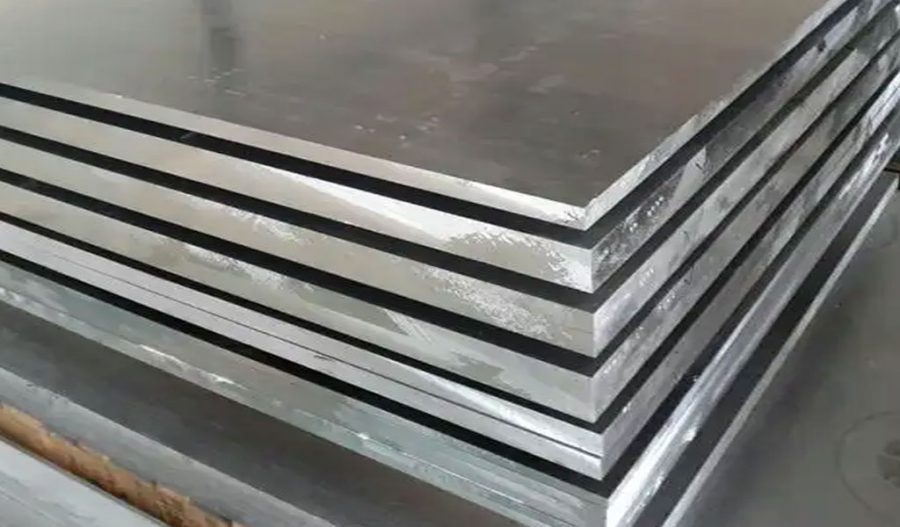
Textured aluminum sheet metal is a versatile and widely utilized material in various industries, ranging from architecture and automotive manufacturing to aerospace engineering and consumer goods production. Characterized by its distinctive surface patterns, enhanced mechanical properties, and aesthetic appeal, textured aluminum sheet metal represents a specialized form of aluminum that has undergone specific processing techniques to achieve its unique physical and chemical attributes. This article provides an in-depth exploration of textured aluminum sheet metal, delving into its composition, manufacturing processes, types, properties, applications, and comparative analyses with other materials. Through a detailed scientific lens, we aim to elucidate the significance of this material in modern engineering and design contexts.
Aluminum, a lightweight, durable, and corrosion-resistant metal, serves as the foundational material for textured sheet metal. With an atomic number of 13 and a position in group 13 of the periodic table, aluminum is abundant in the Earth’s crust, primarily extracted from bauxite ore via the Bayer process followed by the Hall-Héroult electrolytic process. Its intrinsic properties—such as a density of approximately 2.7 g/cm³, a melting point of 660.32°C, and a high strength-to-weight ratio—make it an ideal candidate for further modification into textured forms. The addition of texture enhances both its functional and decorative qualities, allowing it to meet diverse industrial demands.
Composition and Alloying of Aluminum for Textured Sheets
Textured aluminum sheet metal is typically produced from aluminum alloys rather than pure aluminum, as alloying improves its mechanical strength, ductility, and resistance to environmental degradation. The Aluminum Association classifies aluminum alloys into wrought and cast categories, with wrought alloys being the primary type used for sheet metal applications. These alloys are further divided into series based on their primary alloying elements:
- 1xxx Series: Comprising nearly pure aluminum (99% or higher purity), this series is soft, highly ductile, and corrosion-resistant but lacks significant strength. It is infrequently used for textured sheets unless aesthetic qualities are the sole priority.
- 2xxx Series: Copper is the primary alloying element, providing high strength and excellent machinability. These alloys, such as 2024, are common in aerospace applications but are less corrosion-resistant unless coated.
- 3xxx Series: Manganese alloys, such as 3003, offer moderate strength and good formability, making them suitable for general-purpose textured sheets.
- 5xxx Series: Magnesium alloys, like 5052, exhibit excellent corrosion resistance and weldability, ideal for marine and architectural applications.
- 6xxx Series: Combining magnesium and silicon, alloys like 6061 provide a balance of strength, formability, and corrosion resistance, widely used in structural textured sheets.
