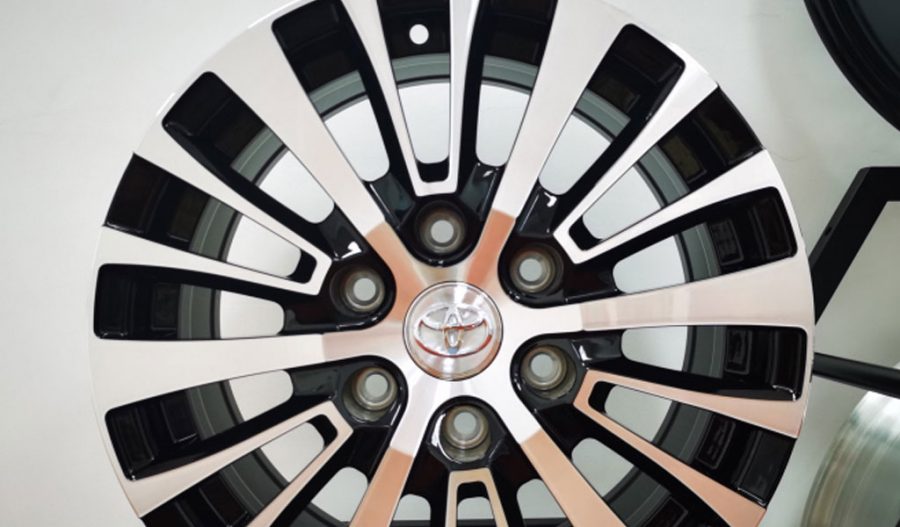
Expansion spinning is a critical manufacturing process used to produce thin-walled hemispherical heads, which are essential components in various industries, including aerospace, automotive, and chemical processing. This process involves the deformation of a thin-walled cylindrical blank into a hemispherical shape through a combination of rotational and axial forces. The large-reduction-rate thin-walled hemispherical head expansion spinning is particularly challenging due to the high risk of instability, which can lead to defects such as wrinkling, buckling, and fracture. This article delves into the instability research of this process, providing a comprehensive overview of the underlying mechanisms, influencing factors, and mitigation strategies.
Mechanisms of Instability
The instability in large-reduction-rate thin-walled hemispherical head expansion spinning can be attributed to several interrelated mechanisms:
- Wrinkling: This occurs when the material undergoes compressive stresses that exceed its yield strength, leading to localized deformations. Wrinkling is more pronounced in thin-walled structures due to their lower resistance to buckling.
- Buckling: This phenomenon arises when the axial load exceeds the critical buckling load of the material. In thin-walled structures, buckling can occur at relatively low loads, leading to significant deformations and potential failure.
- Fracture: High strain rates and localized stress concentrations can cause the material to fracture, particularly in regions with geometric discontinuities or material defects.
- Necking: This occurs when the material thins out excessively in certain regions, leading to a reduction in cross-sectional area and increased susceptibility to fracture.
Factors Influencing Instability
Several factors contribute to the instability in large-reduction-rate thin-walled hemispherical head expansion spinning:
- Material Properties: The mechanical properties of the material, such as yield strength, ductility, and strain hardening behavior, significantly influence the stability of the spinning process. Materials with higher ductility and strain hardening capabilities are less prone to instability.
- Geometric Parameters: The initial dimensions of the cylindrical blank, including wall thickness and diameter, play a crucial role in determining the stability of the process. Thinner walls and larger diameters increase the risk of instability.
- Process Parameters: The spinning speed, feed rate, and tool geometry are critical process parameters that affect the stability of the expansion spinning process. Higher spinning speeds and feed rates can lead to increased instability due to higher strain rates and localized stress concentrations.
- Tool Design: The design of the spinning tool, including its geometry and material, influences the distribution of stresses and strains during the spinning process. Optimized tool designs can help mitigate instability by reducing stress concentrations and ensuring uniform deformation.
