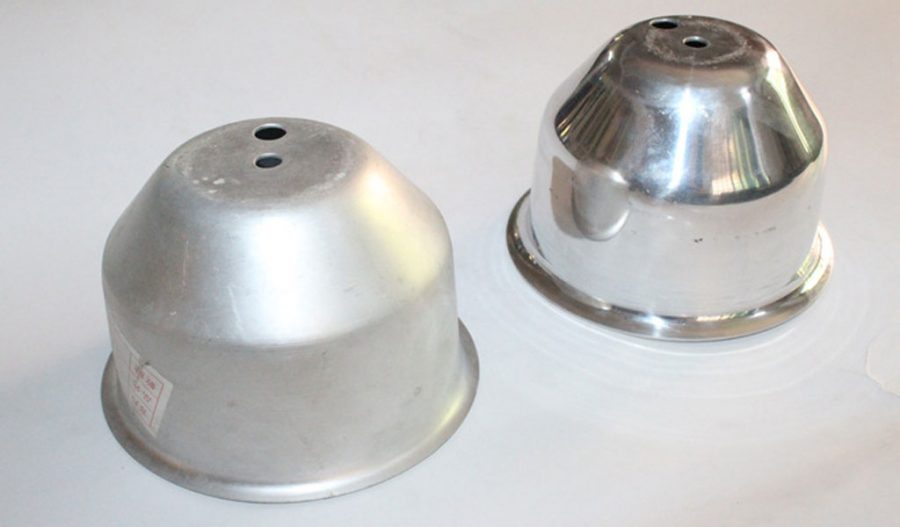
The precision spinning forming process is a highly specialized manufacturing technique used to produce large-size, thin-walled cylindrical parts from magnesium alloys. This process combines the advantages of traditional spinning with advanced material science to create components that are both lightweight and structurally robust. Magnesium alloys, known for their excellent strength-to-weight ratio and good machinability, are increasingly being used in aerospace, automotive, and other high-performance industries. This article delves into the intricacies of the precision spinning forming process, focusing on the unique challenges and advantages associated with large-size magnesium alloy thin-walled cylindrical parts.
Historical Context
The origins of spinning can be traced back to ancient times, where it was used for shaping metals into various forms. However, the modern precision spinning process has evolved significantly with the advent of advanced materials and computer-controlled machinery. The application of magnesium alloys in precision spinning is a more recent development, driven by the need for lightweight and high-performance materials in industries such as aerospace and automotive.
Material Properties of Magnesium Alloys
Magnesium alloys are characterized by their low density, high specific strength, and good damping capacity. These properties make them ideal for applications where weight reduction is critical. Common magnesium alloys used in precision spinning include AZ31, AZ61, and AZ91. The following table compares the mechanical properties of these alloys:
Property | AZ31 | AZ61 | AZ91 |
---|---|---|---|
Density (g/cm³) | 1.77 | 1.80 | 1.81 |
Tensile Strength (MPa) | 260 | 310 | 275 |
Yield Strength (MPa) | 200 | 240 | 160 |
Elongation (%) | 15 | 12 | 6 |
Modulus of Elasticity (GPa) | 45 | 45 | 45 |
Precision Spinning Process
The precision spinning process involves the use of a spinning lathe, where a blank (typically a disc or a preformed cylinder) is rotated at high speeds. A spinning tool, usually made of hardened steel or carbide, is then used to shape the blank into the desired cylindrical form. The process can be broken down into several key steps:
- Blank Preparation: The magnesium alloy blank is prepared to the required dimensions. This may involve cutting a disc from a sheet or casting a preformed cylinder.
- Mandrel Mounting: The blank is mounted on a mandrel, which is then secured in the spinning lathe.
- Spinning: The mandrel and blank are rotated at high speeds, typically ranging from 500 to 2000 RPM, depending on the size and material of the blank.
- Tool Application: The spinning tool is applied to the rotating blank, gradually shaping it into the desired cylindrical form. The tool follows a predetermined path, controlled by a computer numerical control (CNC) system.
- Finishing: After the initial spinning, the part may undergo additional finishing steps, such as annealing to relieve residual stresses or further machining to achieve the final dimensions and surface finish.
Challenges in Precision Spinning of Magnesium Alloys
While magnesium alloys offer numerous advantages, they also present unique challenges in the precision spinning process:
- Thermal Stability: Magnesium alloys are prone to thermal instability, which can lead to cracking and distortion during the spinning process. Careful control of the spinning speed and tool pressure is essential to mitigate these issues.
- Corrosion Resistance: Magnesium alloys are susceptible to corrosion, particularly in humid environments. Special coatings or surface treatments may be required to protect the finished parts.
- Tool Wear: The high strength and hardness of magnesium alloys can lead to accelerated tool wear. The use of advanced tool materials, such as carbide or diamond-coated tools, can help extend tool life.
Advantages of Precision Spinning
Despite the challenges, the precision spinning process offers several advantages for the production of large-size magnesium alloy thin-walled cylindrical parts:
- High Precision: The process allows for the production of parts with tight dimensional tolerances and excellent surface finish.
- Cost-Effectiveness: Precision spinning is generally more cost-effective than other forming processes, such as forging or casting, particularly for large-size parts.
- Flexibility: The process can be adapted to produce a wide range of cylindrical shapes and sizes, making it suitable for various applications.
Applications
The precision spinning forming process of large-size magnesium alloy thin-walled cylindrical parts has found applications in several high-performance industries:
- Aerospace: Magnesium alloy cylindrical parts are used in aircraft structures, such as fuselage frames and engine components, where weight reduction is critical.
