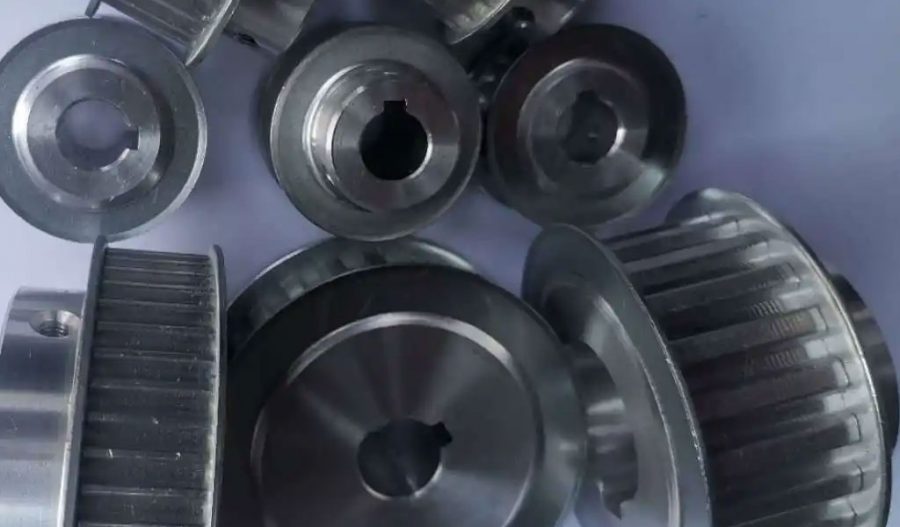
The roller spinning process is a critical manufacturing technique used to produce thin-walled, axisymmetric components from sheet metal. This process is particularly advantageous for materials like stainless steel 1Cr18Ni9Ti, which is known for its excellent corrosion resistance, high strength, and good formability. This article delves into the intricacies of the roller spinning process, focusing on the material properties of 1Cr18Ni9Ti, the process parameters, and the resulting mechanical and metallurgical characteristics.
Introduction to Stainless Steel 1Cr18Ni9Ti
Stainless steel 1Cr18Ni9Ti, also known as AISI 321, is an austenitic stainless steel that contains chromium, nickel, and titanium. The addition of titanium helps to stabilize the material against intergranular corrosion, making it suitable for high-temperature applications. The chemical composition of 1Cr18Ni9Ti is typically as follows:
Element | Weight Percentage (%) |
---|---|
Cr | 17.0 – 19.0 |
Ni | 8.0 – 10.5 |
Ti | 5 x %C (min 0.15%) |
C | 0.08 (max) |
Mn | 2.0 (max) |
Si | 1.0 (max) |
P | 0.045 (max) |
S | 0.030 (max) |
Fe | Balance |
The mechanical properties of 1Cr18Ni9Ti make it an ideal candidate for roller spinning. Its high ductility and formability allow for significant deformation without fracture, which is essential for achieving the desired thin-walled geometry.
Roller Spinning Process
The roller spinning process involves the use of a spinning lathe, where a flat sheet metal blank is clamped between a mandrel and a tailstock. The mandrel rotates at high speeds, and a roller tool is applied to the outer surface of the blank, gradually deforming it into the desired shape. The process can be divided into several stages:
- Preparation: The sheet metal blank is cut to the required size and shape. The mandrel is selected based on the final part dimensions and is mounted on the spinning lathe.
- Clamping: The blank is clamped between the mandrel and the tailstock. Proper clamping is crucial to prevent slippage and ensure uniform deformation.
- Initial Forming: The roller tool is applied to the outer surface of the blank, and the mandrel is rotated. The roller tool gradually deforms the blank, reducing its thickness and increasing its diameter.
- Intermediate Forming: As the blank is deformed, the roller tool is adjusted to maintain contact with the blank. The mandrel speed and roller tool pressure are carefully controlled to achieve the desired wall thickness and diameter.
- Final Forming: The final dimensions are achieved by making fine adjustments to the roller tool and mandrel speed. The part is then removed from the lathe and inspected for quality.
Process Parameters
Several key parameters influence the roller spinning process of 1Cr18Ni9Ti:
- Mandrel Speed: The rotational speed of the mandrel affects the deformation rate and the quality of the final part. Higher speeds can lead to better surface finish but may also increase the risk of defects such as wrinkling or tearing.
- Roller Tool Pressure: The pressure applied by the roller tool determines the rate of deformation. Too much pressure can cause excessive thinning or fracture, while too little pressure may result in insufficient deformation.
- Feed Rate: The rate at which the roller tool moves along the blank affects the uniformity of deformation. A consistent feed rate is essential for achieving uniform wall thickness.
- Lubrication: Proper lubrication is crucial to reduce friction between the roller tool and the blank, preventing galling and improving the surface finish.
- Temperature: The process temperature can affect the formability of the material. Elevated temperatures can enhance ductility but may also lead to microstructural changes.
Mechanical and Metallurgical Characteristics
The roller spinning process significantly alters the mechanical and metallurgical properties of 1Cr18Ni9Ti. The primary changes include:
- Grain Structure: The deformation induced by roller spinning can lead to grain refinement, which enhances the material’s strength and toughness. The grain structure can be analyzed using techniques such as optical microscopy and electron backscatter diffraction (EBSD).
- Residual Stress: The spinning process introduces residual stresses in the material, which can affect its performance. Residual stresses can be measured using X-ray diffraction or hole-drilling methods.
