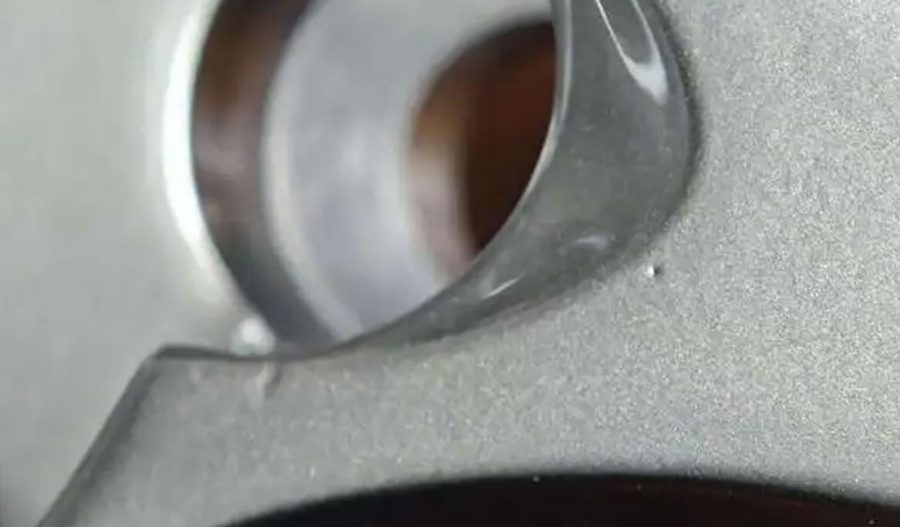
Metal bellows are precision-engineered, flexible components designed to accommodate axial, lateral, and angular movements while maintaining a hermetic seal. These versatile structures are critical in industries such as aerospace, semiconductor manufacturing, medical devices, and oil and gas, where they serve as actuators, seals, expansion joints, and sensors. The manufacturing of metal bellows involves several techniques, including hydroforming, edge-welding, and electroforming, but one of the foundational processes for creating seamless bellows is metal spinning, also known as spin forming. This article explores the technology of spinning in the manufacture of metal bellows, delving into its historical evolution, technical principles, material considerations, process variations, and modern advancements. Detailed comparisons of spinning with other bellows manufacturing methods are provided to highlight its unique advantages and limitations.
Metal spinning is a metalworking process that involves rotating a metal disc or tube at high speed while applying localized pressure to shape it into an axially symmetric part. In the context of bellows manufacturing, spinning is primarily used to create seamless tubular preforms, which are subsequently formed into convoluted bellows through secondary processes like hydroforming or rolling. The process is valued for its ability to produce high-precision components with minimal material waste, making it a cost-effective and sustainable option for both prototyping and high-volume production. Spinning’s adaptability to various metals, including stainless steel, titanium, and nickel alloys, further enhances its suitability for bellows applications, where material properties such as corrosion resistance and flexibility are paramount.
The significance of spinning in bellows manufacturing lies in its capacity to produce seamless tubes with consistent wall thickness and tight dimensional tolerances. These preforms serve as the foundation for bellows that must withstand extreme pressures, temperatures, and cyclic stresses in demanding environments. Unlike welded bellows, which may have seams that introduce potential failure points, spun seamless bellows offer superior reliability and fatigue resistance, making them ideal for mission-critical applications such as vacuum interrupters and aerospace actuators. This article aims to provide a comprehensive examination of spinning technology, its role in bellows production, and its comparative advantages over other methods, supported by detailed tables and technical analyses.
Historical Context of Metal Spinning
Origins and Early Development
Metal spinning traces its origins to ancient civilizations, where rudimentary forms of the process were used to shape soft metals like gold, silver, and copper into decorative and functional objects. Archaeological evidence suggests that the Ancient Egyptians employed spinning techniques as early as the 4th Dynasty (circa 2600 BCE), using human-powered lathes to form metal vessels. These early methods relied on manual tools and soft metals with high ductility, limiting the complexity and scale of the components produced.
