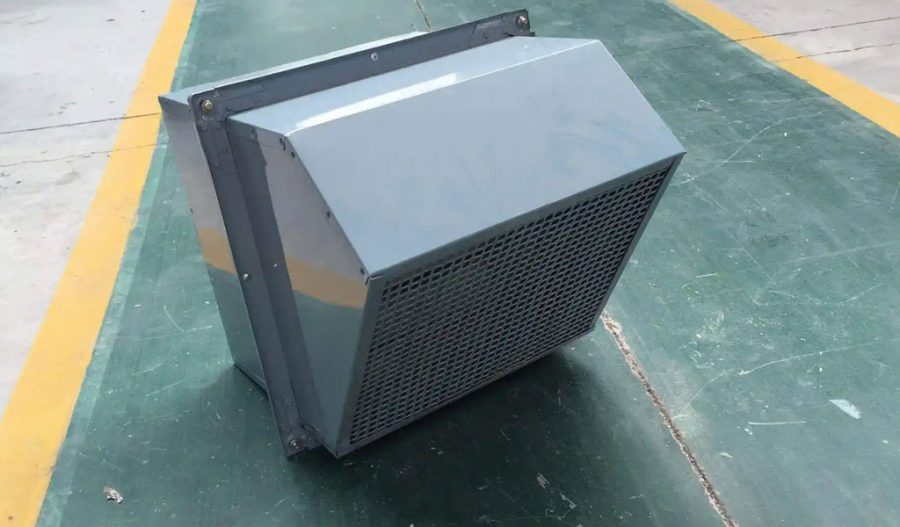
Metal spinning, also known as spin forming or metal turning, is a metalworking process that transforms a flat metal disc or tube into axially symmetric parts through high-speed rotation and localized plastic deformation. This ancient technique, with roots traceable to Ancient Egypt, has evolved into a sophisticated manufacturing method used across industries such as aerospace, automotive, and defense. A critical yet often underexplored aspect of metal spinning is shell nosing, a specialized process that involves forming the open end of a spun metal shell into a tapered, rounded, or otherwise contoured shape. Shell nosing enhances the structural integrity, functionality, and aesthetic appeal of spun components, making it a pivotal operation in the production of high-precision parts like artillery shells, rocket nose cones, and pressure vessels.
This article delves into the multifaceted importance of shell nosing in metal spinning, exploring its historical context, technical principles, material considerations, process parameters, and applications. By examining recent advancements, failure modes, and comparative analyses, the article aims to provide a comprehensive understanding of shell nosing’s role in modern manufacturing. Detailed tables and scientific sections will facilitate a rigorous exploration of the topic, ensuring clarity for both general readers and technical experts.
Historical Context of Shell Nosing
Origins in Metal Spinning
Metal spinning has been practiced for millennia, with early artisans using manual techniques to shape soft metals like copper and bronze. The process gained industrial significance in the 19th century with the advent of steam and electric power, enabling the production of more complex geometries. Shell nosing, as a subset of metal spinning, emerged as a critical technique for forming the ends of cylindrical or conical shells, particularly in military applications. During the Crimean War (1853–1856), wrought-iron artillery shells were produced using a combination of spinning and hammering to achieve bottle-like shapes, a precursor to modern shell nosing techniques.
Evolution of Shell Nosing
By the early 20th century, shell nosing became integral to the production of munitions, as the tapered nose of a shell improved aerodynamic performance and structural resilience. The development of computer numerical control (CNC) technology in the 1970s revolutionized shell nosing, allowing for precise control over toolpaths and process parameters. Today, shell nosing is employed in both conventional and advanced spinning processes, including hot spinning for difficult-to-deform alloys and mandrel-free spinning for non-axisymmetric shapes.
Technical Principles of Shell Nosing
Definition and Process Overview
Shell nosing is the process of shaping the open end of a spun metal shell to achieve a specific geometry, such as a hemispherical, ogival, or tapered profile. The process typically involves a rotating workpiece clamped against a mandrel, with one or more rollers applying localized force to deform the material. Unlike general spinning, which focuses on forming the entire workpiece, shell nosing targets the edge or mouth, often requiring precise control to avoid defects like cracking or wrinkling.
