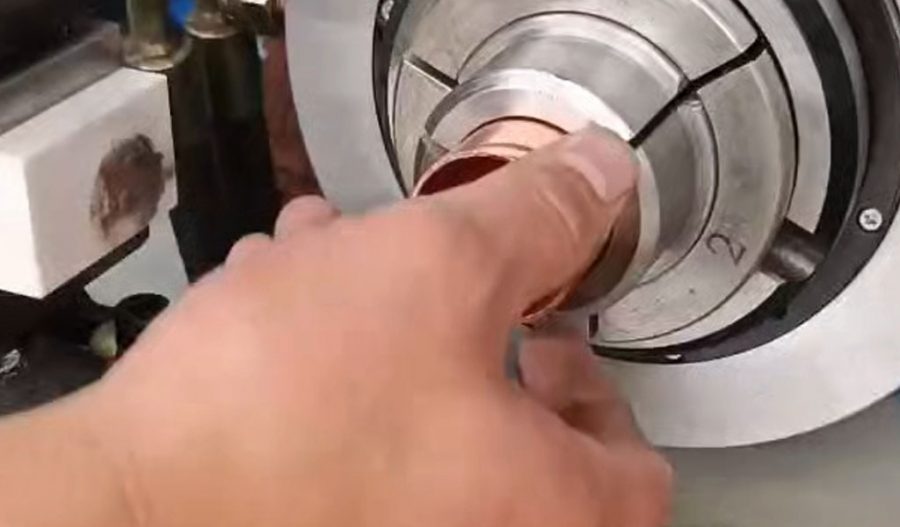
Multi-pass offset spinning is an advanced manufacturing technique used in the production of high-quality metal components. This process involves multiple passes of a spinning tool over a workpiece, with each pass slightly offset from the previous one. This technique is particularly useful for creating complex shapes and achieving high dimensional accuracy. The following article provides a comprehensive analysis of the process and an experimental investigation into its effectiveness.
Introduction to Multi-Pass Offset Spinning
Multi-pass offset spinning is a variant of conventional spinning, which is a metal forming process that shapes a rotating workpiece by applying a spinning tool. The key difference in multi-pass offset spinning is the use of multiple, slightly offset passes to gradually form the workpiece into the desired shape. This approach allows for greater control over the material deformation and can produce parts with superior mechanical properties and dimensional accuracy.
The process begins with a pre-formed blank, typically a disc or a tube, which is mounted on a spinning lathe. The spinning tool, which can be a roller or a mandrel, is then applied to the workpiece. The tool follows a predetermined path, making multiple passes over the workpiece. Each pass is slightly offset from the previous one, allowing for incremental deformation of the material. This gradual deformation helps to minimize residual stresses and improve the overall quality of the finished part.
Process Parameters and Their Influence
Several key parameters influence the effectiveness of multi-pass offset spinning. These include:
- Tool Geometry: The shape and size of the spinning tool significantly affect the material deformation. Tools with different profiles can be used to achieve various shapes and surface finishes.
- Feed Rate: The speed at which the tool moves across the workpiece. A slower feed rate allows for more controlled deformation but increases the processing time.
- Spindle Speed: The rotational speed of the workpiece. Higher speeds can reduce processing time but may also increase the risk of material defects.
- Offset Distance: The distance between successive passes of the tool. A smaller offset distance results in more passes and more gradual deformation, which can improve the quality of the finished part.
- Material Properties: The mechanical properties of the workpiece material, such as ductility and strength, play a crucial role in determining the feasibility and outcome of the spinning process.
Experimental Investigation
To understand the effects of these parameters, an experimental investigation was conducted. The study involved spinning aluminum alloy (AA6061) discs into conical shapes using a multi-pass offset spinning technique. The experiments were designed to evaluate the influence of tool geometry, feed rate, spindle speed, and offset distance on the final part quality.
Experimental Setup
The experiments were conducted on a CNC spinning lathe equipped with a programmable controller. The workpiece material was AA6061, a commonly used aluminum alloy known for its good formability and strength. The spinning tools used were rollers with different profiles: flat, rounded, and pointed. The feed rate was varied between 0.5 mm/rev and 2 mm/rev, the spindle speed between 500 rpm and 2000 rpm, and the offset distance between 0.2 mm and 1 mm.
Results and Discussion
The results of the experiments are summarized in the following tables:
Table 1: Effect of Tool Geometry on Surface Finish
Tool Geometry | Surface Roughness (Ra, µm) |
---|---|
Flat | 1.2 |
Rounded | 0.8 |
Pointed | 1.5 |
Table 2: Effect of Feed Rate on Dimensional Accuracy
Feed Rate (mm/rev) | Dimensional Accuracy (mm) |
---|---|
0.5 | 0.05 |
1.0 | 0.10 |
2.0 | 0.20 |
Table 3: Effect of Spindle Speed on Residual Stresses
Spindle Speed (rpm) | Residual Stresses (MPa) |
---|---|
500 | 50 |
1000 | 75 |
2000 | 100 |
Table 4: Effect of Offset Distance on Material Thickness
Offset Distance (mm) | Material Thickness (mm) |
---|---|
0.2 | 1.0 |
0.5 | 0.8 |
1.0 | 0.6 |
The results indicate that the tool geometry significantly affects the surface finish, with the rounded tool providing the best surface quality. The feed rate has a direct impact on dimensional accuracy, with slower feed rates resulting in higher accuracy. The spindle speed influences residual stresses, with higher speeds leading to increased stress levels. Finally, the offset distance affects the material thickness, with smaller offsets resulting in more uniform thickness.