The Industrial Revolution marked a significant turning point for metal spinning. The introduction of steam-powered machinery in the 19th century enabled the spinning of harder metals, such as brass and copper, at higher speeds and with greater precision. By the early 20th century, the advent of electric motors further revolutionized the process, providing the power and control needed to spin stainless steel and other high-strength alloys. These advancements coincided with the growing demand for precision components in industries such as automotive, aerospace, and chemical processing, where metal bellows began to play a critical role.
Evolution in Bellows Manufacturing
The application of spinning to bellows manufacturing emerged in the late 19th and early 20th centuries, driven by the need for flexible, leak-tight seals in industrial machinery and scientific instruments. Early bellows were often made from leather or rubber, but the development of metal spinning allowed for the creation of durable, metallic bellows capable of withstanding high pressures and temperatures. The process of spinning seamless tubes provided a reliable starting point for forming convoluted bellows, which were initially shaped using manual rolling or pressing techniques.
The 20th century saw significant refinements in spinning technology, particularly with the introduction of computer numerical control (CNC) lathes in the 1960s and 1970s. CNC spinning enabled unprecedented levels of precision and repeatability, allowing manufacturers to produce bellows with complex geometries and tight tolerances. The integration of spinning with secondary forming processes, such as hydroforming, further expanded the capabilities of bellows production, enabling the creation of seamless, multi-ply bellows for specialized applications. Today, spinning remains a cornerstone of bellows manufacturing, particularly for seamless designs used in high-precision industries.
Principles of Metal Spinning
Basic Mechanics of Spinning
Metal spinning involves the deformation of a metal blank—typically a flat disc or a cylindrical tube—by rotating it at high speed on a lathe and applying localized pressure with a forming tool. The blank is clamped against a mandrel, which defines the internal shape of the final component. The forming tool, often a roller or a pointed instrument, is moved across the surface of the blank in a series of passes, gradually shaping the metal into the desired form. The process is incremental, with each pass refining the shape and reducing the wall thickness as the material flows over the mandrel.
The mechanics of spinning can be described as a combination of plastic deformation and shear forming. Plastic deformation occurs as the metal is stretched and compressed under the pressure of the forming tool, while shear forming reduces the wall thickness by controlling the flow of material along the mandrel. The process is highly dependent on the material’s ductility, the speed of rotation, and the force applied by the tool. For bellows manufacturing, spinning is typically used to create seamless tubes with uniform wall thickness, which are then processed further to form the characteristic convolutions of a bellows.
Types of Spinning Processes
Metal spinning encompasses several variations, each suited to specific applications and component geometries. The three primary types relevant to bellows manufacturing are conventional spinning, shear spinning, and flow forming:
- Conventional Spinning: In conventional spinning, the blank is shaped without significant changes in wall thickness. The metal is stretched and bent over the mandrel to form the desired shape, making this method ideal for creating shallow or moderately deep components. In bellows production, conventional spinning is used to form tubular preforms with consistent wall thickness, which are later hydroformed into convoluted shapes.
- Shear Spinning: Shear spinning, also known as power spinning, involves a deliberate reduction in wall thickness as the metal is formed over the mandrel. The forming tool applies high pressure to shear the material, resulting in a thinner, elongated component. Shear spinning is used in bellows manufacturing to produce long, thin-walled tubes for applications requiring high flexibility and low spring rates.
- Flow Forming: Flow forming is an advanced form of spinning that combines elements of shear spinning and rolling. The metal blank is mounted on a rotating mandrel, and rollers apply axial and radial forces to elongate the material and reduce its wall thickness. Flow forming is particularly effective for creating seamless, high-strength tubes with precise dimensional control, making it a preferred method for bellows preforms in aerospace and defense applications.
Each of these spinning processes offers distinct advantages in terms of material utilization, dimensional accuracy, and production efficiency. The choice of process depends on the specific requirements of the bellows, including its size, wall thickness, and intended application.
Equipment and Tooling
Metal spinning for bellows manufacturing requires specialized equipment, including spinning lathes, mandrels, and forming tools. Modern spinning lathes are typically CNC-controlled, allowing for precise control of tool paths, rotation speeds, and applied forces. The mandrel, which defines the internal shape of the spun component, is custom-designed for each bellows preform and is usually made from hardened steel or aluminum to withstand the stresses of spinning.
