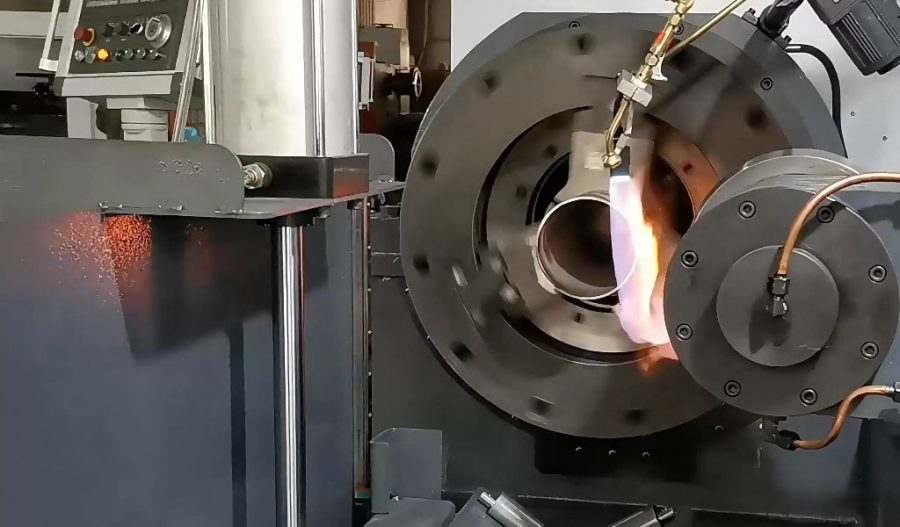
High-pressure spinning, also known as flow forming, is a metalworking process used to manufacture cylindrical parts with high precision and strength. This process involves the use of a mandrel and rollers to deform a preform (usually a thick-walled tube or a solid billet) into a thin-walled, high-precision cylindrical part. The high-pressure spinning process is widely used in industries such as aerospace, automotive, and defense, where the production of high-strength, lightweight components is crucial. The quality and efficiency of the high-pressure spinning process are significantly influenced by various process parameters, including feed rate, mandrel speed, roller pressure, and material properties. This article delves into the intricate details of how these parameters affect the high-pressure spinning process and the resulting properties of the cylindrical parts.
Feed Rate
The feed rate, which refers to the speed at which the rollers move along the axis of the mandrel, is a critical parameter in the high-pressure spinning process. The feed rate directly influences the deformation rate of the material and the overall cycle time of the process. A higher feed rate results in a faster deformation rate, which can lead to increased productivity. However, excessively high feed rates can cause excessive heat generation due to friction, leading to material failure or defects such as cracks and surface roughness.
Conversely, a lower feed rate allows for more controlled deformation, reducing the risk of material failure and improving surface finish. However, a very low feed rate can significantly increase the cycle time, reducing productivity. Therefore, optimizing the feed rate is essential to balance productivity and part quality. Research has shown that an optimal feed rate can be determined based on the material’s flow stress, the desired wall thickness, and the roller geometry. For instance, in the spinning of aluminum alloys, a feed rate of 0.5 to 1.0 mm/rev is often recommended to achieve a good balance between productivity and quality.
Mandrel Speed
The mandrel speed, or the rotational speed of the mandrel, is another crucial parameter in the high-pressure spinning process. The mandrel speed affects the material flow and the heat generated during the process. A higher mandrel speed increases the material flow rate, which can improve the surface finish and reduce the cycle time. However, excessively high mandrel speeds can cause excessive heat generation, leading to material failure or defects such as thermal softening and residual stresses.
On the other hand, a lower mandrel speed allows for more controlled material flow, reducing the risk of material failure and improving dimensional accuracy. However, a very low mandrel speed can significantly increase the cycle time, reducing productivity. Therefore, optimizing the mandrel speed is essential to balance productivity and part quality. Studies have indicated that the optimal mandrel speed depends on the material’s flow stress, the desired wall thickness, and the roller geometry. For example, in the spinning of stainless steel, a mandrel speed of 500 to 1000 rpm is often recommended to achieve a good balance between productivity and quality.
