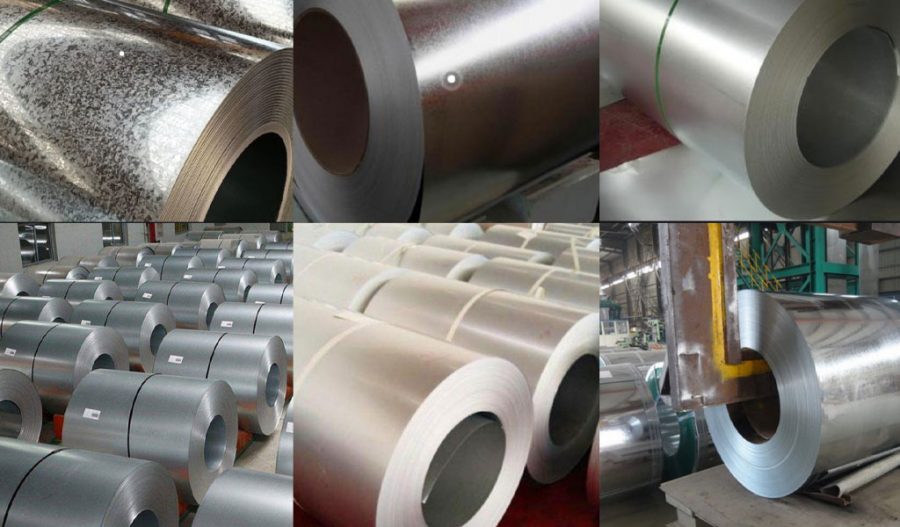
Metal spinning blanks are fundamental components in the metalworking process known as metal spinning, a technique used to form axially symmetric, hollow metal parts by rotating a flat or preformed metal disc or tube at high speed and applying localized force to shape it over a mandrel. These blanks serve as the starting material, typically consisting of sheet metal or tubular stock, and their properties—such as material composition, thickness, diameter, and surface condition—directly influence the feasibility, quality, and efficiency of the spinning process. Metal spinning, also referred to as spin forming or metal turning, is a versatile manufacturing method with applications ranging from artisanal crafts to high-precision industrial components, including aerospace nose cones, cookware, and musical instrument bells. This article explores the nature of metal spinning blanks, their material characteristics, preparation methods, role in various spinning techniques, and comparative analyses with other forming processes.
Definition and Role of Metal Spinning Blanks
In metal spinning, a blank is the initial workpiece that undergoes deformation to achieve the desired geometry. Unlike subtractive processes such as machining, which remove material, metal spinning is a forming process that reshapes the blank without significant material loss. The blank is typically a flat, circular disc cut from sheet metal, though it can also be a preformed shape (e.g., a deep-drawn cup or machined tube) depending on the complexity of the final part. The blank is clamped against a mandrel—a rotating tool that defines the inner contour of the finished piece—and deformed using rollers or hand tools that apply pressure incrementally or continuously.
The primary role of the blank is to provide a malleable, uniform starting material capable of withstanding the tensile and compressive stresses induced during spinning. The blank’s dimensions and properties dictate the limits of deformation, influencing factors such as wall thickness variation, springback, and the risk of defects like wrinkling or fracture. For conventional spinning, the blank’s thickness remains relatively constant, while in shear spinning or flow forming, it may be intentionally reduced to achieve specific mechanical properties or geometries.
Materials Used for Metal Spinning Blanks
The choice of material for a metal spinning blank is critical, as it must exhibit sufficient ductility and tensile elongation to deform plastically without failing. Virtually any ductile metal can be used, though the selection depends on the application, cost, and processing requirements. Common materials include:
- Aluminum: Widely used due to its excellent formability, lightweight nature, and corrosion resistance. Grades such as 1100 (commercially pure) and 6061 (heat-treatable alloy) are popular for spinning blanks in applications like cookware and aerospace components.
- Stainless Steel: Valued for its strength, durability, and resistance to corrosion, stainless steel (e.g., 304, 316) is spun into parts like dairy utensils and medical equipment. Its higher strength requires more robust equipment and careful control to avoid work hardening.
- Copper: Known for its malleability and conductivity, copper is a traditional choice for decorative items and electrical components. It spins easily but may require annealing to restore ductility during multi-pass processes.
- Brass: A copper-zinc alloy, brass (e.g., 70-30 composition) offers a balance of formability and aesthetic appeal, making it suitable for musical instruments and ornamental objects.
- Mild Steel: Inexpensive and moderately ductile, mild steel is used for industrial parts like gas cylinders. Thicknesses up to 9 mm can be spun, though cold working may necessitate annealing.
- High-Strength Alloys: Materials like titanium, Inconel, and Hastelloy are employed in aerospace and high-temperature applications. These require specialized equipment due to their strength and lower ductility.