Forming tools vary in design depending on the spinning process and the desired shape. Rollers are commonly used in shear spinning and flow forming, as they distribute pressure evenly across the blank, reducing the risk of defects such as wrinkling or tearing. For conventional spinning, pointed tools or lever arms may be used to apply localized pressure. Tool materials, such as carbide or high-speed steel, are selected for their durability and resistance to wear, ensuring consistent performance over multiple production runs.
Materials for Spinning Metal Bellows
Common Materials and Their Properties
The choice of material for spinning metal bellows is critical, as it directly affects the component’s performance, durability, and manufacturability. Bellows are typically made from metals with high ductility, corrosion resistance, and fatigue strength to withstand cyclic stresses and harsh environments. The following materials are commonly used in spinning seamless bellows preforms:
- Stainless Steel: Stainless steel, particularly 300-series alloys like 304, 316, and 321, is the most widely used material for bellows due to its excellent corrosion resistance, tensile strength, and formability. It is suitable for applications in chemical processing, medical devices, and semiconductor manufacturing, where exposure to aggressive media is common.
- Titanium: Titanium and its alloys, such as Ti-6Al-4V, offer high strength-to-weight ratios, corrosion resistance, and biocompatibility, making them ideal for aerospace and medical bellows. Titanium’s low ductility at room temperature requires elevated temperatures during spinning to achieve the necessary deformation.
- Nickel Alloys: Nickel-based alloys, including Inconel (e.g., 625, 718) and Hastelloy, are used in bellows for extreme environments, such as high-temperature aerospace applications and corrosive chemical processing. These alloys have high strength and oxidation resistance but are challenging to spin due to their low ductility.
- Brass and Bronze: Brass and bronze are used in bellows for low-temperature applications, such as HVAC systems and mechanical altimeters. These materials offer good formability and corrosion resistance but have lower tensile strength than stainless steel or titanium.
- Beryllium Copper: Beryllium copper is valued for its high tensile strength, electrical conductivity, and fatigue resistance, making it suitable for bellows in electrical interrupters and precision sensors. It can be spun and subsequently heat-treated to enhance its dimensional stability.
Material Selection Criteria
Selecting the appropriate material for spinning bellows involves balancing several factors, including:
- Ductility: The material must have sufficient ductility to undergo plastic deformation without cracking or tearing during spinning. Materials with high elongation percentages, such as stainless steel and brass, are preferred.
- Corrosion Resistance: Bellows are often exposed to corrosive media, such as chemicals, seawater, or high-humidity environments. Materials like stainless steel, titanium, and nickel alloys offer superior resistance to corrosion.
- Fatigue Strength: Bellows are subjected to cyclic stresses during operation, requiring materials with high fatigue strength to ensure long cycle life. Nickel alloys and beryllium copper excel in this regard.
- Temperature Range: The operating temperature of the bellows dictates the choice of material. For high-temperature applications (e.g., aerospace actuators), nickel alloys and titanium are preferred, while brass and bronze are suitable for lower temperatures.
- Cost: Material cost is a significant consideration, particularly for high-volume production. Stainless steel and brass are relatively affordable, while titanium and nickel alloys are more expensive due to their specialized properties.
Challenges in Spinning High-Strength Alloys
Spinning high-strength alloys, such as titanium and Inconel, presents unique challenges due to their low ductility and high work-hardening rates. These materials require specialized techniques, such as hot spinning, to achieve the necessary deformation. Hot spinning involves heating the blank to elevated temperatures (typically 500–1000°C) to increase its ductility and reduce the forces required for forming. However, this introduces additional complexities, including the need for precise temperature control and specialized tooling to prevent oxidation and thermal distortion.
Work hardening, a phenomenon where the material becomes harder and less ductile as it is deformed, can also lead to defects such as cracking or uneven wall thickness. To mitigate this, manufacturers may use multiple annealing steps during spinning to restore the material’s ductility. These challenges underscore the importance of expertise and advanced equipment in spinning high-strength alloys for bellows applications.
