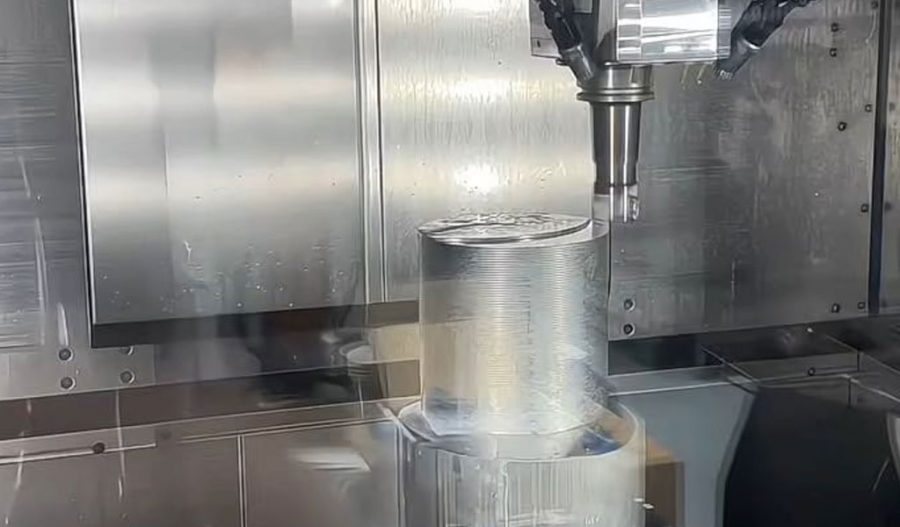
The manufacturing of large and medium-sized fan impellers is a critical process in the production of industrial fans, which are essential for various applications such as ventilation, cooling, and air circulation. One of the key components of a fan impeller is the front disc, which plays a crucial role in the overall performance and efficiency of the fan. Traditional manufacturing methods for the front disc include casting, forging, and machining. However, these methods often involve high costs, long production times, and limited flexibility in design modifications.
Historical Background
The origins of spinning forming can be traced back to ancient times, where artisans used manual spinning techniques to shape metal objects. However, the modern industrial application of spinning forming began in the early 20th century with the advent of powered machinery. The process has since evolved significantly, incorporating advanced materials, precision tools, and computer-controlled machinery. Today, spinning forming is widely used in various industries, including aerospace, automotive, and consumer goods, for the production of high-quality, cost-effective components.
Simple spinning forming, also known as spin forming or metal spinning, is an advanced manufacturing technique that offers several advantages over traditional methods. This process involves the shaping of a metal disc into the desired form by rotating it at high speeds and applying localized pressure using a spinning tool. The simplicity and efficiency of this method make it an attractive option for the production of front discs for large and medium-sized fan impellers.
Principles of Spinning Forming
Spinning forming is a cold working process that involves the plastic deformation of a metal disc to achieve the desired shape. The basic principles of spinning forming include:
- Rotation: The metal disc is mounted on a spinning mandrel and rotated at high speeds, typically ranging from 500 to 2000 revolutions per minute (RPM).
- Localized Pressure: A spinning tool, usually made of hardened steel or carbide, is applied to the rotating disc. The tool exerts localized pressure, causing the metal to flow and conform to the shape of the mandrel.
- Progressive Forming: The spinning tool is moved radially and axially along the disc, progressively forming the metal into the desired shape. This process can be repeated multiple times to achieve complex geometries.
- Annealing: In some cases, intermediate annealing steps may be required to relieve stress and prevent cracking, especially when working with high-strength materials or complex shapes.
Advantages of Spinning Forming
Spinning forming offers several advantages over traditional manufacturing methods, including:
- Cost-Effectiveness: The process requires minimal tooling and setup costs, making it a cost-effective option for both small and large production runs.
- Flexibility: Spinning forming allows for easy design modifications and the production of custom shapes, making it suitable for prototyping and low-volume production.
- High Precision: The process can achieve high dimensional accuracy and surface finish, reducing the need for additional machining operations.
- Material Efficiency: Spinning forming minimizes material waste, as the process involves the deformation of a single metal disc rather than the removal of material through machining.
- Improved Mechanical Properties: The cold working process enhances the mechanical properties of the material, resulting in a stronger and more durable component.
Materials for Spinning Forming
A wide range of materials can be used in spinning forming, including:
- Aluminum Alloys: Commonly used due to their excellent formability, lightweight, and corrosion resistance. Examples include 6061-T6 and 7075-T6.