- 7xxx Series: Zinc-based alloys, such as 7075, are among the strongest aluminum alloys, employed in high-stress environments like aerospace but require protective finishes due to lower corrosion resistance.
The choice of alloy influences the texture’s effectiveness, as alloy composition affects how the metal responds to mechanical or chemical texturing processes. Minor elements such as iron, silicon, and chromium may also be present, either as impurities or intentional additives, to refine grain structure or enhance specific properties.
Manufacturing Processes for Textured Aluminum Sheet Metal
The production of textured aluminum sheet metal involves a multi-step process that begins with the creation of flat aluminum sheets through rolling, followed by the application of texture via specialized techniques. Below, we explore these processes in detail:
- Rolling: Aluminum ingots are heated and passed through rollers to reduce thickness and achieve a uniform sheet. Hot rolling occurs above the recrystallization temperature (typically 300–500°C), while cold rolling at room temperature enhances strength through work hardening. Sheet thicknesses for textured applications generally range from 0.2 mm to 6 mm, depending on the intended use.
- Texturing Techniques:
- Mechanical Texturing: This involves physical deformation of the surface using tools such as embossing rolls, stamping dies, or abrasive blasting. Embossing, for instance, uses patterned rollers to imprint designs like diamond, stucco, or hammer-tone patterns onto the sheet. Abrasive blasting employs high-pressure particles (e.g., sand or glass beads) to create a matte or satin finish.
- Chemical Texturing: Etching with acids or alkalis (e.g., hydrochloric acid or sodium hydroxide) selectively removes material to produce patterns or roughness. This method is precise but requires careful control to avoid over-etching.
- Electrochemical Texturing: Anodizing, an electrolytic process, can create micro-textured surfaces while enhancing corrosion resistance. The aluminum acts as an anode in an acidic electrolyte, forming a porous oxide layer that can be dyed or sealed.
- Laser Texturing: Advanced laser systems ablate or melt the surface to create intricate patterns with high precision. This method is costly but allows for complex, repeatable designs suited to niche applications.
- Finishing: Post-texturing, sheets may undergo cleaning, polishing, or coating (e.g., powder coating, painting, or lacquering) to enhance durability or aesthetics. Anodized finishes are particularly common, increasing surface hardness and resistance to wear.
The choice of texturing method depends on factors such as desired pattern complexity, production volume, and cost constraints. Mechanical texturing dominates mass production due to its scalability, while laser and electrochemical methods cater to high-precision or decorative needs.
Types of Textures in Aluminum Sheet Metal
Textured aluminum sheet metal is available in a variety of patterns, each imparting distinct functional and visual characteristics. Common textures include:
- Diamond Plate: Featuring raised, diamond-shaped ridges, this texture enhances slip resistance and is prevalent in flooring, truck beds, and industrial walkways.
- Stucco: Resembling a pebbled or hammered surface, stucco-textured aluminum diffuses light, reducing glare, and is used in refrigeration panels and wall cladding.
- Hammered: Mimicking the look of hand-hammered metal, this texture offers a rustic aesthetic for decorative applications like furniture or interior design.
- Brushed: Linear scratches or lines created by abrasive belts give a sleek, modern finish, popular in appliances and architectural trim.
- Perforated: Sheets with punched holes provide ventilation or acoustic dampening, used in speaker grilles or ceiling panels.
- Custom Patterns: Laser or chemical texturing enables bespoke designs, such as logos or geometric shapes, tailored to specific client needs.
Each texture modifies the sheet’s surface roughness (measured in Ra, or arithmetic average roughness), friction coefficient, and reflectivity, influencing its suitability for particular applications.
Physical and Mechanical Properties
Texturing alters the inherent properties of aluminum sheet metal, often improving its performance in specific contexts. Key properties include:
- Surface Roughness: Textured surfaces increase Ra values (e.g., from 0.1 µm for polished aluminum to 5–50 µm for heavily textured sheets), enhancing grip or adhesion for coatings.
- Strength: Cold rolling and alloying boost tensile strength (e.g., 6061-T6 reaches ~310 MPa), though texturing itself does not significantly alter bulk strength unless deep embossing induces localized strain.
