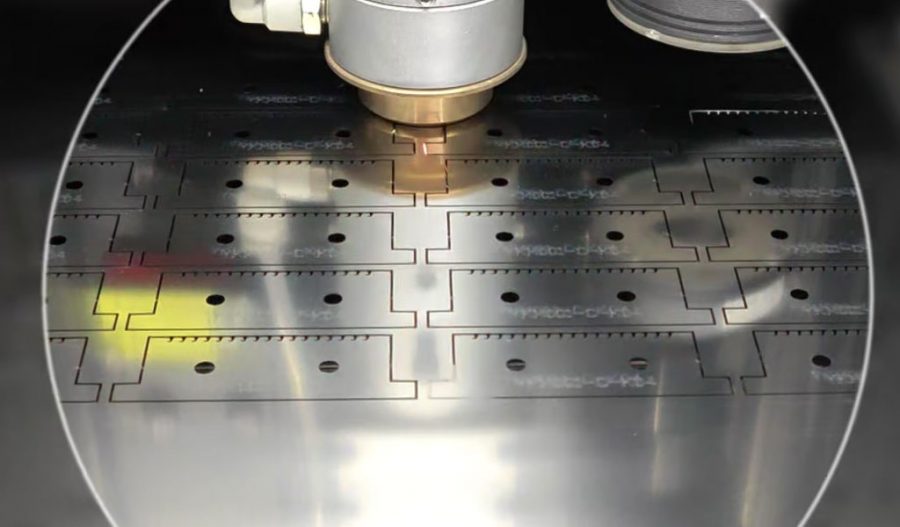
Laser-assisted metal spinning (LAMS) represents a transformative advancement in the field of materials processing, particularly for the forming of challenging materials such as titanium, nickel-based alloys, and strain-hardening stainless steels. Metal spinning, a traditional manufacturing technique, involves the incremental deformation of a rotating metal blank over a mandrel to produce axisymmetric components. While effective for ductile materials, conventional metal spinning struggles with high-strength, low-formability materials due to their resistance to deformation, high forming forces, and propensity for cracking. The integration of laser technology into metal spinning addresses these limitations by selectively heating the forming zone, thereby enhancing material formability, reducing forming forces, and improving product quality. This article provides a comprehensive exploration of laser-assisted metal spinning, including its principles, technological developments, applications, advantages, limitations, and future directions. Detailed comparisons with conventional metal spinning and other forming techniques are presented to elucidate the benefits of LAMS in modern manufacturing.
Historical Context
Metal spinning has been practiced for centuries, with origins traced to ancient civilizations where artisans shaped metals into vessels and decorative items. The industrial revolution formalized metal spinning as a manufacturing process, enabling the production of components such as cookware, lighting fixtures, and aerospace parts. However, the process remained limited to materials with high ductility, such as aluminum and mild steel. The advent of high-performance materials in the 20th century, driven by demands in aerospace, automotive, and energy sectors, exposed the shortcomings of conventional spinning. Materials like titanium and Inconel, prized for their strength and corrosion resistance, required excessive forming forces and often necessitated intermediate heat treatments, increasing production time and costs.
The concept of thermally assisted forming emerged in the late 20th century as a solution to these challenges. Early experiments with flame heating and induction heating demonstrated improved formability but lacked precision and control. The development of laser technology in the 1960s, following Theodore Maiman’s invention of the ruby laser, opened new possibilities for localized heating. By the early 2000s, researchers began integrating lasers into metal spinning machines, leveraging their high energy density and precise control to heat specific regions of the workpiece. This marked the birth of laser-assisted metal spinning, a process that combines the mechanical deformation of spinning with the thermal softening induced by laser irradiation.
Principles of Laser-Assisted Metal Spinning
Fundamentals of Metal Spinning
Metal spinning is a chipless forming process that shapes a flat metal blank or preform into a rotationally symmetric part by applying localized pressure via a roller or tool. The blank is clamped against a rotating mandrel, and the tool incrementally deforms the material, causing it to conform to the mandrel’s shape. Spinning can be categorized into conventional spinning, shear spinning, and flow forming, each differing in the degree of thickness reduction and deformation mechanics. Conventional spinning maintains the blank’s thickness, shear spinning reduces thickness while maintaining diameter, and flow forming significantly reduces thickness to produce thin-walled, high-strength components.
