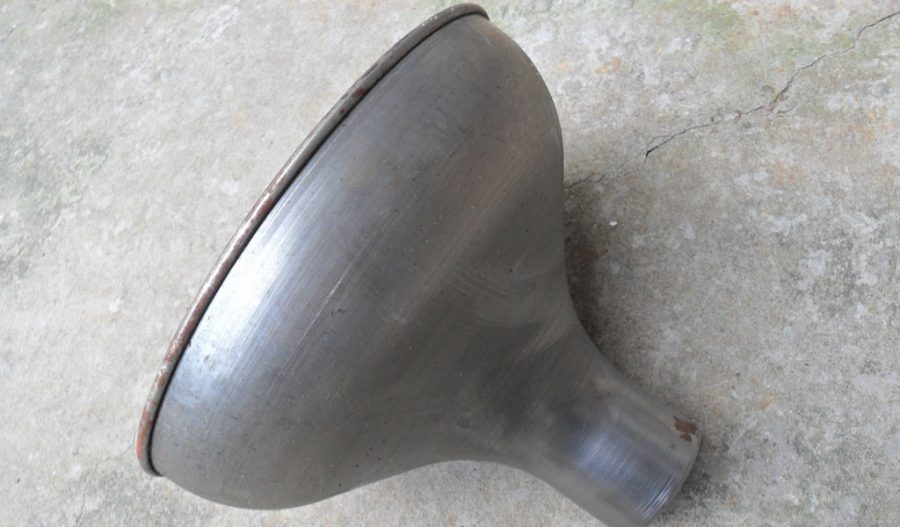
Ball spinning is a metal forming process used to produce thin-walled cylindrical parts, such as those used in aerospace, automotive, and other high-precision industries. The process involves the use of a spinning tool, typically a ball-shaped roller, to deform a metal blank into the desired shape. The quality and precision of the final product are significantly influenced by various process parameters, including the spinning speed, feed rate, tool geometry, and material properties. This article explores the influence of these parameters on the spinning deformation of thin-walled cylindrical parts, providing a comprehensive understanding of the underlying mechanisms and their practical implications.
Introduction to Ball Spinning
Ball spinning, also known as flow forming or shear forming, is a cold forming process that utilizes a rotating mandrel and a spinning tool to deform a metal blank into a cylindrical shape. The process begins with a pre-formed metal blank, which is clamped onto a rotating mandrel. The spinning tool, typically a ball-shaped roller, is then pressed against the blank and moved along its length, causing the material to flow and conform to the shape of the mandrel. This results in a thin-walled cylindrical part with high dimensional accuracy and excellent surface finish.
The ball spinning process offers several advantages over traditional manufacturing methods, such as machining and deep drawing. These include reduced material waste, improved mechanical properties, and the ability to produce complex shapes with high precision. However, the success of the ball spinning process is highly dependent on the careful control of various process parameters, which can significantly affect the deformation behavior and final quality of the spun parts.
Spinning Speed
The spinning speed, or the rotational speed of the mandrel, is a critical parameter that influences the deformation behavior of the metal blank during ball spinning. Higher spinning speeds generally result in increased material flow and reduced forming forces, leading to improved surface finish and dimensional accuracy. However, excessively high spinning speeds can cause excessive heat generation, tool wear, and material defects such as cracking and wrinkling.
Table 1: Influence of Spinning Speed on Deformation Behavior
Spinning Speed (RPM) | Material Flow | Forming Forces | Surface Finish | Dimensional Accuracy | Tool Wear | Material Defects |
---|---|---|---|---|---|---|
500 | Low | High | Fair | Moderate | Low | Minimal |
1000 | Moderate | Moderate | Good | High | Moderate | Minimal |
1500 | High | Low | Excellent | Very High | High | Possible |
2000 | Very High | Very Low | Excellent | Very High | Very High | Likely |
The optimal spinning speed depends on the material properties, tool geometry, and desired part dimensions. For example, aluminum alloys typically require higher spinning speeds compared to steel alloys due to their lower strength and higher ductility. Additionally, the spinning speed should be carefully controlled to avoid excessive heat generation, which can lead to material softening and reduced dimensional accuracy.
Feed Rate
The feed rate, or the rate at which the spinning tool moves along the length of the metal blank, is another important parameter that affects the deformation behavior during ball spinning. A higher feed rate results in increased material flow and reduced forming forces, leading to improved surface finish and dimensional accuracy. However, excessively high feed rates can cause material defects such as wrinkling and thinning, as well as increased tool wear.