The process can be performed hot or cold, depending on the material and desired outcome. Cold shell nosing, for instance, is common for ductile metals like aluminum, while hot shell nosing is used for high-strength alloys like nickel-based superalloys. The choice of mandrel (solid or segmented) and tooling (roller geometry, nose radius) significantly influences the final shape and material properties.
Mechanics of Deformation
Shell nosing induces complex stress and strain states in the workpiece, combining tensile, compressive, and shear forces. The material undergoes plastic deformation as the roller compresses the shell’s edge, causing it to flow inward or outward depending on the desired contour. The Bauschinger effect, where prior plastic deformation reduces tensile strength, is a critical consideration in shell nosing, as it can lead to brittle fracture if not managed properly.
Finite element analysis (FEA) models, such as those implemented in ANSYS Mechanical APDL or MSC Simufact.Forming, are widely used to simulate shell nosing. These models reveal that shell elements may struggle to capture the nuanced deformation behavior, necessitating advanced modeling techniques like solid elements or adaptive meshing. Experimental validation, often involving strain gauges or optical measurement systems, confirms the accuracy of these simulations.
Process Parameters
Key process parameters in shell nosing include:
- Mandrel Speed: Typically ranging from 300 to 1000 rpm, mandrel speed affects frictional heat and material flow. Higher speeds reduce forming forces but may increase surface defects.
- Feed Rate: The roller’s axial or radial advancement, measured in mm/rev, influences deformation uniformity. Optimal feed rates (e.g., 0.5–2 mm/rev) minimize wrinkling.
- Roller Geometry: The roller’s nose radius and angle of attack determine contact pressure and material flow. A larger nose radius (e.g., 6 mm) reduces stress concentrations.
- Temperature: For hot spinning, temperatures range from 0.7 to 0.9 of the material’s homologous temperature to enhance formability.
- Reduction Ratio: The degree of diameter reduction per pass affects strain distribution and defect formation. Multi-pass nosing often employs incremental reductions to prevent failure.
These parameters are optimized through experimental trials and numerical simulations, balancing formability, surface finish, and mechanical properties.
Material Considerations in Shell Nosing
Material Selection
The choice of material for shell nosing depends on the application, with common choices including:
- Aluminum Alloys: Annealed aluminum (e.g., AL-1050) offers excellent ductility, achieving limiting spinning ratios (LSRs) up to 2.40 in deep spinning. Hard aluminum is less formable but provides higher strength.
- Steels: Q235 steel, used in cylindrical shells, balances cost and formability. High-strength steels like AISI 4340 are employed in demanding applications like gears.
- Superalloys: Nickel-based superalloys (e.g., Inconel) and titanium alloys are used in aerospace for their high strength-to-weight ratios but require hot spinning due to low ductility.
- Magnesium Alloys: Lightweight magnesium alloys are gaining traction for automotive applications, though their formability is limited without elevated temperatures.
Material Behavior
Material behavior during shell nosing is governed by its microstructure, anisotropy, and strain-hardening characteristics. For instance, aluminum exhibits isotropic behavior in annealed states but may show anisotropy in rolled sheets, affecting springback and shape accuracy. Superalloys, with their complex grain structures, are prone to grain size evolution during hot spinning, impacting formability and fatigue resistance.
Plastic deformation-induced embrittlement (PDIE) is a critical concern, particularly in cold shell nosing. PDIE reduces tensile strength due to accumulated compressive strains, increasing the risk of brittle fracture. Two indicators—critical PDIE value and allowable tensile strength—are used to predict fracture likelihood. When the maximum principal stress exceeds the allowable tensile strength and PDIE surpasses the critical value, brittle fracture is imminent.
Table 1: Material Properties for Shell Nosing
Material | Yield Strength (MPa) | Ultimate Tensile Strength (MPa) | Elongation (%) | Formability (LSR) | Common Applications |
---|---|---|---|---|---|
Annealed Aluminum | 30–50 | 80–120 | 30–40 | 2.40 | Rocket nose cones, cookware |
Hard Aluminum | 100–150 | 150–200 | 15–20 | 2.24 | Structural components |
Q235 Steel | 235 | 370–500 | 20–25 | 1.80–2.00 | Cylindrical shells, pipelines |
AISI 4340 Steel | 710 | 860–1000 | 12–15 | 1.60–1.80 | Gears, artillery shells |
Inconel 718 | 1030 | 1240–1400 | 10–12 | 1.50–1.70 | Jet engine components |
Magnesium AZ31 | 150 | 240–290 | 10–15 | 1.60–1.80 | Automotive parts |
Note: LSR values are for deep spinning with optimized parameters.