Roller Pressure
Roller pressure, which refers to the force exerted by the rollers on the material, is a critical parameter in the high-pressure spinning process. The roller pressure directly influences the deformation rate and the final wall thickness of the cylindrical part. A higher roller pressure results in a faster deformation rate and a thinner wall thickness, which can improve the strength and lightness of the part. However, excessively high roller pressures can cause material failure or defects such as cracks and surface roughness.
Conversely, a lower roller pressure allows for more controlled deformation, reducing the risk of material failure and improving surface finish. However, a very low roller pressure can result in insufficient deformation, leading to inadequate wall thickness and reduced strength. Therefore, optimizing the roller pressure is essential to achieve the desired wall thickness and part quality. Research has shown that the optimal roller pressure depends on the material’s flow stress, the desired wall thickness, and the roller geometry. For instance, in the spinning of titanium alloys, a roller pressure of 50 to 100 MPa is often recommended to achieve a good balance between wall thickness and quality.
Material Properties
The properties of the material being spun, such as flow stress, ductility, and thermal conductivity, significantly influence the high-pressure spinning process. Flow stress, which is the stress required to cause plastic deformation, affects the deformation rate and the final wall thickness. Materials with higher flow stress require higher roller pressures and mandrel speeds to achieve the desired deformation. Conversely, materials with lower flow stress can be deformed more easily, allowing for lower roller pressures and mandrel speeds.
Ductility, which is the ability of a material to deform plastically without fracturing, affects the risk of material failure during the spinning process. Materials with higher ductility can withstand more deformation without failing, allowing for higher feed rates and roller pressures. Conversely, materials with lower ductility are more prone to failure, requiring more controlled deformation and lower feed rates and roller pressures.
Thermal conductivity, which is the ability of a material to conduct heat, affects the heat generated during the spinning process. Materials with higher thermal conductivity can dissipate heat more efficiently, reducing the risk of thermal softening and residual stresses. Conversely, materials with lower thermal conductivity are more prone to heat buildup, requiring more controlled deformation and lower mandrel speeds.
Temperature Control
Temperature control is a critical aspect of the high-pressure spinning process, as it directly influences the material’s flow stress and ductility. The temperature of the material during spinning can be controlled by adjusting the mandrel speed, roller pressure, and cooling methods. A higher mandrel speed and roller pressure increase the heat generated during the process, which can improve the material’s ductility and reduce the flow stress. However, excessively high temperatures can cause thermal softening and residual stresses, leading to material failure or defects.
Conversely, a lower mandrel speed and roller pressure reduce the heat generated, allowing for more controlled deformation and improved dimensional accuracy. However, a very low temperature can increase the material’s flow stress, requiring higher roller pressures and mandrel speeds to achieve the desired deformation. Therefore, optimizing the temperature control is essential to balance material ductility and flow stress. Studies have shown that the optimal temperature depends on the material’s properties, the desired wall thickness, and the roller geometry. For example, in the spinning of aluminum alloys, a temperature range of 200 to 300°C is often recommended to achieve a good balance between ductility and flow stress.
Tool Geometry
The geometry of the tools used in the high-pressure spinning process, including the mandrel and rollers, significantly influences the deformation rate and the final wall thickness. The mandrel geometry, which includes the diameter and surface finish, affects the material flow and the final dimensions of the cylindrical part. A mandrel with a larger diameter allows for more material flow, reducing the risk of material failure and improving dimensional accuracy. However, a very large mandrel diameter can increase the cycle time, reducing productivity.
The roller geometry, which includes the diameter, width, and surface finish, affects the deformation rate and the final wall thickness. Rollers with a larger diameter and width can exert higher pressures, allowing for faster deformation and thinner wall thicknesses. However, excessively large rollers can cause material failure or defects such as cracks and surface roughness. Conversely, rollers with a smaller diameter and width allow for more controlled deformation, reducing the risk of material failure and improving surface finish. However, a very small roller diameter and width can result in insufficient deformation, leading to inadequate wall thickness and reduced strength.
