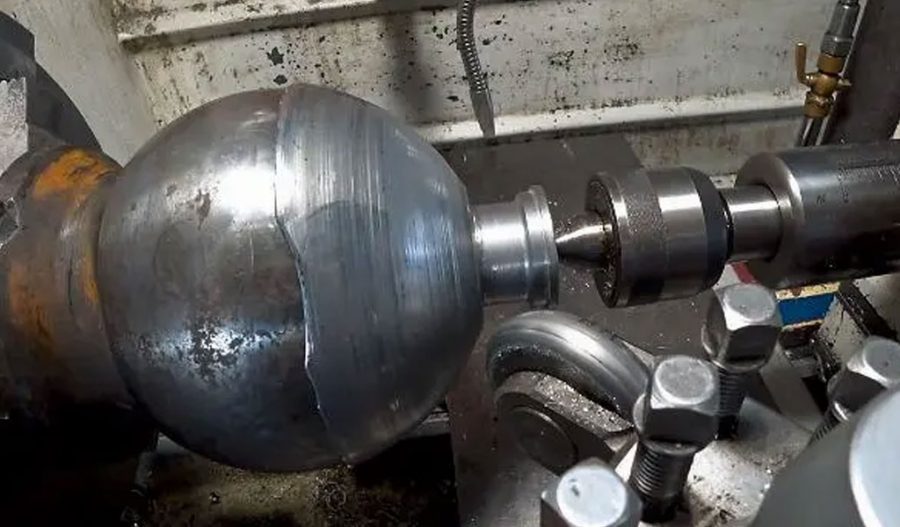
Metal spinning, a time-honored metalworking technique, has been instrumental in the production of high-end commercial cookware. This process, which involves the high-speed rotation of metal discs or tubes to form axially symmetric components, offers unparalleled benefits in terms of material efficiency, structural integrity, thermal properties, and design flexibility. As the culinary world demands cookware that combines durability, performance, and aesthetics, metal spinning has emerged as a preferred method for producing premium-quality pots, pans, and specialty items. This article explores the intricacies of metal spinning, its application in the cookware industry, and the advantages it brings to professional kitchens around the world.
Historical Background
- Origins of Metal Spinning Metal spinning, also referred to as spin forming, dates back to ancient times. Evidence suggests that early civilizations, including the Egyptians and Chinese, employed basic forms of spinning to create functional and decorative items from metal. These early techniques involved manual rotation and shaping, laying the foundation for more sophisticated methods developed during the Industrial Revolution.
- Development of Cookware The evolution of cookware materials and production methods parallels the advancements in metalworking techniques. Early cookware was primarily made from clay and cast iron, with metalworking gaining prominence as technologies improved. The introduction of metal spinning revolutionized cookware design, enabling the production of seamless, robust, and thermally efficient components that met the demands of both domestic and commercial kitchens.
Metal Spinning Process
- Basics of Metal Spinning Metal spinning involves mounting a metal blank onto a lathe, which is then rotated at high speeds. Using various tools, the metal is gradually shaped against a pre-formed mold or mandrel. This process can be applied to a range of metals, including aluminum, stainless steel, copper, and more, each offering unique properties that cater to specific cookware requirements.
- Detailed Process Steps The metal spinning process comprises several stages, starting with the preparation of the metal blank. This involves cutting and smoothing the metal to the desired size and shape. The blank is then secured onto the lathe, and initial shaping begins. Intermediate stages involve progressively refining the shape, with the final stage focusing on precision detailing and finishing touches. Trimming and finishing ensure the component meets exact specifications and quality standards.
- Technical Considerations Successful metal spinning requires careful consideration of various factors, such as material properties, tooling design, speed, force, and temperature control. Different metals respond uniquely to the spinning process, necessitating specific techniques and adjustments to achieve optimal results. Quality control measures are essential to ensure consistency and performance in the final product.
Advantages of Metal Spinning for Cookware
- Material Efficiency One of the primary advantages of metal spinning is its material efficiency. The process generates minimal waste, as the metal is reshaped rather than removed. This efficiency translates to cost savings in raw materials and contributes to the sustainability of the manufacturing process.
- Structural Integrity The seamless construction achieved through metal spinning results in cookware components with superior structural integrity. Unlike welded or riveted parts, metal spun components are less prone to warping, deformation, and leaks, ensuring longevity and reliability in high-intensity cooking environments.
- Thermal Properties Cookware made using metal spinning boasts excellent thermal properties. The even distribution of heat across the surface ensures consistent cooking results, while the material’s ability to retain heat improves energy efficiency. These thermal advantages are particularly beneficial in professional kitchens where precision and performance are paramount.
- Design Flexibility Metal spinning offers remarkable design flexibility, allowing manufacturers to create cookware in a wide range of shapes and sizes. This versatility extends to both functional and aesthetic aspects, enabling customization to meet specific culinary needs and preferences. From intricate detailing to ergonomic handles, metal spinning accommodates various design innovations.
Applications in High-End Commercial Cookware
- Pots and Pans Metal spun pots and pans are staples in commercial kitchens due to their durability and performance. Common types include sauté pans, saucepans, stockpots, and frying pans. The seamless construction and excellent heat distribution make them ideal for professional cooking environments where consistency and reliability are crucial.
- Specialty Cookware In addition to standard pots and pans, metal spinning is used to produce specialty cookware such as woks, kettles, and pressure cookers. Each of these items has unique requirements, and metal spinning provides the precision and customization needed to meet these demands. For instance, the rounded shape of a wok benefits from the even heat distribution offered by metal spinning.
