Laser Cutting
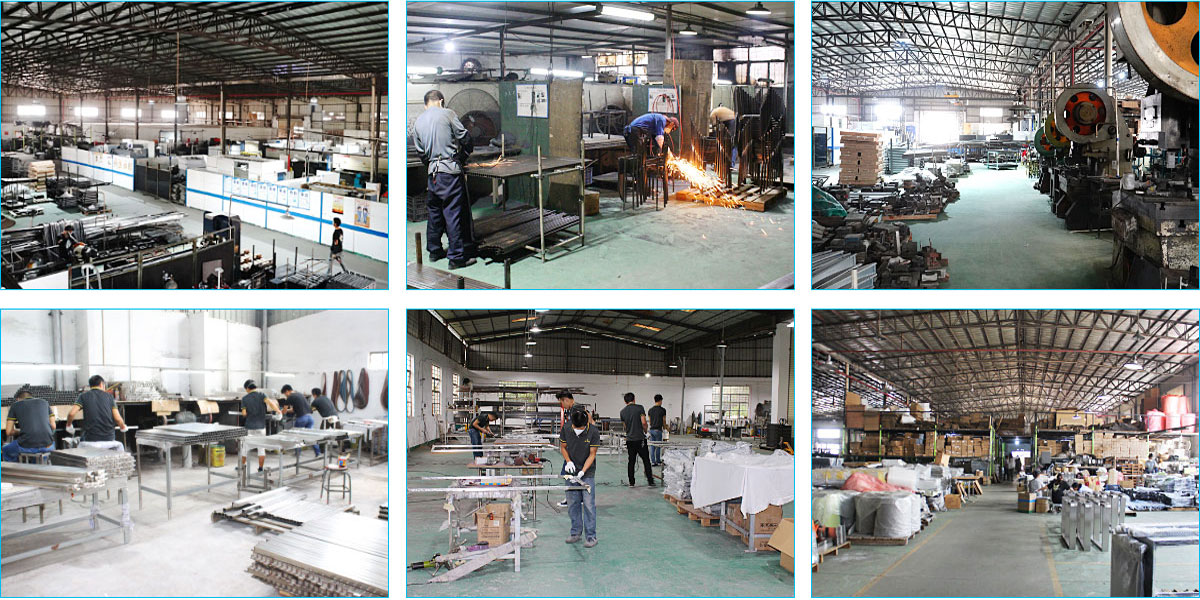
Are you looking for an expert manufacturer of laser cutting products? Whether you want mass quantities of everyday laser cutting items or custom laser cutting prototypes, sheet metal laser cutting in China is the most effective manufacturing method for you. At BE-CU, our China sheet metal laser cutting and professional 3d laser cutting makers can create your ideal sheet metal product all at an affordable price. Whether it’s food containers, signs, frame, toys, utensils, kitchen items, gadgets, or devices that you need.
Over the decades, sheet metal has become a popular material choice for manufacturing all kinds of goods because it can be laser cutting into any shape. Whether you’re from the United States or Europe, finding a reputable laser cutting in China to be your supplier can offer you a range of benefits. From low costs, low scrap rates, great customer service, and more. Read on to learn more about why you should trust BE-CU as your laser cutting company & manufacturer in China.
Why BE-CU Is the Laser Cutting Company You Need.
Most everybody knows that Laser Cutting from China are cheap, but there are also plenty of horror stories in the industry. If Laser Cutting process in China goes wrong, it tends to go wrong in quite a big way; it can break a company.
We have many years of experience in the Laser Cutting service business and know very well all customers’ concerns.
- Protection of intellectual property
- We are a company that can provide original factory price
- Laser Cutting parts that adhere to original product design
- Redesign solutions that can provide lower pricing
- High level of service and quality 3D laser cutting
At BE-CU we offer you the best of both worlds: our China Laser Cutting and Sheet metal parts have a competitive price, while our team of china engineers assures full conformity to top of the line quality standards and on-time delivery of parts.
