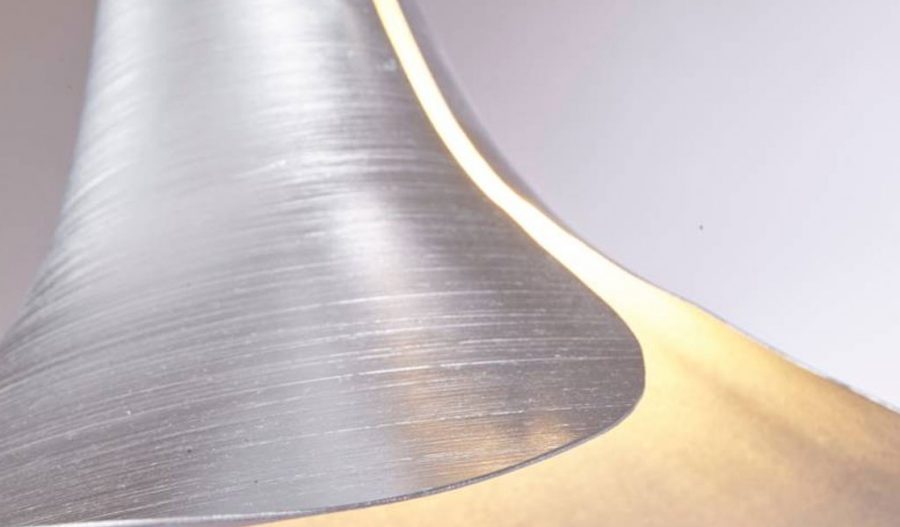
The railway industry is a critical component of modern transportation infrastructure, and the quality of railway axles is paramount to ensuring the safety and efficiency of train operations. Traditional methods of manufacturing railway axles often involve forging and machining processes, which can be time-consuming and costly. In recent years, the development of precision plastic forming techniques, particularly strong hot spinning, has emerged as a promising alternative for producing hollow railway axle blanks. This method offers several advantages, including improved material properties, reduced production time, and enhanced dimensional accuracy.
Historical Context
The concept of hot spinning has been around for centuries, with its origins tracing back to ancient metalworking practices. However, the application of strong hot spinning to the production of railway axles is a relatively recent innovation. The advent of advanced materials and sophisticated manufacturing technologies has enabled the refinement of this process, making it a viable option for the railway industry.
Principles of Strong Hot Spinning
Strong hot spinning is a metal forming process that involves the deformation of a workpiece under high temperatures and rotational forces. The process begins with a preheated billet, which is then subjected to spinning forces that shape it into the desired form. The key parameters that influence the outcome of the spinning process include temperature, rotational speed, and the geometry of the spinning tools.
Temperature Control
Temperature control is crucial in strong hot spinning. The workpiece must be heated to a temperature that allows for sufficient plastic deformation without compromising the material’s structural integrity. For railway axle blanks, the optimal temperature range is typically between 800°C and 1000°C, depending on the material composition.
Rotational Speed
The rotational speed of the spinning tools plays a significant role in determining the final shape and surface finish of the workpiece. Higher rotational speeds can lead to more uniform deformation but may also increase the risk of material defects. Conversely, lower speeds can result in less uniform deformation but are generally safer for the material.
Tool Geometry
The geometry of the spinning tools is another critical factor. The tools must be designed to apply the necessary forces to deform the workpiece into the desired shape. This includes considerations such as the angle of the tool’s contact surface, the radius of curvature, and the overall profile of the tool.
Material Selection
The choice of material for railway axle blanks is crucial for ensuring the durability and performance of the final product. Common materials used in strong hot spinning for railway axles include high-strength steels and alloys. These materials offer a balance of strength, toughness, and wear resistance, making them suitable for the demanding conditions of railway operations.
High-Strength Steels
High-strength steels are widely used in the manufacturing of railway axles due to their excellent mechanical properties. These steels typically contain alloying elements such as chromium, molybdenum, and vanadium, which enhance their strength and resistance to fatigue. The chemical composition of high-strength steels used in strong hot spinning is shown in Table 1.
