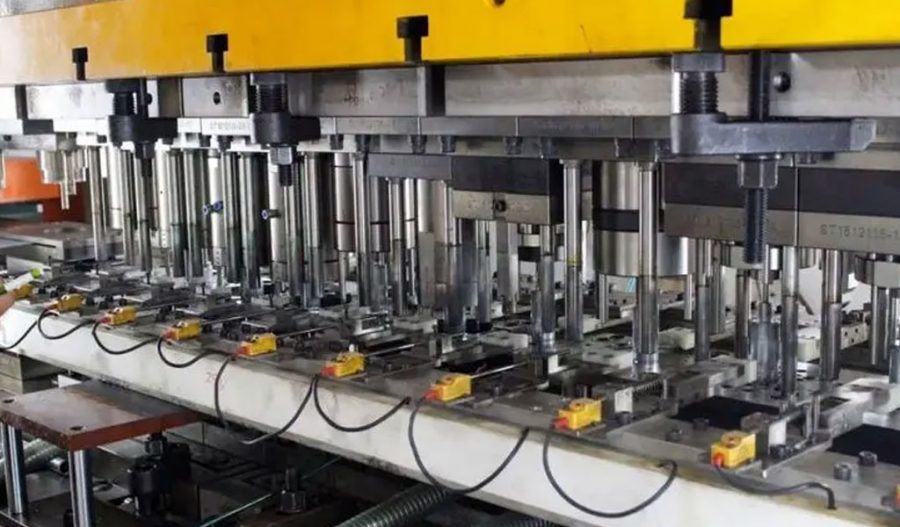
Metal forming processes are fundamental to manufacturing industries, offering various techniques to shape metals into desired forms. Among these, metal spinning and deep drawing are two widely utilized processes. Each method has distinct characteristics, advantages, and limitations, making them suitable for specific applications. This article delves into a comprehensive comparison of metal spinning and deep drawing, exploring their history, techniques, applications, advantages, and disadvantages.
A Comparison Chart Of Metal Spinning and Deep Drawing
Here is a detailed comparison table of Metal Spinning vs. Deep Drawing:
Aspect | Metal Spinning | Deep Drawing |
---|---|---|
History | Ancient origins, manual processes, industrial evolution | Developed in early 20th century for containers and automotive parts |
Basic Technique | Rotating a metal blank and forming it against a mandrel | Stretching a metal blank into a die cavity using a punch |
Equipment Used | Lathe, mandrel, rollers, CNC machines | Hydraulic/mechanical presses, punches, dies |
Typical Shapes | Symmetrical, axisymmetric shapes (e.g., bowls, cones) | Cylindrical, box-shaped, complex geometries |
Material Utilization | High material efficiency, minimal wastage | Good material utilization, but potential for material thinning |
Tooling Costs | Lower tooling costs, suitable for small runs and prototyping | Higher tooling costs, suited for high-volume production |
Production Volume | Cost-effective for small to medium production runs | Economical for high-volume production |
Part Strength | Seamless parts with uniform wall thickness | Enhanced strength due to work hardening |
Surface Finish | Smooth, seamless surfaces | Generally good, but may require finishing processes |
Material Flexibility | Limited by material thickness and hardness | Wide range of materials including aluminum, steel, and alloys |
Defect Risks | Limited to operator skill and material properties | Prone to wrinkling, tearing, and thinning, requiring control |
Manual Skill Requirement | High for manual spinning, skilled operators needed | Less manual skill required due to mechanized process |
Application Examples | Aerospace (nose cones), automotive (wheel rims), lighting | Packaging (beverage cans), automotive (fuel tanks), appliances |
Versatility | High for simple and complex symmetrical shapes | High for complex, deep geometries |