Lubrication
Lubrication plays a crucial role in the high-pressure spinning process, as it reduces friction between the material and the tools, improving material flow and reducing heat generation. The type and amount of lubricant used can significantly influence the deformation rate and the final wall thickness. Common lubricants used in high-pressure spinning include oils, greases, and solid lubricants such as graphite and molybdenum disulfide.
The choice of lubricant depends on the material being spun, the desired wall thickness, and the process parameters. For example, in the spinning of aluminum alloys, oil-based lubricants are often used to achieve a good balance between material flow and heat generation. Conversely, in the spinning of titanium alloys, solid lubricants such as graphite are often used to reduce friction and improve material flow.
The amount of lubricant used is also critical, as excessively high amounts can cause material slippage, leading to inadequate deformation and reduced strength. Conversely, insufficient lubrication can increase friction, leading to material failure or defects such as surface roughness and residual stresses. Therefore, optimizing the type and amount of lubricant is essential to achieve the desired deformation and part quality.
Residual Stresses
Residual stresses, which are the stresses that remain in a material after it has been deformed, are a critical consideration in the high-pressure spinning process. Residual stresses can affect the dimensional stability, fatigue life, and overall performance of the cylindrical part. The magnitude and distribution of residual stresses depend on the process parameters, including feed rate, mandrel speed, roller pressure, and material properties.
High feed rates, mandrel speeds, and roller pressures can increase the heat generated during the process, leading to thermal softening and residual stresses. Conversely, low feed rates, mandrel speeds, and roller pressures allow for more controlled deformation, reducing the risk of residual stresses. Materials with higher ductility and thermal conductivity are less prone to residual stresses, as they can dissipate heat more efficiently and withstand more deformation without failing.
Residual stresses can be managed through various methods, including post-process heat treatment, shot peening, and stress relief annealing. Post-process heat treatment involves heating the cylindrical part to a specific temperature and holding it for a certain period to relieve residual stresses. Shot peening involves bombarding the surface of the part with small, hard particles to induce compressive residual stresses, improving fatigue life. Stress relief annealing involves heating the part to a specific temperature and slowly cooling it to relieve residual stresses.
Surface Finish
The surface finish of the cylindrical part is a critical quality attribute in the high-pressure spinning process. The surface finish affects the part’s aesthetic appeal, corrosion resistance, and fatigue life. The surface finish is influenced by various process parameters, including feed rate, mandrel speed, roller pressure, and tool geometry.
High feed rates, mandrel speeds, and roller pressures can increase the heat generated during the process, leading to surface roughness and defects. Conversely, low feed rates, mandrel speeds, and roller pressures allow for more controlled deformation, improving surface finish. The geometry of the tools, including the mandrel and rollers, also affects the surface finish. Mandrels and rollers with smooth surfaces and precise dimensions can improve material flow and reduce surface roughness.
The surface finish can be improved through various methods, including post-process polishing, honing, and coating. Post-process polishing involves using abrasive materials to smooth the surface of the part, improving its aesthetic appeal and corrosion resistance. Honing involves using abrasive stones to remove material from the surface, improving dimensional accuracy and surface finish. Coating involves applying a protective layer to the surface, improving corrosion resistance and fatigue life.
Dimensional Accuracy
Dimensional accuracy is a critical quality attribute in the high-pressure spinning process, as it affects the part’s fit, function, and overall performance. Dimensional accuracy is influenced by various process parameters, including feed rate, mandrel speed, roller pressure, and tool geometry.
High feed rates, mandrel speeds, and roller pressures can increase the heat generated during the process, leading to dimensional inaccuracies. Conversely, low feed rates, mandrel speeds, and roller pressures allow for more controlled deformation, improving dimensional accuracy. The geometry of the tools, including the mandrel and rollers, also affects dimensional accuracy. Mandrels and rollers with precise dimensions and smooth surfaces can improve material flow and reduce dimensional inaccuracies.
