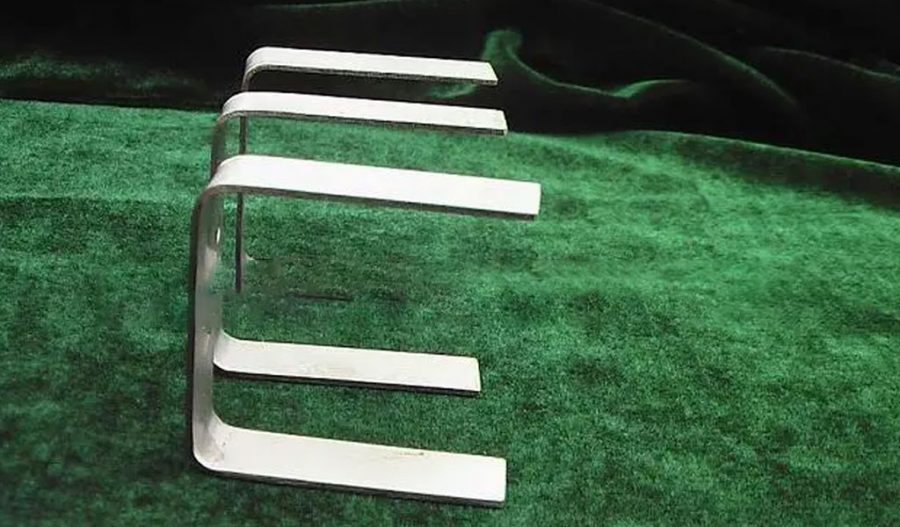
Manufacturing processes play a pivotal role in determining the quality, efficiency, and cost-effectiveness of metal parts. Hydroforming and metal stamping are two prevalent techniques used in the industry, each with its unique advantages and applications. Understanding the differences between these methods can help manufacturers make informed decisions about which process to choose for their specific needs. In this article, we will delve into the intricacies of hydroforming and metal stamping, comparing them across various parameters.
1. What is Hydroforming?
Hydroforming is a specialized metal forming process that uses high-pressure fluid to shape ductile metals into complex geometries. The process involves placing a metal blank or tube into a die and then injecting it with a pressurized fluid, typically water or oil, to force the metal into the shape of the die.
Advantages of Hydroforming:
- Complex Shapes: Hydroforming excels at producing parts with intricate geometries and complex shapes that would be difficult or impossible to achieve with traditional stamping methods.
- Reduced Material Waste: Since hydroforming utilizes a single piece of metal, it often results in less material waste compared to stamping, where cutting and shearing are involved.
- Improved Strength: The uniformity of metal distribution in hydroformed parts often leads to increased strength and durability.
2. What is Metal Stamping?
Metal stamping, also known as pressing, is a manufacturing process that uses dies and punches to convert flat metal sheets into specific shapes. The process involves placing the metal sheet between the dies and applying mechanical force to deform the metal into the desired shape.
Advantages of Metal Stamping:
- Cost-Effective for High Volume Production: Metal stamping is highly efficient for producing large quantities of parts, making it cost-effective for high-volume production runs.
- Accuracy and Precision: With advancements in technology, metal stamping can achieve high levels of accuracy and repeatability, ensuring consistent quality across parts.
- Wide Range of Materials: Metal stamping can be used with a variety of metals and alloys, offering flexibility in material selection.
Comparison Across Parameters
1. Complexity of Shapes:
- Hydroforming: Hydroforming is more suited for producing complex, three-dimensional shapes with smooth contours and varying wall thicknesses.
- Metal Stamping: While metal stamping can produce a wide range of shapes, it may struggle with complex geometries that require multiple forming steps or tool changes.
2. Material Utilization:
- Hydroforming: Hydroforming generally results in better material utilization due to the absence of cutting and shearing processes, leading to less waste.
- Metal Stamping: Metal stamping can result in significant material waste, especially when cutting out shapes from larger sheets or coils.
3. Tooling Costs:
- Hydroforming: Initial tooling costs for hydroforming can be higher due to the complexity of the dies and the need for high-pressure equipment.
- Metal Stamping: Tooling costs for metal stamping are generally lower, especially for simpler parts, making it more economical for low-volume runs.