Cost Efficiency | Economical for small batches and prototypes | More cost-effective for large-scale production |
Process Speed | Generally slower, especially for manual spinning | Faster for high-volume production with automated systems |
Quality Consistency | Can vary with manual processes, high with CNC | High consistency with proper control |
Seamlessness | Produces seamless parts | May require welding or joining for some complex shapes |
Common Industries | Aerospace, automotive, consumer goods, industrial equipment | Packaging, automotive, electronics, household appliances |
History and Development
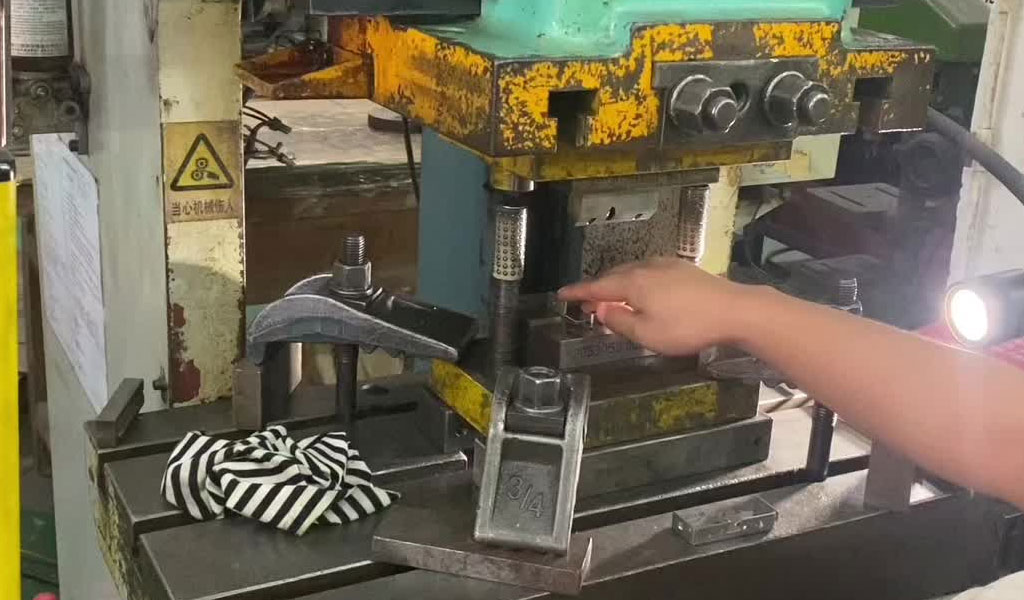
Metal Spinning
Metal spinning, also known as spin forming or spinning, dates back to ancient times. It has been used for centuries to create symmetrical objects such as bowls, pots, and other vessels. Historically, artisans performed metal spinning manually using a lathe and simple hand tools. The process involved rotating a metal blank at high speeds and forming it against a mandrel using a roller or other shaping tools.
With the advent of the Industrial Revolution and advances in technology, metal spinning evolved into a more sophisticated and mechanized process. The introduction of powered lathes and computer numerical control (CNC) machines revolutionized metal spinning, allowing for higher precision, consistency, and production efficiency. Today, metal spinning is used in various industries, including aerospace, automotive, and consumer goods, to produce components such as rocket nose cones, automotive wheel rims, and decorative lighting fixtures.
Deep Drawing
Deep drawing, on the other hand, has its origins in the early 20th century. The process was developed to meet the growing demand for metal containers and automotive parts. Deep drawing involves the use of a punch and die to transform a flat sheet of metal into a hollow, cylindrical or box-shaped component. The name “deep drawing” is derived from the ability to create parts with significant depth relative to their diameter.
Advancements in metallurgy and manufacturing technologies have significantly improved deep drawing processes. Modern deep drawing techniques utilize hydraulic and mechanical presses, precision tooling, and advanced lubricants to achieve high-quality, complex shapes with minimal material wastage. Deep drawing is widely used in industries such as packaging, automotive, electronics, and household appliances, producing items like beverage cans, fuel tanks, and kitchen sinks.