Mitigation Strategies
To address the instability issues in large-reduction-rate thin-walled hemispherical head expansion spinning, various mitigation strategies have been developed:
- Material Selection: Choosing materials with higher ductility and strain hardening capabilities can enhance the stability of the spinning process. Alloys such as aluminum, titanium, and certain steels are commonly used due to their favorable mechanical properties.
- Process Optimization: Optimizing process parameters, such as spinning speed and feed rate, can help reduce the risk of instability. Lower spinning speeds and feed rates can minimize strain rates and stress concentrations, leading to more stable deformation.
- Tool Design Optimization: Designing spinning tools with optimized geometries and materials can help distribute stresses and strains more uniformly, reducing the risk of instability. Tools with rounded edges and smooth surfaces are preferred to minimize stress concentrations.
- Lubrication: Applying appropriate lubricants during the spinning process can reduce friction between the tool and the workpiece, leading to more uniform deformation and reduced risk of instability.
- Pre-forming: Pre-forming the cylindrical blank into an intermediate shape before the final spinning process can help distribute stresses and strains more evenly, reducing the risk of instability.
Comparative Analysis
To provide a clearer understanding of the factors influencing instability, a comparative analysis of different materials, geometric parameters, and process conditions is presented in the following tables:
Table 1: Comparison of Material Properties
Material | Yield Strength (MPa) | Ductility (%) | Strain Hardening Exponent | Instability Risk |
---|---|---|---|---|
Aluminum 6061 | 276 | 12 | 0.2 | Low |
Titanium Ti-6Al-4V | 825 | 14 | 0.3 | Moderate |
Stainless Steel 304 | 205 | 40 | 0.4 | Low |
Copper | 70 | 45 | 0.5 | Low |
Table 2: Comparison of Geometric Parameters
Wall Thickness (mm) | Diameter (mm) | Instability Risk |
---|---|---|
1.0 | 100 | High |
1.5 | 100 | Moderate |
2.0 | 100 | Low |
1.0 | 150 | Very High |
1.5 | 150 | High |
2.0 | 150 | Moderate |
Table 3: Comparison of Process Parameters
Spinning Speed (rpm) | Feed Rate (mm/min) | Instability Risk |
---|---|---|
500 | 10 | Low |
1000 | 10 | Moderate |
1500 | 10 | High |
500 | 20 | Moderate |
1000 | 20 | High |
1500 | 20 | Very High |
Case Studies
Several case studies have been conducted to investigate the instability in large-reduction-rate thin-walled hemispherical head expansion spinning. These studies provide valuable insights into the practical challenges and solutions associated with this process.
Case Study 1: Aluminum 6061 Hemispherical Head
In this case study, an aluminum 6061 cylindrical blank with a wall thickness of 1.5 mm and a diameter of 100 mm was spun into a hemispherical head. The spinning speed was set at 1000 rpm, and the feed rate was 10 mm/min. The results showed that the process was stable, with minimal wrinkling and no buckling or fracture observed. The final hemispherical head exhibited uniform wall thickness and good dimensional accuracy.
Case Study 2: Titanium Ti-6Al-4V Hemispherical Head
This case study involved spinning a titanium Ti-6Al-4V cylindrical blank with a wall thickness of 1.0 mm and a diameter of 150 mm. The spinning speed was 500 rpm, and the feed rate was 20 mm/min. Despite the lower spinning speed, the process exhibited significant instability, with wrinkling and buckling observed in the final hemispherical head. The results highlighted the challenges associated with spinning thin-walled titanium blanks at large reduction rates.
Case Study 3: Stainless Steel 304 Hemispherical Head
In this case study, a stainless steel 304 cylindrical blank with a wall thickness of 2.0 mm and a diameter of 100 mm was spun into a hemispherical head. The spinning speed was 1500 rpm, and the feed rate was 10 mm/min. The process was stable, with no wrinkling, buckling, or fracture observed. The final hemispherical head exhibited uniform wall thickness and excellent dimensional accuracy, demonstrating the benefits of using materials with high ductility and strain hardening capabilities.