Importance of Shell Nosing in Metal Spinning
Structural Enhancement
Shell nosing significantly enhances the structural integrity of spun components. By tapering or rounding the open end, nosing reduces stress concentrations that could lead to crack initiation. For example, in artillery shells, the ogival nose improves resistance to impact and pressure loads, extending service life. In pressure vessels, nosing ensures uniform wall thickness at the mouth, preventing localized thinning during pressurization.
The process also induces compressive residual stresses, enhancing fatigue resistance. Vickers hardness tests on spun shells reveal increased hardness at the nosed region, reflecting work-hardening effects that bolster mechanical properties.
Functional Optimization
Shell nosing optimizes the functionality of components by tailoring their geometry to specific requirements. In aerospace, nosed rocket cones improve aerodynamic efficiency, reducing drag and fuel consumption. In automotive applications, nosed connecting rods achieve precise dimensional accuracy, ensuring compatibility with mating components. The ability to form complex contours without machining the inner surface preserves material integrity and reduces production costs.
Aesthetic and Finishing Benefits
Nosing enhances the aesthetic appeal of spun parts, producing smooth, polished surfaces suitable for decorative applications. For instance, in lighting fixtures, nosed edges create seamless transitions that enhance visual appeal. Post-processing techniques like planishing and trimming, often paired with nosing, further improve surface finish, meeting stringent industry standards.
Economic Advantages
Shell nosing offers economic benefits by minimizing material waste and tooling costs. Unlike die-stamping, which requires dedicated molds, nosing uses flexible tooling that can be adapted to various geometries. The process’s low forming forces reduce energy consumption, and CNC automation enables high repeatability, making it cost-effective for both low- and high-volume production.
Applications of Shell Nosing
Aerospace and Defense
Shell nosing is indispensable in aerospace and defense, where precision and reliability are paramount. Rocket nose cones, jet engine components, and missile casings rely on nosing to achieve aerodynamic profiles and structural robustness. For example, Inconel 718 nose cones are hot-spun to withstand extreme temperatures and mechanical loads during flight.
Artillery shells, a historical application of nosing, benefit from the process’s ability to form complex ogival shapes from a single piece of material. This eliminates welds, reducing failure points and enhancing ballistic performance.
Automotive Industry
In the automotive sector, shell nosing is used to produce lightweight, high-strength components like connecting rods, fuel tank caps, and exhaust system parts. Magnesium alloys, formed via hot spinning, offer weight savings critical for fuel efficiency. The process’s scalability supports high-volume production, meeting the industry’s demand for cost-effective solutions.
Industrial and Consumer Goods
Shell nosing is employed in the production of pressure vessels, gas cylinders, and cookware, where seamless geometries and uniform wall thickness are essential. Decorative items, such as lampshades and urns, leverage nosing for aesthetic precision. The process’s versatility accommodates a wide range of materials and shapes, from small-scale pins to large-diameter tanks.
Failure Modes in Shell Nosing
Common Defects
Shell nosing is susceptible to several failure modes, including:
- Wrinkling: Excessive compressive stresses in the flange cause buckling, particularly at high feed rates or low mandrel speeds.
- Tearing: Tensile stresses exceeding the material’s ultimate strength lead to cracks, often at the nosed edge.
- Brittle Fracture: PDIE-induced embrittlement, exacerbated by the Bauschinger effect, causes unexpected fractures in cold nosing.
- Flange Jamming: Improper roller trajectories or excessive reduction ratios trap material, halting the process.
- Wall Fracture: Localized thinning during multi-pass nosing can result in wall rupture, especially in hard materials.
Mitigation Strategies
Mitigating these defects requires careful process design:
- Optimized Toolpaths: Convex toolpaths minimize thinning and tool forces, reducing tearing risks.
- Incremental Reductions: Multi-pass nosing with small reduction ratios prevents wrinkling and jamming.
