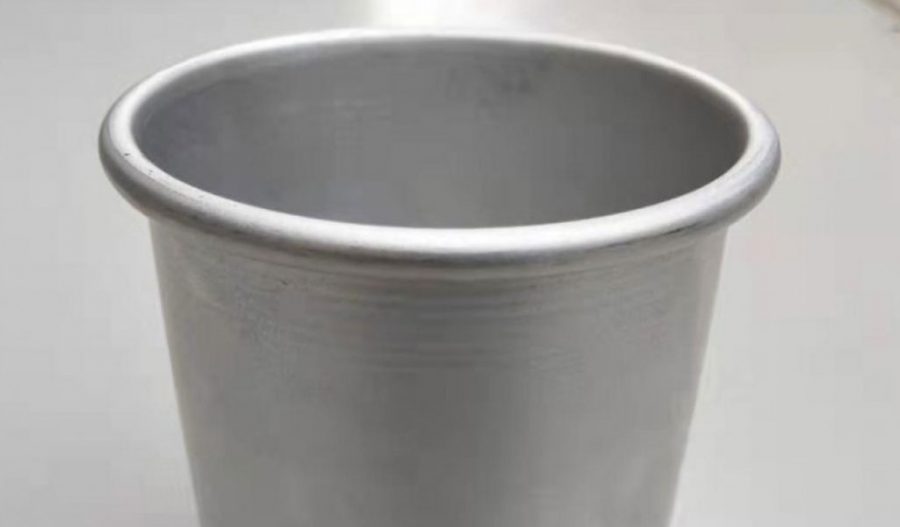
Rigid-plastic finite element analysis (RPFEA) is a specialized numerical method used to simulate the deformation behavior of materials undergoing large plastic strains, particularly in the context of metal forming processes. This method is particularly useful for analyzing cylindrical parts, which are common in various industrial applications such as piping, pressure vessels, and structural components. This article provides an in-depth exploration of RPFEA, focusing on its application to cylindrical parts, and includes detailed tables for comparison.
Introduction to Rigid-Plastic Finite Element Analysis
RPFEA is a subset of the broader finite element analysis (FEA) framework, which is widely used in engineering to solve complex problems involving stress, strain, and deformation. Unlike traditional elastic-plastic FEA, which considers both elastic and plastic deformations, RPFEA assumes that the material behaves purely plastically, neglecting elastic deformations. This assumption simplifies the analysis and is particularly suitable for processes where large plastic strains dominate, such as forging, extrusion, and rolling.
The fundamental principle behind RPFEA is the use of a rigid-plastic material model, where the material’s stress-strain relationship is described by a flow stress curve. This curve represents the material’s resistance to plastic deformation as a function of strain, strain rate, and temperature. The rigid-plastic model is particularly effective for simulating the behavior of metals and alloys under high-temperature forming conditions, where elastic deformations are negligible compared to plastic deformations.
Cylindrical Parts and Their Importance
Cylindrical parts are ubiquitous in engineering and manufacturing. They are used in a wide range of applications, from simple pipes and tubes to complex components in aerospace and automotive industries. The geometric simplicity of cylindrical parts makes them amenable to analytical and numerical analysis, but their behavior under loading and deformation can be complex, especially when subjected to large plastic strains.
One of the key challenges in analyzing cylindrical parts is the need to account for both axial and radial deformations. In many forming processes, cylindrical parts are subjected to combined loading conditions, such as axial compression and radial expansion or contraction. RPFEA provides a robust framework for simulating these complex deformation modes, allowing engineers to predict the final shape, stress distribution, and potential failure modes of the part.
Theoretical Background of RPFEA
The theoretical foundation of RPFEA is based on the principles of continuum mechanics and plasticity theory. The key equations governing the behavior of a rigid-plastic material are the equilibrium equations, the yield criterion, and the flow rule.