Spinning Process in Bellows Manufacturing
Preparation of the Blank
The spinning process begins with the preparation of the metal blank, which is typically a flat disc or a cylindrical tube cut from sheet or bar stock. The blank’s dimensions are determined by the desired size of the bellows preform, accounting for material thinning during spinning. For seamless bellows, the blank is often a seamless tube produced by deep drawing or extrusion, ensuring uniformity and eliminating weld seams that could compromise the bellows’ integrity.
The blank is cleaned and inspected to remove surface contaminants, such as oil, grease, or oxides, which could affect the quality of the spun component. Surface preparation may involve chemical cleaning, abrasive blasting, or ultrasonic cleaning, depending on the material and application requirements.
Spinning the Preform
The spinning process for bellows preforms typically involves conventional spinning or flow forming, depending on the desired wall thickness and length. The blank is mounted on a rotating mandrel, and the forming tool is positioned to apply pressure to the outer surface. The tool follows a programmed path (in CNC spinning) or is guided manually, gradually shaping the blank into a seamless tube with the desired diameter and wall thickness.
Key parameters in the spinning process include:
- Rotation Speed: The speed of the lathe, typically ranging from 500 to 2000 RPM, affects the material’s flow and the quality of the surface finish. Higher speeds are used for softer materials like brass, while lower speeds are preferred for high-strength alloys to minimize heat generation.
- Tool Pressure: The force applied by the forming tool determines the rate of deformation and the extent of wall thinning. Excessive pressure can cause defects such as wrinkling or tearing, while insufficient pressure may result in incomplete forming.
- Tool Path: The path of the forming tool, whether linear or curved, defines the shape of the preform. CNC spinning allows for complex tool paths, enabling the production of tapered or contoured tubes.
- Lubrication: Lubricants, such as oil-based or synthetic compounds, are applied to reduce friction between the tool and the blank, minimizing wear and improving surface quality.
The spinning process is iterative, with multiple passes required to achieve the final shape. Each pass refines the preform’s geometry, reducing wall thickness and improving dimensional accuracy. For high-precision bellows, the spun preform may undergo intermediate annealing to relieve residual stresses and enhance formability.
Secondary Forming of Bellows
Once the seamless tube is spun, it is subjected to secondary forming processes to create the characteristic convolutions of a bellows. The most common method is hydroforming, in which the tube is placed in a die and pressurized with a fluid (typically water or oil) to form the convolutions. Hydroforming allows for precise control of the convolution shape, spacing, and wall thickness, ensuring uniformity and consistency.
Alternatively, the tube may be rolled or mechanically formed to create convolutions. Rolling involves passing the tube through a series of rollers that progressively shape the metal, while mechanical forming uses presses or dies to stamp the convolutions. These methods are less common for seamless bellows, as they may introduce stresses or inconsistencies that affect performance.
The secondary forming process is critical to the bellows’ functionality, as it determines its flexibility, spring rate, and pressure capacity. The spun preform’s uniform wall thickness and lack of seams ensure that the convolutions are consistent and free of defects, enhancing the bellows’ reliability and fatigue life.
Comparison of Spinning with Other Bellows Manufacturing Methods
Overview of Bellows Manufacturing Methods
In addition to spinning-based seamless bellows, metal bellows can be produced using several other methods, each with distinct advantages and limitations. The primary methods are:
- Edge-Welded Bellows: Edge-welded bellows are made by welding a series of stamped metal diaphragms together, alternating inner diameter (ID) and outer diameter (OD) welds. This method allows for high flexibility and long stroke lengths, making it suitable for applications requiring significant axial movement.
- Electroformed Bellows: Electroformed bellows are created by electroplating a thin layer of metal (typically nickel or copper) onto a mandrel, which is later removed. This method is ideal for producing small, lightweight bellows with intricate geometries and low tooling costs.
