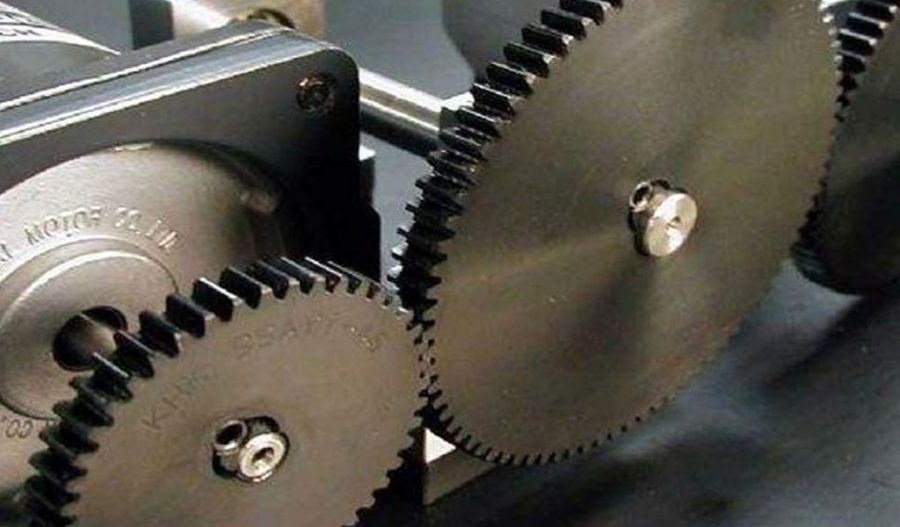
Spinning trapezoidal internal gears is a sophisticated process used in the manufacturing of gears with specific geometries, where the tooth profile is not circular but trapezoidal. This process is employed primarily in industries where precision, durability, and the ability to operate under high stress are paramount. Trapezoidal internal gears are crucial components in machines that require high torque and reliable performance, such as in the automotive, aerospace, and heavy machinery sectors. The use of the spinning process to manufacture these gears allows for greater flexibility in terms of geometry, precision, and material efficiency compared to traditional gear cutting methods.
Internal gears are gears that have teeth cut on the inside of a cylindrical surface, and trapezoidal profiles are used in specific applications where a high load-bearing capacity is required in combination with a smooth engagement between meshing gears. The trapezoidal shape of the tooth flanks provides an optimized contact surface, resulting in improved load distribution, reduced wear, and longer operational life for the gears.
Spinning, in this context, refers to a method of deforming metal to create complex geometries by rotating the material at high speeds, usually under the influence of a tool that progressively shapes the workpiece. The process is widely used in industries such as aerospace, automotive, and precision engineering due to its efficiency in producing parts with complex shapes and fine tolerances. It is an advanced manufacturing technique that requires highly specialized equipment, knowledge of material properties, and an understanding of gear mechanics.
1. The Basics of Trapezoidal Internal Gears
Before diving into the specifics of the spinning process, it is essential to understand the nature of trapezoidal internal gears. These gears differ from traditional involute gears in that the teeth are not uniformly shaped but have a trapezoidal form, which provides specific benefits for certain mechanical applications.
Key Characteristics:
- Tooth Profile: The tooth profile of a trapezoidal internal gear resembles a trapezoid rather than the more common involute shape. This shape can result in higher load-bearing capacity and smoother meshing with corresponding gears.
- Material Selection: The materials used for trapezoidal internal gears vary depending on the application, but common choices include high-strength steel alloys, titanium, and other advanced materials designed to withstand high mechanical stress.
- Load Distribution: The trapezoidal shape allows for a more even distribution of the load across the teeth during engagement, which can reduce the risk of premature wear and failure.
2. The Spinning Process for Trapezoidal Internal Gears
Spinning, as a method of manufacturing gears, involves using a lathe-like machine to rotate a workpiece while a tool is pressed against the material to form it into a desired shape. When spinning trapezoidal internal gears, the process must be adapted to handle the specific requirements of internal gear geometries and the trapezoidal tooth profiles.