Techniques and Processes
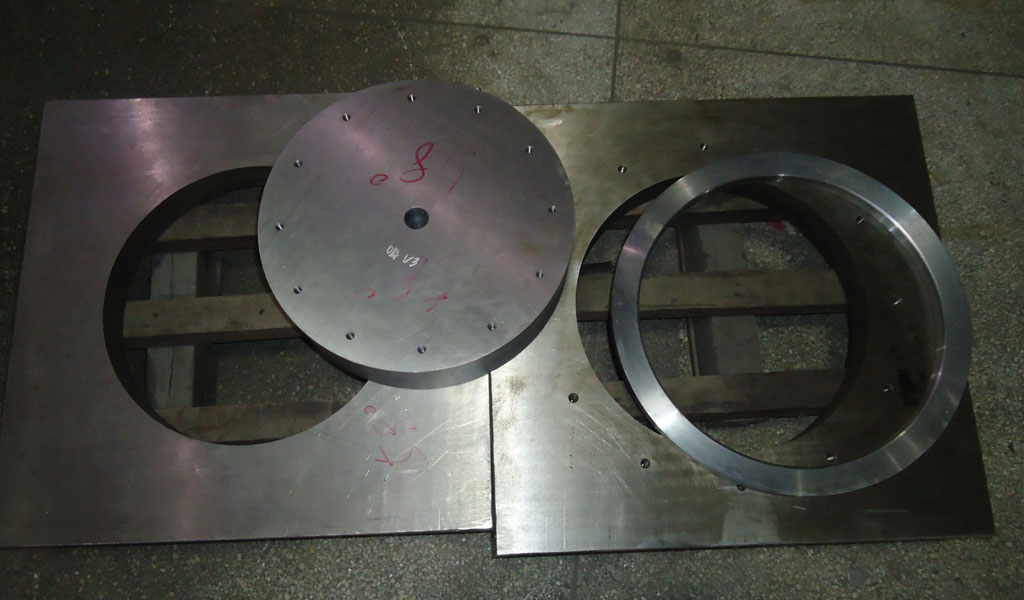
Metal Spinning
Metal spinning is a versatile and flexible process that can create both simple and complex shapes. The basic steps of metal spinning include:
- Blank Preparation: A flat metal disc, known as a blank, is cut from a sheet of metal. The blank’s size and thickness depend on the final component’s dimensions and material properties.
- Mounting: The blank is securely mounted on a lathe, which rotates the blank at high speeds.
- Forming: A mandrel, which serves as a template for the desired shape, is positioned against the blank. The blank is pressed and shaped against the mandrel using a roller or other forming tool. This step may involve multiple passes to achieve the final shape.
- Finishing: The formed part is trimmed, polished, and subjected to any additional finishing processes required to meet the desired specifications.
Metal spinning can be performed manually or using CNC machines. Manual spinning relies on the skill and expertise of the operator, while CNC spinning offers higher precision and repeatability, making it suitable for mass production.
Deep Drawing
Deep drawing is a sheet metal forming process that involves stretching the metal into a desired shape using a punch and die. The main steps in deep drawing include:
- Blank Preparation: A flat sheet of metal is cut into a blank of appropriate size and shape. The blank may be circular or rectangular, depending on the final component’s geometry.
- Blank Holding: The blank is placed on a die, and a blank holder applies pressure to hold the blank in place and prevent wrinkling during the drawing process.
- Drawing: A punch, which has the shape of the desired component, presses down on the blank, forcing it into the die cavity. The metal flows and stretches to conform to the punch and die shapes, creating a hollow part.
- Trimming and Finishing: After the drawing process, the part may require trimming to remove excess material and achieve the final dimensions. Additional finishing processes, such as annealing, surface treatment, or coating, may be applied to enhance the part’s properties.
Deep drawing requires precise control of the process parameters, including punch speed, blank holder force, and lubrication, to avoid defects such as tearing, wrinkling, or excessive thinning of the material.