The process is governed by material properties such as ductility, yield strength, and strain-hardening behavior. For challenging materials, high yield strength and low ductility result in large forming forces, tool wear, and potential defects like cracking or wrinkling. Additionally, springback—the elastic recovery of the material after deformation—complicates dimensional accuracy.
Role of Laser Heating
Laser-assisted metal spinning introduces a localized heat source to the forming zone, typically using a high-power laser such as a CO2, Nd:YAG, or fiber laser. The laser beam is directed at the region where the spinning tool contacts the workpiece, raising the material’s temperature to reduce its yield strength and enhance ductility. The key advantage of laser heating is its precision, allowing for controlled temperature gradients that minimize thermal distortion and preserve the material’s microstructure outside the forming zone.
The interaction between the laser and the metal involves absorption, reflection, and conduction of thermal energy. The absorptivity of the material, which depends on its surface condition and the laser’s wavelength, determines the efficiency of energy transfer. For instance, titanium absorbs infrared laser light more effectively than polished stainless steel, necessitating adjustments in laser power and beam focus. The heated region experiences a reduction in flow stress, enabling deformation at lower forces and reducing the risk of defects.
Process Mechanics
The mechanics of LAMS combine thermal and mechanical effects. The laser induces a temperature field that softens the material, while the spinning tool applies mechanical force to deform it. The temperature field is critical, as excessive heating can lead to melting or microstructural damage, while insufficient heating may not adequately reduce flow stress. Finite element modeling (FEM) and infrared (IR) imaging are commonly used to optimize the temperature distribution and ensure uniform heating of the forming zone.
The deformation process in LAMS can be described by the following stages:
- Initial Heating: The laser heats the forming zone to a target temperature, typically 300–800°C for titanium or 600–1000°C for nickel-based alloys, depending on the material’s thermal properties.
- Deformation: The spinning tool applies force, causing plastic deformation. The reduced yield strength allows for greater strain without cracking.
- Cooling: As the tool moves to a new region, the heated zone cools rapidly due to conduction and convection, minimizing thermal effects on adjacent areas.
- Iteration: The process repeats incrementally, with the laser and tool advancing along the workpiece to complete the forming operation.
This iterative process enhances formability, reduces forming forces by up to 50%, and improves surface quality by minimizing springback and tool-material friction.
Technological Developments
Laser Integration into Spinning Machines
The integration of lasers into spinning machines required significant engineering advancements. Early prototypes used stationary laser sources with mirrors to direct the beam, but modern systems employ dynamic laser heads mounted on robotic arms or CNC-controlled gantries. These systems allow for precise positioning of the laser beam relative to the spinning tool, enabling complex forming paths and multi-pass spinning strategies.
A notable development is the use of fiber lasers, which offer high beam quality, efficiency, and flexibility compared to traditional CO2 lasers. Fiber lasers can be coupled with optical fibers, simplifying beam delivery and allowing for integration into compact spinning setups. Additionally, advancements in beam shaping and power modulation enable tailored heating profiles, such as Gaussian or top-hat distributions, to optimize thermal effects for specific materials.
Process Monitoring and Control
Real-time monitoring is critical for ensuring process stability and product quality in LAMS. Infrared cameras and pyrometers measure the temperature of the forming zone, providing feedback to adjust laser power and prevent overheating. Force-torque sensors monitor the mechanical loads on the spinning tool, allowing for adaptive control of tool feed rates and pressure. These sensors are often integrated into closed-loop control systems that maintain optimal forming conditions.
Advanced techniques such as electron backscatter diffraction (EBSD) and residual stress measurement are used post-process to characterize the formed parts. EBSD provides insights into microstructural changes, such as grain refinement or recrystallization, while residual stress analysis evaluates the impact of thermal gradients on part integrity. These tools have confirmed that LAMS reduces residual stresses compared to conventional spinning, contributing to improved fatigue performance.
Material-Specific Processing Strategies
LAMS has been tailored to specific materials through experimental and computational studies. For titanium grade 2, laser heating to 400–600°C significantly enhances formability by reducing flow stress and increasing elongation-to-fracture. For Inconel 718, a nickel-based superalloy, temperatures of 800–1000°C are required to overcome its high strength and strain-hardening behavior. Austenitic stainless steel (e.g., X5CrNi18-10) benefits from laser heating at 600–800°C, which minimizes work hardening and improves surface finish.