The key steps involved in spinning trapezoidal internal gears are as follows:
- Material Preparation: The process begins by selecting an appropriate metal alloy based on the application’s demands, such as strength, heat resistance, or corrosion resistance. The material is prepared in the form of a blank, typically a cylindrical workpiece with a diameter and thickness that exceed the finished dimensions.
- Tool Selection: The tools used for spinning trapezoidal internal gears are specifically designed for the task. A spinning tool typically consists of a rotating spindle and a mandrel that holds the workpiece. The tool is often made of high-speed steel (HSS) or carbide to ensure durability and maintain sharpness during the shaping process.
- Setting Up the Spinning Machine: The spinning machine, often a CNC lathe or a hydraulic spinning machine, is set up to accommodate the blank and the tools. The workpiece is securely held in place, and the tool is calibrated to achieve the required tooth profile.
- Spinning Process: As the workpiece is spun, the tool presses against it and gradually shapes the material into the trapezoidal tooth profile. The spinning tool’s movement is carefully controlled, often in combination with other machining operations, to ensure that the teeth are accurately formed to the desired dimensions.
- Quality Control: During and after the spinning process, quality control measures are taken to ensure that the dimensions of the gear are within the required tolerance. This often includes the use of precision measuring instruments, such as calipers and coordinate measuring machines (CMM), to check tooth spacing, depth, and alignment.
3. Comparison of Spinning with Other Gear Manufacturing Methods
While spinning offers several advantages for the production of trapezoidal internal gears, it is crucial to compare this method with other traditional and modern gear manufacturing techniques. These include gear hobbing, gear shaping, and casting.
Table 1: Comparison of Spinning with Traditional Gear Manufacturing Methods
Method | Advantages | Disadvantages | Best Used For |
---|---|---|---|
Spinning | High precision, minimal material waste, capable of complex geometries | Requires specialized equipment, limited to certain geometries | Aerospace, automotive, high-precision gears |
Hobbing | Efficient for high-volume production, versatile in terms of tooth profiles | Can result in more material waste, limited to external gears | High-volume production, external gears |
Shaping | Excellent for producing internal gears, allows for fine tooth profiles | Slower than hobbing, may require additional finishing operations | Internal gears, low-volume production |
Casting | Suitable for complex shapes, large production volumes | Lower precision, requires more post-processing, material limitations | Large-volume production of simple gears |
The comparison reveals that while spinning offers high precision and minimal waste, it is most suited for high-precision, low-volume production. Traditional methods like hobbing and shaping are more suited to larger-scale production, especially when external gears are involved. Casting is often used for large-scale manufacturing of simpler gears, although it requires additional finishing and is less precise.
4. Advantages of Spinning Trapezoidal Internal Gears
The spinning process offers several advantages over traditional gear manufacturing techniques. These benefits include:
- Material Efficiency: Spinning minimizes material waste, as the process involves forming the material rather than removing it through cutting or milling. This is particularly important in industries where material costs are high.
- Precision: The spinning process can achieve very tight tolerances, which is crucial for applications requiring highly accurate gears. The method allows for complex internal geometries that are difficult to achieve through traditional machining.
- Cost-Effectiveness for Low Volumes: While spinning equipment may be more expensive than traditional machines, the reduction in material waste and the ability to create complex parts in fewer steps can make it more cost-effective for low-volume, high-precision applications.
- Strength and Durability: The spinning process can impart favorable mechanical properties to the material, such as improved grain structure and increased strength. This can result in a longer operational life for the gears and increased reliability under heavy loads.
5. Challenges in Spinning Trapezoidal Internal Gears
Despite the many advantages, spinning trapezoidal internal gears also presents certain challenges. These include:
- Tool Wear: The high rotational speeds and pressures involved in spinning can lead to rapid tool wear, especially when working with tough, high-strength materials. Regular tool maintenance and replacement are essential to maintain the quality of the gears.
