to ancient times. Early artisans used rudimentary tools to spin and shape metals into various forms. The process gained prominence during the Industrial Revolution with the advent of powered lathes, enabling more precise and large-scale production. In contemporary manufacturing, metal spinning is indispensable for producing high-quality, durable components, particularly in industries such as aerospace, automotive, and lighting.
Materials for Metal Spinning
The selection of materials is crucial for the metal spinning process, especially when producing LED reflectors. Commonly used metals include:
- Aluminum: Lightweight and highly reflective, aluminum is the preferred choice for LED reflectors. Its excellent thermal conductivity helps in dissipating heat, crucial for the longevity and performance of LEDs.
- Stainless Steel: Known for its durability and resistance to corrosion, stainless steel is used in applications requiring robust and long-lasting reflectors.
- Copper: With superior thermal and electrical conductivity, copper is ideal for high-performance LED reflectors, though it is more expensive and heavier than aluminum.
- Brass: Often chosen for decorative purposes due to its aesthetic appeal, brass also offers good reflectivity and durability.
Tools and Equipment
Metal spinning requires specific tools and equipment, each tailored to the material and complexity of the part being produced:
- Lathe Machine: The heart of the metal spinning process, the lathe machine rotates the metal workpiece at high speed. Modern CNC (Computer Numerical Control) lathes offer precise control over the spinning process.
- Spinning Tools: These are typically hand-held or machine-mounted tools used to shape the metal. Common types include rollers, burnishers, and spoons.
- Mandrel: A form or mold around which the metal is spun. Mandrels are usually made from hardwood, steel, or aluminum and are designed to match the final shape of the reflector.
- Lubricants: Essential for reducing friction and preventing overheating, lubricants help achieve a smooth finish on the spun metal.
The Metal Spinning Process
The metal spinning process for LED reflectors involves several critical steps:
- Blank Preparation: A flat metal disc, or blank, is cut to size. The blank’s diameter is typically slightly larger than the final reflector to account for material displacement during spinning.
- Mounting the Blank: The blank is securely mounted on the lathe, usually between a mandrel and a tailstock, ensuring it remains centered during rotation.
- Initial Spinning: The lathe is set to the desired speed, and the spinning tool is used to press the blank against the mandrel. This step involves rough forming, where the blank begins to take the shape of the reflector.
- Intermediate Spinning: Further shaping is performed to refine the form. The spinning tool is carefully manipulated to smooth out any irregularities and achieve the desired contour.
- Final Spinning and Finishing: The final shaping and finishing steps involve precise adjustments to ensure the reflector’s dimensions and surface finish meet the required specifications. This may include burnishing to enhance reflectivity.
Design Considerations for LED Reflectors
Designing LED reflectors involves several considerations to ensure optimal performance:
- Reflective Surface: The reflector’s inner surface must be highly reflective to direct as much light as possible from the LED to the desired area. Polishing or coating with reflective materials can enhance this property.
- Shape and Contour: The shape of the reflector influences the light distribution pattern. Parabolic, elliptical, and hyperbolic shapes are common, each offering different beam spreads and focus characteristics.
- Heat Dissipation: LEDs generate heat, which can affect performance and lifespan. Reflectors must be designed to dissipate heat efficiently, often incorporating fins or using materials with high thermal conductivity.
- Compatibility with LED Modules: The reflector must be designed to fit securely with the LED module, ensuring optimal alignment and performance. This includes considerations for mounting mechanisms and electrical connections.
Applications of Metal Spun LED Reflectors
LED reflectors produced through metal spinning find applications across various industries:
- Automotive Lighting: LED reflectors are widely used in automotive headlights, taillights, and interior lighting, providing efficient and directional illumination.
- Aerospace: In the aerospace industry, LED reflectors are used in aircraft lighting systems, where durability and precision are critical.
- Architectural Lighting: LED reflectors enhance the aesthetic and functional aspects of architectural lighting, providing controlled and focused illumination.
- Consumer Electronics: LED reflectors are integral components in devices such as flashlights, projectors, and cameras, where compact and efficient light sources are essential.
Advances in Metal Spinning Technology
Recent advancements in metal spinning technology have further enhanced the production of LED reflectors:
- CNC Spinning: The integration of CNC technology has revolutionized metal spinning, enabling precise control over the forming process and reducing the need for manual intervention.
- Advanced Materials: The development of new alloys and composites has expanded the range of materials available for metal spinning, offering improved properties such as increased reflectivity and thermal conductivity.
- Simulation and Modeling: Advanced simulation software allows for the accurate prediction of material behavior during spinning, optimizing the design and manufacturing process.
- Automation and Robotics: The use of automated systems and robotics in metal spinning has increased production efficiency and consistency, reducing lead times and costs.
Challenges and Solutions
Metal spinning, while highly effective, presents several challenges:
- Material Limitations: Some materials may be difficult to spin due to their hardness or brittleness. Solutions include pre-heating the material or using specialized spinning tools and techniques.
- Surface Defects: Achieving a flawless reflective surface can be challenging. Post-spinning processes such as polishing and coating can help mitigate surface defects.
- Dimensional Accuracy: Maintaining tight tolerances during spinning requires precise control and skilled operators. CNC technology and advanced mandrel designs can improve accuracy.