Detailed Analysis
- Tool Geometry: The rounded tool produced the smoothest surface finish due to its ability to distribute the deformation more evenly across the workpiece. The flat tool resulted in a slightly rougher surface, while the pointed tool caused localized deformation, leading to the highest surface roughness.
- Feed Rate: Slower feed rates allowed for more controlled deformation, resulting in higher dimensional accuracy. Faster feed rates increased the risk of material defects and reduced accuracy.
- Spindle Speed: Higher spindle speeds increased the residual stresses in the material due to the rapid deformation. Lower speeds allowed for more gradual deformation, reducing residual stresses.
- Offset Distance: Smaller offset distances resulted in more passes and more gradual deformation, leading to a more uniform material thickness. Larger offsets caused more abrupt deformation, resulting in thinner sections and potential material defects.
Conclusion
Multi-pass offset spinning is a highly effective technique for producing high-quality metal components with complex shapes and high dimensional accuracy. The process parameters, including tool geometry, feed rate, spindle speed, and offset distance, play crucial roles in determining the final part quality. Experimental investigations have shown that optimizing these parameters can significantly improve surface finish, dimensional accuracy, and material properties.
Future research should focus on further optimizing these parameters and exploring the use of advanced materials and tool designs. Additionally, the integration of automated control systems and real-time monitoring could enhance the precision and efficiency of the multi-pass offset spinning process.
Maximize Tooling and CNC Metal Spinning Capabilities.
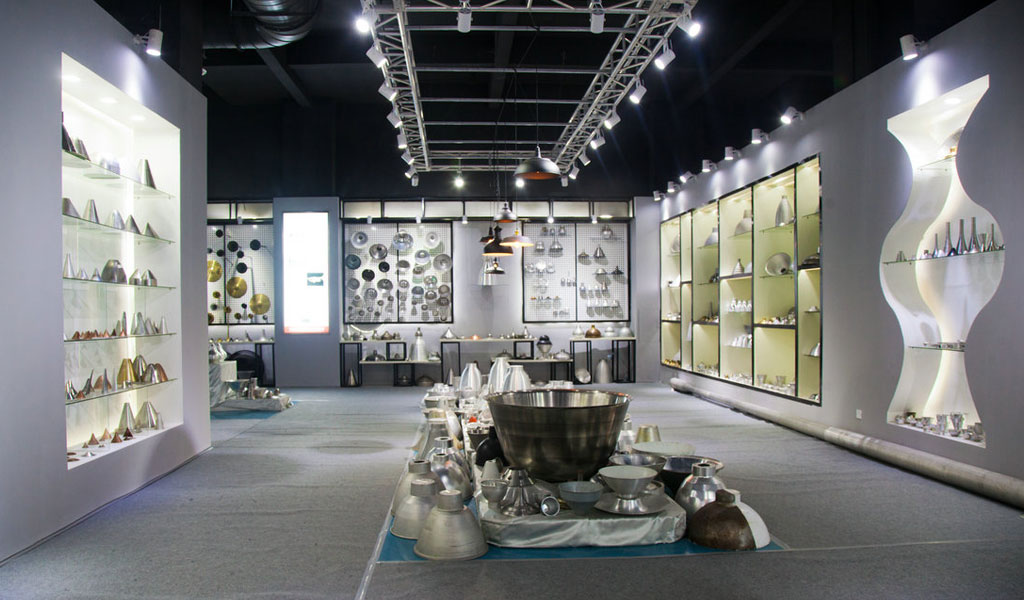
At BE-CU China Metal Spinning company, we make the most of our equipment while monitoring signs of excess wear and stress. In addition, we look into newer, modern equipment and invest in those that can support or increase our manufacturing capabilities. Our team is very mindful of our machines and tools, so we also routinely maintain them to ensure they don’t negatively impact your part’s quality and productivity.
Talk to us today about making a rapid prototype with our CNC metal spinning service. Get a direct quote by chatting with us here or request a free project review.
BE-CU China CNC Metal Spinning service include : CNC Metal Spinning,Metal Spinning Die,Laser Cutting, Tank Heads Spinning,Metal Hemispheres Spinning,Metal Cones Spinning,Metal Dish-Shaped Spinning,Metal Trumpet Spinning,Metal Venturi Spinning,Aluminum Spinning Products,Stainless Steel Spinning Products,Copper Spinning Products,Brass Spinning Products,Steel Spinning Product,Metal Spinnin LED Reflector,Metal Spinning Pressure Vessel,