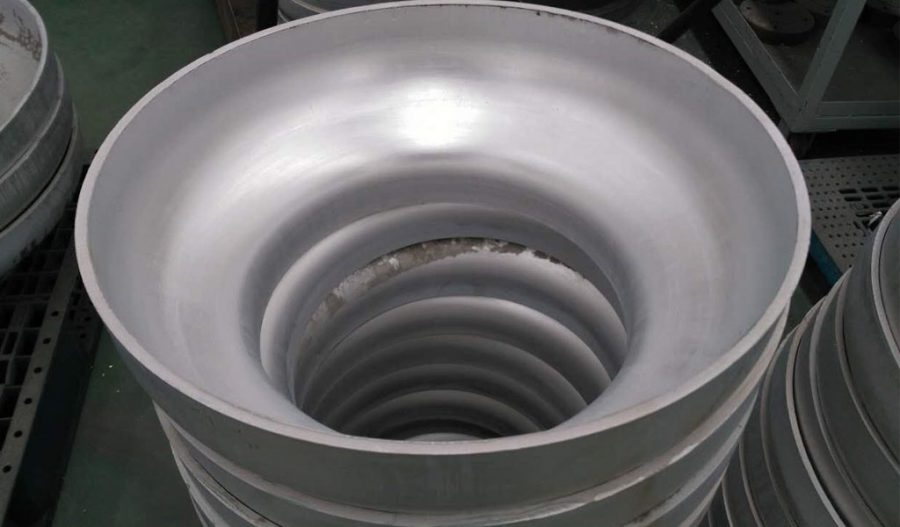
In order to machine 3 mm thick large-size cylindrical Al alloy part with curvilinear generatrix followed by straight- walled section, power-conventional spinning combination method supplemented with heat spinning via horizontal CNC spinning machine was explored through process tests, namely, power spinning of the conical curve section at the small end fol-lowed by multi-pass heat conventional spinning. It has been proved that power-conventional spinning combination method is feasible for the machining of large-size Al alloy cylindrical parts with cone-curved profile. Part blank design, necking amount of conventional spinning and part expanding are primary factors affecting the success of the above spinning processes.
A certain aluminum alloy cylindrical part is a large-sized cylindrical part with a small taper curved generatrix connected to a straight wall section. The diameter of the small end of the part is Φ630 mm. It is divided into three sections along the axis and transitions to a straight cylinder in a parabolic shape. The length is 1200 mm, the height of the straight cylinder section is 330 mm, the diameter of the large end is Φ820 mm, the wall thickness requirement of the part is (3±0.1) mm, and the inner surface profile is ≤1 mm. Its structural dimensions are shown in Figure 1. The part is a hollow rotating body, and it is very difficult to use stretch bulging processing; if the part is formed by tailor welding, there are disadvantages such as long and many welds, difficult to ensure welding quality, and low part strength, so it is not applicable. According to the shape characteristics of the part, the spinning forming process is given priority [1-4]. 1.1 Spinability of part material The part is made of 5A06-0 aluminum alloy, which has high strength and corrosion stability. It has good plasticity in annealing and extrusion state. Its tensile strength is 315 MPa, yield strength is 155 MPa, elongation after fracture (50 mm) is 16%, and annealing temperature is 310-335 ℃. The material has a small yield strength ratio and high elongation, which is suitable for spinning forming [5-7].
