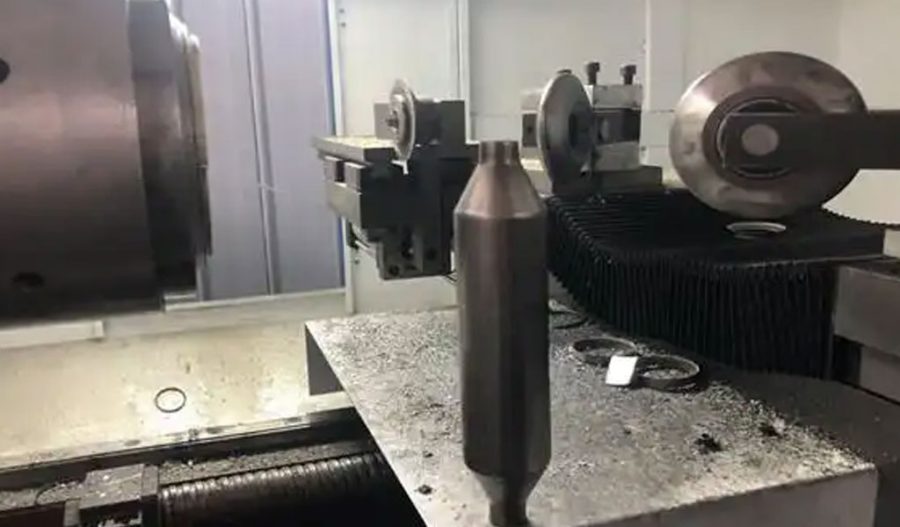
Precision spinning is a manufacturing process used to produce complex curved thin-walled parts with high accuracy and repeatability. This technique is particularly valuable in industries such as aerospace, automotive, and medical devices, where the demand for lightweight, high-strength components is paramount. The process involves the controlled deformation of a metal blank into a desired shape using a spinning tool, typically on a lathe. This article delves into the intricacies of precision spinning, its applications, advantages, and the scientific principles underlying its effectiveness.
Historical Background
The origins of spinning can be traced back to ancient times, where artisans used manual techniques to shape metal into various forms. However, the modern precision spinning process emerged during the Industrial Revolution, driven by the need for mass production and standardization. The advent of computer numerical control (CNC) machines in the late 20th century further revolutionized the process, enabling the production of highly complex and precise parts.
Fundamental Principles
Precision spinning relies on the principles of plastic deformation, where a metal blank is shaped by applying a controlled force. The process can be broadly categorized into two types: conventional spinning and shear spinning.
- Conventional Spinning: This method involves the gradual deformation of a metal blank over a mandrel using a spinning tool. The tool applies pressure to the blank, causing it to flow and conform to the shape of the mandrel. This process is typically used for producing axisymmetric parts.
- Shear Spinning: In shear spinning, the metal blank is deformed by a spinning tool that applies a shearing force. This method is particularly effective for producing parts with complex curves and thin walls. The shearing action allows for more controlled deformation, resulting in higher precision and reduced material waste.
Material Considerations
The choice of material is crucial in precision spinning. Commonly used materials include aluminum, stainless steel, titanium, and various alloys. Each material has unique properties that affect the spinning process, such as ductility, strength, and formability.
Material | Ductility (%) | Tensile Strength (MPa) | Formability Index |
---|---|---|---|
Aluminum | 30-40 | 200-300 | High |
Stainless Steel | 20-30 | 500-700 | Medium |
Titanium | 15-25 | 800-1000 | Low |
Copper | 40-50 | 200-300 | High |
Process Parameters
Several key parameters influence the precision spinning process, including:
- Spindle Speed: The rotational speed of the spindle affects the deformation rate and surface finish of the part. Higher speeds generally result in smoother surfaces but can also increase the risk of material tearing.
- Feed Rate: The rate at which the spinning tool advances determines the amount of material deformation per revolution. A slower feed rate allows for more controlled deformation but increases processing time.
- Tool Geometry: The shape and angle of the spinning tool significantly impact the deformation process. Tools with sharper angles can achieve higher precision but may require more frequent maintenance.
- Lubrication: Proper lubrication is essential to reduce friction and heat generation during the spinning process. Common lubricants include oils, greases, and solid lubricants like graphite.
