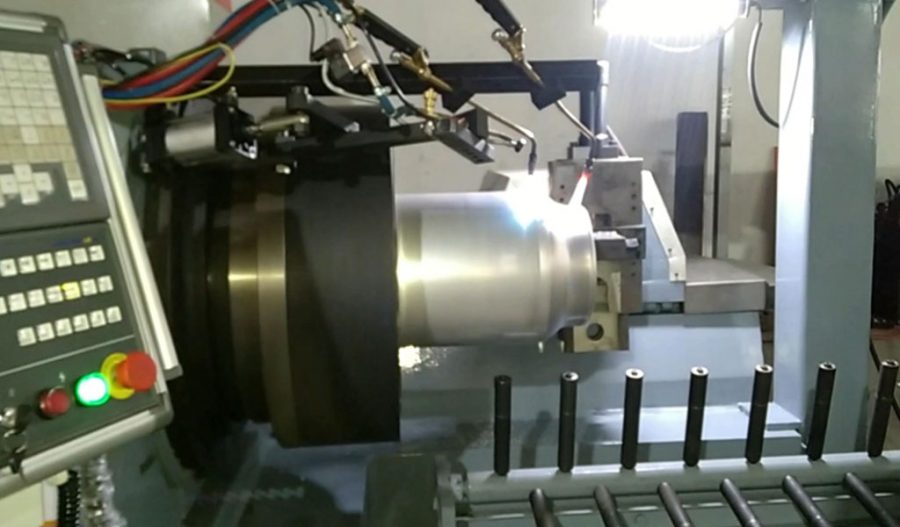
Spin Machining (commonly referred to as metal spinning, spin forming, or spinning) is a metalworking process by which a disc or tube of metal is rotated at high speed and formed into an axially symmetric part. This technique, rooted in ancient craftsmanship and refined through modern engineering, leverages the principles of plastic deformation to shape materials without removing significant amounts of material, distinguishing it from subtractive manufacturing methods like milling or turning. Spinning machining is widely utilized in industries such as aerospace, automotive, and consumer goods manufacturing, producing components ranging from cookware to rocket nose cones. This article explores the history, principles, techniques, materials, equipment, applications, and comparative analyses of spin machining, providing a detailed scientific overview of the process.
Historical Development
The origins of metal spinning can be traced back to ancient civilizations, with evidence of spun metal artifacts found in Egyptian tombs dating to around 1400 BCE. Early practitioners used rudimentary tools—wooden sticks or bones—to shape softened metal over a rotating form, a process likely developed alongside pottery wheel techniques. By the Middle Ages, metal spinning had evolved into a skilled trade in Europe and Asia, with guilds formalizing techniques for producing vessels, armor, and decorative items. The Industrial Revolution marked a turning point, as mechanized lathes and steam power enabled greater precision and scale. In the 20th century, the advent of computer numerical control (CNC) technology revolutionized spin machining, transforming it into a high-precision manufacturing method capable of meeting the exacting demands of modern engineering.
Principles of Spinning Machining
Spin machining operates on the principle of plastic deformation, wherein a metal workpiece—typically a flat disc or preformed tube—is subjected to localized forces while rotating at high speed. The workpiece is clamped against a mandrel (a solid form or mold defining the final shape) and deformed incrementally by a tool, often a roller or spoon-shaped implement. The process relies on the ductility of the material, allowing it to flow and stretch without fracturing. Unlike cutting processes, spin machining preserves the material’s volume, redistributing it into the desired geometry.
The mechanics of spin machining involve several key parameters:
- Rotational Speed: Typically ranging from 300 to 1,500 RPM, depending on material and part size, this governs the centrifugal forces acting on the workpiece.
- Tool Pressure: Applied force, often 1–10 kN, determines the rate of deformation and surface finish.
- Feed Rate: The speed at which the tool advances along the workpiece, usually 0.5–5 mm/revolution, balances efficiency and precision.
- Material Thickness: Initial blanks range from 0.5 mm to over 10 mm, with thinning occurring as the metal is stretched.
The process can be modeled using the theory of plasticity, with stress-strain relationships described by equations such as the von Mises yield criterion: σe=σ12+σ22−σ1σ2\sigma_e = \sqrt{\sigma_1^2 + \sigma_2^2 – \sigma_1\sigma_2}σe=σ12+σ22−σ1σ2
where σe\sigma_eσe is the effective stress, and σ1\sigma_1σ1 and σ2\sigma_2σ2 are principal stresses. Finite element analysis (FEA) is often employed to simulate material flow and predict thinning or wrinkling.