Selection of spinning process
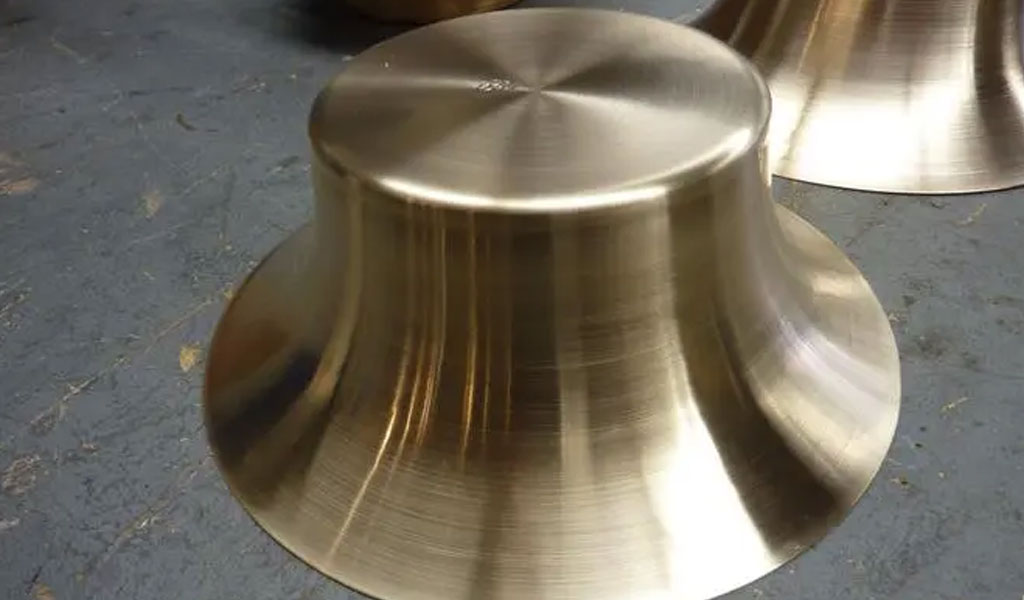
There are two forming schemes to choose from when implementing spinning: one is to spin the curved busbar segment and straight tube segment in sections, and then weld them; the other is to spin the whole part directly. The former has low processing difficulty, but the welding quality affects the pressing effect, the strength is low, many tooling and molds are required, the production cycle is long, and the parts face many quality inspection problems, so it is not suitable for use; the latter has a long straight section of the part, large material deformation, and high difficulty in part forming. There are many uncertain factors in blank design and mold control; but the material utilization rate is high, the tooling is simple, and the production cycle is short. If it can be successful, it is very beneficial to production, so it is preliminarily determined to directly spin the entire part [8]. Spinning is usually divided into two types: strong spinning and general spinning. During the strong spinning process, the wall thickness of the plate follows the sine law to reduce, which is suitable for thick plate parts processing; general spinning generally only changes the shape of the plate, and the wall thickness remains basically unchanged or changes less, which is suitable for thin plate parts processing [9-14]. According to the structural characteristics of the product, the front half of the part is a wall thickness structure such as a conical curved generatrix, which is suitable for shear spinning in strong spinning, and the back half is a straight cylinder, which is also suitable for thinning spinning in strong spinning; but how to deal with the transition between the two is a difficult problem to deal with, and it is also the key to the success of this spinning process. It still needs to be analyzed in detail in actual processing.
Determination of spinning equipment
At present, the spinning processing of large-size cylindrical parts in China is mostly carried out on a horizontal three-wheel cylinder spinning machine, which is conducive to the centering and mold adhesion of the parts. Our factory only has two-wheel horizontal CNC spinning machines available. According to the characteristics of the parts, it is determined to be processed on a CNC1500 CNC spinning machine. The processing range of this machine is suitable, mainly because the tail stroke can reach 2 m, there is enough space to complete the unloading after the parts are processed, and there will be no interference with the left and right bed; in addition, the machine tool has a suitable working tonnage and the equipment is easy to adjust [15-16]. 1.4 Blank design The design and processing of the blank is very important. It is an important link in the spinning process. It is related to whether the part is successfully formed and the quality of the forming, so it should be treated with caution. The initial idea is to machine and anneal the 4.8 mm thick flat blank before spinning, as shown in Figure 2. The turning amount during machining is based on the corresponding points on the part, the value calculated under the sine law and an appropriate amount of margin, so that the material is in a negative deviation state as much as possible during spinning, as shown in Table 2 (partial data). Considering that in actual operation, this scheme is difficult to machine the blank, the inspection is cumbersome, the quality and progress are not easy to guarantee, and the closing amount of the rear straight barrel section during spinning is too large, and it may not be possible to form the process. After many considerations, it was decided to use the blank shown in Figure 3 for spinning. The scheme uses a ring forging to turn out a prefabricated blank with a certain taper, which directly reduces the closing amount of the rear straight barrel section of the part during spinning and reduces the difficulty of spinning.