- Seam-Welded Formed Bellows: Seam-welded bellows are made from rolled and welded sheet metal, which is then formed into convolutions. This method is cost-effective for large-diameter bellows but may have less precise spring rates due to variations in wall thickness.
Each method has unique characteristics that influence its suitability for specific applications. The following sections compare spinning-based seamless bellows with these methods, focusing on key performance parameters such as cost, flexibility, pressure capacity, and cycle life.
Detailed Comparison Tables
The following tables provide a comprehensive comparison of spinning-based seamless bellows with edge-welded, electroformed, and seam-welded bellows across various criteria. These tables are designed to assist engineers and manufacturers in selecting the appropriate method for their application.
Table 1: Manufacturing Cost and Scalability
Method | Tooling Cost | Piece Cost (Low Volume) | Piece Cost (High Volume) | Scalability | Typical Applications |
---|---|---|---|---|---|
Spinning (Seamless) | High | Moderate | Low | Excellent | Aerospace, medical, semiconductor |
Edge-Welded | Moderate | High | Moderate | Good | Vacuum systems, actuators |
Electroformed | Low | Low | Moderate | Moderate | Sensors, small-scale vacuum |
Seam-Welded | Low | Low | Low | Excellent | Expansion joints, large-scale industrial |
Analysis: Spinning-based seamless bellows have high initial tooling costs due to the need for custom mandrels and CNC equipment. However, their piece cost decreases significantly in high-volume production, making them cost-competitive for large-scale applications. Edge-welded bellows have moderate tooling costs but higher piece costs due to the labor-intensive welding process. Electroformed bellows are cost-effective for prototyping and small-scale production, while seam-welded bellows offer the lowest overall cost for large-diameter components.
Table 2: Flexibility and Stroke Length
Method | Maximum Stroke (% of Free Length) | Spring Rate Precision | Flexibility in Axial/Lateral Movement | Typical Convolution Shape |
---|---|---|---|---|
Spinning (Seamless) | 50–70% | High | Moderate | Sinusoidal, omega |
Edge-Welded | 80–90% | Moderate | High | Rectangular, toroidal |
Electroformed | 30–50% | High | Low | Sinusoidal |
Seam-Welded | 40–60% | Low | Moderate | Sinusoidal |
Analysis: Edge-welded bellows offer the highest stroke length and flexibility, making them ideal for applications requiring significant movement, such as actuators and expansion joints. Spinning-based seamless bellows provide moderate flexibility with high spring rate precision, suitable for applications where consistent performance is critical. Electroformed bellows have limited flexibility due to their thin walls, while seam-welded bellows offer moderate flexibility but lower precision due to weld seam variability.
Table 3: Pressure and Temperature Capabilities
Method | Maximum Pressure (PSI) | Operating Temperature Range (°C) | Leak Tightness | Typical Materials |
---|---|---|---|---|
Spinning (Seamless) | Up to 5000 | -200 to 600 | Excellent | Stainless steel, titanium, nickel alloys |
Edge-Welded | Up to 3000 | -250 to 800 | Excellent | Stainless steel, Inconel, Hastelloy |
Electroformed | Up to 3000 | -100 to 200 | Good | Nickel, copper |
Seam-Welded | Up to 2000 | -150 to 500 | Moderate | Stainless steel, brass |
Analysis: Spinning-based seamless bellows excel in high-pressure applications, with the ability to withstand up to 5000 PSI, depending on material and design. Their seamless construction ensures excellent leak tightness, making them suitable for vacuum and high-pressure systems. Edge-welded bellows offer comparable performance but are limited by weld integrity at extreme pressures. Electroformed bellows are suitable for moderate pressures and lower temperatures, while seam-welded bellows have lower pressure capabilities due to potential weaknesses at the weld seam.