- Professional Kitchen Requirements Professional kitchens demand cookware that can withstand rigorous use and maintain performance over time. Metal spun cookware meets these requirements with its robust construction, resistance to warping, and compliance with health and safety standards. Chefs and culinary professionals often prefer metal spun cookware for its reliability and superior cooking results.
Case Studies and Examples
- Leading Manufacturers Several leading cookware manufacturers have embraced metal spinning to produce high-end commercial cookware. Companies such as All-Clad, Demeyere, and Mauviel utilize this technique to create their signature products, renowned for their quality, performance, and design.
- Chef and Industry Testimonials Renowned chefs and culinary experts often endorse metal spun cookware for its exceptional performance. Testimonials highlight the even heat distribution, durability, and versatility of these products, underscoring their suitability for professional use.
- Comparative Analysis A comparative analysis of metal spun cookware and other manufacturing methods reveals distinct advantages. While traditional methods such as casting and stamping have their merits, metal spinning offers superior structural integrity, design flexibility, and thermal properties, making it the preferred choice for high-end commercial cookware.
Challenges and Future Directions
- Technical Challenges Despite its advantages, metal spinning presents certain technical challenges. Complex designs and shapes may be difficult to achieve, and some materials require specialized techniques to spin effectively. Addressing these challenges involves ongoing research and development to refine the process and expand its capabilities.
- Environmental Considerations The sustainability of metal spinning is a key consideration for manufacturers. While the process is material-efficient, efforts are being made to further reduce its environmental impact. This includes optimizing energy use, recycling metal waste, and exploring eco-friendly materials.
- Innovations and Trends Advances in metal spinning technology continue to shape the future of high-end commercial cookware. Innovations such as computer-aided design (CAD) and automation enhance precision and efficiency, while emerging trends in materials and coatings offer new possibilities for cookware performance and aesthetics.
Conclusion
Metal spun high-end commercial cookware components represent the pinnacle of culinary equipment, combining traditional craftsmanship with modern technology. The seamless construction, superior thermal properties, and design flexibility offered by metal spinning make it an ideal method for producing top-quality cookware. As the culinary industry evolves, metal spinning will continue to play a crucial role in meeting the demands of professional kitchens and discerning chefs worldwide.
Metal Spinning at BE-CU SPUN
At BE-CU SPUN, our experts work closely with you to create custom cookware tailored to your exact specifications. We are able to accommodate a wide array of material thicknesses and part sizes. Our machinery can work with parts up to 100 inches in diameter, as well as 60 inches between centers.
Metal spinning offers rapid turnaround times and affordable costs, and is ideally suited to create strong, lightweight cookware that meets FDA guidelines. To learn more about our metal spinning capabilities, contact us or request your quote today.
Maximize Tooling and CNC Metal Spinning Capabilities.
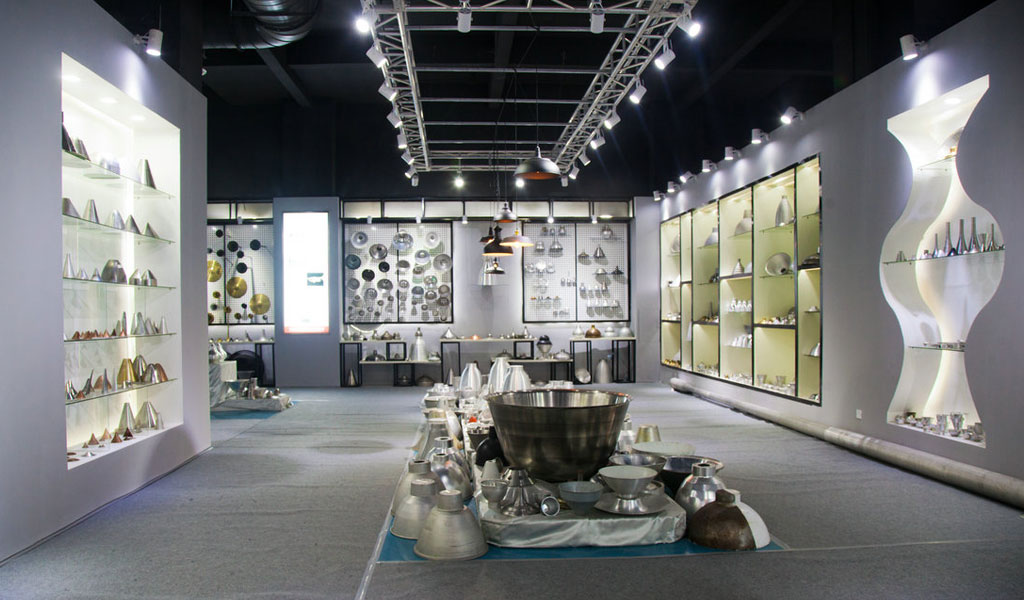
At BE-CU China Metal Spinning company, we make the most of our equipment while monitoring signs of excess wear and stress. In addition, we look into newer, modern equipment and invest in those that can support or increase our manufacturing capabilities. Our team is very mindful of our machines and tools, so we also routinely maintain them to ensure they don’t negatively impact your part’s quality and productivity.
Talk to us today about making a rapid prototype with our CNC metal spinning service. Get a direct quote by chatting with us here or request a free project review.
BE-CU China CNC Metal Spinning service include : CNC Metal Spinning,Metal Spinning Die,Laser Cutting, Tank Heads Spinning,Metal Hemispheres Spinning,Metal Cones Spinning,Metal Dish-Shaped Spinning,Metal Trumpet Spinning,Metal Venturi Spinning,Aluminum Spinning Products,Stainless Steel Spinning Products,Copper Spinning Products,Brass Spinning Products,Steel Spinning Product,Metal Spinnin LED Reflector,Metal Spinning Pressure Vessel,