Dimensional accuracy can be improved through various methods, including post-process machining, honing, and heat treatment. Post-process machining involves using cutting tools to remove material from the surface, improving dimensional accuracy. Honing involves using abrasive stones to remove material from the surface, improving dimensional accuracy and surface finish. Heat treatment involves heating the part to a specific temperature and holding it for a certain period to relieve residual stresses and improve dimensional stability.
Fatigue Life
Fatigue life is a critical performance attribute in the high-pressure spinning process, as it affects the part’s durability and reliability. Fatigue life is influenced by various process parameters, including feed rate, mandrel speed, roller pressure, and material properties.
High feed rates, mandrel speeds, and roller pressures can increase the heat generated during the process, leading to residual stresses and reduced fatigue life. Conversely, low feed rates, mandrel speeds, and roller pressures allow for more controlled deformation, improving fatigue life. Materials with higher ductility and thermal conductivity are less prone to residual stresses, improving fatigue life.
Fatigue life can be improved through various methods, including post-process heat treatment, shot peening, and coating. Post-process heat treatment involves heating the part to a specific temperature and holding it for a certain period to relieve residual stresses and improve fatigue life. Shot peening involves bombarding the surface of the part with small, hard particles to induce compressive residual stresses, improving fatigue life. Coating involves applying a protective layer to the surface, improving corrosion resistance and fatigue life.
Corrosion Resistance
Corrosion resistance is a critical performance attribute in the high-pressure spinning process, as it affects the part’s durability and reliability. Corrosion resistance is influenced by various process parameters, including feed rate, mandrel speed, roller pressure, and material properties.
High feed rates, mandrel speeds, and roller pressures can increase the heat generated during the process, leading to surface roughness and reduced corrosion resistance. Conversely, low feed rates, mandrel speeds, and roller pressures allow for more controlled deformation, improving corrosion resistance. Materials with higher ductility and thermal conductivity are less prone to surface roughness, improving corrosion resistance.
Corrosion resistance can be improved through various methods, including post-process polishing, honing, and coating. Post-process polishing involves using abrasive materials to smooth the surface of the part, improving its aesthetic appeal and corrosion resistance. Honing involves using abrasive stones to remove material from the surface, improving dimensional accuracy and surface finish. Coating involves applying a protective layer to the surface, improving corrosion resistance and fatigue life.
Economic Considerations
The economic considerations of the high-pressure spinning process are crucial, as they affect the overall cost and profitability of the manufacturing process. The economic considerations include the cost of materials, tools, lubricants, and energy, as well as the cycle time and productivity.
The cost of materials is a significant economic consideration, as it affects the overall cost of the cylindrical part. The choice of material depends on the desired properties, including strength, ductility, and corrosion resistance. Common materials used in high-pressure spinning include aluminum alloys, stainless steel, and titanium alloys.
The cost of tools, including the mandrel and rollers, is another significant economic consideration. The choice of tools depends on the desired dimensions, surface finish, and dimensional accuracy. Common tools used in high-pressure spinning include mandrels with smooth surfaces and precise dimensions, and rollers with smooth surfaces and precise widths.
The cost of lubricants is a significant economic consideration, as it affects the overall cost of the cylindrical part. The choice of lubricant depends on the material being spun, the desired wall thickness, and the process parameters. Common lubricants used in high-pressure spinning include oils, greases, and solid lubricants such as graphite and molybdenum disulfide.
The cost of energy is a significant economic consideration, as it affects the overall cost of the cylindrical part. The choice of energy source depends on the process parameters, including feed rate, mandrel speed, and roller pressure. Common energy sources used in high-pressure spinning include electricity and compressed air.
The cycle time and productivity are significant economic considerations, as they affect the overall cost and profitability of the manufacturing process. The cycle time and productivity depend on the process parameters, including feed rate, mandrel speed, and roller pressure. Optimizing the process parameters can improve cycle time and productivity, reducing the overall cost and increasing profitability.