Process parameters, such as laser power, beam diameter, tool feed rate, and spindle speed, are optimized for each material. For example, titanium requires lower laser power (1–2 kW) and slower feed rates to avoid excessive heating, while Inconel may require higher power (3–5 kW) and faster feeds to maintain productivity. These parameters are often determined through design of experiments (DOE) and validated using FEM simulations.
Applications
Aerospace Industry
The aerospace industry is a primary beneficiary of LAMS due to its reliance on high-performance materials like titanium and nickel-based alloys. Components such as turbine disks, engine casings, and structural panels require precise forming and high strength-to-weight ratios. LAMS enables the production of these parts with reduced forming forces, improved dimensional accuracy, and enhanced surface quality. For instance, laser-assisted shear spinning of Inconel 718 has been used to produce thin-walled turbine components with minimal defects and lower residual stresses.
Automotive Industry
In the automotive sector, LAMS is applied to produce lightweight components from high-strength steels and titanium alloys. Parts such as exhaust manifolds, wheel rims, and suspension components benefit from the process’s ability to handle complex geometries and reduce manufacturing costs. The elimination of intermediate heat treatments in LAMS streamlines production, making it attractive for high-volume manufacturing.
Energy Sector
The energy sector uses LAMS to fabricate components for gas turbines, nuclear reactors, and renewable energy systems. Nickel-based alloys and titanium are common in these applications due to their corrosion resistance and high-temperature performance. LAMS allows for the efficient forming of large-diameter parts, such as reactor vessels and turbine blades, with improved mechanical properties and reduced production times.
Medical Devices
In the medical field, LAMS is used to produce implants and surgical instruments from biocompatible materials like titanium. The process’s precision and ability to minimize residual stresses ensure that components meet stringent regulatory requirements. For example, laser-assisted spinning of titanium has been used to create seamless, thin-walled implants with excellent fatigue resistance.
Advantages of Laser-Assisted Metal Spinning
LAMS offers several advantages over conventional metal spinning and other forming techniques:
- Enhanced Formability: Localized heating reduces yield strength and increases ductility, enabling the forming of challenging materials without cracking.
- Reduced Forming Forces: Laser-induced softening decreases the mechanical loads on the spinning tool, extending tool life and reducing energy consumption.
- Improved Product Quality: Minimized springback and residual stresses result in higher dimensional accuracy and better surface finish.
- Process Efficiency: Elimination of intermediate heat treatments reduces throughput times and manufacturing costs.
- Flexibility: The ability to adjust laser parameters and tool paths allows for the processing of diverse materials and geometries.
- Automation Potential: Integration with CNC systems and real-time monitoring enables automated, high-precision production.
These advantages translate to significant economic benefits, including a reported 15–25% increase in turnover and a 25% increase in order capacity for small and medium enterprises (SMEs) adopting LAMS.
Limitations and Challenges
Despite its benefits, LAMS faces several challenges:
- Equipment Costs: The integration of high-power lasers and advanced control systems increases initial investment costs, which may deter small manufacturers.
- Thermal Management: Precise control of the temperature field is critical to avoid overheating, which can cause microstructural damage or melting.
- Material Variability: Variations in material properties, such as absorptivity and thermal conductivity, require tailored process parameters, complicating standardization.
- Process Complexity: The combination of thermal and mechanical effects necessitates sophisticated modeling and monitoring to ensure consistent results.
- Scalability: While effective for small to medium batches, scaling LAMS for mass production requires further optimization of cycle times and energy efficiency.
Ongoing research aims to address these challenges through improved laser technologies, advanced process modeling, and cost-effective equipment designs.
Comparison with Other Forming Techniques
To highlight the advantages of LAMS, the following tables compare it with conventional metal spinning, hot forging, and superplastic forming for processing challenging materials.