Applications
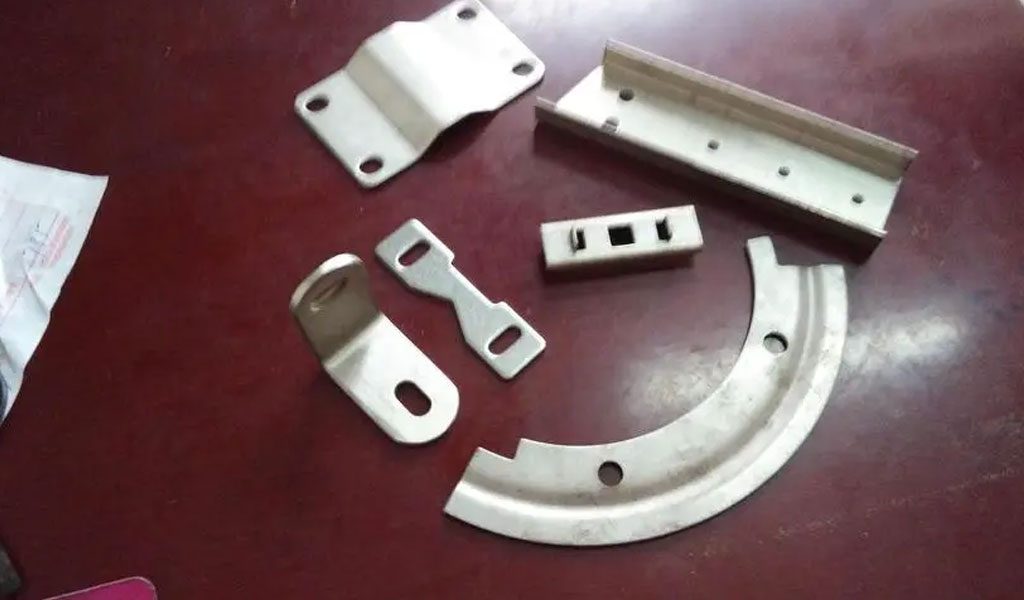
Metal Spinning
Metal spinning is commonly used to produce symmetrical, axisymmetric components with varying diameters and depths. Some typical applications include:
- Aerospace: Nose cones, rocket fairings, and other aerodynamic components.
- Automotive: Wheel rims, exhaust components, and air intake systems.
- Lighting: Reflectors, lamp shades, and decorative fixtures.
- Consumer Goods: Cookware, musical instruments, and decorative items.
- Industrial Equipment: Pressure vessels, filtration components, and ventilation systems.
The ability to create seamless, structurally sound parts with smooth surfaces makes metal spinning ideal for applications where aesthetics, strength, and aerodynamic properties are crucial.
Deep Drawing
Deep drawing is widely used to produce components with significant depth and intricate shapes. Common applications include:
- Packaging: Beverage cans, food containers, and aerosol cans.
- Automotive: Fuel tanks, oil pans, and transmission housings.
- Electronics: Battery housings, enclosures, and heat sinks.
- Household Appliances: Kitchen sinks, cookware, and washing machine tubs.
- Medical Devices: Surgical instruments, containers, and housings.
The ability to produce high-strength, lightweight components with complex geometries and consistent quality makes deep drawing suitable for high-volume production in various industries.