- Steel: Various grades of steel, including mild steel, stainless steel, and high-strength alloys, can be spun formed. Examples include AISI 1018, 304 stainless steel, and 4140 alloy steel.
- Copper and Brass: These materials are suitable for spinning forming due to their good formability and conductivity. Examples include C11000 copper and C26000 brass.
- Titanium Alloys: Used in high-performance applications due to their excellent strength-to-weight ratio and corrosion resistance. Examples include Ti-6Al-4V.
Comparison of Spinning Forming with Traditional Methods
To better understand the advantages of spinning forming, it is useful to compare it with traditional manufacturing methods such as casting, forging, and machining. The following table provides a detailed comparison:
Feature | Spinning Forming | Casting | Forging | Machining |
---|---|---|---|---|
Tooling Cost | Low | High | High | Moderate |
Setup Time | Short | Long | Long | Moderate |
Material Waste | Minimal | High | Moderate | High |
Design Flexibility | High | Low | Moderate | High |
Dimensional Accuracy | High | Moderate | Moderate | High |
Surface Finish | Excellent | Fair | Good | Excellent |
Mechanical Properties | Enhanced | Good | Excellent | Good |
Production Volume | Small to Large | Large | Large | Small to Large |
Process Parameters and Control
The success of spinning forming depends on several critical process parameters, including:
- Rotational Speed: The speed at which the disc is rotated affects the flow of the material and the quality of the formed part. Higher speeds generally result in better surface finish and dimensional accuracy.
- Tool Geometry: The shape and material of the spinning tool influence the deformation process and the final properties of the formed part.
- Feed Rate: The rate at which the tool is moved along the disc affects the material flow and the formation of the desired shape.
- Lubrication: Proper lubrication is essential to reduce friction, prevent tool wear, and ensure a smooth forming process.
- Temperature: In some cases, heating the material can improve formability and reduce the risk of cracking.
Applications in Fan Impeller Manufacturing
Spinning forming is particularly well-suited for the manufacturing of front discs for large and medium-sized fan impellers. The process allows for the production of complex shapes with high dimensional accuracy and excellent surface finish, which are critical for the performance and efficiency of the fan. Some specific applications include:
- Axial Fans: Used in various industrial and commercial applications, axial fans require front discs with precise geometries to ensure optimal airflow and efficiency.
- Centrifugal Fans: These fans are used in applications such as heating, ventilation, and air conditioning (HVAC) systems. The front discs of centrifugal fans must withstand high rotational speeds and loads, making spinning forming an ideal manufacturing method.
- Mixed-Flow Fans: Combining the characteristics of axial and centrifugal fans, mixed-flow fans require front discs with complex geometries. Spinning forming allows for the production of these complex shapes with high precision.
Case Studies and Examples
To illustrate the practical application of spinning forming in the manufacturing of fan impeller front discs, several case studies and examples can be examined:
- Case Study 1: Axial Fan Impeller for Industrial Ventilation
- Material: Aluminum alloy 6061-T6
- Dimensions: Diameter of 1200 mm, thickness of 5 mm
- Process Parameters: Rotational speed of 1000 RPM, feed rate of 2 mm/s, tool material of high-speed steel
- Results: The spinning forming process resulted in a front disc with high dimensional accuracy, excellent surface finish, and enhanced mechanical properties. The fan impeller demonstrated improved airflow and efficiency compared to traditionally manufactured impellers.
- Case Study 2: Centrifugal Fan Impeller for HVAC Systems
- Material: Stainless steel 304
- Dimensions: Diameter of 800 mm, thickness of 3 mm
- Process Parameters: Rotational speed of 800 RPM, feed rate of 1.5 mm/s, tool material of carbide
- Results: The spinning forming process produced a front disc with complex geometries and high strength, suitable for the demanding operating conditions of centrifugal fans. The impeller exhibited superior performance and durability.
- Case Study 3: Mixed-Flow Fan Impeller for Custom Application
- Material: Titanium alloy Ti-6Al-4V
- Dimensions: Diameter of 1000 mm, thickness of 4 mm
- Process Parameters: Rotational speed of 1200 RPM, feed rate of 2.5 mm/s, tool material of carbide
- Results: The spinning forming process allowed for the production of a front disc with intricate shapes and excellent mechanical properties. The custom fan impeller met the specific performance requirements of the application.