- Hardness: The hardness of the material may increase due to work hardening. This can be quantified using Vickers or Rockwell hardness tests.
- Corrosion Resistance: The deformation and potential heat treatment during spinning can affect the material’s corrosion resistance. Electrochemical tests, such as potentiodynamic polarization, can be used to evaluate corrosion resistance.
Comparative Analysis
To understand the effectiveness of the roller spinning process, it is essential to compare it with other forming methods. The following table provides a comparative analysis of roller spinning, deep drawing, and hydroforming for thin-walled stainless steel components:
Parameter | Roller Spinning | Deep Drawing | Hydroforming |
---|---|---|---|
Process Complexity | Moderate | High | High |
Tooling Cost | Low | High | High |
Formability | High | Moderate | High |
Surface Finish | Good | Fair | Excellent |
Wall Thickness Uniformity | High | Moderate | High |
Production Rate | Moderate | High | Moderate |
Material Wastage | Low | Moderate | Low |
Suitability for Complex Shapes | Moderate | High | High |
Case Studies
Several case studies have been conducted to evaluate the roller spinning process for 1Cr18Ni9Ti. One notable study involved the production of thin-walled cylinders for aerospace applications. The study found that roller spinning could achieve wall thicknesses as low as 0.5 mm with excellent dimensional accuracy and surface finish. The mechanical properties of the spun cylinders were comparable to those of deep-drawn components, with improved corrosion resistance due to the stabilizing effect of titanium.
Another study focused on the optimization of process parameters for roller spinning of 1Cr18Ni9Ti. The researchers used finite element analysis (FEA) to simulate the spinning process and identify optimal mandrel speeds, roller tool pressures, and feed rates. The results showed that careful control of these parameters could minimize defects such as wrinkling and tearing, leading to high-quality parts with uniform wall thickness.
Conclusion
The roller spinning process is a highly effective method for producing thin-walled stainless steel components, particularly for materials like 1Cr18Ni9Ti. The process offers several advantages, including low tooling costs, high formability, and excellent surface finish. By carefully controlling process parameters such as mandrel speed, roller tool pressure, and feed rate, it is possible to achieve high-quality parts with uniform wall thickness and enhanced mechanical properties.
Further research is needed to optimize the roller spinning process for different applications and to explore the potential for combining roller spinning with other forming techniques. The ongoing development of advanced simulation tools and material characterization techniques will continue to enhance our understanding of the roller spinning process and its applications in various industries.
Maximize Tooling and CNC Metal Spinning Capabilities.
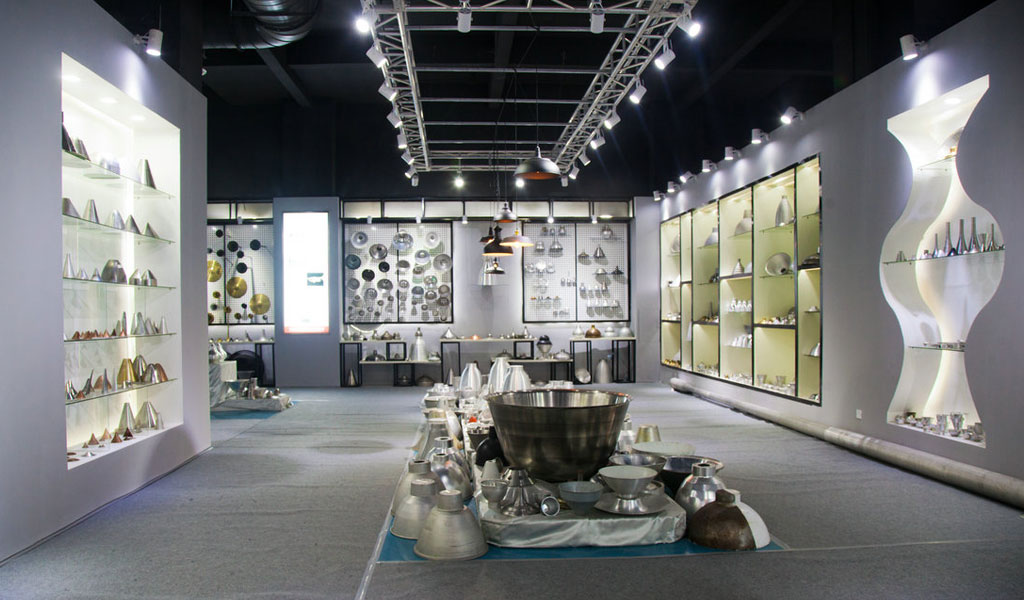
At BE-CU China Metal Spinning company, we make the most of our equipment while monitoring signs of excess wear and stress. In addition, we look into newer, modern equipment and invest in those that can support or increase our manufacturing capabilities. Our team is very mindful of our machines and tools, so we also routinely maintain them to ensure they don’t negatively impact your part’s quality and productivity.
Talk to us today about making a rapid prototype with our CNC metal spinning service. Get a direct quote by chatting with us here or request a free project review.
BE-CU China CNC Metal Spinning service include : CNC Metal Spinning,Metal Spinning Die,Laser Cutting, Tank Heads Spinning,Metal Hemispheres Spinning,Metal Cones Spinning,Metal Dish-Shaped Spinning,Metal Trumpet Spinning,Metal Venturi Spinning,Aluminum Spinning Products,Stainless Steel Spinning Products,Copper Spinning Products,Brass Spinning Products,Steel Spinning Product,Metal Spinnin LED Reflector,Metal Spinning Pressure Vessel,