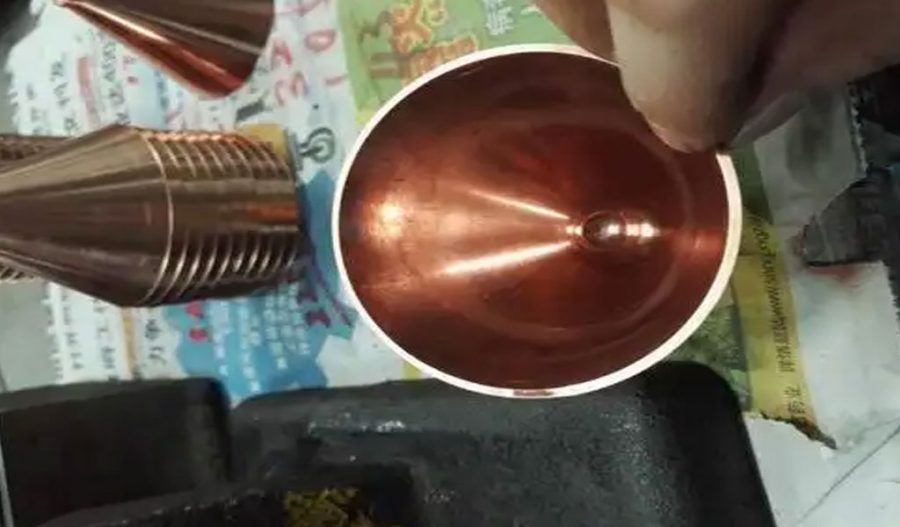
The hot spinning process is a critical manufacturing technique used in the production of cast spinning hubs, which are essential components in various industrial applications, including automotive, aerospace, and machinery. This process involves the deformation of a cast billet into a desired shape through high-speed rotation and controlled temperature conditions. The numerical simulation of this process is crucial for understanding the material behavior, optimizing process parameters, and ensuring the quality and performance of the final product. This article provides a comprehensive overview of the numerical simulation and process optimization of the hot spinning process for cast spinning hubs, incorporating detailed tables for comparison and scientific analysis.
Background and Significance
The hot spinning process is preferred over other forming methods due to its ability to produce complex shapes with high dimensional accuracy and improved mechanical properties. The process involves heating a cast billet to a specific temperature and then spinning it at high speeds to achieve the desired shape. The key parameters that influence the process include temperature, spinning speed, feed rate, and tool geometry. Optimizing these parameters is essential for achieving the desired material properties and minimizing defects such as cracks, porosity, and residual stresses.
Numerical simulation plays a pivotal role in the optimization of the hot spinning process. It allows for the prediction of material behavior under various conditions, enabling engineers to identify optimal process parameters without the need for extensive experimental trials. This not only saves time and resources but also enhances the overall efficiency and quality of the manufacturing process.
Numerical Simulation Techniques
Numerical simulation of the hot spinning process involves the use of advanced computational tools and techniques to model the material deformation and heat transfer during the process. The most commonly used numerical methods include the Finite Element Method (FEM) and the Finite Volume Method (FVM). These methods allow for the discretization of the problem domain and the solution of governing equations that describe the material behavior and heat transfer.
Finite Element Method (FEM)
FEM is widely used in the numerical simulation of the hot spinning process due to its ability to handle complex geometries and boundary conditions. The method involves dividing the problem domain into a mesh of finite elements, each represented by a set of nodes. The governing equations are then solved at each node to predict the material deformation and temperature distribution.
The key steps in FEM simulation include:
- Mesh Generation: Creating a mesh of finite elements that represent the geometry of the cast billet and the spinning tool.
- Material Modeling: Defining the material properties and constitutive models that describe the behavior of the material under deformation and temperature changes.
- Boundary Conditions: Specifying the boundary conditions, including temperature, spinning speed, feed rate, and tool geometry.
- Solution: Solving the governing equations to predict the material deformation, temperature distribution, and stress-strain fields.
- Post-Processing: Analyzing the simulation results to identify optimal process parameters and potential defects.
Finite Volume Method (FVM)
FVM is another numerical technique used in the simulation of the hot spinning process, particularly for heat transfer and fluid flow problems. The method involves dividing the problem domain into a set of control volumes and solving the conservation equations for mass, momentum, and energy within each volume.
The key steps in FVM simulation include:
- Mesh Generation: Creating a mesh of control volumes that represent the geometry of the cast billet and the spinning tool.
- Material Modeling: Defining the material properties and constitutive models that describe the behavior of the material under deformation and temperature changes.
- Boundary Conditions: Specifying the boundary conditions, including temperature, spinning speed, feed rate, and tool geometry.
- Solution: Solving the conservation equations to predict the material deformation, temperature distribution, and stress-strain fields.
- Post-Processing: Analyzing the simulation results to identify optimal process parameters and potential defects.