The table below summarizes key properties of these materials relevant to spinning blanks:
Material | Density (g/cm³) | Yield Strength (MPa) | Tensile Strength (MPa) | Elongation (%) | Typical Thickness Range (mm) | Applications |
---|---|---|---|---|---|---|
Aluminum (1100) | 2.71 | 34 | 90 | 35–45 | 0.5–6 | Cookware, lighting reflectors |
Stainless Steel (304) | 8.00 | 215 | 505 | 40–60 | 0.5–3 | Dairy utensils, medical devices |
Copper | 8.96 | 70 | 220 | 40–50 | 0.5–4 | Decorative items, conductors |
Brass (70-30) | 8.53 | 120 | 350 | 35–50 | 0.5–4 | Musical bells, trophies |
Mild Steel | 7.85 | 250 | 400 | 20–30 | 1–9 | Gas cylinders, structural parts |
Titanium (Grade 2) | 4.51 | 275 | 345 | 20–25 | 0.5–3 | Aerospace components |
Preparation of Metal Spinning Blanks
The preparation of blanks is a crucial step that affects the spinning process’s success. Blanks are typically sourced from sheet metal stock, cut into circular discs using methods such as shearing, laser cutting, or waterjet cutting. The choice of cutting method influences edge quality, which can impact the blank’s behavior during spinning—e.g., rough edges may promote cracking. Key preparation considerations include:
- Diameter: The blank’s initial diameter must exceed the mandrel’s maximum diameter to allow material flow. For conventional spinning, blank diameters typically range from 1.2 to 1.5 times the final part’s diameter, though larger ratios (up to 2.5) are possible with advanced techniques like deep spinning.
- Thickness: Uniform thickness is essential for consistent deformation. Standard thicknesses range from 0.5 mm for thin-walled parts to over 25 mm for heavy-duty components, depending on material and equipment capacity.
- Surface Condition: Blanks are often cleaned and lubricated to reduce friction between the blank, mandrel, and roller. Common lubricants include oils, waxes, or graphite-based compounds, selected based on material and temperature.
- Preforming: For complex shapes, blanks may be preformed via deep drawing or stamping to approximate the final geometry, reducing the number of spinning passes required.
Metal Spinning Processes Involving Blanks
Metal spinning encompasses several techniques, each with distinct effects on the blank:
- Conventional Spinning: The blank is deformed over the mandrel with multiple roller passes, maintaining near-constant thickness. The process relies on bending and stretching, with the blank’s diameter decreasing and depth increasing. This method is ideal for prototypes and low-volume production due to its flexibility and low tooling costs.
- Shear Spinning: The blank is thinned intentionally by applying downward force, following the sine law (t = t₀ sin α, where t is final thickness, t₀ is initial thickness, and α is the mandrel angle). This enhances mechanical properties like strength but requires precise control to avoid over-thinning or fracture.
- Flow Forming: A variant often starting with tubular blanks, flow forming uses multiple rollers to elongate and thin the material axially. It’s suited for cylindrical parts like rocket casings, where high strength and tight tolerances are critical.
- Necking/Reducing: The blank is spun without a mandrel (“on air”) to form reentrant geometries, such as bottle necks. This technique is less common but valuable for seamless, high-pressure vessels.
The table below compares these processes based on blank requirements and outcomes:
Process | Blank Type | Thickness Change | Diameter Change | Force Application | Typical Products |
---|---|---|---|---|---|
Conventional Spinning | Flat disc | Minimal | Decreases | Incremental (multi-pass) | Cookware, reflectors |
Shear Spinning | Flat disc | Reduced (sine law) | Constant | Continuous (single-pass) | Cones, missile nose cones |
Flow Forming | Tube or preform | Reduced | Constant or reduced | Axial (multi-roller) | Cylinders, wheel rims |
Necking/Reducing | Flat disc or tube | Variable | Reduced | Localized (no mandrel) | Gas bottles, pressure vessels |
Mechanical Behavior of Blanks During Spinning
The deformation of a metal spinning blank involves complex interactions of stress and strain. In conventional spinning, the blank experiences radial tension and circumferential compression as it conforms to the mandrel, leading to potential wrinkling if compressive stresses exceed the material’s buckling limit. Shear spinning introduces additional axial compression, thinning the blank and aligning its grain structure, which can enhance tensile strength but risks fracture if ductility is insufficient.
Key mechanical phenomena include:
- Springback: Elastic recovery after deformation, influenced by material modulus and thickness. Thicker blanks and high-strength alloys exhibit greater springback, necessitating over-forming or heat treatment.
- Work Hardening: Cold spinning increases hardness and strength but reduces ductility, often requiring intermediate annealing for multi-pass processes.
- Failure Modes: Wrinkling (due to excessive compression), cracking (due to tensile failure), and flange jamming (in deep spinning) are common defects, mitigated by optimizing roller paths and blank geometry.