Element | Content (wt%) |
---|---|
Carbon | 0.25-0.35 |
Manganese | 0.50-0.80 |
Silicon | 0.15-0.35 |
Chromium | 0.80-1.20 |
Molybdenum | 0.20-0.40 |
Vanadium | 0.05-0.15 |
Iron | Balance |
Alloys
Alloys, particularly those containing nickel and chromium, are also used in the production of railway axle blanks. These alloys offer superior corrosion resistance and high-temperature strength, making them ideal for applications where the axles are exposed to harsh environmental conditions. The typical composition of alloys used in strong hot spinning is shown in Table 2.
Element | Content (wt%) |
---|---|
Nickel | 8.0-12.0 |
Chromium | 17.0-21.0 |
Molybdenum | 2.0-3.0 |
Iron | Balance |
Process Steps
The strong hot spinning process for producing hollow railway axle blanks involves several key steps, each of which is critical to achieving the desired final product. These steps include preheating, spinning, cooling, and finishing.
Preheating
Preheating is the initial step in the strong hot spinning process. The billet is heated to the required temperature to ensure uniform deformation during spinning. This step is typically carried out in a furnace, where the temperature is carefully controlled to avoid overheating or underheating the material.
Spinning
Spinning is the core of the strong hot spinning process. The preheated billet is placed on a spinning machine, where it is subjected to rotational forces that deform it into the desired shape. The spinning tools apply pressure to the workpiece, gradually forming it into a hollow cylindrical shape. The spinning process is carefully monitored to ensure that the workpiece maintains its dimensional accuracy and surface finish.
Cooling
Cooling is an essential step in the strong hot spinning process. After spinning, the workpiece is cooled to room temperature to stabilize its structure. The cooling rate is carefully controlled to prevent the formation of residual stresses and to ensure uniform material properties.
Finishing
Finishing is the final step in the strong hot spinning process. The cooled workpiece is subjected to additional machining and surface treatment processes to achieve the required dimensional accuracy and surface finish. This may include operations such as turning, grinding, and polishing.
Advantages of Strong Hot Spinning
Strong hot spinning offers several advantages over traditional methods of manufacturing railway axle blanks. These advantages include improved material properties, reduced production time, and enhanced dimensional accuracy.
Improved Material Properties
The strong hot spinning process results in improved material properties, including higher strength, better toughness, and enhanced wear resistance. This is due to the uniform deformation and controlled cooling rates, which help to refine the material’s microstructure.
Reduced Production Time
Strong hot spinning is a more efficient process compared to traditional forging and machining methods. The spinning process can be completed in a shorter time, reducing the overall production cycle and increasing productivity.
Enhanced Dimensional Accuracy
The strong hot spinning process allows for precise control over the final dimensions of the workpiece. The spinning tools can be designed to achieve the desired shape and size with high accuracy, reducing the need for extensive finishing operations.
Comparison with Traditional Methods
To better understand the benefits of strong hot spinning, it is useful to compare it with traditional methods of manufacturing railway axle blanks. Table 3 provides a comparison of strong hot spinning with traditional forging and machining methods.
Parameter | Strong Hot Spinning | Traditional Forging | Traditional Machining |
---|---|---|---|
Production Time | Short | Long | Long |
Material Properties | Improved | Good | Good |
Dimensional Accuracy | High | Moderate | High |
Surface Finish | Good | Moderate | Excellent |
Cost | Moderate | High | High |
Energy Consumption | Moderate | High | High |
Environmental Impact | Moderate | High | High |
Case Studies
Several case studies have been conducted to evaluate the effectiveness of strong hot spinning in the production of hollow railway axle blanks. These studies have demonstrated the feasibility and advantages of the process in real-world applications.
Case Study 1: High-Speed Railway Axles
In a study conducted by a leading railway manufacturer, strong hot spinning was used to produce hollow axle blanks for high-speed trains. The results showed that the axles produced by strong hot spinning exhibited superior material properties and dimensional accuracy compared to those produced by traditional forging methods. The production time was also significantly reduced, leading to increased productivity and cost savings.
Case Study 2: Heavy-Duty Railway Axles
Another study focused on the production of heavy-duty railway axles using strong hot spinning. The axles were subjected to extensive testing to evaluate their performance under demanding conditions. The results indicated that the axles produced by strong hot spinning had better wear resistance and fatigue strength compared to those produced by traditional machining methods. The improved material properties were attributed to the uniform deformation and controlled cooling rates achieved during the spinning process.
Future Directions
The strong hot spinning process holds great promise for the future of railway axle manufacturing. As the technology continues to advance, several areas of research and development are likely to gain attention.