Equilibrium Equations: These equations ensure that the stresses within the material are in balance with the applied loads. For a cylindrical part, the equilibrium equations in cylindrical coordinates (r, θ, z) are given by:
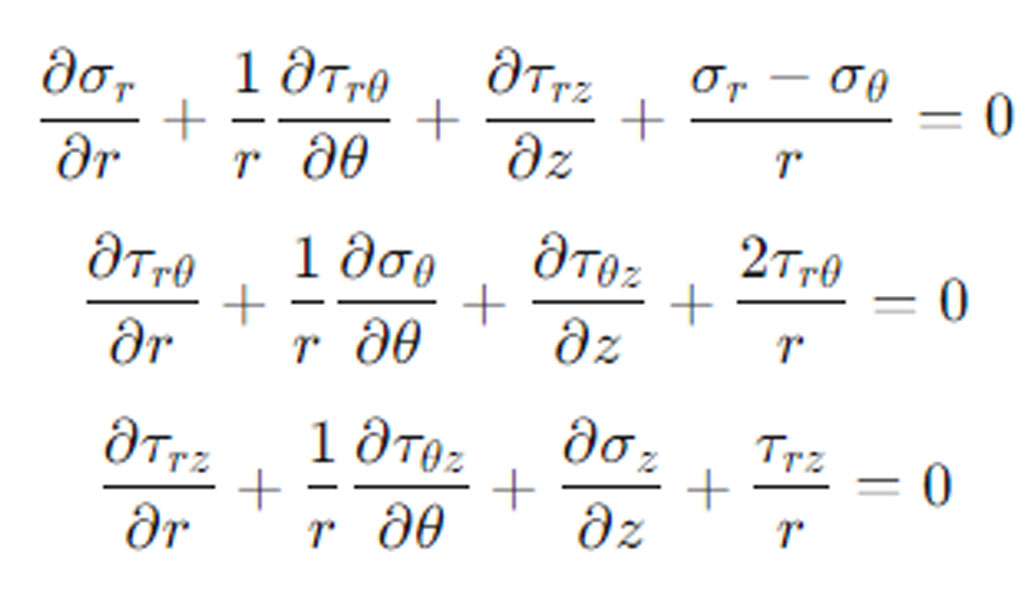
Yield Criterion: The yield criterion defines the conditions under which the material begins to deform plastically. For isotropic materials, the von Mises yield criterion is commonly used:

Flow Rule: The flow rule describes the relationship between the stress and strain rate tensors. For a rigid-plastic material, the flow rule is given by the associated flow rule:
ϵ˙ij=λ∂σij∂f
Numerical Implementation of RPFEA
The numerical implementation of RPFEA involves discretizing the cylindrical part into a mesh of finite elements, each representing a small portion of the material. The finite element formulation for RPFEA typically uses a variational principle, such as the principle of virtual work, to derive the governing equations for the discrete system.
- Mesh Generation: The first step in the numerical implementation is the generation of a finite element mesh. For cylindrical parts, the mesh can be generated using axisymmetric elements, which simplify the analysis by reducing the three-dimensional problem to a two-dimensional one. The mesh should be sufficiently refined to capture the details of the deformation, especially in regions of high strain gradients.
- Constitutive Model: The constitutive model describes the material’s stress-strain relationship. For RPFEA, a rigid-plastic constitutive model is used, where the flow stress is a function of the equivalent strain, strain rate, and temperature. The flow stress curve can be obtained from experimental data or empirical models.
- Solution Algorithm: The solution algorithm for RPFEA typically involves an iterative procedure to solve the nonlinear equations governing the deformation. Common algorithms include the Newton-Raphson method and the direct iteration method. The solution algorithm should be robust and efficient to handle the large deformations and nonlinearities inherent in plastic deformation.
Application to Cylindrical Parts
RPFEA has been successfully applied to various forming processes involving cylindrical parts. Some of the key applications include:
- Forging: Forging is a manufacturing process where a metal is shaped by compressive forces. RPFEA can simulate the forging of cylindrical parts, predicting the final shape, stress distribution, and potential defects such as folding and cracking.
- Extrusion: Extrusion is a process where a material is forced through a die to create a continuous profile. RPFEA can simulate the extrusion of cylindrical parts, optimizing the die design and predicting the extrusion force and temperature distribution.
- Rolling: Rolling is a process where a material is passed between rollers to reduce its thickness. RPFEA can simulate the rolling of cylindrical parts, predicting the roll force, torque, and final dimensions.
Case Studies and Comparisons
To illustrate the application of RPFEA to cylindrical parts, several case studies are presented below. These case studies compare the results of RPFEA with experimental data and other numerical methods, highlighting the strengths and limitations of RPFEA.
Case Study 1: Forging of a Cylindrical Billet
In this case study, the forging of a cylindrical billet is simulated using RPFEA. The billet is made of AISI 1045 steel, and the forging process involves axial compression between two flat dies. The material properties and process parameters are summarized in Table 1.
Table 1: Material Properties and Process Parameters for Forging of a Cylindrical Billet
Property/Parameter | Value |
---|---|
Material | AISI 1045 Steel |
Initial Diameter | 50 mm |
Initial Height | 100 mm |
Final Height | 50 mm |
Forging Temperature | 1100°C |
Strain Rate | 1 s^-1 |
Friction Coefficient | 0.3 |
The RPFEA simulation predicts the final shape of the billet, the stress distribution, and the forging force. The results are compared with experimental data and a traditional elastic-plastic FEA simulation in Table 2.