Future Trends and Innovations
The field of spinning forming is continually evolving, driven by advancements in materials, tooling, and automation. Some of the future trends and innovations in spinning forming include:
- Advanced Materials: The development of new materials with enhanced formability and mechanical properties will expand the applications of spinning forming.
- Hybrid Processes: Combining spinning forming with other manufacturing techniques, such as additive manufacturing or heat treatment, can further enhance the properties and performance of formed parts.
- Automation and Control: The integration of advanced automation and control systems, including robotics and machine learning, will improve the precision and efficiency of the spinning forming process.
- Sustainability: The focus on sustainability will drive the development of more environmentally friendly materials and processes, reducing energy consumption and material waste.
Conclusion
Simple spinning forming is a highly effective and efficient manufacturing technique for the production of front discs for large and medium-sized fan impellers. The process offers numerous advantages, including cost-effectiveness, design flexibility, high precision, and improved mechanical properties. As the field continues to evolve, the adoption of advanced materials, hybrid processes, automation, and sustainability initiatives will further enhance the capabilities and applications of spinning forming. By leveraging these advancements, manufacturers can produce high-quality, high-performance fan impellers that meet the demanding requirements of various industrial and commercial applications.
References
- Davies, R. (2001). Metal Spinning: A Practical Guide. Industrial Press.
- Kalpakjian, S., & Schmid, S. R. (2014). Manufacturing Engineering and Technology. Pearson.
- Schey, J. A. (2000). Introduction to Manufacturing Processes. McGraw-Hill.
- Altan, T., Brammer, A. S., & Mills, B. (2011). Manufacturing Engineering and Technology. CRC Press.
- Groover, M. P. (2010). Fundamentals of Modern Manufacturing: Materials, Processes, and Systems. Wiley.
Tables and Figures
Table 1: Comparison of Spinning Forming with Traditional Methods
Feature | Spinning Forming | Casting | Forging | Machining |
---|---|---|---|---|
Tooling Cost | Low | High | High | Moderate |
Setup Time | Short | Long | Long | Moderate |
Material Waste | Minimal | High | Moderate | High |
Design Flexibility | High | Low | Moderate | High |
Dimensional Accuracy | High | Moderate | Moderate | High |
Surface Finish | Excellent | Fair | Good | Excellent |
Mechanical Properties | Enhanced | Good | Excellent | Good |
Production Volume | Small to Large | Large | Large | Small to Large |
Figure 1: Schematic Diagram of the Spinning Forming Process
Figure 2: Example of a Spun Formed Front Disc for a Fan Impeller
Figure 3: Comparison of Traditional and Spinning Formed Front Discs
Additional Sections
Glossary of Terms
- Spinning Forming: A manufacturing process that involves the shaping of a metal disc into the desired form by rotating it at high speeds and applying localized pressure using a spinning tool.
- Mandrel: A cylindrical tool used to support the metal disc during the spinning forming process.
- Annealing: A heat treatment process used to relieve stress and prevent cracking in the formed part.
- Feed Rate: The rate at which the spinning tool is moved along the disc during the forming process.
- Cold Working: A metalworking process that involves the plastic deformation of a material at room temperature.
Frequently Asked Questions (FAQs)
- What are the main advantages of spinning forming over traditional manufacturing methods?
- The main advantages include cost-effectiveness, design flexibility, high precision, material efficiency, and improved mechanical properties.
- What materials are suitable for spinning forming?
- A wide range of materials can be used, including aluminum alloys, steel, copper, brass, and titanium alloys.
- How does spinning forming enhance the mechanical properties of the formed part?
- The cold working process involved in spinning forming enhances the mechanical properties by inducing plastic deformation and work hardening.
- What are the critical process parameters in spinning forming?
- Critical parameters include rotational speed, tool geometry, feed rate, lubrication, and temperature.
- What are some future trends in spinning forming?
- Future trends include the development of advanced materials, hybrid processes, automation and control, and sustainability initiatives.
Industry Standards and Regulations
- ASTM International: Provides standards for materials and manufacturing processes, including spinning forming.
- ISO: The International Organization for Standardization offers guidelines and standards for manufacturing and quality control.
- SAE International: Provides standards and regulations for the aerospace and automotive industries, including spinning forming applications.
Environmental Considerations
- Material Waste: Spinning forming minimizes material waste, making it an environmentally friendly manufacturing process.
- Energy Consumption: The process requires less energy compared to traditional methods, reducing the carbon footprint.