Die Design
The die is made of heat-resistant steel forged and then turned, with a hardness of HRC45; considering the expansion factor of the cylindrical part, the diameter of the straight part of the large end of the die is slightly smaller than the drawing requirement by 1.5 mm. In order to solve the problem of fixing the part blank, first add a 25 mm straight section to the small end of the part blank, and then leave a corresponding step at the small end of the die. At the same time, the tail top is designed with a corresponding annular working part to act on the blank, which is convenient for clamping and locking the part, as shown in Figure 4.
Direct strong spinning trial processing
Since the 5A06-0 aluminum alloy material has good plasticity, we want to try the possibility of direct strong spinning to form the part first, and at the same time find the difficulties and problems that are easy to occur during the spinning process of the part. Equipment: CNC1500 CNC spinning machine. Spinning parameters: speed n=50 r/min, feed f=80~60 mm/min, gap z=2.6 mm, roller fillet radius R=10 mm, roller attack angle should take into account the shape characteristics of the large and small ends of the part as much as possible to avoid defects such as scraping and back extrusion; Lubricant: Apply MoS2 paste + chlorinated paraffin on the outer surface, and apply 90# engine oil on the inner surface and mold. Processing effect: The wall thickness of the part is 3.5~3.6 mm, and the small end curve part is well attached to the mold; the gap between the mold and the last 30 mm of the small end curve gradually increases, and a large unstable bulge appears 50 mm after the small end curve is just spun, which eventually leads to the tearing of the part and the failure of the plan, as shown in Figure 5.
Trial processing of combined strong spinning and general spinning
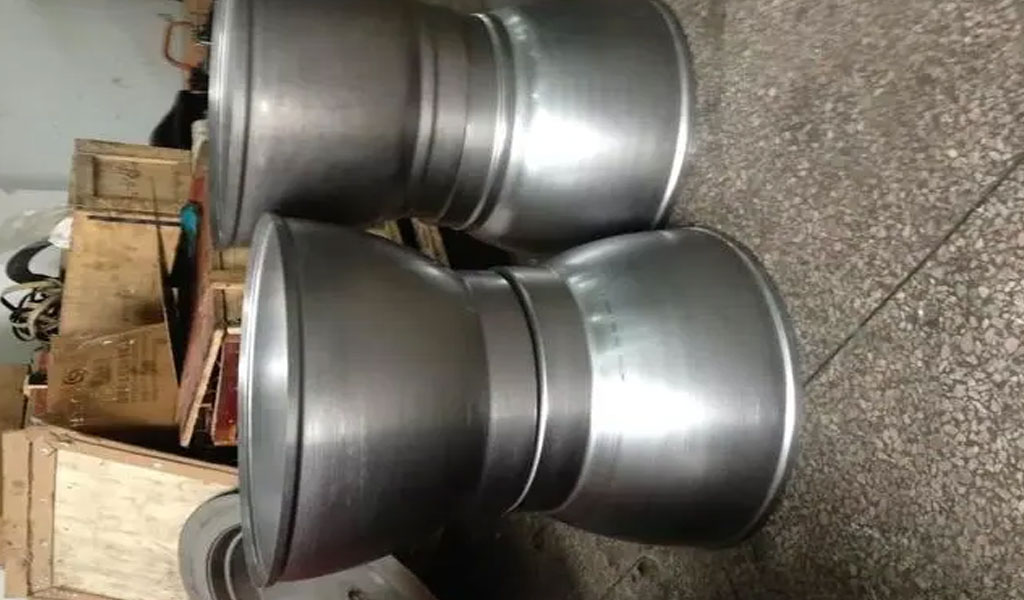
Existing problems
According to the previous trial spinning observations, the danger zone is in the transition area between the mold curve and the straight section. A closer look revealed that the radius of the transition section where the mold curve and the straight section meet is too small and too sharp, which is not conducive to the flow and forming of the material. When spinning the straight section, due to the extrusion stress during the previous curved surface forming, the material of the final processing section produces a certain amount of backward expansion effect, causing the angle between the blank and the mold to widen, resulting in the blank turning back and causing friction with the spinning wheel before the spinning wheel is pressed down in place during spinning, which is very unfavorable for the spinning of the final straight section, causing the parts to break due to instability and scratching.