- Corrosion Resistance: Aluminum’s natural oxide layer (Al₂O₃) provides inherent protection, further improved by anodizing or alloying with magnesium. Textured surfaces may trap moisture, necessitating protective finishes in humid environments.
- Thermal Conductivity: Aluminum’s high thermal conductivity (~237 W/m·K for pure aluminum) remains largely unaffected by surface texture, though thicker oxide layers from anodizing slightly reduce it.
- Reflectivity: Smooth aluminum reflects up to 92% of visible light, while textured surfaces scatter light, reducing reflectivity to 50–70%, depending on pattern depth.
These properties are quantifiable through standardized tests, such as ASTM E8 for tensile strength or ISO 4287 for surface roughness, ensuring consistency across applications.
Applications of Textured Aluminum Sheet Metal
The versatility of textured aluminum sheet metal manifests in its broad range of applications across multiple sectors:
- Architecture: Stucco or brushed textures adorn building facades, roofing, and interior panels, offering durability and visual appeal. Perforated sheets enhance acoustic performance in auditoriums.
- Automotive: Diamond plate textures line truck beds and toolboxes, while lightweight 5xxx series sheets form car body panels, balancing strength and fuel efficiency.
- Aerospace: High-strength 7xxx series textured sheets are used in aircraft fuselages and wings, where surface patterns may reduce drag or improve paint adhesion.
- Consumer Goods: Brushed aluminum features in kitchen appliances (e.g., refrigerators, ovens), combining aesthetics with scratch resistance.
- Industrial: Perforated or diamond-textured sheets serve as conveyor guards, machine enclosures, or anti-slip platforms in factories.
The adaptability of textured aluminum to both structural and decorative roles underscores its importance in modern manufacturing.
Comparative Analysis with Other Materials
To contextualize textured aluminum sheet metal’s utility, a comparison with alternative materials—such as stainless steel, carbon steel, and copper—is warranted. Below are detailed tables summarizing key attributes:
Table 1: Mechanical and Physical Property Comparison
Material | Density (g/cm³) | Tensile Strength (MPa) | Corrosion Resistance | Thermal Conductivity (W/m·K) | Cost (Relative) |
---|---|---|---|---|---|
Textured Aluminum | 2.7 | 150–700 (alloy-dependent) | High (with coating) | 237 | Moderate |
Stainless Steel | 7.8 | 500–1000 | Very High | 16–20 | High |
Carbon Steel | 7.85 | 400–1200 | Low (requires coating) | 50 | Low |
Copper | 8.96 | 200–400 | High (patina forms) | 401 | Very High |
Table 2: Application Suitability Comparison
Application | Textured Aluminum | Stainless Steel | Carbon Steel | Copper |
---|---|---|---|---|
Architectural Cladding | High (lightweight, aesthetic) | High (durability) | Moderate (weight) | High (aesthetic) |
Automotive Panels | High (weight savings) | Moderate (cost) | High (strength) | Low (cost) |
Aerospace Structures | High (strength-to-weight) | Low (weight) | Low (weight) | Low (weight) |
Consumer Appliances | High (cost-effective) | High (premium look) | Low (corrosion) | Moderate |
Aluminum’s lower density provides a significant advantage in weight-sensitive applications, while its moderate cost and ease of texturing make it competitive against heavier or pricier alternatives. Stainless steel excels in corrosion resistance and strength but is less practical for lightweight designs. Carbon steel offers superior strength at a lower cost but requires extensive corrosion protection. Copper, though highly conductive and visually striking, is prohibitively expensive for large-scale use.
Environmental and Economic Considerations
The production of textured aluminum sheet metal aligns with sustainability goals due to aluminum’s recyclability. Approximately 75% of all aluminum ever produced remains in use, as it can be melted and reformed with minimal loss of quality. Recycling consumes only 5% of the energy required for primary production (20.6 MJ/kg vs. 211 MJ/kg), reducing greenhouse gas emissions. However, texturing processes—particularly chemical or laser methods—may introduce environmental challenges, such as waste acid disposal or energy-intensive equipment operation.
