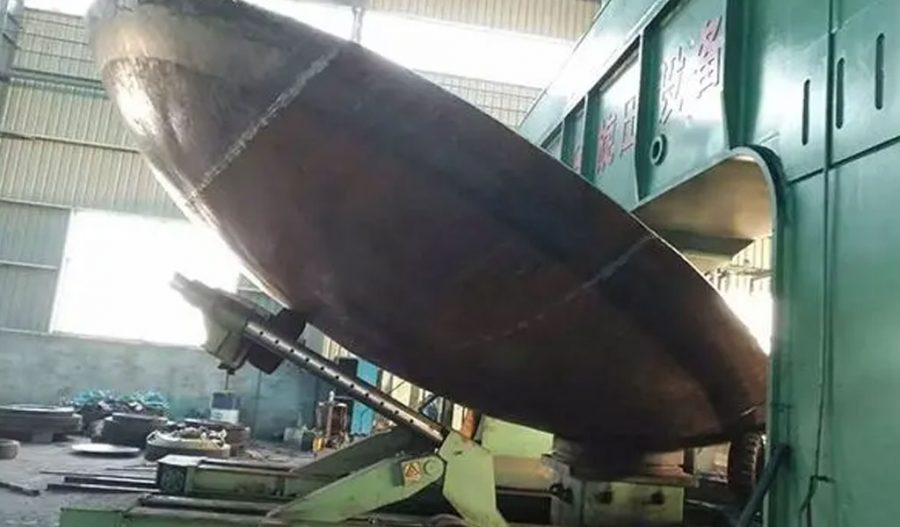
Cold spinning is a metalworking process that involves shaping a metal blank into a desired form by rotating it at high speeds while applying pressure through rollers or mandrels. This process is particularly useful for manufacturing components with rotational symmetry, such as elliptical heads, which are commonly used in pressure vessels, tanks, and other industrial applications. The thinning effect induced by cold spinning processing has significant implications for the mechanical properties of elliptical heads, particularly their strength. This article delves into the intricate relationship between cold spinning processing thinning and the strength of elliptical heads, exploring the underlying mechanisms, material behavior, and engineering considerations.
Introduction to Cold Spinning
Cold spinning, also known as flow forming or shear forming, is a cold working process that transforms a metal blank into a desired shape through plastic deformation. The process involves rotating the workpiece at high speeds while applying pressure through rollers or mandrels, which gradually reduce the thickness of the material and elongate it to form the desired shape. Unlike hot spinning, cold spinning is performed at room temperature, which eliminates the need for heating and cooling cycles, making it more efficient and cost-effective.
The primary advantage of cold spinning is its ability to produce components with high dimensional accuracy and excellent surface finish. The process also enhances the mechanical properties of the material by inducing work hardening, which increases the strength and hardness of the final product. However, the thinning effect associated with cold spinning can have complex implications for the strength of elliptical heads, requiring a detailed understanding of the material behavior and processing parameters.
Mechanisms of Cold Spinning Processing Thinning
The thinning effect in cold spinning is a result of the plastic deformation of the material as it is stretched and compressed by the rollers or mandrels. During the spinning process, the material undergoes significant shear deformation, which leads to a reduction in thickness and an increase in length. The extent of thinning depends on various factors, including the material properties, spinning speed, feed rate, and the geometry of the rollers or mandrels.
The thinning process can be described by the following mechanisms:
- Plastic Deformation: The primary mechanism of thinning in cold spinning is plastic deformation, where the material is permanently deformed beyond its elastic limit. The applied pressure from the rollers or mandrels causes the material to flow and elongate, resulting in a reduction in thickness.
- Work Hardening: As the material undergoes plastic deformation, it experiences work hardening, which increases its strength and hardness. Work hardening is a result of the dislocation movement and multiplication within the material’s crystal structure, which creates obstacles to further deformation.
- Residual Stresses: The thinning process also introduces residual stresses within the material. These stresses arise from the non-uniform deformation and can affect the mechanical properties of the final product. Residual stresses can be either compressive or tensile, depending on the processing parameters and material behavior.
- Microstructural Changes: The cold spinning process can induce microstructural changes in the material, such as grain refinement and phase transformations. These changes can enhance the material’s strength and toughness but may also introduce defects such as microcracks or voids.
Effect of Thinning on the Strength of Elliptical Heads
The strength of elliptical heads is a critical consideration in their design and manufacture, as they are often subjected to high pressures and loads in industrial applications. The thinning effect induced by cold spinning processing has a significant impact on the strength of elliptical heads, which can be analyzed through various mechanical properties and failure modes.
