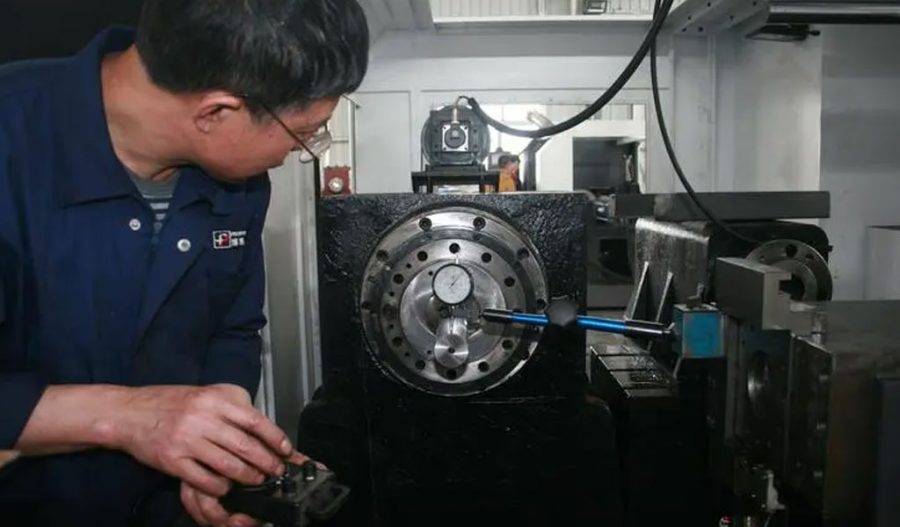
Precision spinning and metal stamping are two widely used manufacturing processes in the metalworking industry. Each method offers unique advantages and applications, making them suitable for different types of production requirements. This article provides an in-depth comparison of precision spinning and metal stamping, detailing their processes, advantages, limitations, applications, and technological advancements.
Precision Spinning
Precision spinning, also known as metal spinning or spin forming, is a machining process used to create axially symmetric parts by rotating a metal blank at high speed while applying pressure with a tool. This process can produce complex shapes with high accuracy and smooth finishes. It is particularly suited for creating cylindrical, conical, and spherical components.
History
The origins of metal spinning can be traced back to ancient times when craftsmen used rudimentary tools to form metal objects. The industrial revolution and advancements in machinery in the 19th and 20th centuries significantly improved the precision and efficiency of the spinning process.
Process
The precision spinning process involves several key steps:
- Blank Preparation: A flat metal disc, or blank, is cut to the required size.
- Mounting: The blank is mounted onto a mandrel, which is attached to a lathe.
- Spinning: The lathe rotates the mandrel and blank at high speed. A roller or forming tool applies pressure to the blank, gradually shaping it against the mandrel.
- Finishing: The formed part is trimmed and finished to achieve the desired specifications.
Materials
Precision spinning can be performed on various materials, including:
- Metals: Aluminum, stainless steel, brass, copper, and titanium.
- Alloys: Various metal alloys depending on the required properties.
- Other Materials: Certain plastics and composite materials can also be spun.
Advantages
- Cost-Effective for Small Batches: Precision spinning is economical for low to medium production volumes, as it requires minimal tooling compared to other methods.
- Flexibility: The process can produce a wide range of shapes and sizes with intricate details.
- Material Efficiency: Minimal material wastage as the process involves deforming the blank rather than cutting away excess material.
- High Strength: Spun parts often exhibit enhanced strength and durability due to work hardening during the spinning process.
Limitations
- Limited Geometries: Precision spinning is primarily suitable for axially symmetric parts, limiting its application for complex non-symmetric shapes.
- Labor-Intensive: Skilled operators are required to achieve high precision, which can increase labor costs.
- Thickness Variation: Maintaining consistent thickness across the part can be challenging, especially for large components.
Applications
Precision spinning is widely used in various industries, including:
- Aerospace: Components such as rocket nose cones, satellite dishes, and aircraft engine parts.
- Automotive: Parts like wheel rims, exhaust components, and fuel tanks.
- Lighting: Reflectors, lampshades, and decorative fixtures.
- Consumer Goods: Cookware, musical instruments, and decorative items.
Metal Stamping
Metal stamping is a manufacturing process that involves shaping metal sheets into desired forms using a press and a set of dies. This process is highly efficient for producing large quantities of parts with consistent quality and precision. Metal stamping includes various techniques such as blanking, punching, bending, and embossing.
History
The history of metal stamping dates back to the early industrial era when the need for mass production led to the development of mechanical presses and dies. Over time, advancements in machinery and computer technology have significantly enhanced the precision and speed of the stamping process.
Process
The metal stamping process comprises several stages:
- Blanking: Cutting the metal sheet into specific shapes or blanks.
- Forming: Shaping the blanks into the desired geometry using various techniques like bending, drawing, and coining.
- Punching: Creating holes or cutouts in the metal sheet.
- Trimming: Removing excess material to achieve the final shape.
- Finishing: Additional processes such as deburring, polishing, or coating to enhance the surface quality.
Materials
Metal stamping can be performed on a wide range of materials, including:
- Metals: Steel, aluminum, brass, copper, and nickel.
- Alloys: Various alloys tailored to specific applications.
- Non-Metal Materials: Plastics and composite materials can also be stamped.
Advantages
- High Production Efficiency: Metal stamping is ideal for high-volume production, offering fast cycle times and consistent quality.
- Precision and Consistency: The use of dies ensures high precision and uniformity across all parts.