Techniques of Spinning Machining
Spin machining encompasses several distinct techniques, each suited to specific applications:
- Conventional Spinning: The most common form, where the workpiece is deformed over a mandrel in multiple passes. The tool follows a radial or linear path, gradually shaping the metal. This method excels at producing conical, cylindrical, or hemispherical shapes.
- Shear Spinning: A variant that reduces wall thickness intentionally by applying shear forces, often used for lightweight components like aircraft parts. The final thickness tft_ftf is related to the initial thickness tit_iti by the sine law: tf=ti⋅sin(α)t_f = t_i \cdot \sin(\alpha)tf=ti⋅sin(α) where α\alphaα is the angle of the mandrel’s surface relative to the axis.
- Tube Spinning: Involves shaping a tubular preform, either by expanding or reducing its diameter. This is common in producing seamless pipes or pressure vessels.
- Flow Forming: An advanced form of shear spinning, flow forming elongates and thins the material significantly, achieving high strength-to-weight ratios. It is prevalent in military applications, such as missile casings.
Each technique varies in complexity, cost, and material behavior, with CNC automation enhancing repeatability across all methods.
Materials Used in Spinning Machining
The suitability of a material for spin machining depends on its ductility, strength, and work-hardening characteristics. Common materials include:
- Aluminum: Highly ductile and lightweight, ideal for aerospace and consumer goods. Alloys like 6061 or 5052 are frequently spun.
- Steel: Carbon and stainless steels (e.g., 304, 316) offer strength and corrosion resistance, used in industrial and automotive parts.
- Copper and Brass: Valued for their malleability and aesthetic appeal in decorative items.
- Titanium: Challenging due to its strength and low thermal conductivity, but critical for high-performance aerospace components.
Material properties such as elongation percentage (typically 10–40% for spinnable metals) and yield strength dictate process parameters. Table 1 compares key materials:
Material | Yield Strength (MPa) | Elongation (%) | Thermal Conductivity (W/m·K) | Common Applications |
---|---|---|---|---|
Aluminum 6061 | 276 | 17 | 167 | Aircraft panels, cookware |
Stainless 304 | 215 | 40 | 16.2 | Pressure vessels, fittings |
Copper | 70 | 50 | 401 | Decorative bowls, tubing |
Titanium Ti-6Al-4V | 880 | 14 | 6.7 | Rocket cones, medical parts |
Equipment and Tooling
Spin machining requires specialized equipment, primarily a spinning lathe, which differs from conventional lathes by its ability to handle high radial forces. Key components include:
- Spindle: Drives the mandrel and workpiece, with power ratings from 5 kW for small machines to over 50 kW for industrial models.
- Mandrel: A precision-engineered form, often made of hardened steel or wood for prototyping, tailored to the part’s internal geometry.
- Tooling: Rollers (for smooth finishes) or pointed tools (for tight radii), typically made of tool steel or carbide.
- Tailstock: Provides clamping force, adjustable to accommodate varying blank sizes.
CNC spinning lathes integrate servo motors and programmable logic controllers (PLCs), enabling complex tool paths and real-time adjustments. Table 2 compares manual and CNC spinning equipment:
Feature | Manual Spinning | CNC Spinning |
---|---|---|
Precision | ±0.5 mm | ±0.05 mm |
Setup Time | 30–60 min | 10–20 min |
Production Rate | 1–5 parts/hour | 10–50 parts/hour |
Operator Skill | High | Moderate |
Cost (USD) | $10,000–$50,000 | $100,000–$500,000 |
Applications
Spin machining’s versatility makes it indispensable across industries:
- Aerospace: Nose cones, fuel tanks, and engine components benefit from seamless, lightweight designs.
- Automotive: Wheels, exhaust components, and decorative trim leverage cost-effective production.
- Consumer Goods: Cookware, lighting fixtures, and musical instruments (e.g., cymbals) showcase spinning’s aesthetic potential.
- Defense: Flow-formed missile casings and artillery shells require high strength and precision.
The process’s ability to produce thin-walled, complex shapes with minimal waste aligns with sustainability goals, reducing material costs by up to 30% compared to casting or forging.