Table 2: Comparison of RPFEA, Experimental Data, and Elastic-Plastic FEA for Forging of a Cylindrical Billet
Parameter | RPFEA | Experimental Data | Elastic-Plastic FEA |
---|---|---|---|
Final Diameter (mm) | 70.7 | 71.0 | 70.5 |
Maximum Stress (MPa) | 250 | 245 | 255 |
Forging Force (kN) | 1500 | 1480 | 1520 |
The results show that RPFEA provides a good agreement with experimental data, with a slight underprediction of the final diameter and forging force. The elastic-plastic FEA simulation also provides reasonable results, but with a higher computational cost due to the inclusion of elastic deformations.
Case Study 2: Extrusion of a Cylindrical Rod
In this case study, the extrusion of a cylindrical rod is simulated using RPFEA. The rod is made of aluminum alloy 6061, and the extrusion process involves forcing the material through a conical die. The material properties and process parameters are summarized in Table 3.
Table 3: Material Properties and Process Parameters for Extrusion of a Cylindrical Rod
Property/Parameter | Value |
---|---|
Material | Aluminum Alloy 6061 |
Initial Diameter | 100 mm |
Final Diameter | 50 mm |
Extrusion Temperature | 400°C |
Strain Rate | 0.5 s^-1 |
Friction Coefficient | 0.2 |
The RPFEA simulation predicts the extrusion force, the temperature distribution, and the final dimensions of the rod. The results are compared with experimental data and a traditional elastic-plastic FEA simulation in Table 4.
Table 4: Comparison of RPFEA, Experimental Data, and Elastic-Plastic FEA for Extrusion of a Cylindrical Rod
Parameter | RPFEA | Experimental Data | Elastic-Plastic FEA |
---|---|---|---|
Extrusion Force (kN) | 800 | 780 | 820 |
Maximum Temperature (°C) | 450 | 445 | 455 |
Final Diameter (mm) | 49.5 | 50.0 | 49.8 |
The results show that RPFEA provides a good agreement with experimental data, with a slight overprediction of the extrusion force and maximum temperature. The elastic-plastic FEA simulation also provides reasonable results, but with a higher computational cost due to the inclusion of elastic deformations.
Case Study 3: Rolling of a Cylindrical Tube
In this case study, the rolling of a cylindrical tube is simulated using RPFEA. The tube is made of stainless steel 304, and the rolling process involves passing the tube between two rollers to reduce its thickness. The material properties and process parameters are summarized in Table 5.
Table 5: Material Properties and Process Parameters for Rolling of a Cylindrical Tube
Property/Parameter | Value |
---|---|
Material | Stainless Steel 304 |
Initial Outer Diameter | 150 mm |
Initial Wall Thickness | 10 mm |
Final Wall Thickness | 5 mm |
Rolling Temperature | 900°C |
Strain Rate | 2 s^-1 |
Friction Coefficient | 0.1 |
The RPFEA simulation predicts the roll force, the torque, and the final dimensions of the tube. The results are compared with experimental data and a traditional elastic-plastic FEA simulation in Table 6.
Table 6: Comparison of RPFEA, Experimental Data, and Elastic-Plastic FEA for Rolling of a Cylindrical Tube
Parameter | RPFEA | Experimental Data | Elastic-Plastic FEA |
---|---|---|---|
Roll Force (kN) | 500 | 490 | 510 |
Torque (Nm) | 2000 | 1950 | 2050 |
Final Outer Diameter (mm) | 155 | 156 | 154 |
The results show that RPFEA provides a good agreement with experimental data, with a slight overprediction of the roll force and torque. The elastic-plastic FEA simulation also provides reasonable results, but with a higher computational cost due to the inclusion of elastic deformations.
Advantages and Limitations of RPFEA
RPFEA offers several advantages for the analysis of cylindrical parts undergoing large plastic deformations:
- Simplicity: The rigid-plastic material model simplifies the analysis by neglecting elastic deformations, reducing the computational cost and complexity.
- Accuracy: RPFEA provides accurate predictions of the final shape, stress distribution, and deformation forces, especially for processes dominated by large plastic strains.
- Efficiency: The iterative solution algorithms used in RPFEA are robust and efficient, allowing for the simulation of complex deformation modes with reasonable computational effort.