- Temperature Control: Hot spinning enhances formability, reducing brittle fracture risks in superalloys.
- Lubrication: Proper lubrication reduces friction and heat, minimizing surface defects and wear.
Table 2: Failure Modes and Mitigation Strategies
Failure Mode | Cause | Mitigation Strategy | Reference |
---|---|---|---|
Wrinkling | High feed rate, low mandrel speed | Reduce feed rate, increase mandrel speed | |
Tearing | Excessive tensile stress | Use convex toolpaths, reduce reduction ratio | |
Brittle Fracture | PDIE, Bauschinger effect | Hot spinning, monitor PDIE indicators | |
Flange Jamming | Improper roller trajectory | Optimize roller path, incremental reductions | |
Wall Fracture | Localized thinning | Multi-pass nosing, monitor thickness |
Recent Advancements in Shell Nosing
Automation and CNC Integration
The integration of CNC technology has transformed shell nosing, enabling precise control over roller movements and process parameters. Modern spinning machines, equipped with servomotors and real-time feedback systems, achieve tolerances as low as ±0.1 mm. Haptic systems, which record craftsman-designed toolpaths, combine manual expertise with automation, improving productivity without sacrificing quality.
Non-Axisymmetric and Mandrel-Free Nosing
Recent developments in mandrel-free spinning have expanded shell nosing’s capabilities, allowing the formation of non-axisymmetric geometries. Numerically controlled rollers replace traditional mandrels, reducing lead times and tooling costs. FEA models have validated the stress and strain distributions in these processes, confirming their viability for complex shapes.
Hot Spinning for Lightweight Alloys
Hot spinning has gained prominence for forming difficult-to-deform lightweight alloys like AA7075 and magnesium AZ31. Studies show that optimal spinning temperatures (e.g., 0.8 homologous temperature) and roller nose radii (e.g., 6 mm) improve surface straightness and formability. These advancements are critical for aerospace and automotive applications, where weight reduction is a priority.
Intelligent Design and Optimization
Knowledge-based intelligent design systems, coupled with FEA, streamline preform design for shell nosing. These systems automatically transfer CAD models to CAE environments, simulating and modifying designs based on desired shapes. This reduces iterative trial-and-error, enhancing efficiency and accuracy.
Comparative Analysis of Shell Nosing Techniques
Conventional vs. Deep Spinning
Conventional spinning, with its planar roller paths, is suitable for simple geometries but struggles with deep, complex shapes. Deep spinning, aided by blank-holders and roller sets, achieves higher LSRs (e.g., 2.40 vs. 1.75 for annealed aluminum), making it ideal for shell nosing in aerospace components. However, deep spinning increases the risk of flange jamming and requires precise parameter control.
Cold vs. Hot Spinning
Cold spinning is cost-effective and suitable for ductile materials but risks PDIE-induced brittle fracture. Hot spinning enhances formability for superalloys and magnesium alloys, though it requires sophisticated temperature control and increases energy costs. The choice depends on material properties and application requirements.
Mandrel vs. Mandrel-Free Spinning
Mandrel spinning ensures dimensional accuracy but incurs high tooling costs. Mandrel-free spinning, using numerically controlled rollers, offers flexibility for non-axisymmetric shapes and reduces lead times. However, it demands advanced FEA models to predict deformation behavior accurately.
Table 3: Comparison of Shell Nosing Techniques
Technique | Advantages | Disadvantages | Applications | Reference |
---|---|---|---|---|
Conventional Spinning | Simple setup, low cost | Limited to simple shapes, low LSR | Cookware, decorative items | |
Deep Spinning | High LSR, complex geometries | Risk of flange jamming, complex setup | Rocket nose cones, shells | |
Cold Spinning | Cost-effective, high surface finish | Risk of brittle fracture, limited formability | Aluminum components | |
Hot Spinning | High formability, suitable for superalloys | High energy costs, temperature control | Aerospace, automotive parts | |
Mandrel Spinning | High accuracy, repeatable | High tooling costs, limited flexibility | Precision components | |
Mandrel-Free Spinning | Flexible, low tooling costs | Complex control, requires FEA | Non-axisymmetric parts |
Future Directions
Advanced Materials
The development of new lightweight alloys, such as advanced aluminum-lithium and titanium matrix composites, will drive innovations in shell nosing. These materials promise superior strength-to-weight ratios but require tailored spinning parameters to overcome their low ductility.
