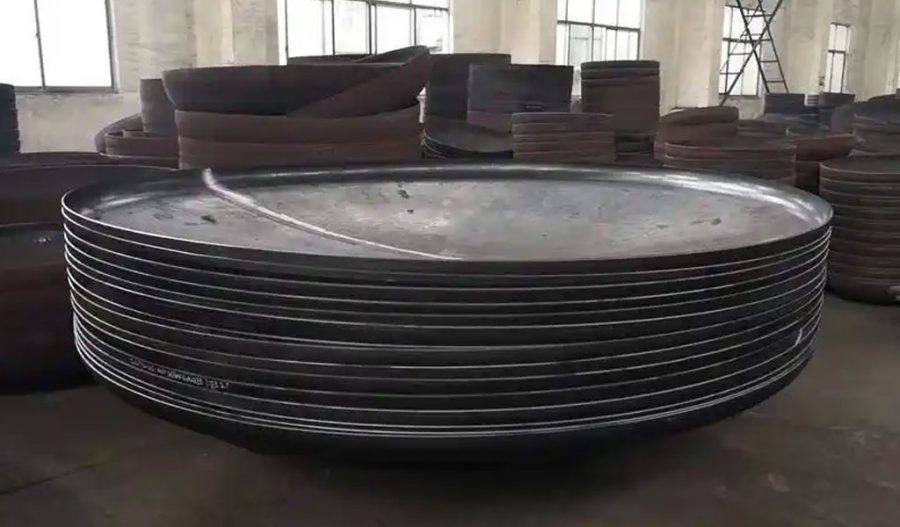
Ball spinning is a critical manufacturing process used to produce thin-walled tubes from stainless steel. This process involves the deformation of a metal blank into a tubular shape through the application of rotational forces. The quality and integrity of the final product are heavily dependent on the parameters and conditions of the spinning process. This article delves into the simulation and defect analysis of ball spinning for stainless steel thin-walled tubes, providing a comprehensive understanding of the process, its challenges, and the methods used to ensure high-quality outcomes.
The Ball Spinning Process
Ball spinning is a form of metal spinning where a rotating mandrel is used to shape a metal blank into a thin-walled tube. The process involves several key steps:
- Preparation of the Blank: The initial metal blank is prepared to the required dimensions and material properties. Stainless steel, known for its corrosion resistance and strength, is a common material choice.
- Mounting the Blank: The blank is mounted onto a rotating mandrel. The mandrel serves as the mold around which the blank will be shaped.
- Application of Force: A spinning tool, often a ball-shaped roller, applies pressure to the rotating blank, gradually deforming it into the desired tubular shape.
- Forming the Tube: As the blank rotates, the spinning tool moves along its length, progressively thinning and elongating the material until the final tube dimensions are achieved.
- Finishing: The formed tube is then removed from the mandrel and subjected to finishing processes such as polishing or heat treatment to enhance its properties.
Simulation of Ball Spinning
Simulation plays a crucial role in understanding and optimizing the ball spinning process. Finite Element Analysis (FEA) is a commonly used method for simulating metal forming processes. FEA involves dividing the material into a finite number of elements and analyzing the behavior of each element under applied forces.
Finite Element Analysis (FEA)
FEA software, such as ABAQUS or ANSYS, can simulate the ball spinning process by modeling the material properties, tool geometry, and process parameters. The simulation provides insights into stress distribution, strain rates, and temperature changes during the spinning process.
Key Parameters in FEA Simulation
- Material Properties: The mechanical properties of stainless steel, including yield strength, tensile strength, and ductility, are essential inputs for the simulation.
- Tool Geometry: The shape and size of the spinning tool significantly influence the deformation process. Simulations can test different tool designs to optimize the process.
- Process Parameters: Rotational speed, feed rate, and applied pressure are critical parameters that affect the final tube quality. Simulations can help identify the optimal settings for these parameters.
Simulation Results
Table 1: Simulation Parameters and Results
Parameter | Value/Range | Simulation Outcome |
---|---|---|
Rotational Speed | 500-1000 RPM | Optimal speed: 750 RPM for minimal defects |
Feed Rate | 0.5-1.5 mm/rev | Optimal feed rate: 1.0 mm/rev for uniform thickness |
Applied Pressure | 100-300 MPa | Optimal pressure: 200 MPa for controlled deformation |
Tool Radius | 5-15 mm | Optimal radius: 10 mm for reduced stress concentration |
Material Yield Strength | 200-300 MPa | Higher yield strength results in fewer defects |
Defect Analysis
Defects in ball-spun stainless steel thin-walled tubes can significantly impact their performance and lifespan. Common defects include cracks, wrinkles, and non-uniform wall thickness. Defect analysis involves identifying the causes of these defects and developing strategies to mitigate them.
Common Defects
- Cracks: Cracks can occur due to excessive stress concentrations during the spinning process. High rotational speeds and applied pressures can lead to crack formation.
- Wrinkles: Wrinkles are caused by compressive stresses that result in material buckling. Insufficient applied pressure or inadequate tool geometry can contribute to wrinkle formation.