Economically, textured aluminum balances initial material costs (e.g., $2–$5/kg depending on alloy and texture complexity) with long-term benefits like reduced maintenance and extended service life. Market demand, driven by construction and transportation sectors, continues to grow, with global aluminum sheet production exceeding 65 million metric tons annually as of 2023.
Future Trends and Innovations
Advancements in texturing technology promise to expand the capabilities of aluminum sheet metal. Nano-texturing, achieved through precision laser or plasma processes, could enhance hydrophobicity or antibacterial properties, opening applications in medical devices or water-repellent surfaces. Additive manufacturing (3D printing) of aluminum with integrated textures may also emerge, allowing for custom, single-step production of complex components. Additionally, the integration of smart coatings—responsive to temperature or light—could pair with textured surfaces to create adaptive materials for next-generation engineering.
Conclusion
Textured aluminum sheet metal exemplifies the synergy of material science, engineering, and design. Its diverse textures, robust properties, and wide-ranging applications position it as a cornerstone of modern industry. Through ongoing innovation and refinement, this material will likely continue to evolve, meeting the challenges of sustainability, performance, and aesthetics in an increasingly demanding technological landscape.
Maximize Tooling and CNC Metal Spinning Capabilities.
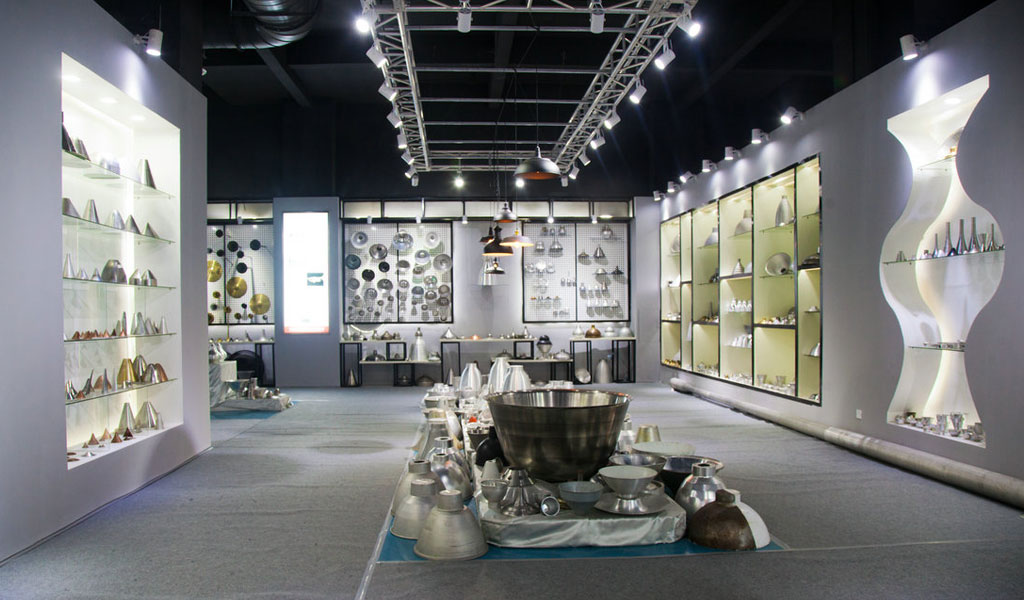
At BE-CU China Metal Spinning company, we make the most of our equipment while monitoring signs of excess wear and stress. In addition, we look into newer, modern equipment and invest in those that can support or increase our manufacturing capabilities. Our team is very mindful of our machines and tools, so we also routinely maintain them to ensure they don’t negatively impact your part’s quality and productivity.
Talk to us today about making a rapid prototype with our CNC metal spinning service. Get a direct quote by chatting with us here or request a free project review.
BE-CU China CNC Metal Spinning service include : CNC Metal Spinning,Metal Spinning Die,Laser Cutting, Tank Heads Spinning,Metal Hemispheres Spinning,Metal Cones Spinning,Metal Dish-Shaped Spinning,Metal Trumpet Spinning,Metal Venturi Spinning,Aluminum Spinning Products,Stainless Steel Spinning Products,Copper Spinning Products,Brass Spinning Products,Steel Spinning Product,Metal Spinnin LED Reflector,Metal Spinning Pressure Vessel,