Table 1: Comparison of Forming Techniques for Titanium Grade 2
Parameter | Laser-Assisted Metal Spinning | Conventional Metal Spinning | Hot Forging | Superplastic Forming |
---|---|---|---|---|
Formability | High (laser softens material) | Low (limited by ductility) | Moderate | Very high |
Forming Forces | Low (50% reduction) | High | High | Low |
Tool Wear | Low (reduced forces) | High | Moderate | Low |
Dimensional Accuracy | High (minimal springback) | Moderate (significant springback) | Moderate | High |
Surface Finish | Excellent (smooth surfaces) | Good | Poor | Excellent |
Cycle Time | Moderate (incremental process) | Moderate | Fast | Slow |
Equipment Cost | High (laser integration) | Low | Moderate | High |
Material Utilization | High (near-net-shape) | High | Moderate | High |
Applications | Aerospace, medical, energy | General components | Structural parts | Aerospace, niche parts |
Table 2: Comparison of Forming Techniques for Inconel 718
Parameter | Laser-Assisted Metal Spinning | Conventional Metal Spinning | Hot Forging | Superplastic Forming |
---|---|---|---|---|
Formability | High (laser enhances ductility) | Very low (high strength) | Moderate | High |
Forming Forces | Low (30–50% reduction) | Very high | High | Low |
Tool Wear | Low (softened material) | Very high | High | Low |
Dimensional Accuracy | High (reduced springback) | Poor (significant springback) | Moderate | High |
Surface Finish | Excellent (minimal defects) | Poor | Poor | Excellent |
Cycle Time | Moderate (multi-pass) | Slow (multiple steps) | Fast | Very slow |
Equipment Cost | High (laser and CNC) | Low | Moderate | Very high |
Material Utilization | High (near-net-shape) | High | Low | High |
Applications | Turbine components, aerospace | Limited | Engine parts | Aerospace, specialized |
Analysis of Comparisons
The tables demonstrate that LAMS excels in formability, dimensional accuracy, and surface finish for challenging materials. Compared to conventional spinning, LAMS significantly reduces forming forces and springback, making it viable for titanium and Inconel. Hot forging, while faster, produces poorer surface quality and requires additional finishing. Superplastic forming offers excellent formability but is slow and costly, limiting its use to niche applications. LAMS strikes a balance between flexibility, quality, and efficiency, making it a versatile choice for advanced manufacturing.
Microstructural Effects
Titanium Grade 2
In LAMS of titanium grade 2, laser heating to 400–600°C induces dynamic recrystallization in the forming zone, resulting in refined grain structures. EBSD analysis reveals a reduction in grain size from 20–30 µm in the as-received material to 5–10 µm in the formed part, enhancing strength and ductility. The process also minimizes the formation of alpha-case (a brittle oxygen-enriched layer), which is a common issue in conventional hot forming.
Inconel 718
For Inconel 718, laser heating to 800–1000°C promotes partial recrystallization and dissolution of strengthening phases like gamma-prime (γ′). This reduces work hardening and allows for greater deformation without cracking. Post-process analysis shows a uniform microstructure with minimal voids and improved fatigue resistance, critical for aerospace applications.
Austenitic Stainless Steel
In austenitic stainless steel (X5CrNi18-10), laser heating at 600–800°C suppresses martensitic transformation, which occurs in cold forming and reduces ductility. The resulting microstructure exhibits fine, equiaxed grains and low residual stresses, contributing to excellent corrosion resistance and surface quality.
Economic and Socio-Economic Impacts
The adoption of LAMS has significant economic implications, particularly for SMEs in the metal spinning industry. By enabling the processing of high-value materials, LAMS allows manufacturers to enter new markets, such as aerospace and medical devices, where demand for titanium and nickel-based alloys is growing. Reported benefits include a 15–25% reduction in manufacturing costs due to fewer processing steps and a 25% increase in order capacity, as SMEs can accept contracts previously rejected due to material limitations.
Socio-economically, LAMS enhances the competitiveness of European manufacturers against low-cost competitors in Asia and other regions. The technology creates higher-skilled jobs, as operators require training in laser systems and CNC programming. Additionally, the availability of laser sources in spinning facilities opens opportunities for other laser-based processes, such as cutting and welding, further diversifying SME portfolios.
Future Directions
The future of LAMS lies in addressing current limitations and expanding its applications. Key research areas include:
- Cost Reduction: Developing lower-cost laser systems and modular spinning machines to make LAMS accessible to smaller manufacturers.
- Process Optimization: Advancing FEM and machine learning models to predict optimal process parameters for new materials and geometries.