Over 20 years we’ve carefully selected, tested, and work countless times with specific metal material makers; we’ve reached a level where we can confidently and consistently follow a laser cutting process that works.
You’d be surprised at the number of companies out there that get a project done like this; some sales managers will take a western company’s money and then just forward emails to a custom sheet metal manufacturer in China; they’ll outline some sheet metal characteristics to be produced and have a factory produce something.
Needless to say that laser cutting parts produced this way won’t meet the levels of quality you’re expecting.
A lot of money goes into engineering strength and manufacturing; the whole process requires a lot of attention to ensure project manufacturers get the project right; when it comes to laser cutting there’s no place for companies to make a mistake.
Many companies never make it to the market, not because of supplier issues or market downturns; they simply go out of business because they were never able to get their sheet metal parts right and ran out of money before they could produce a good quality products.
China Laser Cutting Forming: Low Cost Sheet Metal Laser Cutting
We offer:
- In-depth evaluation of your Sheet Metal parts designs so you can avoid production problems such as product returns due to poor quality.
- Redesign of your parts to assure the manufacturer optimal Design For Manufacturing and Assembly
- On-the-ground bilingual Sheet Metal project managers to assure clear communication.
- Weekly progress reports on your Sheet Metal laser cutting project process.
Performance of 3D Fiber Laser Cutting Service
The 3D fiber laser cutting machine is an advanced laser cutting device capable of flexible cutting at multiple angles and positions on metal sheets of varying thicknesses. It consists of a dedicated fiber laser cutting head, high-precision capacitive tracking system, fiber laser generator, and industrial robot system.
Utilizing the flexible and rapid motion capabilities of industrial robots, the machine adapts its actions according to the size of the workpiece specified by the user. By adjusting the orientation of the robot, either upright or inverted, and employing teach pendant programming or offline programming for different products and trajectories, the machine achieves three-dimensional cutting of irregular workpieces using the fiber laser cutting head. Fiber optics transmit the laser to the cutting head (equipped with fiber follow-up devices and optical path transmission devices), and then the focusing system focuses the laser, enabling multi-angle cutting of various three-dimensional metal sheets.
The power of the selected fiber laser varies according to the thickness of the metal sheet, with options typically ranging from 500W to 1000W for 3D cutting. Different cooling systems are equipped for lasers of different powers to ensure their normal operation. Additionally, the appropriate length of optical fiber transmission for laser cutting must be selected based on the working radius of the robotic arm and the size of the customer’s workpiece to meet cutting requirements.
The auxiliary gas used in 3D fiber laser cutting machines is typically 99.99% oxygen, greatly aiding in cutting precision, speed, and the quality of the cut section.
These machines find applications in industries such as automotive manufacturing, automotive parts production, and engineering machinery processing.
How Laser Cutting Revolutionizes Metal Spinning
Metal spinning, a centuries-old technique, involves shaping metal sheets or tubes into various forms through rotational motion. Historically reliant on manual labor and traditional tools, the process has evolved significantly with the advent of modern technologies. Among these advancements, laser cutting stands out as a transformative force, enabling enhanced precision, efficiency, and versatility in metal spinning.
Laser cutting, a non-contact process utilizing a focused beam of light, has found extensive applications across diverse industries, from automotive to aerospace, owing to its ability to precisely cut through various materials, including metals, with unparalleled accuracy. When integrated into metal spinning processes, laser cutting brings forth a myriad of benefits, revolutionizing the way metal components are crafted.
- 1. Precise Material Preparation: Before metal spinning commences, precise material preparation is paramount to ensuring high-quality end products. Laser cutting excels in this aspect by offering unmatched precision in trimming metal sheets or tubes to desired shapes and dimensions. Whether it’s intricate designs or complex geometries, laser cutting ensures uniformity and consistency, laying the foundation for flawless metal spinning operations.