Advantages and Disadvantages
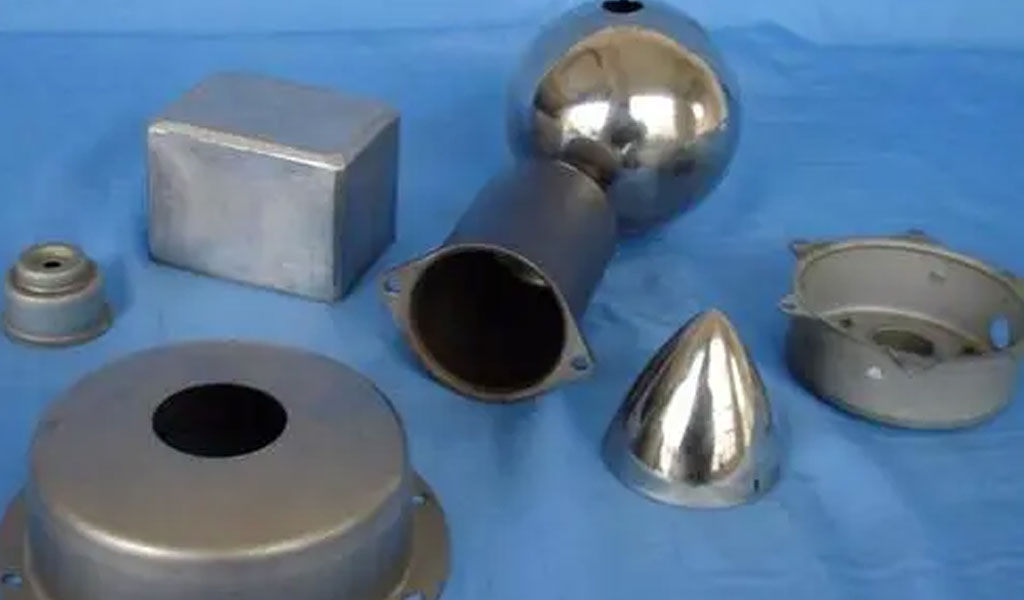
Metal Spinning
Advantages:
- Versatility: Metal spinning can produce a wide range of shapes and sizes, making it suitable for both small and large-scale production.
- Seamless Parts: The process creates seamless parts with uniform wall thickness, enhancing structural integrity and reducing the risk of leaks or failures.
- Cost-Effective for Small Runs: Metal spinning is economical for small production runs and prototyping, as it requires minimal tooling compared to other forming processes.
- Material Efficiency: The process minimizes material wastage, as the metal is deformed rather than removed.
Disadvantages:
- Limited to Symmetrical Shapes: Metal spinning is primarily suitable for axisymmetric shapes, limiting its application for complex, non-symmetrical geometries.
- Manual Skill Requirement: Manual spinning requires skilled operators, which can be a limitation in achieving consistent quality for complex parts.
- Limited Material Thickness: The process may not be suitable for very thick or hard materials, as excessive forces can lead to defects or equipment damage.
Deep Drawing
Advantages:
- Complex Geometries: Deep drawing can produce complex shapes with significant depth, making it ideal for components with intricate designs.
- High Volume Production: The process is well-suited for high-volume production, offering consistent quality and repeatability.
- Strength and Durability: Deep drawn parts exhibit high strength and durability due to work hardening during the drawing process.
- Material Versatility: The process can be used with a wide range of materials, including aluminum, steel, copper, and alloys.
Disadvantages:
- Tooling Costs: Deep drawing requires precision tooling, which can be expensive and time-consuming to design and manufacture.
- Defect Risks: The process is prone to defects such as wrinkling, tearing, and thinning, which require careful control of process parameters.
- Material Limitations: Some materials, especially those with low ductility, may not be suitable for deep drawing due to the risk of cracking or tearing.
Comparison and Selection Criteria
When choosing between metal spinning and deep drawing, several factors need to be considered to determine the most suitable process for a given application. These factors include:
- Geometry: Metal spinning is ideal for axisymmetric shapes, while deep drawing is suitable for complex, deep geometries.
- Production Volume: Metal spinning is cost-effective for small to medium production runs, whereas deep drawing is more economical for high-volume production.
- Material: Both processes can work with various materials, but deep drawing offers greater flexibility in material selection.
- Tooling Costs: Metal spinning typically has lower tooling costs, making it suitable for prototyping and small runs. Deep drawing involves higher tooling costs but offers economies of scale for large production volumes.