Countermeasures
- 1) Increase the arc of the intersection of the mold surface: Use a coarse grinding wheel, oilstone, and sandpaper to manually polish and smooth the edges on the mold to reduce the interference of the steep drop rate on material forming.
- 2) According to the analysis of the inspection data of the failed parts, appropriately reduce the spinning gap to enhance the mold-fitting effect while ensuring the thickness of the parts.
- 3) For the straight section of the rear section of the part, the plan of first general spinning and then strong spinning is adopted. In order to avoid the material hardening affecting the forming effect, heating means are used.
Implementation of measures
- 1) The upper edge of the mold is polished from R3 mm to R8 mm.
- 2) Strong spinning parameters: speed n=50 r/min, feed f=40 mm/min, gap z=2.45 mm.
- 3) After the part is spun through the curved busbar section, it is paused first; two acetylene flame guns are used to evenly heat the remaining unprocessed section of the material (see Figure 6), and then three passes of front rolling and front closing are used to close the mouth.
When the tail end of the material is closed to about two finger widths from the mold, the last strong spinning is performed to complete the part processing. Processing parameters during general spinning: speed n=80 r/min, feed f=240 mm/min, and the downward pressure of the large end of each closing is 12 mm. In actual processing, due to the rapid heat dissipation of aluminum alloy, large mold size, flame heating loss and other reasons, the parts were heated to 180 and 260 ℃ respectively, and one was tried to spin each. Processing effect: of the two tested pieces, one had a heavy knife mark, and the other had a crack near the end of processing, and the effect was not very good. The wall thickness of the part is about 3.15-3.35 mm. The wall thickness is smaller at high heating temperature, and the wall thickness is larger at low temperature. The surface quality is not very good; when the part is processed to the last 100 mm section, due to factors such as instability and cold work hardening, fracture and tearing defects are very likely to occur (see Figure 7), resulting in spinning failure. At the same time, the diameter expansion phenomenon of the part is very serious (≥10 mm or so), which cannot meet the requirements of the process documents.
Improved strong spinning and general spinning schemes
Technical analysis
- 1) The various measures that may be implemented at present cannot completely solve the defect of 10 mm diameter expansion, so it is necessary to consider the rationality of the diameter expansion concession in the mold size.
- 2) In order to reduce the forming pressure during the later stage of general spinning, the material should be rolled back as much as possible during the early stage of strong spinning, so that the material can be as close to the mold as possible, and the length of the effective forming part of the part during strong spinning can be increased as much as possible.
- 3) The downward pressure during general spinning should not be too large, otherwise it will cause excessive deformation fatigue to the material, and the plasticity will drop rapidly, resulting in spinning failure.
- 4) The temperature level and control are important links that affect the processing effect. Too high temperature can easily cause large thinning, instability, and diameter expansion; too low temperature can cause insufficient material plasticity and part forming failure. It has been observed that the corresponding processing effect is better when the temperature is around 220 ℃.
Countermeasures
- 1) First repair the mold: reduce the diameter of its straight barrel part by 6 mm on the original basis, and then spin it.
- 2) Perform non-destructive testing on the blank, and remove the blank with defects such as stratification and slag inclusion to avoid affecting the spinning quality.
- 3) Reduce the feed ratio when the small end is strongly spun, and appropriately reduce the tool clearance.
- 4) Increase the effective part of the strong spinning forming of the part as much as possible, and reduce the length of the closing during the general spinning process; and appropriately distribute the pressure during the general spinning process.
- 5) Heating evenly, and controlling the heating temperature of the blank during hot spinning, so that it can be kept at around 220 ℃ during processing.
Implementation of measures
- 1) In addition to reducing the diameter of the straight section, the mold rework also performs a smooth transition treatment on the edge of the transition section.
- 2) When the small end is strongly spun: reduce the feed ratio to 0.6 mm/r, and reduce the gap by 0.05 mm; appropriately reduce the wall thickness of the part, improve the mold fit, and reduce the instability of the transition area.