- Versatility: Capable of producing complex shapes with fine details.
- Cost-Effective for Large Volumes: The initial tooling costs are offset by the low per-unit cost in large production runs.
Limitations
- High Initial Tooling Cost: Designing and manufacturing dies can be expensive, making it less cost-effective for small production runs.
- Limited Material Thickness: Stamping is generally suitable for thinner materials, as thicker materials require more force and robust dies.
- Potential for Material Waste: Excess material from blanking and punching processes can lead to material wastage.
Applications
Metal stamping is widely used in various industries, including:
- Automotive: Body panels, chassis components, brackets, and fasteners.
- Electronics: Connectors, terminals, and heat sinks.
- Aerospace: Structural components, brackets, and shielding parts.
- Consumer Goods: Appliances, tools, and electronic enclosures.
Technological Advancements
Precision Spinning
- Computer Numerical Control (CNC): CNC technology has revolutionized precision spinning by automating the process and enhancing accuracy. CNC spinning machines can produce complex shapes with minimal human intervention.
- Advanced Materials: Development of new alloys and composite materials has expanded the range of applications for precision spinning.
- Simulation Software: Advanced simulation software allows engineers to model and optimize the spinning process, reducing trial-and-error and improving efficiency.
Metal Stamping
- High-Speed Stamping: Modern high-speed presses can achieve higher production rates, significantly reducing cycle times.
- Progressive Die Stamping: This method uses a series of dies to perform multiple operations in a single press cycle, enhancing efficiency and reducing handling.
- Servo-Driven Presses: Servo-driven presses offer precise control over the stamping process, enabling the production of complex parts with high accuracy.
- Laser Cutting Integration: Combining laser cutting with stamping allows for intricate designs and reduces the need for multiple dies.
Conclusion
Precision spinning and metal stamping are essential manufacturing processes with distinct advantages and applications. Precision spinning excels in producing complex, axially symmetric parts with high strength and minimal material waste, making it ideal for industries like aerospace and automotive. Metal stamping, on the other hand, is highly efficient for large-volume production of complex shapes with consistent quality, suitable for automotive, electronics, and consumer goods industries.
Both processes have seen significant technological advancements, enhancing their capabilities and expanding their applications. The choice between precision spinning and metal stamping depends on factors such as production volume, part geometry, material, and cost considerations. Understanding the strengths and limitations of each method is crucial for selecting the most appropriate manufacturing process for specific requirements.
Maximize Tooling and CNC Metal Spinning Capabilities.
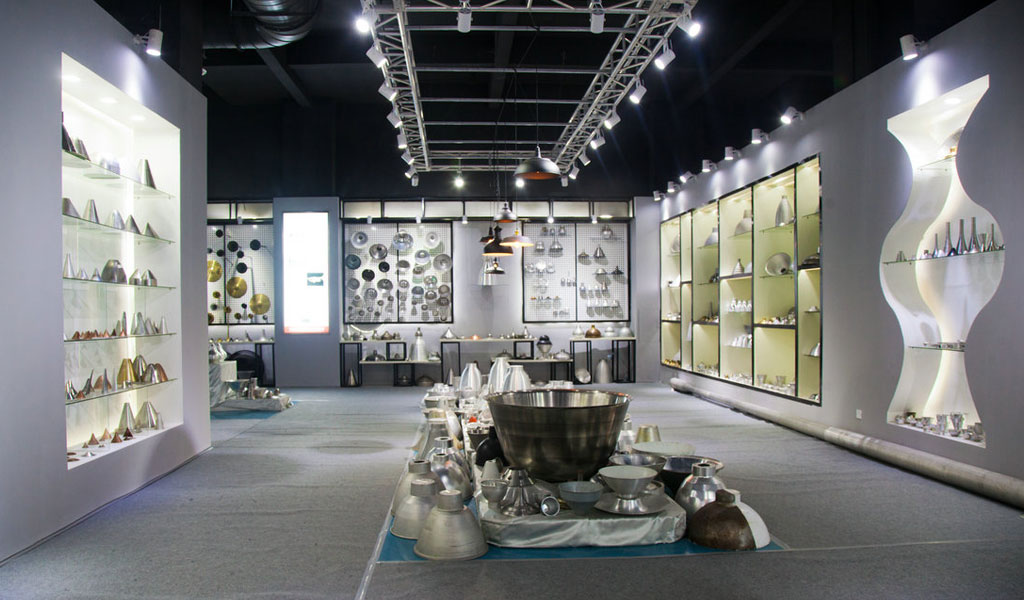
At BE-CU China Metal Spinning company, we make the most of our equipment while monitoring signs of excess wear and stress. In addition, we look into newer, modern equipment and invest in those that can support or increase our manufacturing capabilities. Our team is very mindful of our machines and tools, so we also routinely maintain them to ensure they don’t negatively impact your part’s quality and productivity.
Talk to us today about making a rapid prototype with our CNC metal spinning service. Get a direct quote by chatting with us here or request a free project review.
BE-CU China CNC Metal Spinning service include : CNC Metal Spinning,Metal Spinning Die,Laser Cutting, Tank Heads Spinning,Metal Hemispheres Spinning,Metal Cones Spinning,Metal Dish-Shaped Spinning,Metal Trumpet Spinning,Metal Venturi Spinning,Aluminum Spinning Products,Stainless Steel Spinning Products,Copper Spinning Products,Brass Spinning Products,Steel Spinning Product,Metal Spinnin LED Reflector,Metal Spinning Pressure Vessel,