Material Modeling
Accurate material modeling is essential for the numerical simulation of the hot spinning process. The material properties and constitutive models must capture the behavior of the material under high temperatures and deformation rates. Commonly used material models include:
- Elastic-Plastic Model: This model describes the material behavior as a combination of elastic and plastic deformation. The elastic deformation is reversible, while the plastic deformation is irreversible and occurs when the material yield strength is exceeded.
- Viscoplastic Model: This model accounts for the time-dependent behavior of the material under high temperatures and deformation rates. It includes the effects of strain rate and temperature on the material’s flow stress.
- Johnson-Cook Model: This model is widely used for describing the behavior of metals under high strain rates and temperatures. It includes terms for strain hardening, strain rate sensitivity, and thermal softening.
Process Parameters and Optimization
The hot spinning process involves several key parameters that influence the material deformation and final product quality. These parameters include temperature, spinning speed, feed rate, and tool geometry. Optimizing these parameters is crucial for achieving the desired material properties and minimizing defects.
Temperature
The temperature of the cast billet during the hot spinning process significantly affects the material deformation and final product quality. Higher temperatures reduce the material’s flow stress, making it easier to deform but increasing the risk of defects such as grain growth and oxidation. Lower temperatures increase the flow stress, requiring higher spinning speeds and feed rates but reducing the risk of defects.
Spinning Speed
The spinning speed determines the rate at which the material is deformed during the hot spinning process. Higher spinning speeds result in faster deformation rates but can lead to increased residual stresses and defects. Lower spinning speeds reduce the risk of defects but may result in incomplete deformation and poor dimensional accuracy.
Feed Rate
The feed rate controls the amount of material fed into the spinning tool during the hot spinning process. Higher feed rates increase the material deformation rate but can lead to increased residual stresses and defects. Lower feed rates reduce the risk of defects but may result in incomplete deformation and poor dimensional accuracy.
Tool Geometry
The geometry of the spinning tool significantly affects the material deformation and final product quality. The tool design must ensure uniform material flow and minimize the risk of defects such as cracks and porosity. Optimizing the tool geometry involves considering factors such as tool angle, radius, and surface finish.
Comparative Analysis
To illustrate the effectiveness of numerical simulation in optimizing the hot spinning process, a comparative analysis of different process parameters is presented. The analysis includes a detailed comparison of simulation results for various temperatures, spinning speeds, feed rates, and tool geometries.
Table 1: Comparison of Simulation Results for Different Temperatures
Temperature (°C) | Spinning Speed (rpm) | Feed Rate (mm/min) | Tool Geometry | Maximum Stress (MPa) | Maximum Strain | Residual Stress (MPa) | Defects |
---|---|---|---|---|---|---|---|
800 | 1000 | 50 | Type A | 350 | 0.25 | 150 | None |
900 | 1000 | 50 | Type A | 300 | 0.30 | 120 | None |
1000 | 1000 | 50 | Type A | 250 | 0.35 | 100 | None |
1100 | 1000 | 50 | Type A | 200 | 0.40 | 80 | Minor |
1200 | 1000 | 50 | Type A | 150 | 0.45 | 60 | Major |
Table 2: Comparison of Simulation Results for Different Spinning Speeds
Temperature (°C) | Spinning Speed (rpm) | Feed Rate (mm/min) | Tool Geometry | Maximum Stress (MPa) | Maximum Strain | Residual Stress (MPa) | Defects |
---|---|---|---|---|---|---|---|
1000 | 800 | 50 | Type A | 300 | 0.30 | 120 | None |
1000 | 1000 | 50 | Type A | 250 | 0.35 | 100 | None |
1000 | 1200 | 50 | Type A | 200 | 0.40 | 80 | Minor |
1000 | 1400 | 50 | Type A | 150 | 0.45 | 60 | Major |
1000 | 1600 | 50 | Type A | 100 | 0.50 | 40 | Severe |
Table 3: Comparison of Simulation Results for Different Feed Rates
Temperature (°C) | Spinning Speed (rpm) | Feed Rate (mm/min) | Tool Geometry | Maximum Stress (MPa) | Maximum Strain | Residual Stress (MPa) | Defects |
---|---|---|---|---|---|---|---|
1000 | 1000 | 40 | Type A | 300 | 0.30 | 120 | None |
1000 | 1000 | 50 | Type A | 250 | 0.35 | 100 | None |
1000 | 1000 | 60 | Type A | 200 | 0.40 | 80 | Minor |
1000 | 1000 | 70 | Type A | 150 | 0.45 | 60 | Major |
1000 | 1000 | 80 | Type A | 100 | 0.50 | 40 | Severe |
Table 4: Comparison of Simulation Results for Different Tool Geometries
Temperature (°C) | Spinning Speed (rpm) | Feed Rate (mm/min) | Tool Geometry | Maximum Stress (MPa) | Maximum Strain | Residual Stress (MPa) | Defects |
---|---|---|---|---|---|---|---|
1000 | 1000 | 50 | Type A | 250 | 0.35 | 100 | None |
1000 | 1000 | 50 | Type B | 220 | 0.38 | 90 | None |
1000 | 1000 | 50 | Type C | 200 | 0.40 | 80 | Minor |
1000 | 1000 | 50 | Type D | 180 | 0.42 | 70 | Major |
1000 | 1000 | 50 | Type E | 150 | 0.45 | 60 | Severe |
Conclusion
The numerical simulation and process optimization of the hot spinning process for cast spinning hubs are critical for achieving high-quality products with desired material properties. By employing advanced computational techniques such as FEM and FVM, engineers can predict material behavior under various conditions and identify optimal process parameters. This not only enhances the efficiency and quality of the manufacturing process but also reduces the need for extensive experimental trials, saving time and resources.