- Part Strength: Deep drawing enhances part strength due to work hardening, making it preferable for applications requiring high durability.
- Surface Finish: Metal spinning can achieve smooth, seamless surfaces, which may be desirable for aesthetic or aerodynamic applications.
Conclusion
Metal spinning and deep drawing are essential metal forming processes with distinct characteristics and applications. Metal spinning excels in producing symmetrical, seamless parts with versatility and material efficiency, while deep drawing offers the capability to create complex, deep geometries with high strength and volume production efficiency. The choice between these processes depends on the specific requirements of the application, including geometry, production volume, material, and cost considerations. Understanding the strengths and limitations of each process is crucial for selecting the most suitable method to achieve optimal results in metal forming.
Maximize Tooling and CNC Metal Spinning Capabilities.
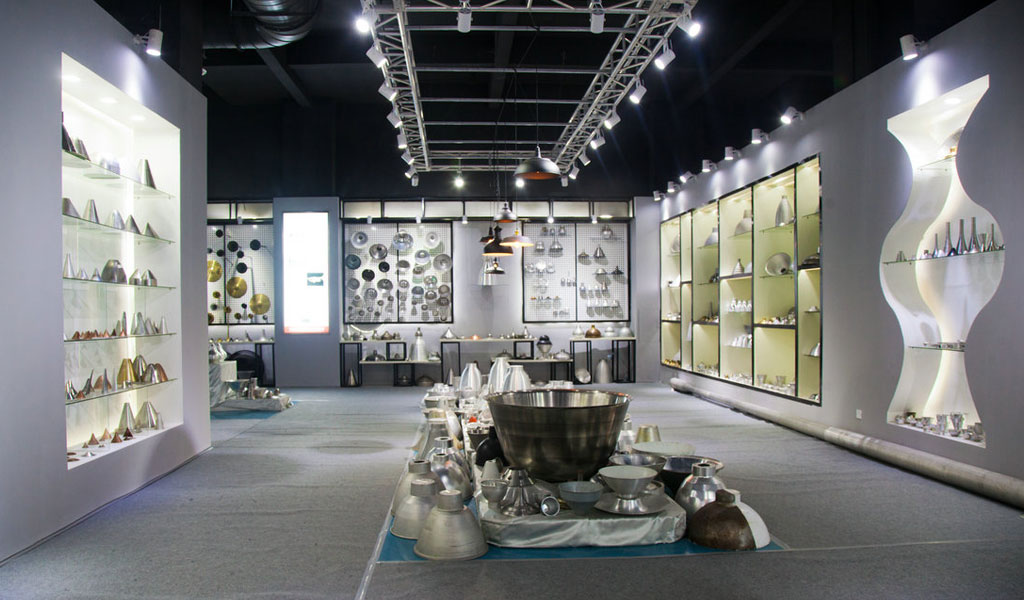
At BE-CU China Metal Spinning company, we make the most of our equipment while monitoring signs of excess wear and stress. In addition, we look into newer, modern equipment and invest in those that can support or increase our manufacturing capabilities. Our team is very mindful of our machines and tools, so we also routinely maintain them to ensure they don’t negatively impact your part’s quality and productivity.
Talk to us today about making a rapid prototype with our CNC metal spinning service. Get a direct quote by chatting with us here or request a free project review.
BE-CU China CNC Metal Spinning service include : CNC Metal Spinning,Metal Spinning Die,Laser Cutting, Tank Heads Spinning,Metal Hemispheres Spinning,Metal Cones Spinning,Metal Dish-Shaped Spinning,Metal Trumpet Spinning,Metal Venturi Spinning,Aluminum Spinning Products,Stainless Steel Spinning Products,Copper Spinning Products,Brass Spinning Products,Steel Spinning Product,Metal Spinnin LED Reflector,Metal Spinning Pressure Vessel,