Digital Twin Technology
Digital twins, integrating real-time process data with FEA models, will enhance shell nosing precision. By simulating and adjusting parameters in real time, digital twins can minimize defects and optimize toolpaths, reducing production costs.
Sustainability
Sustainable manufacturing practices, such as energy-efficient hot spinning and recyclable tooling, will shape the future of shell nosing. Research into bio-based lubricants and low-carbon alloys will further reduce the environmental footprint of the process.
Conclusion
Shell nosing is a cornerstone of metal spinning, enabling the production of high-precision, structurally robust components across diverse industries. Its ability to enhance structural integrity, optimize functionality, and achieve aesthetic excellence underscores its importance in modern manufacturing. By leveraging advancements in automation, material science, and simulation, shell nosing continues to evolve, meeting the demands of increasingly complex applications. As research progresses, the process will likely play a pivotal role in sustainable and innovative manufacturing, solidifying its place as a vital technique in the metalworking arsenal.
Maximize Tooling and CNC Metal Spinning Capabilities.
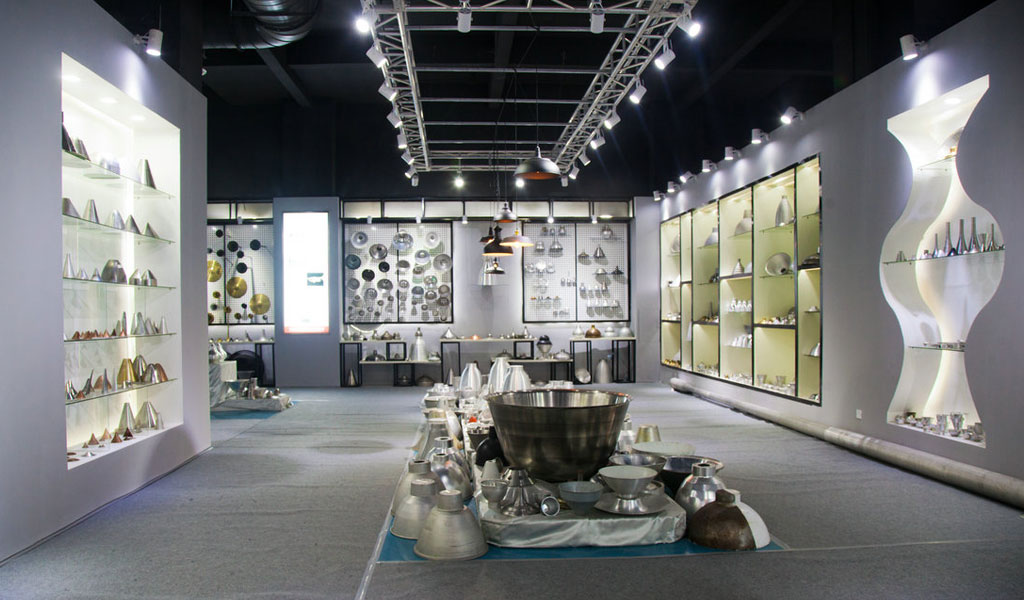
At BE-CU China Metal Spinning company, we make the most of our equipment while monitoring signs of excess wear and stress. In addition, we look into newer, modern equipment and invest in those that can support or increase our manufacturing capabilities. Our team is very mindful of our machines and tools, so we also routinely maintain them to ensure they don’t negatively impact your part’s quality and productivity.
Talk to us today about making a rapid prototype with our CNC metal spinning service. Get a direct quote by chatting with us here or request a free project review.
BE-CU China CNC Metal Spinning service include : CNC Metal Spinning,Metal Spinning Die,Laser Cutting, Tank Heads Spinning,Metal Hemispheres Spinning,Metal Cones Spinning,Metal Dish-Shaped Spinning,Metal Trumpet Spinning,Metal Venturi Spinning,Aluminum Spinning Products,Stainless Steel Spinning Products,Copper Spinning Products,Brass Spinning Products,Steel Spinning Product,Metal Spinnin LED Reflector,Metal Spinning Pressure Vessel,