Table 4: Cycle Life and Fatigue Resistance
Method | Typical Cycle Life (Cycles) | Fatigue Resistance | Sensitivity to Weld Imperfections | Applications Requiring High Cycle Life |
---|---|---|---|---|
Spinning (Seamless) | >1,000,000 | High | None | Aerospace actuators, medical implants |
Edge-Welded | 500,000–1,000,000 | Moderate | High | Vacuum interrupters, sensors |
Electroformed | 100,000–500,000 | Moderate | None | Precision sensors, small-scale actuators |
Seam-Welded | 100,000–500,000 | Low | High | Expansion joints, HVAC systems |
Analysis: Spinning-based seamless bellows offer the highest cycle life and fatigue resistance due to their lack of welds and uniform material properties. They are ideal for applications requiring long-term reliability, such as aerospace and medical devices. Edge-welded bellows have good cycle life but are sensitive to weld imperfections, which can reduce fatigue resistance. Electroformed bellows are suitable for moderate cycle life applications, while seam-welded bellows have the lowest fatigue resistance due to weld seam vulnerabilities.
Advantages of Spinning-Based Seamless Bellows
Spinning-based seamless bellows offer several advantages over other methods, including:
- Seamless Construction: The absence of welds eliminates potential failure points, enhancing reliability and leak tightness.
- High Precision: Spinning allows for tight dimensional tolerances and consistent wall thickness, ensuring precise spring rates and performance.
- Material Versatility: Spinning can accommodate a wide range of materials, from stainless steel to high-strength alloys like Inconel and titanium.
- Cost-Effectiveness in High Volume: While initial tooling costs are high, spinning becomes cost-competitive in large-scale production due to low piece costs.
- Sustainability: Spinning generates minimal material waste compared to subtractive processes, making it an environmentally friendly option.
Limitations of Spinning-Based Seamless Bellows
Despite its advantages, spinning has some limitations:
- High Tooling Costs: The need for custom mandrels and CNC equipment results in significant upfront costs, which may be prohibitive for low-volume production.
- Size Constraints: Spinning is best suited for bellows with outer diameters between 0.25 and 3 inches. Larger diameters are more cost-effectively produced using seam-welded methods.
- Material Challenges: High-strength alloys like titanium and Inconel require specialized techniques, such as hot spinning, which increase complexity and cost.
- Secondary Processing: Spinning produces preforms that require additional forming (e.g., hydroforming) to create convolutions, adding to the overall production time.
Modern Advancements in Spinning Technology
CNC and Automation
The integration of CNC technology has transformed metal spinning, enabling greater precision, repeatability, and efficiency. CNC spinning lathes use computer-controlled tool paths to produce complex geometries with minimal operator intervention. This has reduced the reliance on skilled labor and improved consistency, particularly for high-volume production of bellows preforms. Automation has also streamlined ancillary processes, such as blank preparation and quality inspection, further enhancing productivity.
Finite Element Analysis (FEA) and Simulation
Finite element analysis (FEA) has become a critical tool in optimizing spinning processes for bellows manufacturing. FEA allows engineers to model the stress-strain behavior of the metal blank during spinning, predicting potential defects such as wrinkling, tearing, or uneven wall thickness. By simulating different tool paths, rotation speeds, and material properties, manufacturers can optimize the spinning process before production begins, reducing trial-and-error and minimizing waste. FEA is particularly valuable for spinning high-strength alloys, where precise control of deformation is essential.
Hybrid Manufacturing Techniques
Recent advancements have led to the development of hybrid manufacturing techniques that combine spinning with other processes, such as additive manufacturing and laser forming. For example, additive manufacturing can be used to create complex mandrels with internal cooling channels, improving heat dissipation during hot spinning of titanium or Inconel. Laser-assisted spinning, in which a laser heats the blank locally to enhance ductility, has also shown promise for forming hard-to-deform alloys. These hybrid approaches expand the capabilities of spinning, enabling the production of bellows with unprecedented complexity and performance.
Industry 4.0 and Smart Manufacturing
The adoption of Industry 4.0 principles, such as the Internet of Things (IoT) and machine learning, is reshaping spinning technology. IoT-enabled spinning lathes can monitor real-time data on tool wear, temperature, and vibration, allowing for predictive maintenance and process optimization. Machine learning algorithms can analyze production data to identify patterns and improve process parameters, resulting in higher quality and lower costs. These smart manufacturing techniques are particularly relevant for bellows production, where consistency and reliability are paramount.