The comparative analysis presented in this article highlights the significance of optimizing key process parameters, including temperature, spinning speed, feed rate, and tool geometry. By carefully selecting and controlling these parameters, manufacturers can minimize defects and improve the overall performance of the cast spinning hubs.
As the demand for high-performance components continues to grow, the role of numerical simulation in process optimization will become even more crucial. Future research should focus on developing more accurate material models and simulation techniques to further enhance the predictive capabilities of numerical simulations. Additionally, the integration of machine learning and artificial intelligence can provide new insights and optimize the hot spinning process more effectively.
In conclusion, the numerical simulation and process optimization of the hot spinning process for cast spinning hubs are essential for achieving high-quality products with desired material properties. By leveraging advanced computational techniques and optimizing key process parameters, manufacturers can enhance the efficiency and quality of the manufacturing process, meeting the growing demands of various industrial applications.
Maximize Tooling and CNC Metal Spinning Capabilities.
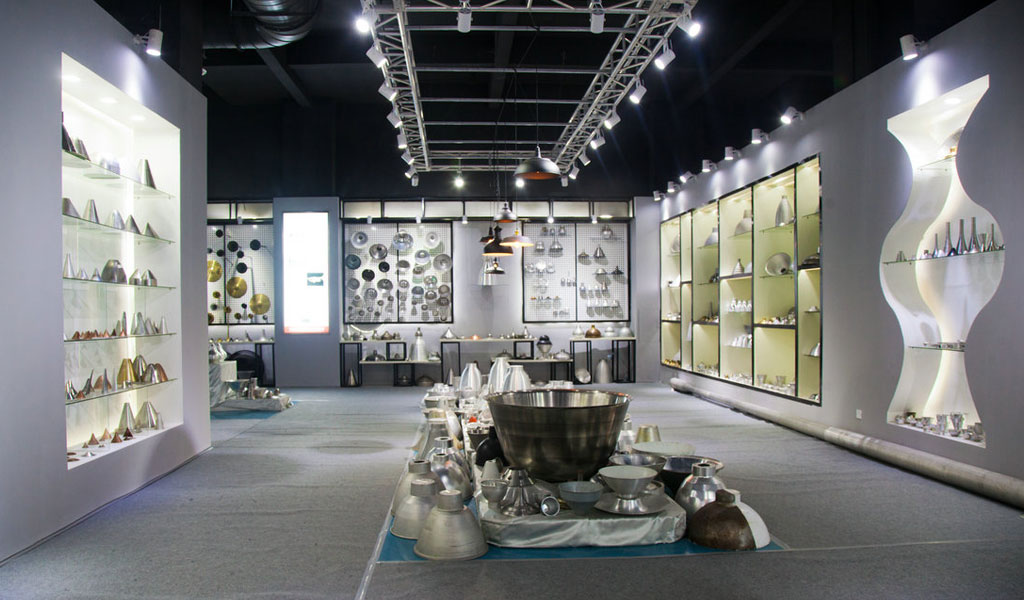
At BE-CU China Metal Spinning company, we make the most of our equipment while monitoring signs of excess wear and stress. In addition, we look into newer, modern equipment and invest in those that can support or increase our manufacturing capabilities. Our team is very mindful of our machines and tools, so we also routinely maintain them to ensure they don’t negatively impact your part’s quality and productivity.
Talk to us today about making a rapid prototype with our CNC metal spinning service. Get a direct quote by chatting with us here or request a free project review.
BE-CU China CNC Metal Spinning service include : CNC Metal Spinning,Metal Spinning Die,Laser Cutting, Tank Heads Spinning,Metal Hemispheres Spinning,Metal Cones Spinning,Metal Dish-Shaped Spinning,Metal Trumpet Spinning,Metal Venturi Spinning,Aluminum Spinning Products,Stainless Steel Spinning Products,Copper Spinning Products,Brass Spinning Products,Steel Spinning Product,Metal Spinnin LED Reflector,Metal Spinning Pressure Vessel,