4. Production Speed:
- Hydroforming: Hydroforming can be slower than metal stamping, especially for complex parts that require multiple forming steps.
- Metal Stamping: Metal stamping is typically faster and more suited for high-volume production due to its ability to produce multiple parts simultaneously.
5. Material Strength:
- Hydroforming: The uniform metal distribution in hydroformed parts often leads to improved material strength and durability.
- Metal Stamping: While metal stamping can produce strong parts, the mechanical deformation involved may lead to variations in material strength across the part.
Conclusion
Both hydroforming and metal stamping offer unique advantages and are suitable for different applications and production volumes. Hydroforming excels in producing complex shapes with reduced material waste and improved strength, making it ideal for applications requiring high precision and durability. On the other hand, metal stamping is more cost-effective for high-volume production runs and offers greater flexibility in material selection.
When choosing between hydroforming and metal stamping, manufacturers should consider factors such as part complexity, production volume, material utilization, and cost. By understanding the strengths and limitations of each process, manufacturers can make informed decisions that optimize both quality and cost-effectiveness for their specific needs.
There are three elements for processing stainless steel precision stamping parts: punch, mold, and material.
Maximize Tooling and CNC Metal Spinning Capabilities.
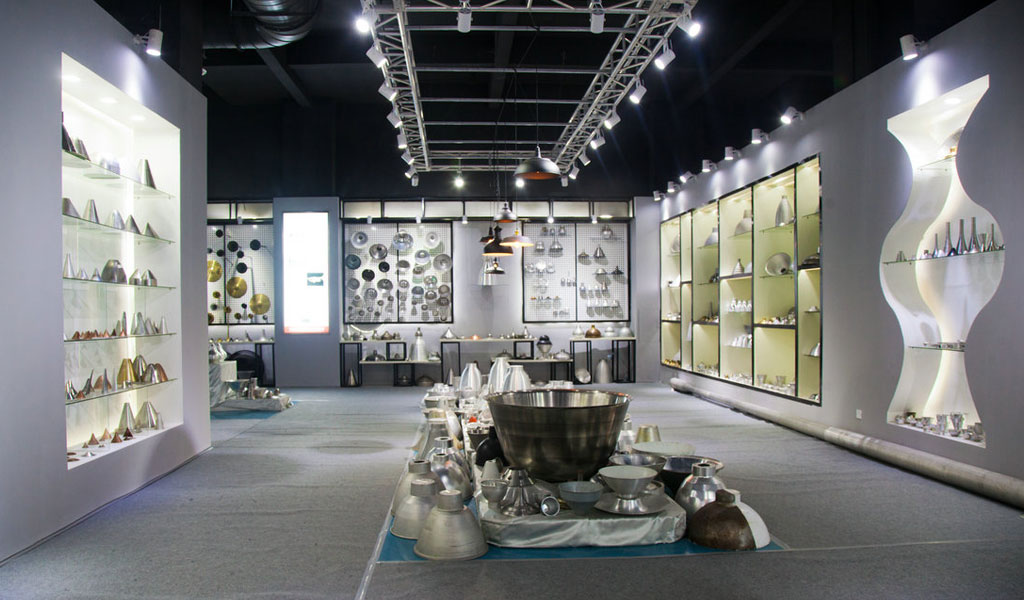
At BE-CU China Metal Spinning company, we make the most of our equipment while monitoring signs of excess wear and stress. In addition, we look into newer, modern equipment and invest in those that can support or increase our manufacturing capabilities. Our team is very mindful of our machines and tools, so we also routinely maintain them to ensure they don’t negatively impact your part’s quality and productivity.
Talk to us today about making a rapid prototype with our CNC metal spinning service. Get a direct quote by chatting with us here or request a free project review.
BE-CU China CNC Metal Spinning service include : CNC Metal Spinning,Metal Spinning Die,Laser Cutting, Tank Heads Spinning,Metal Hemispheres Spinning,Metal Cones Spinning,Metal Dish-Shaped Spinning,Metal Trumpet Spinning,Metal Venturi Spinning,Aluminum Spinning Products,Stainless Steel Spinning Products,Copper Spinning Products,Brass Spinning Products,Steel Spinning Product,Metal Spinnin LED Reflector,Metal Spinning Pressure Vessel,