Applications of Spinning-Based Seamless Bellows
Aerospace and Defense
Spinning-based seamless bellows are widely used in aerospace and defense applications, where their high strength, fatigue resistance, and leak tightness are critical. Common applications include:
- Actuators: Seamless bellows serve as flexible seals in hydraulic and pneumatic actuators, enabling precise control of aircraft control surfaces and satellite mechanisms.
- Vacuum Systems: In ultra-high vacuum (UHV) systems, seamless bellows provide hermetic seals for beamlines, wafer handlers, and other components in semiconductor manufacturing and particle accelerators.
- Cryogenic Systems: Seamless bellows are used in cryogenic chambers for space simulation, maintaining leak-tight seals at temperatures as low as -200°C.
The seamless construction and material versatility of spun bellows make them ideal for these demanding applications, where failure could have catastrophic consequences.
Medical Devices
In the medical industry, seamless bellows are used in devices requiring biocompatibility, flexibility, and high cycle life. Examples include:
- Implantable Devices: Seamless bellows made from titanium or stainless steel are used in pacemakers and drug delivery systems, where they provide hermetic seals and withstand repeated flexing.
- Surgical Instruments: Bellows in endoscopic tools enable precise movement and sealing in minimally invasive surgeries.
- Sensors: Seamless bellows are used in pressure and temperature sensors for diagnostic equipment, converting environmental changes into mechanical motion.
The precision and reliability of spinning-based bellows ensure consistent performance in these critical applications.
Semiconductor Manufacturing
The semiconductor industry relies on seamless bellows for vacuum chambers, wafer handling systems, and gas delivery systems. Spinning-based bellows offer the following advantages in this context:
- Ultra-High Vacuum Compatibility: Seamless bellows maintain leak-tight seals in UHV environments, preventing contamination of semiconductor wafers.
- High Precision: The consistent spring rates of spun bellows ensure accurate positioning of wafers and other components.
- Corrosion Resistance: Materials like stainless steel and Inconel withstand exposure to reactive gases used in semiconductor processes.
Oil and Gas
In the oil and gas industry, seamless bellows are used in downhole drilling equipment, gas lift valves, and expansion joints. Their ability to withstand high pressures, corrosive media, and extreme temperatures makes them suitable for harsh environments. Spinning-based bellows provide reliable performance in applications such as:
- Pressure Transmitters: Bellows convert pressure changes into mechanical motion for accurate measurement in drilling operations.
- Flexible Connectors: Seamless bellows compensate for thermal expansion and vibration in pipelines and processing equipment.
Challenges and Future Directions
Technical Challenges
Despite its advantages, spinning-based bellows manufacturing faces several technical challenges:
- Material Limitations: The need for high ductility restricts the range of materials suitable for spinning, particularly for high-strength alloys like titanium and Inconel.
- Tool Wear: The high forces and temperatures involved in spinning can lead to rapid tool wear, increasing maintenance costs and downtime.
- Process Complexity: Spinning high-precision bellows preforms requires careful control of multiple parameters, including rotation speed, tool pressure, and lubrication, which can be challenging to optimize.
- Scalability for Large Diameters: Spinning is less cost-effective for large-diameter bellows, where seam-welded methods are more economical.
Future Directions
The future of spinning technology in bellows manufacturing lies in addressing these challenges through innovation and research. Key areas of focus include:
- Advanced Materials: Developing new alloys with improved ductility and fatigue resistance could expand the range of materials suitable for spinning, enabling the production of bellows for even more demanding applications.
- Next-Generation Equipment: The development of high-speed, multi-axis CNC spinning lathes with integrated sensors and adaptive control systems could enhance precision and reduce tool wear.
- Sustainable Manufacturing: Advances in spinning processes, such as low-energy forming techniques and recyclable mandrels, could further reduce the environmental impact of bellows production.
- Integration with Emerging Technologies: Combining spinning with technologies like additive manufacturing, laser processing, and artificial intelligence could unlock new possibilities for bellows design and performance.