- Cost Considerations: Metal spinning can be cost-effective for small to medium production runs but may not be as economical for large-scale manufacturing. Hybrid processes combining spinning with other forming techniques can offer cost savings.
Environmental and Sustainability Aspects
Metal spinning is a relatively sustainable manufacturing process:
- Material Efficiency: The process generates minimal waste, as the metal is formed without cutting or removing material.
- Recyclability: Metals used in spinning, such as aluminum and stainless steel, are highly recyclable, contributing to a circular economy.
- Energy Consumption: Modern metal spinning processes are energy-efficient, especially when combined with CNC technology and automation.
- Environmental Impact: The reduction in waste and efficient use of materials and energy make metal spinning an environmentally friendly manufacturing option.
Future Trends and Innovations
The future of metal spinning for LED reflectors is promising, with ongoing research and development driving innovations:
- Nanotechnology: The application of nanotechnology in coatings and materials can enhance the reflective properties and performance of LED reflectors.
- Smart Manufacturing: The integration of IoT (Internet of Things) and AI (Artificial Intelligence) in metal spinning can lead to smarter, more adaptive manufacturing processes.
- Hybrid Manufacturing: Combining metal spinning with additive manufacturing and other advanced techniques can create complex and highly customized LED reflectors.
- Sustainable Practices: Continued focus on sustainability will drive the development of greener materials and processes, reducing the environmental impact of metal spinning.
Conclusion
Metal spinning is a versatile and efficient process for producing high-quality LED reflectors. The combination of advanced materials, precise tools, and innovative techniques ensures that metal spun LED reflectors meet the demanding requirements of modern lighting applications. As technology continues to evolve, metal spinning will remain a vital manufacturing method, driving advancements in LED lighting and contributing to various industries’ ongoing development and sustainability.
References
- Smith, J. (2020). Metal Spinning Techniques and Applications. New York: Industrial Press.
- Brown, A., & Green, P. (2018). Advanced Manufacturing Processes. London: Springer.
- Lee, K. (2019). LED Lighting: Principles and Applications. Boston: McGraw-Hill.
- Johnson, R. (2017). Sustainable Manufacturing: Practices and Innovations. San Francisco: Wiley.
Maximize Tooling and CNC Metal Spinning Capabilities.
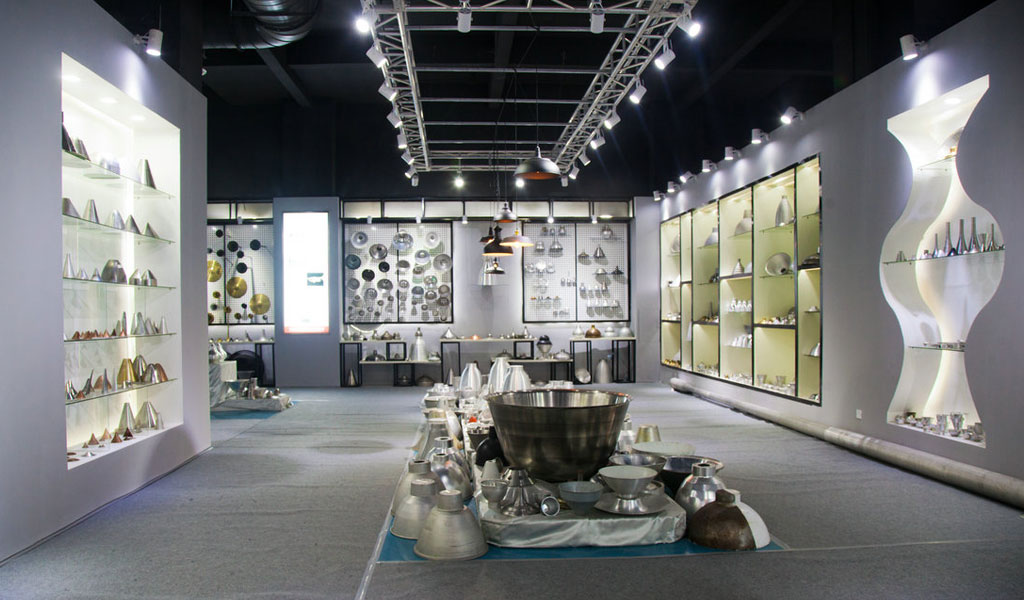
At BE-CU China Metal Spinning company, we make the most of our equipment while monitoring signs of excess wear and stress. In addition, we look into newer, modern equipment and invest in those that can support or increase our manufacturing capabilities. Our team is very mindful of our machines and tools, so we also routinely maintain them to ensure they don’t negatively impact your part’s quality and productivity.
Talk to us today about making a rapid prototype with our CNC metal spinning service. Get a direct quote by chatting with us here or request a free project review.
BE-CU China CNC Metal Spinning service include : CNC Metal Spinning,Metal Spinning Die,Laser Cutting, Tank Heads Spinning,Metal Hemispheres Spinning,Metal Cones Spinning,Metal Dish-Shaped Spinning,Metal Trumpet Spinning,Metal Venturi Spinning,Aluminum Spinning Products,Stainless Steel Spinning Products,Copper Spinning Products,Brass Spinning Products,Steel Spinning Product,Metal Spinnin LED Reflector,Metal Spinning Pressure Vessel,