Advantages and Limitations
Spin machining offers distinct advantages:
- Material Efficiency: Minimal waste compared to machining or stamping.
- Flexibility: Easily adapts to small-batch or custom production.
- Strength: Work hardening during deformation enhances mechanical properties.
However, limitations include:
- Geometry Constraints: Restricted to axially symmetric shapes.
- Material Thickness: Excessive thinning can lead to cracking.
- Initial Cost: High tooling and setup costs for complex parts.
Comparative Analysis
Table 3 compares spin machining with alternative processes:
Process | Material Waste (%) | Tooling Cost (USD) | Production Speed (parts/hour) | Shape Complexity | Strength Gain |
---|---|---|---|---|---|
Spin Machining | 5–10 | 1,000–10,000 | 10–50 | Moderate | High |
CNC Milling | 50–80 | 500–5,000 | 5–20 | High | None |
Forging | 20–30 | 10,000–50,000 | 50–200 | Moderate | High |
Deep Drawing | 15–25 | 5,000–20,000 | 20–100 | Moderate | Moderate |
Advances in spin machining include hybrid processes (e.g., combining spinning with additive manufacturing), improved alloys, and AI-driven process optimization. Research into cryogenic spinning—cooling the workpiece to enhance ductility—promises to expand the range of spinnable materials.
Maximize Tooling and CNC Metal Spinning Capabilities.
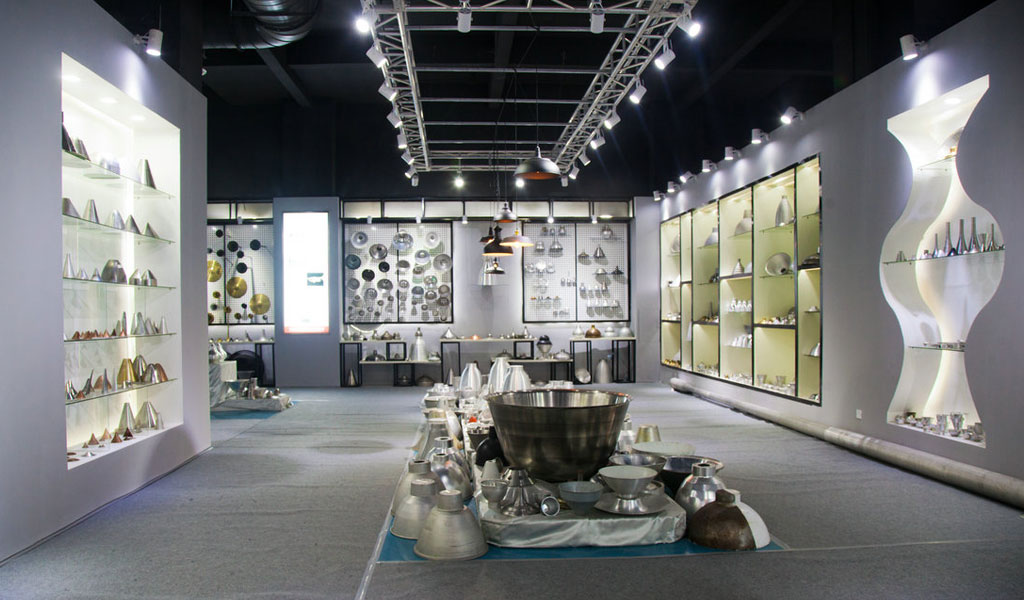
At BE-CU China Metal Spinning company, we make the most of our equipment while monitoring signs of excess wear and stress. In addition, we look into newer, modern equipment and invest in those that can support or increase our manufacturing capabilities. Our team is very mindful of our machines and tools, so we also routinely maintain them to ensure they don’t negatively impact your part’s quality and productivity.
Talk to us today about making a rapid prototype with our CNC metal spinning service. Get a direct quote by chatting with us here or request a free project review.
BE-CU China CNC Metal Spinning service include : CNC Metal Spinning,Metal Spinning Die,Laser Cutting, Tank Heads Spinning,Metal Hemispheres Spinning,Metal Cones Spinning,Metal Dish-Shaped Spinning,Metal Trumpet Spinning,Metal Venturi Spinning,Aluminum Spinning Products,Stainless Steel Spinning Products,Copper Spinning Products,Brass Spinning Products,Steel Spinning Product,Metal Spinnin LED Reflector,Metal Spinning Pressure Vessel,