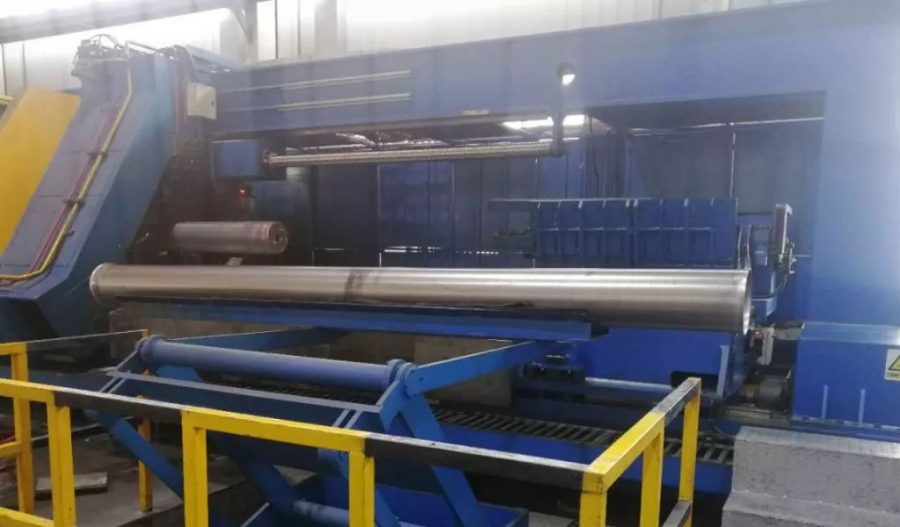
Non-ferrous metal spinning is a manufacturing process used to form axisymmetric parts by rotating a metal blank and forcing it against a mandrel with a spinning tool. This process is particularly advantageous for producing complex shapes from non-ferrous metals, which include aluminum, copper, brass, and titanium, among others. The following article provides a comprehensive analysis of non-ferrous metal spinning, covering its principles, applications, advantages, and detailed comparisons with other manufacturing processes.
Principles of Non-Ferrous Metal Spinning
Non-ferrous metal spinning involves the deformation of a metal blank into a desired shape through a series of controlled rotations and tool movements. The process can be broken down into several key steps:
- Blank Preparation: The initial step involves preparing a metal blank, which is a flat disc or pre-formed shape made from the non-ferrous metal. The blank is typically cut to the required size and shape using shearing or laser cutting techniques.
- Mandrel Setup: The mandrel, a rigid tool that serves as the mold for the final shape, is mounted onto the spinning lathe. The mandrel’s shape corresponds to the desired internal profile of the spun part.
- Blank Mounting: The metal blank is then mounted onto the mandrel. This can be done manually or using automated systems, depending on the complexity and size of the part.
- Spinning Operation: The spinning lathe rotates the mandrel and the blank at high speeds. A spinning tool, typically made from a hard material like tungsten carbide, is applied to the rotating blank. The tool exerts pressure on the blank, forcing it to conform to the shape of the mandrel.
- Finishing: After the spinning operation, the part may undergo additional finishing processes such as trimming, polishing, or heat treatment to achieve the final desired properties and surface finish.
Applications of Non-Ferrous Metal Spinning
Non-ferrous metal spinning is widely used in various industries due to its ability to produce complex, axisymmetric parts with high precision and efficiency. Some of the key applications include:
- Aerospace Industry: Non-ferrous metals like aluminum and titanium are commonly used in the aerospace industry due to their lightweight and high strength-to-weight ratio. Spinning is used to produce components such as jet engine parts, fuel tanks, and structural components.
- Automotive Industry: In the automotive sector, non-ferrous metal spinning is used to manufacture parts like wheel rims, exhaust systems, and fuel tanks. The process allows for the production of lightweight and durable components that meet stringent performance requirements.
- Cookware and Kitchenware: Non-ferrous metals like copper and stainless steel are often spun to produce cookware, such as pots, pans, and bowls. The spinning process ensures uniform wall thickness and excellent surface finish, which are crucial for heat distribution and aesthetics.