Advantages of Precision Spinning
Precision spinning offers several advantages over traditional manufacturing methods such as casting, forging, and machining:
- High Precision: The controlled deformation process allows for the production of parts with tight tolerances and high dimensional accuracy.
- Reduced Material Waste: Unlike machining, which removes material to achieve the desired shape, spinning deforms the material, resulting in minimal waste.
- Cost-Effective: The process is highly efficient, requiring less energy and fewer resources compared to other manufacturing methods.
- Versatility: Precision spinning can produce a wide range of complex shapes and sizes, making it suitable for various applications.
Applications
Precision spinning is widely used in several industries due to its ability to produce high-quality, complex parts. Some of the key applications include:
- Aerospace: The aerospace industry demands lightweight, high-strength components. Precision spinning is used to produce parts such as aircraft engine components, fuel tanks, and structural panels.
- Automotive: In the automotive industry, precision spinning is used to manufacture parts like exhaust systems, fuel tanks, and structural components. The process helps achieve the required strength and durability while minimizing weight.
- Medical Devices: Medical devices often require precise, thin-walled components. Precision spinning is used to produce parts such as implants, surgical instruments, and diagnostic equipment.
- Consumer Goods: Precision spinning is also used in the production of consumer goods, including cookware, lighting fixtures, and decorative items. The process allows for the creation of aesthetically pleasing and functional products.
Scientific Principles
The scientific principles underlying precision spinning involve a combination of materials science, mechanics, and thermodynamics. Key concepts include:
- Plastic Deformation: The deformation of the metal blank occurs in the plastic region, where the material undergoes permanent shape change without fracture. The stress-strain relationship in this region is crucial for understanding the deformation behavior.
- Strain Hardening: As the material deforms, it undergoes strain hardening, where the material’s strength increases due to the accumulation of dislocations. This phenomenon is essential for achieving the desired mechanical properties.
- Heat Generation: The deformation process generates heat, which can affect the material’s properties and the final part’s quality. Proper cooling and lubrication are necessary to manage heat generation and prevent material failure.
- Residual Stresses: The spinning process can introduce residual stresses in the part, which can affect its performance and longevity. Controlling these stresses through process optimization is crucial for achieving high-quality parts.
Comparison with Other Manufacturing Methods
To understand the unique advantages of precision spinning, it is helpful to compare it with other manufacturing methods. The following table provides a comparison of precision spinning with casting, forging, and machining:
Parameter | Precision Spinning | Casting | Forging | Machining |
---|---|---|---|---|
Material Waste | Low | High | Medium | High |
Dimensional Accuracy | High | Low | Medium | High |
Surface Finish | Good | Poor | Fair | Excellent |
Production Speed | Medium | Slow | Fast | Slow |
Cost | Medium | Low | High | High |
Suitability for Complex Shapes | High | Low | Medium | High |
Case Studies
Several case studies highlight the effectiveness of precision spinning in various applications:
- Aerospace Engine Component: A leading aerospace manufacturer used precision spinning to produce a complex curved thin-walled engine component. The process resulted in a 30% reduction in material waste and a 20% improvement in dimensional accuracy compared to traditional machining methods.
- Automotive Exhaust System: An automotive company employed precision spinning to manufacture exhaust system components. The process allowed for the production of lightweight, high-strength parts with improved fuel efficiency and reduced emissions.
- Medical Implant: A medical device manufacturer utilized precision spinning to produce a thin-walled implant. The process ensured high dimensional accuracy and surface finish, critical for the implant’s biocompatibility and functionality.
Future Trends
The future of precision spinning is poised for significant advancements driven by technological innovations and increasing demand for high-precision, lightweight components. Key trends include:
- Advanced Materials: The development of new materials with enhanced properties, such as high-strength alloys and composite materials, will expand the applications of precision spinning.
- Automation and AI: The integration of automation and artificial intelligence (AI) in the spinning process will improve efficiency, accuracy, and consistency. AI-driven systems can optimize process parameters in real-time, reducing the risk of defects and enhancing productivity.
- Sustainability: As sustainability becomes a critical consideration, precision spinning will play a vital role in reducing material waste and energy consumption. The process’s inherent efficiency makes it an attractive option for environmentally conscious manufacturing.