Table 2: Influence of Feed Rate on Deformation Behavior
Feed Rate (mm/min) | Material Flow | Forming Forces | Surface Finish | Dimensional Accuracy | Tool Wear | Material Defects |
---|---|---|---|---|---|---|
50 | Low | High | Fair | Moderate | Low | Minimal |
100 | Moderate | Moderate | Good | High | Moderate | Minimal |
150 | High | Low | Excellent | Very High | High | Possible |
200 | Very High | Very Low | Excellent | Very High | Very High | Likely |
The optimal feed rate depends on the material properties, tool geometry, and desired part dimensions. For example, softer materials such as aluminum alloys typically require lower feed rates compared to harder materials such as steel alloys. Additionally, the feed rate should be carefully controlled to avoid material defects such as wrinkling and thinning, which can compromise the structural integrity of the spun parts.
Tool Geometry
The geometry of the spinning tool, including its shape, size, and angle, plays a crucial role in the deformation behavior during ball spinning. The tool geometry affects the contact area between the tool and the metal blank, which in turn influences the material flow and forming forces. A larger contact area generally results in increased material flow and reduced forming forces, leading to improved surface finish and dimensional accuracy. However, excessively large contact areas can cause material defects such as wrinkling and thinning, as well as increased tool wear.
Table 3: Influence of Tool Geometry on Deformation Behavior
Tool Geometry | Contact Area | Material Flow | Forming Forces | Surface Finish | Dimensional Accuracy | Tool Wear | Material Defects |
---|---|---|---|---|---|---|---|
Small Ball Radius | Small | Low | High | Fair | Moderate | Low | Minimal |
Medium Ball Radius | Moderate | Moderate | Moderate | Good | High | Moderate | Minimal |
Large Ball Radius | Large | High | Low | Excellent | Very High | High | Possible |
Very Large Ball Radius | Very Large | Very High | Very Low | Excellent | Very High | Very High | Likely |
The optimal tool geometry depends on the material properties, spinning speed, and desired part dimensions. For example, harder materials such as steel alloys typically require smaller tool radii compared to softer materials such as aluminum alloys. Additionally, the tool geometry should be carefully designed to avoid material defects such as wrinkling and thinning, which can compromise the structural integrity of the spun parts.
Material Properties
The material properties of the metal blank, including its strength, ductility, and work hardening behavior, significantly influence the deformation behavior during ball spinning. Materials with higher strength and lower ductility generally require higher forming forces and are more susceptible to material defects such as cracking and wrinkling. In contrast, materials with lower strength and higher ductility are easier to form and result in improved surface finish and dimensional accuracy.
Table 4: Influence of Material Properties on Deformation Behavior
Material Property | Strength | Ductility | Work Hardening | Forming Forces | Surface Finish | Dimensional Accuracy | Material Defects |
---|---|---|---|---|---|---|---|
Aluminum Alloys | Low | High | Moderate | Low | Excellent | Very High | Minimal |
Steel Alloys | High | Low | High | High | Fair | Moderate | Possible |
Titanium Alloys | Very High | Moderate | Very High | Very High | Poor | Low | Likely |
Copper Alloys | Moderate | High | Low | Moderate | Good | High | Minimal |
The optimal material properties depend on the spinning speed, feed rate, and tool geometry. For example, aluminum alloys typically require higher spinning speeds and lower feed rates compared to steel alloys. Additionally, the material properties should be carefully selected to avoid material defects such as cracking and wrinkling, which can compromise the structural integrity of the spun parts.
Temperature
The temperature of the metal blank during ball spinning can significantly affect the deformation behavior and final quality of the spun parts. Higher temperatures generally result in reduced forming forces and improved material flow, leading to better surface finish and dimensional accuracy. However, excessively high temperatures can cause material softening, grain growth, and other microstructural changes that can compromise the mechanical properties of the spun parts.
Table 5: Influence of Temperature on Deformation Behavior
Temperature (°C) | Forming Forces | Material Flow | Surface Finish | Dimensional Accuracy | Material Defects | Microstructural Changes |
---|---|---|---|---|---|---|
Room Temperature | High | Low | Fair | Moderate | Minimal | None |
100 | Moderate | Moderate | Good | High | Minimal | Minimal |
200 | Low | High | Excellent | Very High | Possible | Moderate |
300 | Very Low | Very High | Excellent | Very High | Likely | Significant |
The optimal temperature depends on the material properties, spinning speed, and desired part dimensions. For example, aluminum alloys typically require lower temperatures compared to steel alloys due to their lower melting points and higher ductility. Additionally, the temperature should be carefully controlled to avoid material defects and microstructural changes that can compromise the mechanical properties of the spun parts.
Lubrication
Lubrication plays a crucial role in the ball spinning process by reducing friction between the spinning tool and the metal blank. Effective lubrication can significantly reduce forming forces, improve material flow, and enhance the surface finish and dimensional accuracy of the spun parts. However, inadequate lubrication can lead to increased tool wear, material defects, and poor surface finish.