- Complexity of Setup: The process requires specialized equipment and skilled operators who can precisely control the movement of both the workpiece and the tool. Setting up the machine for different gear sizes and tooth profiles can be time-consuming.
- Limited to Certain Materials: Not all materials are suitable for spinning, particularly those that are too brittle or have low ductility. Materials that can withstand the deformation involved in the process must be carefully selected.
6. Applications of Trapezoidal Internal Gears
Trapezoidal internal gears are used in a variety of industries, including:
- Automotive: In automotive applications, these gears are used in differential drives, gearboxes, and various other high-torque mechanisms where durability and smooth engagement are critical.
- Aerospace: The aerospace industry benefits from the strength and precision of trapezoidal internal gears, especially in critical systems such as actuators, turbines, and flight control mechanisms.
- Industrial Machinery: Trapezoidal internal gears are also used in industrial machinery where high-load capacity and reliability are required for continuous operation under challenging conditions.
Maximize Tooling and CNC Metal Spinning Capabilities.
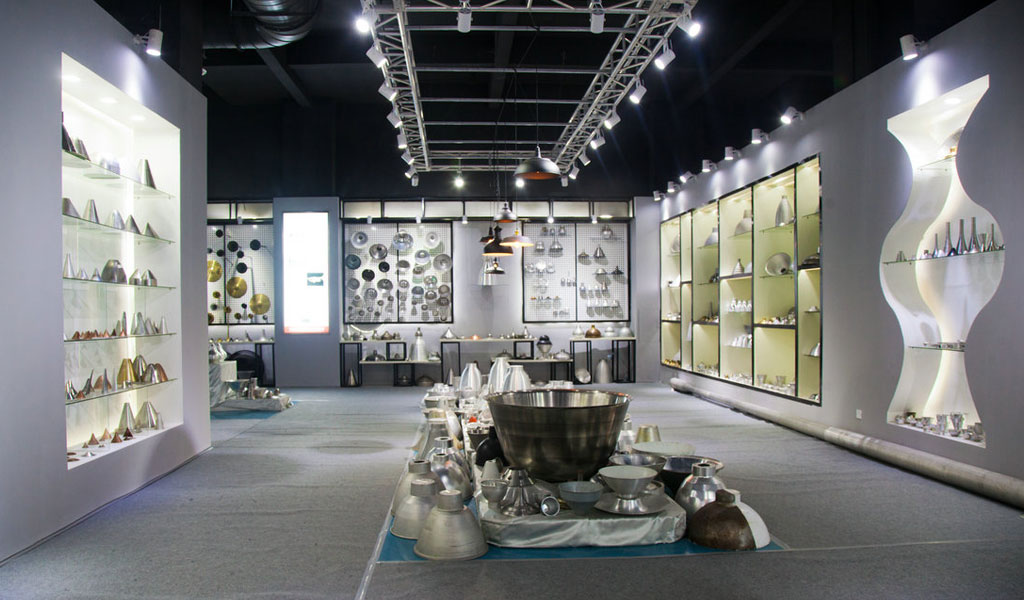
At BE-CU China Metal Spinning company, we make the most of our equipment while monitoring signs of excess wear and stress. In addition, we look into newer, modern equipment and invest in those that can support or increase our manufacturing capabilities. Our team is very mindful of our machines and tools, so we also routinely maintain them to ensure they don’t negatively impact your part’s quality and productivity.
Talk to us today about making a rapid prototype with our CNC metal spinning service. Get a direct quote by chatting with us here or request a free project review.
BE-CU China CNC Metal Spinning service include : CNC Metal Spinning,Metal Spinning Die,Laser Cutting, Tank Heads Spinning,Metal Hemispheres Spinning,Metal Cones Spinning,Metal Dish-Shaped Spinning,Metal Trumpet Spinning,Metal Venturi Spinning,Aluminum Spinning Products,Stainless Steel Spinning Products,Copper Spinning Products,Brass Spinning Products,Steel Spinning Product,Metal Spinnin LED Reflector,Metal Spinning Pressure Vessel,