- Non-Uniform Wall Thickness: Variations in wall thickness can arise from inconsistent feed rates or tool movements. This defect can compromise the structural integrity of the tube.
Defect Mitigation Strategies
- Optimizing Process Parameters: Simulation results can guide the selection of optimal process parameters to minimize defects. For example, maintaining a rotational speed of 750 RPM and a feed rate of 1.0 mm/rev can reduce the likelihood of cracks and wrinkles.
- Tool Design: Proper tool design is crucial for even stress distribution. A tool radius of 10 mm has been found to reduce stress concentrations effectively.
- Material Selection: Choosing stainless steel with higher yield strength can enhance the material’s resistance to deformation-induced defects.
Case Studies
Table 2: Defect Analysis Case Studies
Case Study | Defect Type | Cause | Mitigation Strategy |
---|---|---|---|
1 | Cracks | High rotational speed (1000 RPM) | Reduce speed to 750 RPM |
2 | Wrinkles | Low applied pressure (100 MPa) | Increase pressure to 200 MPa |
3 | Non-Uniform Thickness | Inconsistent feed rate (0.5-1.5 mm/rev) | Maintain a constant feed rate of 1.0 mm/rev |
4 | Cracks | Sharp tool edges | Use a tool with rounded edges |
5 | Wrinkles | Inadequate tool geometry (5 mm radius) | Use a tool with a 10 mm radius |
Conclusion
The simulation and defect analysis of ball spinning for stainless steel thin-walled tubes are essential for ensuring high-quality and defect-free products. Finite Element Analysis (FEA) provides valuable insights into the deformation process, allowing for the optimization of process parameters and tool design. By understanding the causes of common defects and implementing effective mitigation strategies, manufacturers can produce thin-walled tubes with superior performance and reliability.
Future Directions
Future research in this area could focus on advanced simulation techniques, such as multi-scale modeling, to capture the microstructural changes during the spinning process. Additionally, the integration of machine learning algorithms could enhance the prediction and optimization of process parameters, leading to further improvements in the quality and efficiency of ball spinning for stainless steel thin-walled tubes.
Maximize Tooling and CNC Metal Spinning Capabilities.
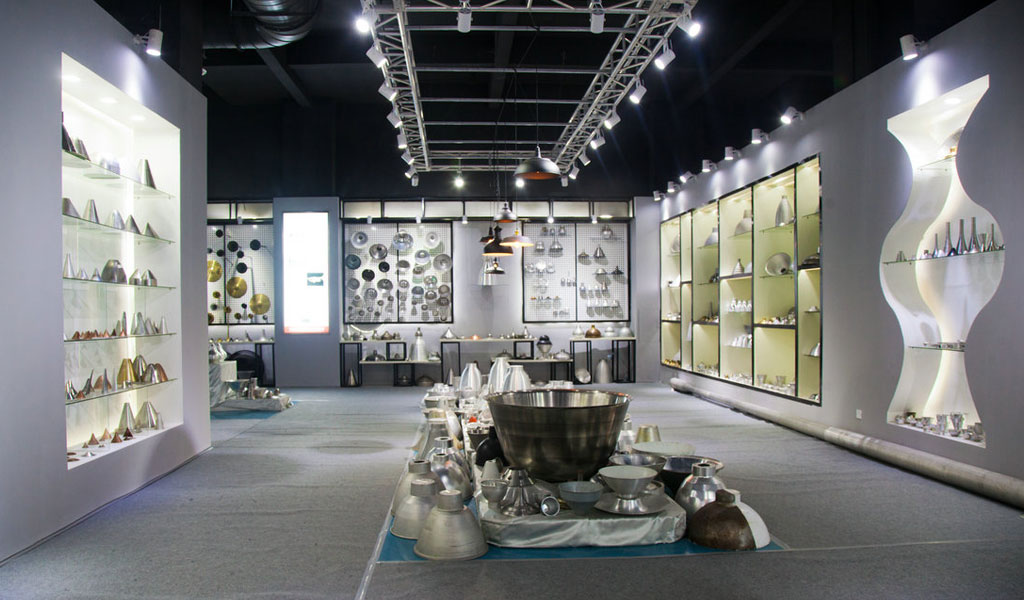
At BE-CU China Metal Spinning company, we make the most of our equipment while monitoring signs of excess wear and stress. In addition, we look into newer, modern equipment and invest in those that can support or increase our manufacturing capabilities. Our team is very mindful of our machines and tools, so we also routinely maintain them to ensure they don’t negatively impact your part’s quality and productivity.
Talk to us today about making a rapid prototype with our CNC metal spinning service. Get a direct quote by chatting with us here or request a free project review.
BE-CU China CNC Metal Spinning service include : CNC Metal Spinning,Metal Spinning Die,Laser Cutting, Tank Heads Spinning,Metal Hemispheres Spinning,Metal Cones Spinning,Metal Dish-Shaped Spinning,Metal Trumpet Spinning,Metal Venturi Spinning,Aluminum Spinning Products,Stainless Steel Spinning Products,Copper Spinning Products,Brass Spinning Products,Steel Spinning Product,Metal Spinnin LED Reflector,Metal Spinning Pressure Vessel,