- 3) After the part is strongly spun to 100 mm past the conical mother line section, it is processed by general spinning; change the three-pass general spinning to four-pass general spinning, and the pressure of each pass is 12, 10, 10, and 8 mm respectively. Processing parameters for general spinning: speed n=80 r/min, feed f=240 mm/min. Considering factors such as heat loss and waiting time, the actual billet temperature is heated to 240 ℃ before general spinning. During the heating operation, one person operates from front to back, and one person operates from back to front, moving at a constant speed and slowly.
- 4) Processing parameters for the last pass of strong spinning of the straight section: speed n=50 r/min, feed f=30 mm/min, gap z=2.30 mm; wheel fillet radius R=10 mm; lubricant: MoS2 paste + chlorinated paraffin is applied to the outer surface, and 90# engine oil is applied to the inner surface and mold.
Processing effect
After two batches of parts processing verification, the wall thickness of the parts is about 3.0-3.1 mm, the inner diameter size tolerance is ≤1 mm, the inner wall is smooth, the outer surface texture is uniform, and the strength can withstand a pressure of 435 MPa after the pressure test, which is greater than the 417 MPa required by the process file. It can be processed in batches and meets the use requirements, see Figure 8.
Key points of operation
- 1) Strong spinning operation. When spinning, pay attention to avoid the step part of the small end used to fix the part to avoid affecting the clamping of the part; the spinning gap should try to make the material in a negative deviation state to make the part better fit the mold.
- 2) General spinning operation. The double-wheel synchronous closing operation is used to avoid the material being subjected to unilateral force when the single-wheel general spinning is used to close the mouth, forming a skewed mouth, which is not conducive to forming and ensuring the wall thickness of the part. The length of the first pass of the general spinning should be sufficient to ensure that the end point of the last pass of the strong spinning does not overlap with the stop point of the general spinning, and a spacing of 10 to 15 mm should be maintained; at the same time, the starting and ending points of each subsequent pass of the general spinning should be staggered with the starting and ending points of the previous pass of the general spinning by 10 to 15 mm, with the starting point staggered forward and the end point staggered backward; to avoid the material from breaking due to repeated rolling and plasticity reduction; the best closing time is to close the gap between the blank and the mold to about two fingers. If it is too wide or too narrow, it is easy to break during the last strong spinning, resulting in spinning failure.
- 3) About the knife connection. In order to reduce the depth of the cutter mark between the hyperbolic curve and the straight tube section, the starting point of the cutter in the first normal rotation is 25 mm back from the stop position of the cutter in the first strong rotation; the cutting point in the last strong rotation is 100 mm back from the stop position of the cutter in the first strong rotation, considering that the material becomes soft after heating and is prone to steps. The gap can be slightly smaller, gradually transitioning from 2.1 mm to 2.3 mm, to prevent strain cracks;
- 4) Heating. Two acetylene flame guns are used for left-right symmetrical heating. Due to the large heating area, one gun heats at the near end while the other heats at the far end. Applying MoS2 paste on the surface of the part can increase the heating speed. The spindle rotation speed is 60 r/min during heating. It should not be too fast, otherwise it will affect the heating effect. When measuring the heating temperature, several points should be measured. Whether the temperature rise is uniform is very important for the success of the processing (the best effect is when the temperature is kept at 210 ℃). In addition, attention should be paid to the fire prevention measures of the equipment to ensure safe production.
- 5) During the processing of parts, the pause time should not exceed 40 minutes. Otherwise, due to factors such as material fatigue sensitivity and cold work hardening, the internal grains of the material will be distorted, the plasticity will decrease, and fracture defects will occur, resulting in processing failure;
- 6) According to the sound of the material when it is rolled by the spinning wheel and the amount of material accumulation in front of the spinning wheel, judge and adjust the spinning processing parameters. A loud sound indicates excessive downward pressure and the material is close to the fatigue limit; when the accumulation is large, the gap is small and it is easy to become unstable.
Within a certain range, the operator can adjust the gap, speed, feed rate, etc. in time to optimize.