- Yield Strength and Ultimate Tensile Strength: The yield strength and ultimate tensile strength of elliptical heads are directly influenced by the thinning effect. As the material undergoes work hardening during the spinning process, its yield strength and ultimate tensile strength increase. This enhancement in strength is beneficial for the performance of elliptical heads, as it allows them to withstand higher pressures and loads without failure.
- Fatigue Strength: The fatigue strength of elliptical heads is also affected by the thinning effect. Fatigue failure occurs due to the cyclic loading and unloading of the material, which can lead to the initiation and propagation of cracks. The residual stresses introduced during the thinning process can influence the fatigue strength of elliptical heads. Compressive residual stresses can improve fatigue strength by inhibiting crack initiation and propagation, while tensile residual stresses can have the opposite effect.
- Fracture Toughness: The fracture toughness of elliptical heads is a measure of their resistance to crack propagation under static loading conditions. The thinning effect can enhance fracture toughness by inducing grain refinement and work hardening, which create obstacles to crack propagation. However, the presence of microcracks or voids introduced during the spinning process can reduce fracture toughness and increase the risk of brittle failure.
- Creep Strength: Creep strength is a critical consideration for elliptical heads operating at elevated temperatures, where the material can deform over time under constant load. The thinning effect can influence creep strength by altering the material’s microstructure and introducing residual stresses. Work hardening and grain refinement can improve creep strength, while the presence of defects can accelerate creep deformation and failure.
Engineering Considerations for Cold Spinning of Elliptical Heads
The design and manufacture of elliptical heads through cold spinning require careful consideration of various engineering factors to optimize their strength and performance. These factors include material selection, processing parameters, and quality control measures.
- Material Selection: The choice of material is crucial for the strength and performance of elliptical heads. Materials with high ductility and work hardening capability, such as stainless steel, aluminum alloys, and titanium alloys, are suitable for cold spinning. These materials can undergo significant plastic deformation without failure, resulting in enhanced strength and dimensional accuracy.
- Processing Parameters: The processing parameters, including spinning speed, feed rate, and roller geometry, play a critical role in determining the thinning effect and the resulting mechanical properties of elliptical heads. Optimizing these parameters can minimize defects, such as microcracks and residual stresses, and enhance the strength and performance of the final product.
- Quality Control Measures: Quality control measures are essential for ensuring the consistency and reliability of elliptical heads manufactured through cold spinning. Non-destructive testing techniques, such as ultrasonic testing and radiographic testing, can be used to detect defects and ensure the integrity of the final product. Additionally, mechanical testing, including tensile testing and fatigue testing, can be employed to evaluate the strength and performance of elliptical heads.
Case Studies and Experimental Investigations
Several case studies and experimental investigations have been conducted to understand the effect of cold spinning processing thinning on the strength of elliptical heads. These studies provide valuable insights into the material behavior, processing parameters, and mechanical properties of elliptical heads manufactured through cold spinning.
- Case Study on Stainless Steel Elliptical Heads: A case study on the cold spinning of stainless steel elliptical heads revealed that the thinning effect significantly enhanced the yield strength and ultimate tensile strength of the material. The study also found that optimizing the spinning speed and feed rate minimized the formation of microcracks and residual stresses, resulting in improved fatigue strength and fracture toughness.
- Experimental Investigation on Aluminum Alloy Elliptical Heads: An experimental investigation on the cold spinning of aluminum alloy elliptical heads demonstrated that the thinning effect induced grain refinement and work hardening, which enhanced the material’s strength and toughness. The study also highlighted the importance of post-processing heat treatment to relieve residual stresses and improve the dimensional stability of the final product.
- Comparative Analysis of Titanium Alloy Elliptical Heads: A comparative analysis of titanium alloy elliptical heads manufactured through cold spinning and conventional machining revealed that the cold-spun heads exhibited superior strength and fatigue resistance. The study attributed these improvements to the work hardening and microstructural changes induced by the thinning effect during the spinning process.
Future Directions and Research Opportunities
The effect of cold spinning processing thinning on the strength of elliptical heads is a complex and multifaceted topic that warrants further investigation. Future research should focus on the following areas to advance the understanding and application of cold spinning in the manufacture of elliptical heads:
- Advanced Materials: Exploring the cold spinning of advanced materials, such as high-strength steels, composite materials, and functionally graded materials, can open new avenues for the manufacture of high-performance elliptical heads. These materials offer unique properties and challenges that require innovative processing techniques and quality control measures.
- Hybrid Manufacturing Techniques: Combining cold spinning with other manufacturing techniques, such as additive manufacturing and heat treatment, can enhance the strength and performance of elliptical heads. Hybrid manufacturing techniques can leverage the advantages of multiple processes to achieve optimal material properties and dimensional accuracy.