Conclusion
The instability research of large-reduction-rate thin-walled hemispherical head expansion spinning is a complex and multifaceted field. Understanding the underlying mechanisms, influencing factors, and mitigation strategies is crucial for achieving stable and defect-free spinning processes. By optimizing material selection, process parameters, tool design, and pre-forming techniques, manufacturers can significantly reduce the risk of instability and produce high-quality hemispherical heads for various industrial applications.
Future Research Directions
Future research in this area should focus on developing advanced simulation tools and experimental techniques to gain deeper insights into the instability mechanisms. Additionally, exploring the use of novel materials and hybrid manufacturing processes can open new avenues for improving the stability and efficiency of large-reduction-rate thin-walled hemispherical head expansion spinning. Collaboration between academia, industry, and research institutions will be essential for driving innovation and advancing the state-of-the-art in this critical manufacturing process.
Maximize Tooling and CNC Metal Spinning Capabilities.
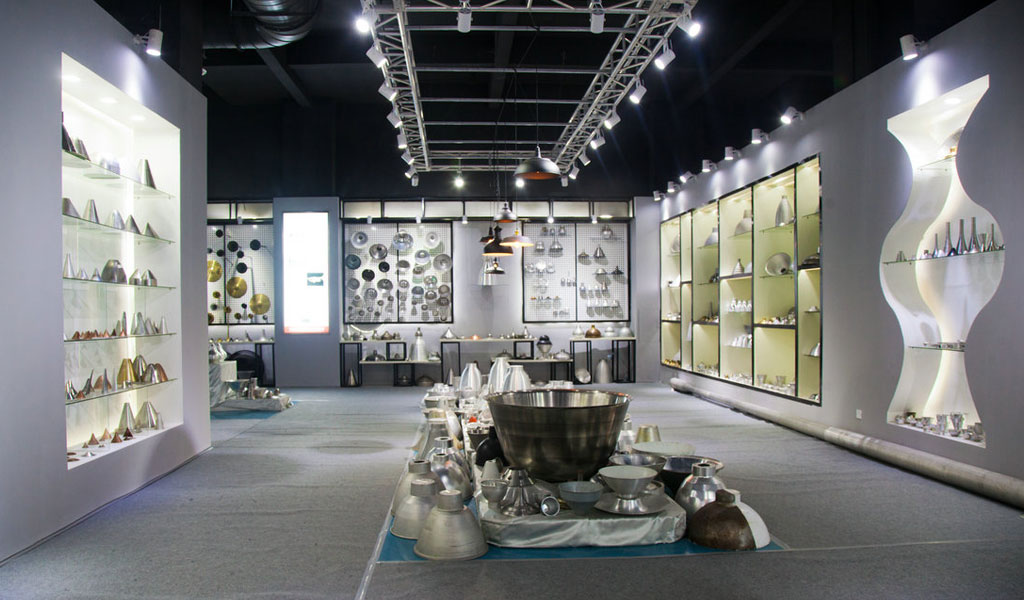
At BE-CU China Metal Spinning company, we make the most of our equipment while monitoring signs of excess wear and stress. In addition, we look into newer, modern equipment and invest in those that can support or increase our manufacturing capabilities. Our team is very mindful of our machines and tools, so we also routinely maintain them to ensure they don’t negatively impact your part’s quality and productivity.
Talk to us today about making a rapid prototype with our CNC metal spinning service. Get a direct quote by chatting with us here or request a free project review.
BE-CU China CNC Metal Spinning service include : CNC Metal Spinning,Metal Spinning Die,Laser Cutting, Tank Heads Spinning,Metal Hemispheres Spinning,Metal Cones Spinning,Metal Dish-Shaped Spinning,Metal Trumpet Spinning,Metal Venturi Spinning,Aluminum Spinning Products,Stainless Steel Spinning Products,Copper Spinning Products,Brass Spinning Products,Steel Spinning Product,Metal Spinnin LED Reflector,Metal Spinning Pressure Vessel,