- 1) It is feasible to use a combination of strong and general on a horizontal CNC spinning machine to spin large-sized aluminum alloy cylindrical parts with conical surfaces. It needs to be supplemented by hot spinning, but it still has certain cost advantages compared with other processing schemes.
- 2) The blank design of large-sized aluminum alloy cylindrical parts with conical surfaces not only involves processing costs and production progress, but is also one of the key factors affecting the success of spinning.
- 3) Large-sized aluminum alloy cylindrical parts have a large amount of expansion, and the specific value needs to be treated specifically; when designing the mold, the margin should be enlarged by 2 to 3 mm compared to the steel part spinning.
- 4) In view of the high sensitivity of aluminum alloy materials, the heating method and the stability of temperature during hot spinning are very important.
- 5) For general spinning with a large amount of closing, the amount of forming processing during the general spinning should be reduced as much as possible in the early stage. During the general spinning, a double-wheel synchronous closing operation is adopted. The use of a multi-pass and small downward pressure distribution method is more conducive to the processing of parts.
Maximize Tooling and CNC Metal Spinning Capabilities.
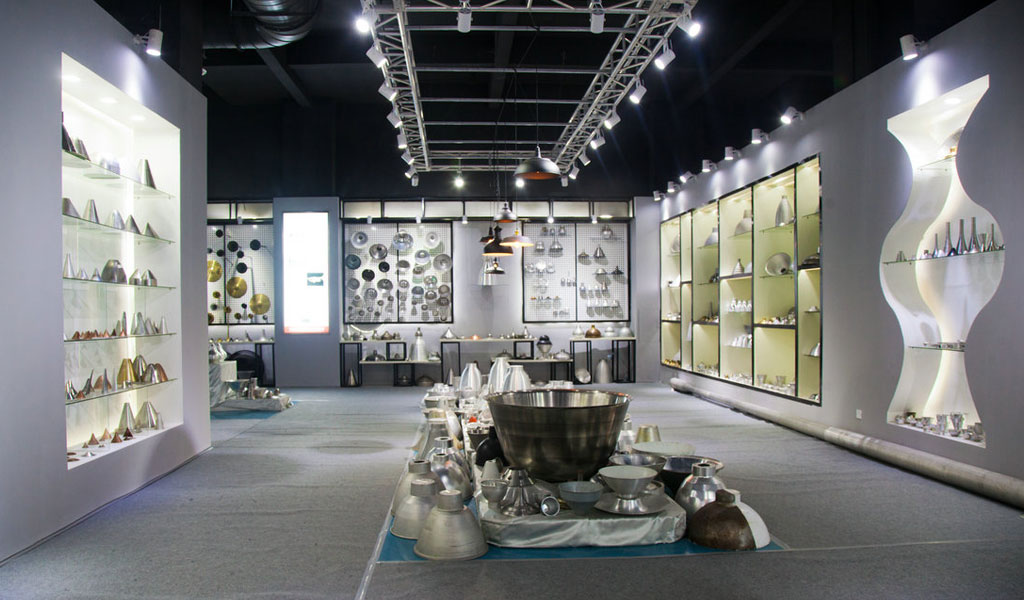
At BE-CU China Metal Spinning company, we make the most of our equipment while monitoring signs of excess wear and stress. In addition, we look into newer, modern equipment and invest in those that can support or increase our manufacturing capabilities. Our team is very mindful of our machines and tools, so we also routinely maintain them to ensure they don’t negatively impact your part’s quality and productivity.
Talk to us today about making a rapid prototype with our CNC metal spinning service. Get a direct quote by chatting with us here or request a free project review.
BE-CU China CNC Metal Spinning service include : CNC Metal Spinning,Metal Spinning Die,Laser Cutting, Tank Heads Spinning,Metal Hemispheres Spinning,Metal Cones Spinning,Metal Dish-Shaped Spinning,Metal Trumpet Spinning,Metal Venturi Spinning,Aluminum Spinning Products,Stainless Steel Spinning Products,Copper Spinning Products,Brass Spinning Products,Steel Spinning Product,Metal Spinnin LED Reflector,Metal Spinning Pressure Vessel,