- Hybrid Manufacturing: The combination of precision spinning with other manufacturing techniques, such as additive manufacturing, will enable the production of even more complex and customized parts. Hybrid manufacturing approaches can leverage the strengths of multiple processes to achieve unprecedented levels of precision and functionality.
Conclusion
Precision spinning of complex curved thin-walled parts is a sophisticated manufacturing process that combines scientific principles with advanced technology to produce high-quality components. Its advantages, including high precision, reduced material waste, and cost-effectiveness, make it a valuable technique in various industries. As technological advancements continue to drive innovation, precision spinning will remain a cornerstone of modern manufacturing, contributing to the development of lighter, stronger, and more sustainable products.
In summary, precision spinning offers a unique blend of precision, efficiency, and versatility, making it an indispensable tool in the manufacturing arsenal. Its applications span a wide range of industries, from aerospace and automotive to medical devices and consumer goods. With ongoing research and development, the future of precision spinning promises even greater capabilities and broader applications, ensuring its continued relevance and importance in the manufacturing landscape.
Maximize Tooling and CNC Metal Spinning Capabilities.
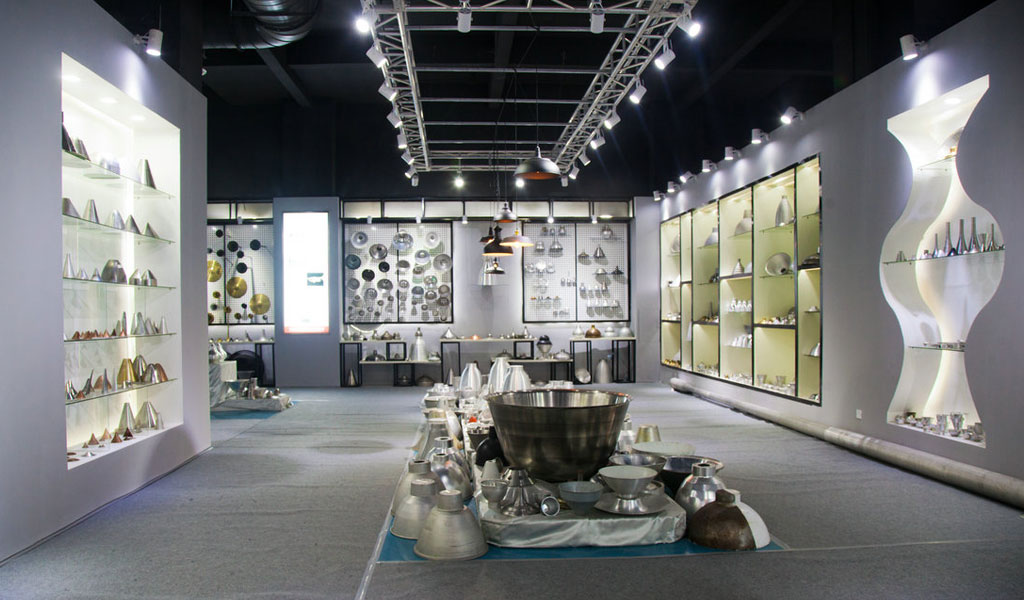
At BE-CU China Metal Spinning company, we make the most of our equipment while monitoring signs of excess wear and stress. In addition, we look into newer, modern equipment and invest in those that can support or increase our manufacturing capabilities. Our team is very mindful of our machines and tools, so we also routinely maintain them to ensure they don’t negatively impact your part’s quality and productivity.
Talk to us today about making a rapid prototype with our CNC metal spinning service. Get a direct quote by chatting with us here or request a free project review.
BE-CU China CNC Metal Spinning service include : CNC Metal Spinning,Metal Spinning Die,Laser Cutting, Tank Heads Spinning,Metal Hemispheres Spinning,Metal Cones Spinning,Metal Dish-Shaped Spinning,Metal Trumpet Spinning,Metal Venturi Spinning,Aluminum Spinning Products,Stainless Steel Spinning Products,Copper Spinning Products,Brass Spinning Products,Steel Spinning Product,Metal Spinnin LED Reflector,Metal Spinning Pressure Vessel,