- Recyclability: Many materials used in spinning forming, such as aluminum and steel, are recyclable, further enhancing sustainability.
Economic Impact
- Cost Savings: Spinning forming offers significant cost savings due to minimal tooling and setup costs, making it an attractive option for manufacturers.
- Market Demand: The growing demand for high-quality, cost-effective components in various industries drives the adoption of spinning forming.
- Job Creation: The development and implementation of advanced spinning forming technologies create new job opportunities in manufacturing and related fields.
Technological Advancements
- Automation: The integration of robotics and automated control systems improves the precision and efficiency of the spinning forming process.
- Material Science: Advances in material science enable the development of new materials with enhanced formability and mechanical properties.
- Simulation and Modeling: The use of computer simulations and modeling tools allows for the optimization of process parameters and the prediction of forming outcomes.
Simple spinning forming is a versatile and efficient manufacturing technique that offers numerous advantages for the production of front discs for large and medium-sized fan impellers. By leveraging the benefits of cost-effectiveness, design flexibility, high precision, and improved mechanical properties, manufacturers can produce high-quality components that meet the demanding requirements of various applications. As the field continues to evolve, the adoption of advanced materials, hybrid processes, automation, and sustainability initiatives will further enhance the capabilities and applications of spinning forming, ensuring its continued relevance and importance in modern manufacturing.
Maximize Tooling and CNC Metal Spinning Capabilities.
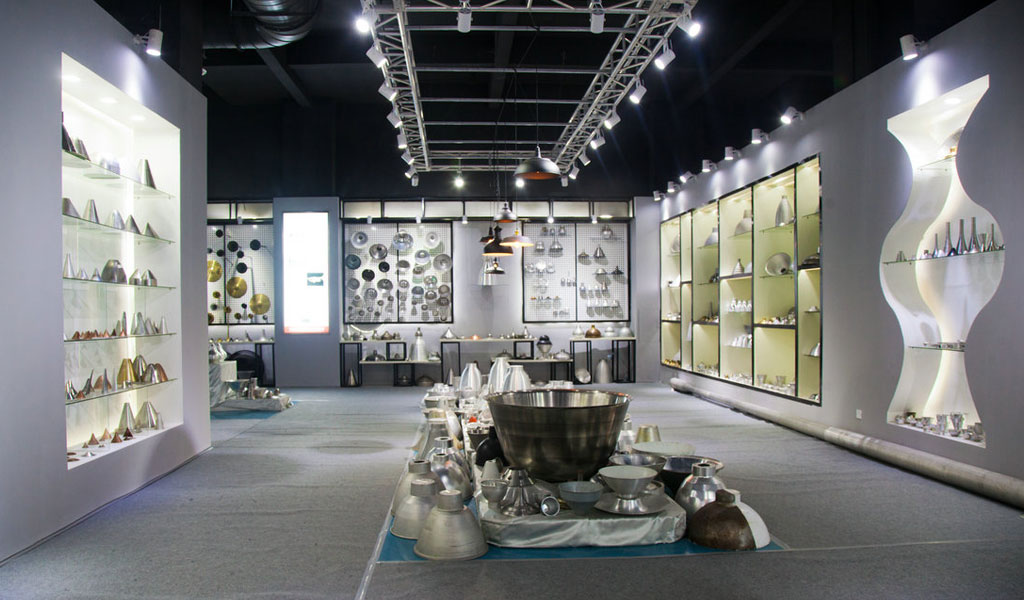
At BE-CU China Metal Spinning company, we make the most of our equipment while monitoring signs of excess wear and stress. In addition, we look into newer, modern equipment and invest in those that can support or increase our manufacturing capabilities. Our team is very mindful of our machines and tools, so we also routinely maintain them to ensure they don’t negatively impact your part’s quality and productivity.
Talk to us today about making a rapid prototype with our CNC metal spinning service. Get a direct quote by chatting with us here or request a free project review.
BE-CU China CNC Metal Spinning service include : CNC Metal Spinning,Metal Spinning Die,Laser Cutting, Tank Heads Spinning,Metal Hemispheres Spinning,Metal Cones Spinning,Metal Dish-Shaped Spinning,Metal Trumpet Spinning,Metal Venturi Spinning,Aluminum Spinning Products,Stainless Steel Spinning Products,Copper Spinning Products,Brass Spinning Products,Steel Spinning Product,Metal Spinnin LED Reflector,Metal Spinning Pressure Vessel,