Comparative Analysis with Other Forming Processes
Metal spinning blanks differ from those used in alternative forming methods like stamping, hydroforming, and deep drawing. The table below provides a detailed comparison:
Process | Blank Type | Material Removal | Tooling Cost | Production Volume | Thickness Control | Applications |
---|---|---|---|---|---|---|
Metal Spinning | Flat disc/tube | None | Low | Low to medium | Variable (process-dependent) | Aerospace, cookware |
Stamping | Flat sheet | Minimal (trimming) | High | High | Constant | Automotive panels |
Hydroforming | Flat sheet/tube | None | Medium | Medium to high | Constant | Exhaust systems, frames |
Deep Drawing | Flat sheet | None | Medium | Medium to high | Thinned (stretching) | Cans, containers |
Metal spinning offers advantages in flexibility and low tooling costs, making it ideal for prototypes and custom parts. However, it is slower and less suited for high-volume production compared to stamping or hydroforming, which benefit from automated, high-speed presses.
Scientific Insights and Research Directions
Recent studies have advanced the understanding of metal spinning blanks. Finite element analysis (FEA) models, such as those by Xia et al. (2014), simulate stress-strain distributions, revealing that uneven compressive strains at blank edges contribute to springback and shape deviation. Experimental work by Kang et al. (1999) on roller path profiles (e.g., concave, convex, linear) demonstrates their impact on wall thickness and tool forces, with concave paths causing greater thinning. Innovations like synchronous multipass spinning, proposed by Xiao et al. (2017), allow non-circular blanks (e.g., octagonal) to form asymmetric shapes, expanding the process’s versatility.
Future research may focus on:
- Microstructure evolution and residual stress during spinning, which remain underexplored.
- Automated toolpath design to optimize blank deformation and minimize defects.
- Spinning of advanced materials like magnesium alloys, driven by demand for lightweight, high-strength components.
Conclusion
Metal spinning blanks are the cornerstone of a process that blends ancient craftsmanship with modern engineering. Their material properties, preparation, and behavior under various spinning techniques determine the quality and functionality of the final product. Through careful selection and processing, blanks enable the production of seamless, robust components across diverse industries. As research and technology evolve, the role of blanks in metal spinning will continue to expand, offering new possibilities in manufacturing science.
Maximize Tooling and CNC Metal Spinning Capabilities.
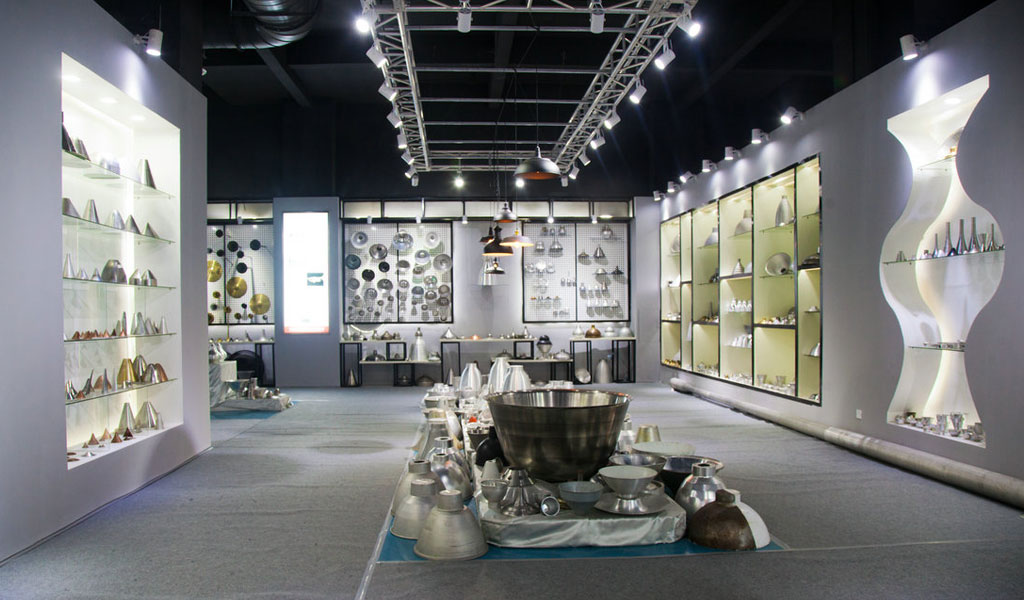
At BE-CU China Metal Spinning company, we make the most of our equipment while monitoring signs of excess wear and stress. In addition, we look into newer, modern equipment and invest in those that can support or increase our manufacturing capabilities. Our team is very mindful of our machines and tools, so we also routinely maintain them to ensure they don’t negatively impact your part’s quality and productivity.
Talk to us today about making a rapid prototype with our CNC metal spinning service. Get a direct quote by chatting with us here or request a free project review.
BE-CU China CNC Metal Spinning service include : CNC Metal Spinning,Metal Spinning Die,Laser Cutting, Tank Heads Spinning,Metal Hemispheres Spinning,Metal Cones Spinning,Metal Dish-Shaped Spinning,Metal Trumpet Spinning,Metal Venturi Spinning,Aluminum Spinning Products,Stainless Steel Spinning Products,Copper Spinning Products,Brass Spinning Products,Steel Spinning Product,Metal Spinnin LED Reflector,Metal Spinning Pressure Vessel,