Advanced Materials
The development of advanced materials with enhanced properties is a key area of research. New alloys and composite materials are being explored to improve the strength, toughness, and wear resistance of railway axles. These materials could further enhance the performance and durability of axles produced by strong hot spinning.
Process Optimization
Optimizing the strong hot spinning process is another important area of research. This includes refining the temperature control, rotational speed, and tool geometry to achieve even better material properties and dimensional accuracy. Advanced simulation tools and machine learning algorithms could be employed to optimize the process parameters and improve the overall efficiency of the spinning process.
Environmental Impact
Reducing the environmental impact of the strong hot spinning process is a growing concern. Research is being conducted to develop more energy-efficient spinning machines and to minimize the use of harmful chemicals in the process. Sustainable manufacturing practices, such as recycling and waste reduction, are also being explored to make the process more environmentally friendly.
Conclusion
The strong hot spinning process offers a promising alternative for the production of hollow railway axle blanks. With its advantages in material properties, production time, and dimensional accuracy, this method has the potential to revolutionize the railway industry. As research and development continue to advance, the strong hot spinning process is likely to become an increasingly important technology in the manufacturing of railway axles.
Maximize Tooling and CNC Metal Spinning Capabilities.
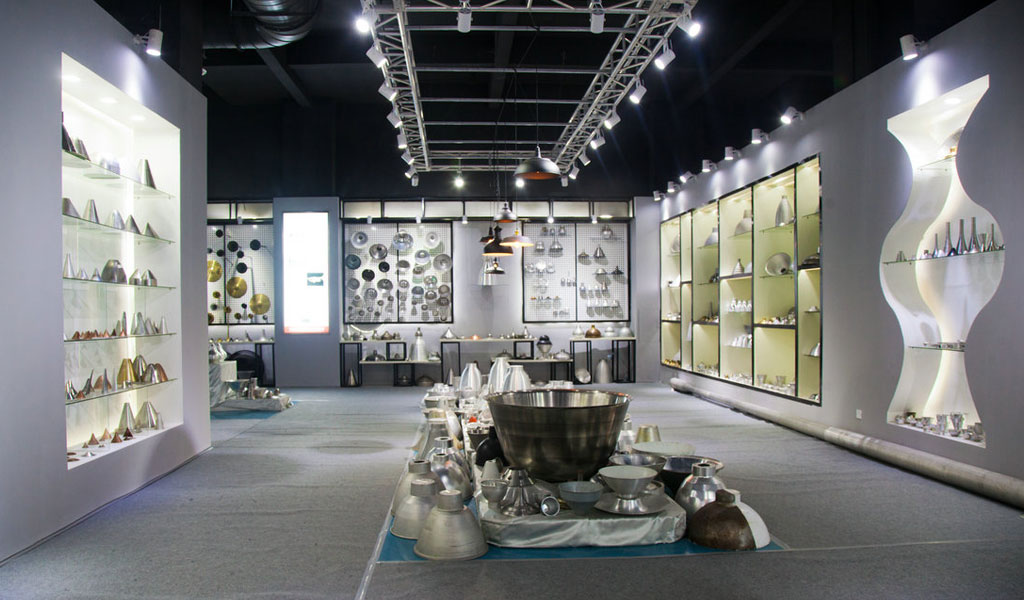
At BE-CU China Metal Spinning company, we make the most of our equipment while monitoring signs of excess wear and stress. In addition, we look into newer, modern equipment and invest in those that can support or increase our manufacturing capabilities. Our team is very mindful of our machines and tools, so we also routinely maintain them to ensure they don’t negatively impact your part’s quality and productivity.
Talk to us today about making a rapid prototype with our CNC metal spinning service. Get a direct quote by chatting with us here or request a free project review.
BE-CU China CNC Metal Spinning service include : CNC Metal Spinning,Metal Spinning Die,Laser Cutting, Tank Heads Spinning,Metal Hemispheres Spinning,Metal Cones Spinning,Metal Dish-Shaped Spinning,Metal Trumpet Spinning,Metal Venturi Spinning,Aluminum Spinning Products,Stainless Steel Spinning Products,Copper Spinning Products,Brass Spinning Products,Steel Spinning Product,Metal Spinnin LED Reflector,Metal Spinning Pressure Vessel,