- Electronics Industry: Non-ferrous metal spinning is used to produce components for electronic devices, such as heat sinks, enclosures, and reflectors. The process allows for the creation of intricate shapes with high dimensional accuracy.
- Architectural and Decorative Items: Non-ferrous metal spinning is employed to manufacture architectural elements like domes, spires, and decorative panels. The process enables the production of aesthetically pleasing and structurally sound components.
Advantages of Non-Ferrous Metal Spinning
Non-ferrous metal spinning offers several advantages over other manufacturing processes, making it a preferred choice for producing axisymmetric parts. Some of the key benefits include:
- Cost-Effectiveness: The spinning process is generally more cost-effective than other forming methods, especially for small to medium production volumes. The tooling costs are relatively low, and the process can be automated to reduce labor costs.
- High Precision: Non-ferrous metal spinning allows for the production of parts with high dimensional accuracy and consistent wall thickness. The process can achieve tight tolerances, making it suitable for applications requiring precise specifications.
- Material Efficiency: The spinning process minimizes material waste compared to other forming methods like machining. The blank is deformed rather than removed, resulting in less scrap and higher material utilization.
- Versatility: Non-ferrous metal spinning can be used to produce a wide range of shapes and sizes, from small components to large structures. The process is adaptable to various non-ferrous metals, allowing for flexibility in material selection.
- Improved Mechanical Properties: The spinning process can enhance the mechanical properties of the spun part by inducing work hardening. This results in increased strength and improved fatigue resistance, making the parts more durable.
Comparison with Other Manufacturing Processes
To better understand the advantages and limitations of non-ferrous metal spinning, it is essential to compare it with other manufacturing processes. The following table provides a detailed comparison of non-ferrous metal spinning with casting, forging, and machining:
Feature | Non-Ferrous Metal Spinning | Casting | Forging | Machining |
---|---|---|---|---|
Material Utilization | High | Low to Moderate | High | Low |
Dimensional Accuracy | High | Moderate | Moderate to High | High |
Surface Finish | Excellent | Fair to Good | Good | Excellent |
Tooling Costs | Low to Moderate | High | Moderate to High | Low to Moderate |
Production Volume | Small to Medium | Medium to Large | Medium to Large | Small to Medium |
Lead Time | Short to Moderate | Long | Moderate | Short to Moderate |
Mechanical Properties | Enhanced | Good | Excellent | Good |
Complexity of Shapes | Moderate to High | High | Moderate | High |
Automation Potential | High | Low to Moderate | Moderate | High |
Casting
Casting involves pouring molten metal into a mold to create the desired shape. While casting is suitable for producing complex shapes, it often results in lower dimensional accuracy and surface finish compared to spinning. Additionally, casting requires significant tooling costs and longer lead times.
Forging
Forging involves the application of compressive forces to deform a metal blank into the desired shape. Forging can produce parts with excellent mechanical properties and good dimensional accuracy. However, the process is generally more suitable for medium to large production volumes and requires higher tooling costs compared to spinning.
Machining
Machining involves the removal of material from a metal blank using cutting tools. Machining can achieve high dimensional accuracy and excellent surface finish. However, it results in significant material waste and higher production costs, making it less suitable for large-scale production.
Detailed Analysis of Non-Ferrous Metal Spinning
To provide a more in-depth understanding of non-ferrous metal spinning, it is essential to analyze the process parameters, material behavior, and quality control measures.
Process Parameters
The success of non-ferrous metal spinning depends on several critical process parameters, including:
- Spindle Speed: The rotational speed of the spindle affects the deformation rate and the final shape of the spun part. Higher spindle speeds generally result in better surface finish and dimensional accuracy.
- Feed Rate: The feed rate determines the rate at which the spinning tool moves along the blank. Optimal feed rates ensure uniform deformation and minimize defects such as wrinkling and tearing.
- Tool Geometry: The geometry of the spinning tool, including its shape, angle, and material, significantly influences the deformation process. Proper tool design ensures efficient material flow and reduces tool wear.