- Automotive: Lightweight magnesium alloy parts are used in vehicle bodies and engine components to improve fuel efficiency.
- Defense: Magnesium alloy cylindrical parts are used in military vehicles and equipment, where strength and durability are essential.
Case Studies
To illustrate the practical application of the precision spinning process, several case studies are presented:
- Aerospace Component: A large-size magnesium alloy cylindrical part was produced for an aircraft engine component. The part had a diameter of 1.5 meters and a wall thickness of 2 mm. The precision spinning process allowed for the production of the part with a dimensional tolerance of ±0.1 mm and a surface finish of Ra 1.6 µm.
- Automotive Component: A magnesium alloy cylindrical part was produced for a vehicle engine component. The part had a diameter of 0.8 meters and a wall thickness of 1.5 mm. The precision spinning process allowed for the production of the part with a dimensional tolerance of ±0.05 mm and a surface finish of Ra 1.2 µm.
Comparison with Other Forming Processes
The following table compares the precision spinning process with other common forming processes for large-size magnesium alloy thin-walled cylindrical parts:
Process | Precision Spinning | Forging | Casting |
---|---|---|---|
Dimensional Tolerance | ±0.1 mm | ±0.5 mm | ±1.0 mm |
Surface Finish | Ra 1.6 µm | Ra 3.2 µm | Ra 6.3 µm |
Cost | Moderate | High | Low |
Flexibility | High | Low | Moderate |
Tool Wear | Moderate | High | Low |
Future Directions
The precision spinning forming process of large-size magnesium alloy thin-walled cylindrical parts is a rapidly evolving field. Future research and development are likely to focus on the following areas:
- Advanced Materials: The development of new magnesium alloys with improved thermal stability and corrosion resistance.
- Tooling Innovations: The use of advanced tool materials and coatings to reduce tool wear and improve part quality.
- Automation: The integration of advanced automation and control systems to improve the precision and efficiency of the spinning process.
Conclusion
The precision spinning forming process of large-size magnesium alloy thin-walled cylindrical parts is a critical technology for the production of lightweight and high-performance components. Despite the challenges associated with magnesium alloys, the process offers numerous advantages, including high precision, cost-effectiveness, and flexibility. As research and development continue, the precision spinning process is poised to play an increasingly important role in high-performance industries such as aerospace, automotive, and defense.
Maximize Tooling and CNC Metal Spinning Capabilities.
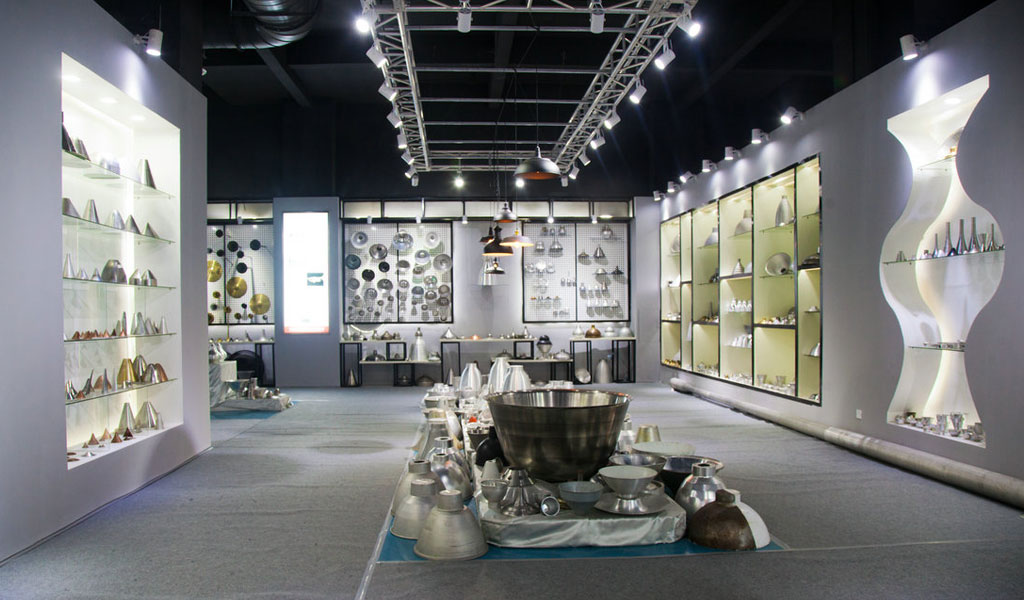
At BE-CU China Metal Spinning company, we make the most of our equipment while monitoring signs of excess wear and stress. In addition, we look into newer, modern equipment and invest in those that can support or increase our manufacturing capabilities. Our team is very mindful of our machines and tools, so we also routinely maintain them to ensure they don’t negatively impact your part’s quality and productivity.
Talk to us today about making a rapid prototype with our CNC metal spinning service. Get a direct quote by chatting with us here or request a free project review.
BE-CU China CNC Metal Spinning service include : CNC Metal Spinning,Metal Spinning Die,Laser Cutting, Tank Heads Spinning,Metal Hemispheres Spinning,Metal Cones Spinning,Metal Dish-Shaped Spinning,Metal Trumpet Spinning,Metal Venturi Spinning,Aluminum Spinning Products,Stainless Steel Spinning Products,Copper Spinning Products,Brass Spinning Products,Steel Spinning Product,Metal Spinnin LED Reflector,Metal Spinning Pressure Vessel,