- Hybrid Processes: Combining LAMS with other techniques, such as laser cladding or additive manufacturing, to produce multifunctional components.
- Sustainability: Improving energy efficiency and exploring green laser technologies to reduce the environmental impact of LAMS.
- Scalability: Optimizing cycle times and automation to enable high-volume production for automotive and consumer goods.
Collaborative projects, such as the European EASYFORM initiative, are driving these advancements by fostering partnerships between academia, industry, and SMEs. The integration of machine learning for real-time process control and the development of new laser sources, such as ultrafast lasers, promise to further enhance the precision and efficiency of LAMS.
Conclusion
Laser-assisted metal spinning is a groundbreaking technology that overcomes the limitations of conventional metal spinning for processing challenging materials. By combining localized laser heating with mechanical deformation, LAMS enhances formability, reduces forming forces, and improves product quality, making it ideal for high-performance applications in aerospace, automotive, energy, and medical sectors. While challenges such as equipment costs and process complexity remain, ongoing research and technological advancements are poised to expand the reach of LAMS. With its economic and socio-economic benefits, LAMS represents a cornerstone of modern manufacturing, enabling the efficient and flexible production of advanced components.
Maximize Tooling and CNC Metal Spinning Capabilities.
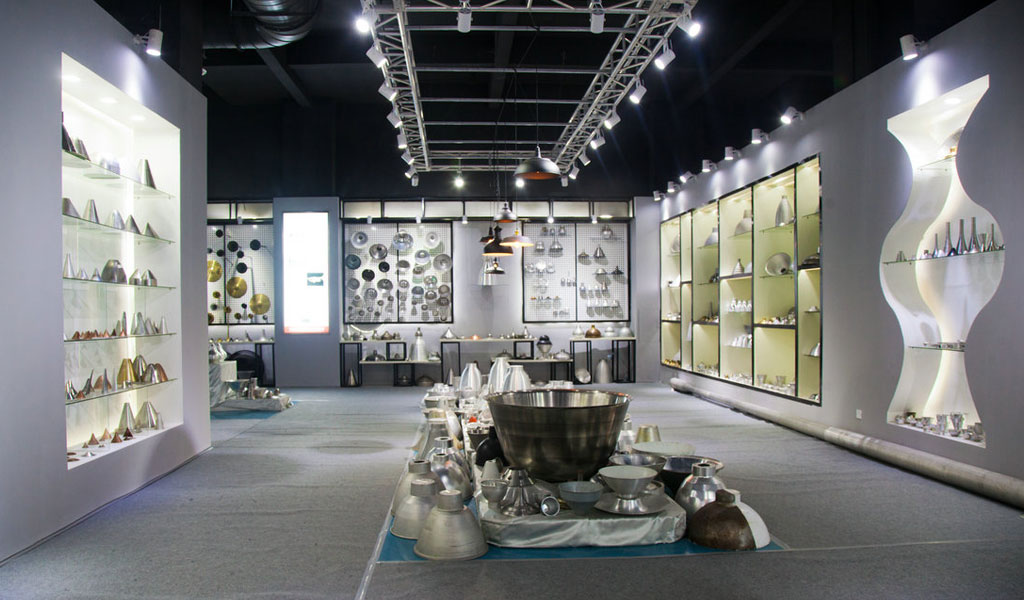
At BE-CU China Metal Spinning company, we make the most of our equipment while monitoring signs of excess wear and stress. In addition, we look into newer, modern equipment and invest in those that can support or increase our manufacturing capabilities. Our team is very mindful of our machines and tools, so we also routinely maintain them to ensure they don’t negatively impact your part’s quality and productivity.
Talk to us today about making a rapid prototype with our CNC metal spinning service. Get a direct quote by chatting with us here or request a free project review.
BE-CU China CNC Metal Spinning service include : CNC Metal Spinning,Metal Spinning Die,Laser Cutting, Tank Heads Spinning,Metal Hemispheres Spinning,Metal Cones Spinning,Metal Dish-Shaped Spinning,Metal Trumpet Spinning,Metal Venturi Spinning,Aluminum Spinning Products,Stainless Steel Spinning Products,Copper Spinning Products,Brass Spinning Products,Steel Spinning Product,Metal Spinnin LED Reflector,Metal Spinning Pressure Vessel,