- Numerical Simulations: Developing numerical simulations and finite element models to predict the thinning effect and mechanical properties of elliptical heads can provide valuable insights for process optimization and design. These simulations can account for various processing parameters, material behaviors, and failure modes, enabling the development of robust and reliable elliptical heads.
- Sustainability and Environmental Impact: Investigating the sustainability and environmental impact of cold spinning processing can contribute to the development of eco-friendly manufacturing practices. Optimizing the energy consumption, waste generation, and resource utilization of the cold spinning process can reduce its environmental footprint and promote sustainable manufacturing.
Conclusion
The effect of cold spinning processing thinning on the strength of elliptical heads is a critical consideration in their design and manufacture. The thinning effect induced by cold spinning involves complex mechanisms, including plastic deformation, work hardening, residual stresses, and microstructural changes, which significantly influence the mechanical properties of elliptical heads. Understanding these mechanisms and their implications for the strength and performance of elliptical heads is essential for optimizing the cold spinning process and ensuring the reliability and safety of the final product.
Future research should focus on exploring advanced materials, hybrid manufacturing techniques, numerical simulations, and sustainability considerations to advance the understanding and application of cold spinning in the manufacture of elliptical heads. By addressing these areas, engineers and researchers can develop innovative solutions that enhance the strength, performance, and environmental sustainability of elliptical heads, contributing to the advancement of industrial applications and manufacturing technologies.
Maximize Tooling and CNC Metal Spinning Capabilities.
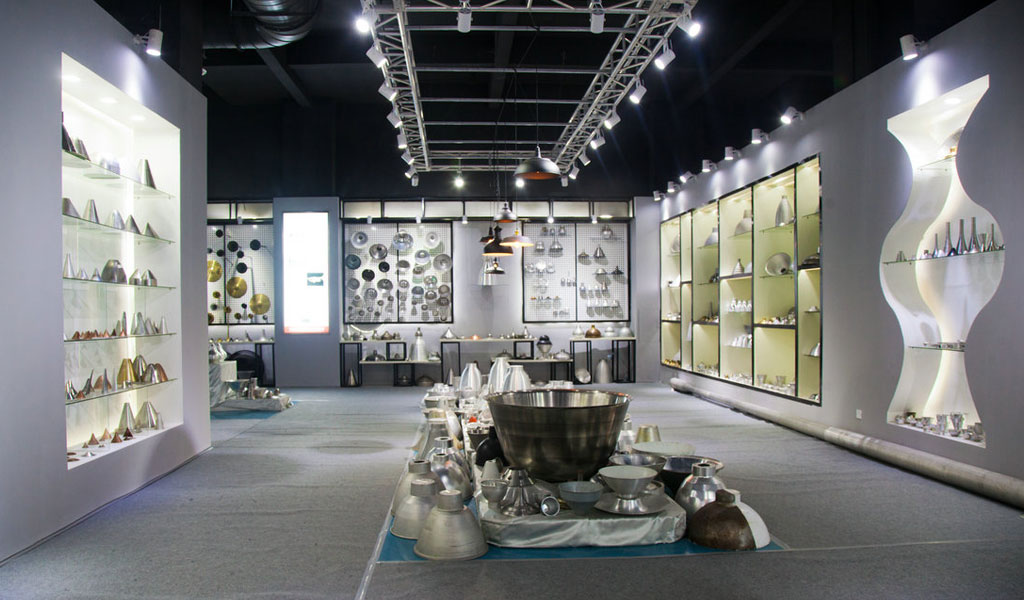
At BE-CU China Metal Spinning company, we make the most of our equipment while monitoring signs of excess wear and stress. In addition, we look into newer, modern equipment and invest in those that can support or increase our manufacturing capabilities. Our team is very mindful of our machines and tools, so we also routinely maintain them to ensure they don’t negatively impact your part’s quality and productivity.
Talk to us today about making a rapid prototype with our CNC metal spinning service. Get a direct quote by chatting with us here or request a free project review.
BE-CU China CNC Metal Spinning service include : CNC Metal Spinning,Metal Spinning Die,Laser Cutting, Tank Heads Spinning,Metal Hemispheres Spinning,Metal Cones Spinning,Metal Dish-Shaped Spinning,Metal Trumpet Spinning,Metal Venturi Spinning,Aluminum Spinning Products,Stainless Steel Spinning Products,Copper Spinning Products,Brass Spinning Products,Steel Spinning Product,Metal Spinnin LED Reflector,Metal Spinning Pressure Vessel,