Conclusion
The technology of spinning in the manufacture of metal bellows represents a critical intersection of precision engineering, materials science, and advanced manufacturing. By producing seamless tubular preforms with high dimensional accuracy and material uniformity, spinning enables the creation of bellows that meet the stringent requirements of industries such as aerospace, medical devices, semiconductors, and oil and gas. While spinning offers significant advantages in terms of reliability, fatigue resistance, and cost-effectiveness in high-volume production, it also faces challenges related to tooling costs, material limitations, and process complexity.
Through ongoing advancements in CNC technology, finite element analysis, hybrid manufacturing, and smart manufacturing, spinning continues to evolve, offering new opportunities for innovation in bellows design and production. The detailed comparisons provided in this article highlight the unique strengths of spinning-based seamless bellows compared to edge-welded, electroformed, and seam-welded methods, providing a valuable resource for engineers and manufacturers. As industries demand increasingly sophisticated and reliable components, the role of spinning in bellows manufacturing is poised to grow, driving advancements in technology and performance for years to come.
Maximize Tooling and CNC Metal Spinning Capabilities.
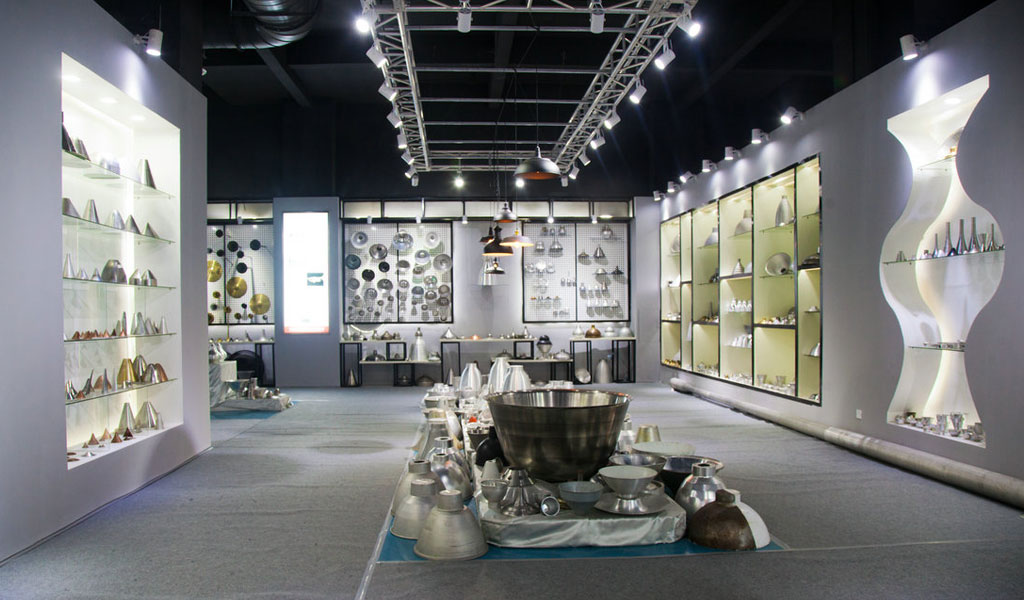
At BE-CU China Metal Spinning company, we make the most of our equipment while monitoring signs of excess wear and stress. In addition, we look into newer, modern equipment and invest in those that can support or increase our manufacturing capabilities. Our team is very mindful of our machines and tools, so we also routinely maintain them to ensure they don’t negatively impact your part’s quality and productivity.
Talk to us today about making a rapid prototype with our CNC metal spinning service. Get a direct quote by chatting with us here or request a free project review.
BE-CU China CNC Metal Spinning service include : CNC Metal Spinning,Metal Spinning Die,Laser Cutting, Tank Heads Spinning,Metal Hemispheres Spinning,Metal Cones Spinning,Metal Dish-Shaped Spinning,Metal Trumpet Spinning,Metal Venturi Spinning,Aluminum Spinning Products,Stainless Steel Spinning Products,Copper Spinning Products,Brass Spinning Products,Steel Spinning Product,Metal Spinnin LED Reflector,Metal Spinning Pressure Vessel,