Table 6: Influence of Lubrication on Deformation Behavior
Lubrication Type | Friction Reduction | Forming Forces | Material Flow | Surface Finish | Dimensional Accuracy | Tool Wear | Material Defects |
---|---|---|---|---|---|---|---|
Dry (No Lubrication) | None | Very High | Low | Poor | Low | Very High | Likely |
Mineral Oil | Moderate | Moderate | Moderate | Good | High | Moderate | Minimal |
Synthetic Oil | High | Low | High | Excellent | Very High | Low | Minimal |
Solid Lubricant | Very High | Very Low | Very High | Excellent | Very High | Very Low | None |
The optimal lubrication depends on the material properties, spinning speed, and tool geometry. For example, harder materials such as steel alloys typically require more effective lubrication compared to softer materials such as aluminum alloys. Additionally, the lubrication should be carefully selected to avoid material defects and tool wear, which can compromise the quality and precision of the spun parts.
Conclusion
The ball spinning process is a highly effective method for producing thin-walled cylindrical parts with high dimensional accuracy and excellent surface finish. The success of the process is heavily dependent on the careful control of various process parameters, including spinning speed, feed rate, tool geometry, material properties, temperature, and lubrication. Each of these parameters plays a crucial role in the deformation behavior and final quality of the spun parts, and their optimal values depend on the specific requirements of the application.
By understanding the influence of these parameters on the spinning deformation of thin-walled cylindrical parts, manufacturers can optimize the ball spinning process to achieve the desired part dimensions, surface finish, and mechanical properties. This comprehensive understanding not only enhances the efficiency and effectiveness of the manufacturing process but also ensures the production of high-quality parts that meet the stringent requirements of various industries.
In summary, the ball spinning process offers a versatile and efficient solution for the production of thin-walled cylindrical parts. Through careful control of the process parameters, manufacturers can achieve the desired deformation behavior and final quality of the spun parts, ensuring their suitability for a wide range of applications.
Maximize Tooling and CNC Metal Spinning Capabilities.
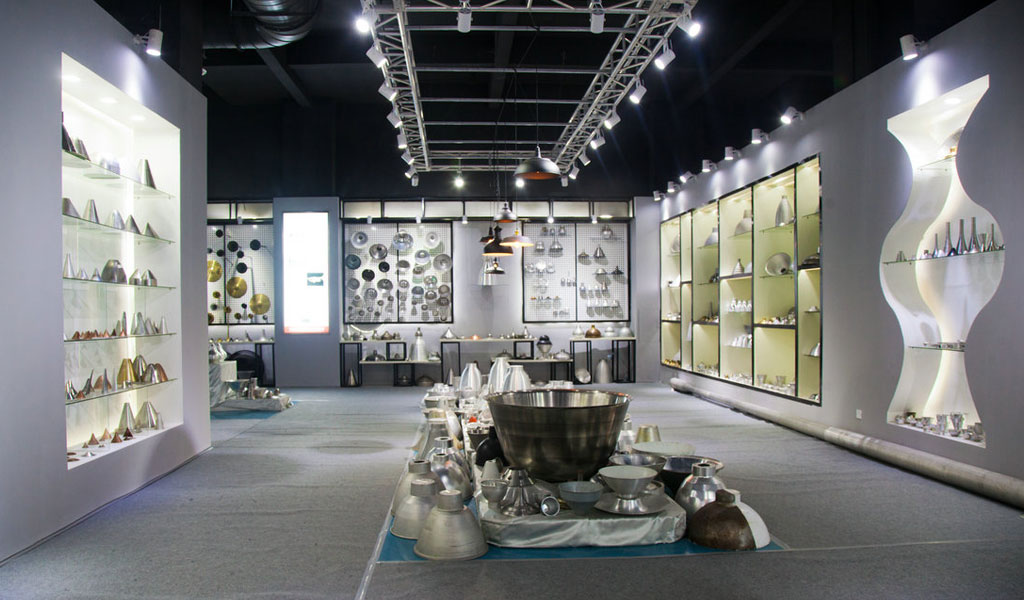
At BE-CU China Metal Spinning company, we make the most of our equipment while monitoring signs of excess wear and stress. In addition, we look into newer, modern equipment and invest in those that can support or increase our manufacturing capabilities. Our team is very mindful of our machines and tools, so we also routinely maintain them to ensure they don’t negatively impact your part’s quality and productivity.
Talk to us today about making a rapid prototype with our CNC metal spinning service. Get a direct quote by chatting with us here or request a free project review.
BE-CU China CNC Metal Spinning service include : CNC Metal Spinning,Metal Spinning Die,Laser Cutting, Tank Heads Spinning,Metal Hemispheres Spinning,Metal Cones Spinning,Metal Dish-Shaped Spinning,Metal Trumpet Spinning,Metal Venturi Spinning,Aluminum Spinning Products,Stainless Steel Spinning Products,Copper Spinning Products,Brass Spinning Products,Steel Spinning Product,Metal Spinnin LED Reflector,Metal Spinning Pressure Vessel,