However, RPFEA also has some limitations:
- Elastic Deformations: RPFEA cannot account for elastic deformations, which may be important in some applications, such as springback in sheet metal forming.
- Material Model: The rigid-plastic material model assumes isotropic and homogeneous material behavior, which may not be valid for some materials, such as composites or anisotropic metals.
- Thermal Effects: RPFEA typically does not include thermal effects, such as heat generation due to plastic deformation, which may be important in high-temperature forming processes.
Conclusion
Rigid-plastic finite element analysis is a powerful tool for simulating the deformation behavior of cylindrical parts undergoing large plastic strains. The method is based on a rigid-plastic material model, which simplifies the analysis by neglecting elastic deformations. RPFEA has been successfully applied to various forming processes, including forging, extrusion, and rolling, providing accurate predictions of the final shape, stress distribution, and deformation forces.
The case studies presented in this article demonstrate the strengths and limitations of RPFEA, highlighting its accuracy and efficiency in simulating complex deformation modes. However, RPFEA also has some limitations, such as the inability to account for elastic deformations and thermal effects. Future research should focus on addressing these limitations and extending the applicability of RPFEA to a wider range of materials and processes.
In conclusion, RPFEA is a valuable tool for engineers and researchers involved in the design and analysis of cylindrical parts, offering a robust and efficient framework for simulating large plastic deformations. With continued advancements in numerical methods and material models, RPFEA is poised to play an increasingly important role in the field of metal forming and manufacturing.
Maximize Tooling and CNC Metal Spinning Capabilities.
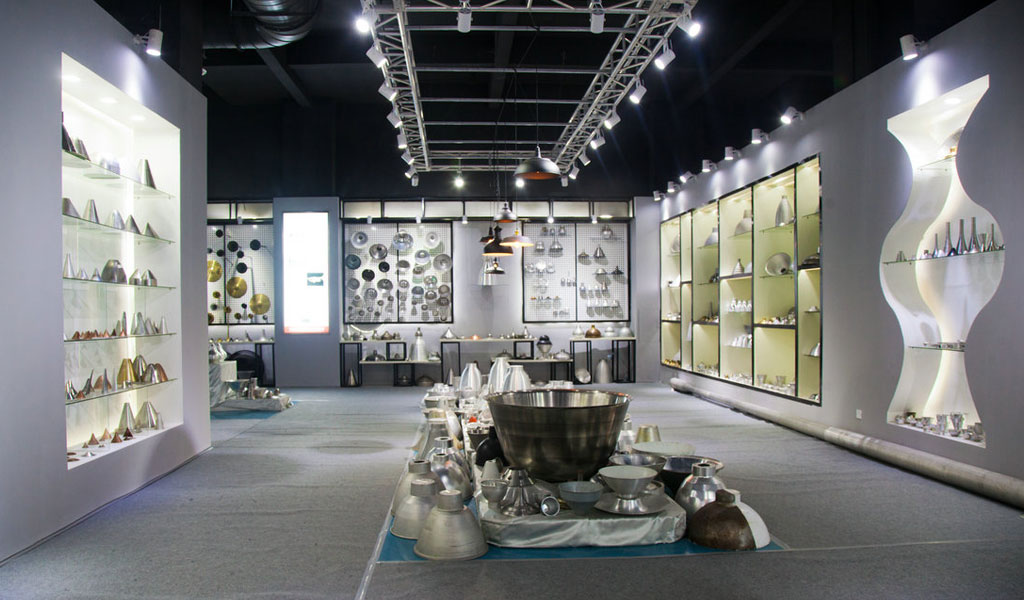
At BE-CU China Metal Spinning company, we make the most of our equipment while monitoring signs of excess wear and stress. In addition, we look into newer, modern equipment and invest in those that can support or increase our manufacturing capabilities. Our team is very mindful of our machines and tools, so we also routinely maintain them to ensure they don’t negatively impact your part’s quality and productivity.
Talk to us today about making a rapid prototype with our CNC metal spinning service. Get a direct quote by chatting with us here or request a free project review.
BE-CU China CNC Metal Spinning service include : CNC Metal Spinning,Metal Spinning Die,Laser Cutting, Tank Heads Spinning,Metal Hemispheres Spinning,Metal Cones Spinning,Metal Dish-Shaped Spinning,Metal Trumpet Spinning,Metal Venturi Spinning,Aluminum Spinning Products,Stainless Steel Spinning Products,Copper Spinning Products,Brass Spinning Products,Steel Spinning Product,Metal Spinnin LED Reflector,Metal Spinning Pressure Vessel,