- Lubrication: The use of lubricants during the spinning process reduces friction between the tool and the blank, enhancing material flow and improving surface finish.
Material Behavior
The behavior of non-ferrous metals during the spinning process is influenced by their mechanical properties, such as ductility, strength, and work hardening characteristics. Some of the key considerations include:
- Ductility: Non-ferrous metals with high ductility, such as aluminum and copper, are more suitable for spinning as they can undergo significant deformation without fracturing.
- Work Hardening: The spinning process induces work hardening, which increases the strength and hardness of the spun part. However, excessive work hardening can lead to embrittlement and reduced formability.
- Thermal Effects: The heat generated during the spinning process can affect the material’s microstructure and mechanical properties. Proper cooling and lubrication are essential to control thermal effects and maintain material integrity.
Quality Control Measures
Ensuring the quality of spun parts requires implementing robust quality control measures, including:
- Dimensional Inspection: Regular dimensional inspections using coordinate measuring machines (CMMs) or other precision instruments ensure that the spun parts meet the required specifications.
- Surface Finish Analysis: Surface finish analysis using profilometers or other surface measurement tools ensures that the spun parts have the desired surface quality.
- Material Testing: Material testing, including tensile tests, hardness tests, and microstructural analysis, ensures that the spun parts meet the required mechanical properties and material standards.
- Process Monitoring: Continuous process monitoring using sensors and data acquisition systems helps detect and correct any deviations in the spinning process, ensuring consistent quality.
Case Studies and Examples
To illustrate the practical applications and benefits of non-ferrous metal spinning, several case studies and examples are presented below:
Case Study 1: Aerospace Component Manufacturing
In the aerospace industry, non-ferrous metal spinning is used to produce critical components such as jet engine casings and fuel tanks. For example, a leading aerospace manufacturer employed spinning to produce titanium engine casings. The process involved spinning a titanium blank onto a mandrel to achieve the desired shape and wall thickness. The spun casings exhibited excellent dimensional accuracy, high strength, and superior fatigue resistance, meeting the stringent performance requirements of the aerospace industry.
Case Study 2: Automotive Wheel Rim Production
In the automotive industry, non-ferrous metal spinning is used to manufacture wheel rims from aluminum alloys. A prominent automotive supplier utilized spinning to produce lightweight and durable wheel rims. The process involved spinning an aluminum blank onto a mandrel to achieve the desired rim profile. The spun rims exhibited uniform wall thickness, excellent surface finish, and enhanced mechanical properties, contributing to improved vehicle performance and fuel efficiency.
Case Study 3: Cookware Manufacturing
In the cookware industry, non-ferrous metal spinning is used to produce high-quality pots and pans from materials like copper and stainless steel. A renowned cookware manufacturer employed spinning to produce copper pots with uniform wall thickness and excellent heat distribution. The spinning process ensured consistent material flow and minimal defects, resulting in cookware with superior performance and aesthetic appeal.
Future Trends and Innovations
The field of non-ferrous metal spinning is continually evolving, driven by advancements in technology and increasing demand for high-performance components. Some of the future trends and innovations in non-ferrous metal spinning include:
- Automation and Robotics: The integration of automation and robotics in the spinning process enhances productivity, reduces labor costs, and improves consistency. Automated spinning systems equipped with robotic arms and advanced sensors enable precise control over the spinning parameters, ensuring high-quality output.
- Advanced Materials: The development of advanced non-ferrous materials, such as high-strength aluminum alloys and titanium composites, expands the applications of metal spinning. These materials offer superior mechanical properties and enhanced performance, making them suitable for demanding industries like aerospace and defense.
- Hybrid Manufacturing: The combination of spinning with other manufacturing processes, such as additive manufacturing and machining, enables the production of complex components with intricate features. Hybrid manufacturing approaches leverage the strengths of each process, resulting in parts with optimized performance and functionality.