- 2. Intricate Pattern Creation: One of the most remarkable capabilities of laser cutting lies in its ability to create intricate patterns and designs on metal surfaces with utmost precision. In metal spinning, this translates to the incorporation of intricate details, be it decorative motifs or functional features, into spun components. From perforations to etchings, laser-cut patterns add both aesthetic appeal and functional value to the final products, elevating their overall quality and marketability.
- 3. Enhanced Efficiency and Cost-Effectiveness: By automating cutting processes and minimizing material wastage, laser cutting enhances the efficiency of metal spinning operations while reducing production costs. The speed and accuracy of laser cutting translate to shorter lead times and increased throughput, enabling manufacturers to meet demanding production schedules and deliver superior-quality components cost-effectively.
- 4. Complex Shape Fabrication: Laser cutting facilitates the fabrication of components with complex shapes and contours, pushing the boundaries of what’s achievable through traditional metal spinning techniques. By precisely cutting out intricate shapes and profiles from metal sheets or tubes, laser technology empowers metal spinners to create components with enhanced functionality and structural integrity, opening doors to innovative design possibilities.
- 5. Seamless Integration with CAD/CAM Systems: The seamless integration of laser cutting with computer-aided design (CAD) and computer-aided manufacturing (CAM) systems further enhances the capabilities of metal spinning processes. Design iterations can be quickly translated into precise cutting instructions, allowing for rapid prototyping and customization. This synergy between laser cutting and digital design tools not only accelerates the product development cycle but also ensures seamless scalability from prototype to mass production.
- 6. Minimal Material Distortion and Heat-Affected Zone: Unlike traditional cutting methods that often introduce heat and mechanical stress, laser cutting produces minimal material distortion and a narrow heat-affected zone. This characteristic is particularly advantageous in metal spinning, where maintaining material integrity is critical to achieving dimensional accuracy and surface finish. By minimizing distortion and heat-induced deformations, laser cutting preserves the structural integrity of spun components, ensuring consistent quality throughout the production process.
China Laser Cutting Parts Gallery
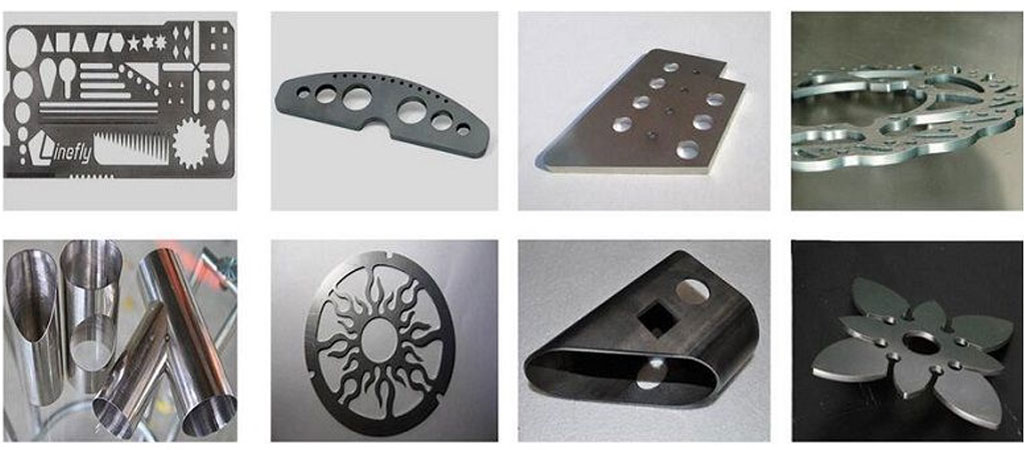
In conclusion, the integration of laser cutting technology into metal spinning processes represents a paradigm shift in the manufacturing landscape. By offering unparalleled precision, efficiency, and versatility, laser cutting unlocks new possibilities for creating intricate, high-quality metal components across a wide range of industries. As manufacturers continue to embrace advancements in laser technology, the future of metal spinning shines brighter than ever before, with limitless potential for innovation and excellence.