- Digital Manufacturing: The adoption of digital manufacturing technologies, including computer-aided design (CAD), computer-aided manufacturing (CAM), and simulation software, enhances the design and production of spun parts. Digital tools enable precise modeling, optimization, and validation of the spinning process, ensuring high-quality and efficient manufacturing.
Conclusion
Non-ferrous metal spinning is a versatile and efficient manufacturing process used to produce axisymmetric parts from a variety of non-ferrous metals. The process offers numerous advantages, including cost-effectiveness, high precision, material efficiency, versatility, and improved mechanical properties. By understanding the principles, applications, and detailed analysis of non-ferrous metal spinning, manufacturers can leverage this process to produce high-quality components for various industries.
As the field of non-ferrous metal spinning continues to evolve, driven by advancements in technology and materials, the potential applications and benefits of this process will expand. The integration of automation, robotics, advanced materials, hybrid manufacturing, and digital technologies will further enhance the capabilities and efficiency of non-ferrous metal spinning, making it a critical manufacturing process for the future.
Maximize Tooling and CNC Metal Spinning Capabilities.
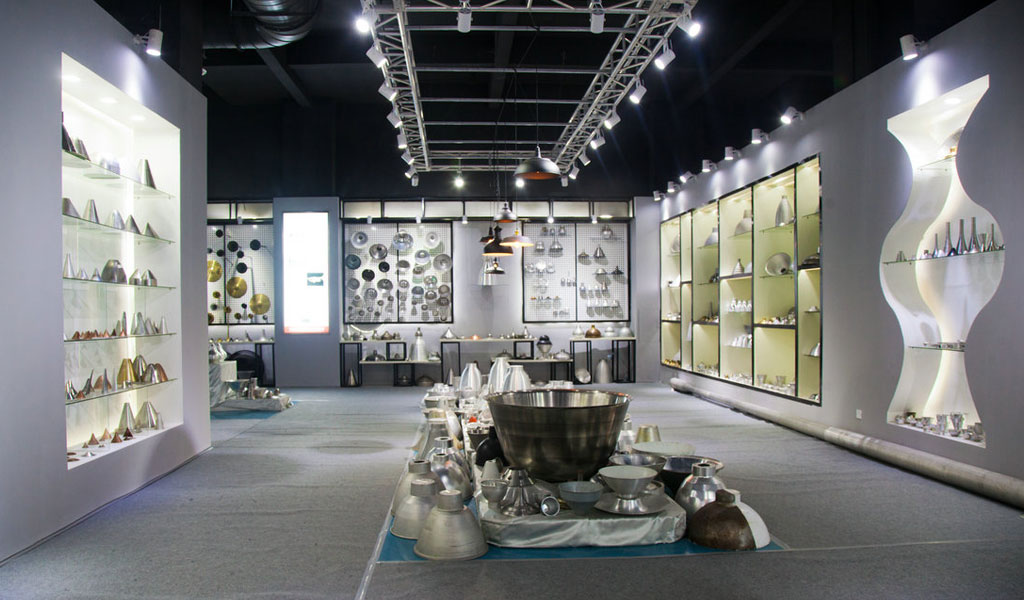
At BE-CU China Metal Spinning company, we make the most of our equipment while monitoring signs of excess wear and stress. In addition, we look into newer, modern equipment and invest in those that can support or increase our manufacturing capabilities. Our team is very mindful of our machines and tools, so we also routinely maintain them to ensure they don’t negatively impact your part’s quality and productivity.
Talk to us today about making a rapid prototype with our CNC metal spinning service. Get a direct quote by chatting with us here or request a free project review.
BE-CU China CNC Metal Spinning service include : CNC Metal Spinning,Metal Spinning Die,Laser Cutting, Tank Heads Spinning,Metal Hemispheres Spinning,Metal Cones Spinning,Metal Dish-Shaped Spinning,Metal Trumpet Spinning,Metal Venturi Spinning,Aluminum Spinning Products,Stainless Steel Spinning Products,Copper Spinning Products,Brass Spinning Products,Steel Spinning Product,Metal Spinnin LED Reflector,Metal Spinning Pressure Vessel,