Environmental Considerations
The environmental considerations of the high-pressure spinning process are crucial, as they affect the overall sustainability and environmental impact of the manufacturing process. The environmental considerations include the use of materials, tools, lubricants, and energy, as well as the generation of waste and emissions.
The use of materials is a significant environmental consideration, as it affects the overall sustainability and environmental impact of the cylindrical part. The choice of material depends on the desired properties, including strength, ductility, and corrosion resistance. Common materials used in high-pressure spinning include aluminum alloys, stainless steel, and titanium alloys. The use of recycled materials can reduce the environmental impact and improve sustainability.
The use of tools, including the mandrel and rollers, is another significant environmental consideration. The choice of tools depends on the desired dimensions, surface finish, and dimensional accuracy. Common tools used in high-pressure spinning include mandrels with smooth surfaces and precise dimensions, and rollers with smooth surfaces and precise widths. The use of durable and recyclable tools can reduce the environmental impact and improve sustainability.
The use of lubricants is a significant environmental consideration, as it affects the overall sustainability and environmental impact of the cylindrical part. The choice of lubricant depends on the material being spun, the desired wall thickness, and the process parameters. Common lubricants used in high-pressure spinning include oils, greases, and solid lubricants such as graphite and molybdenum disulfide. The use of biodegradable and recyclable lubricants can reduce the environmental impact and improve sustainability.
The use of energy is a significant environmental consideration, as it affects the overall sustainability and environmental impact of the cylindrical part. The choice of energy source depends on the process parameters, including feed rate, mandrel speed, and roller pressure. Common energy sources used in high-pressure spinning include electricity and compressed air. The use of renewable energy sources can reduce the environmental impact and improve sustainability.
The generation of waste and emissions is a significant environmental consideration, as it affects the overall sustainability and environmental impact of the manufacturing process. The generation of waste and emissions depends on the process parameters, including feed rate, mandrel speed, and roller pressure. Optimizing the process parameters can reduce the generation of waste and emissions, improving sustainability and reducing the environmental impact.
Future Trends
The high-pressure spinning process is continually evolving, with advancements in materials, tools, and process parameters. Future trends in high-pressure spinning include the use of advanced materials, such as composites and nanomaterials, which offer improved strength, ductility, and corrosion resistance. The development of advanced tools, such as mandrels and rollers with improved surface finishes and precise dimensions, can improve material flow and reduce surface roughness.
The integration of advanced process parameters, such as adaptive control systems and real-time monitoring, can improve cycle time and productivity, reducing the overall cost and increasing profitability. The use of advanced lubricants, such as biodegradable and recyclable lubricants, can reduce the environmental impact and improve sustainability.
The application of high-pressure spinning in new industries, such as renewable energy and medical devices, can expand the market and increase the demand for cylindrical parts. The development of new manufacturing techniques, such as additive manufacturing and hybrid manufacturing, can complement high-pressure spinning, offering new possibilities for the production of complex and high-precision parts.
Conclusion
The high-pressure spinning process is a critical manufacturing technique for the production of cylindrical parts with high precision and strength. The quality and efficiency of the high-pressure spinning process are significantly influenced by various process parameters, including feed rate, mandrel speed, roller pressure, and material properties. Optimizing these parameters is essential to achieve the desired wall thickness, surface finish, dimensional accuracy, and performance attributes, such as fatigue life and corrosion resistance.
The economic and environmental considerations of the high-pressure spinning process are crucial, as they affect the overall cost, profitability, sustainability, and environmental impact of the manufacturing process. The use of advanced materials, tools, and process parameters, as well as the integration of advanced manufacturing techniques, can improve the efficiency, quality, and sustainability of the high-pressure spinning process.
The future trends in high-pressure spinning, including the use of advanced materials, tools, and process parameters, as well as the application in new industries, offer new possibilities for the production of complex and high-precision parts. The continual evolution of the high-pressure spinning process ensures its relevance and importance in the manufacturing industry, contributing to the production of high-quality and sustainable cylindrical parts.
Maximize Tooling and CNC Metal Spinning Capabilities.
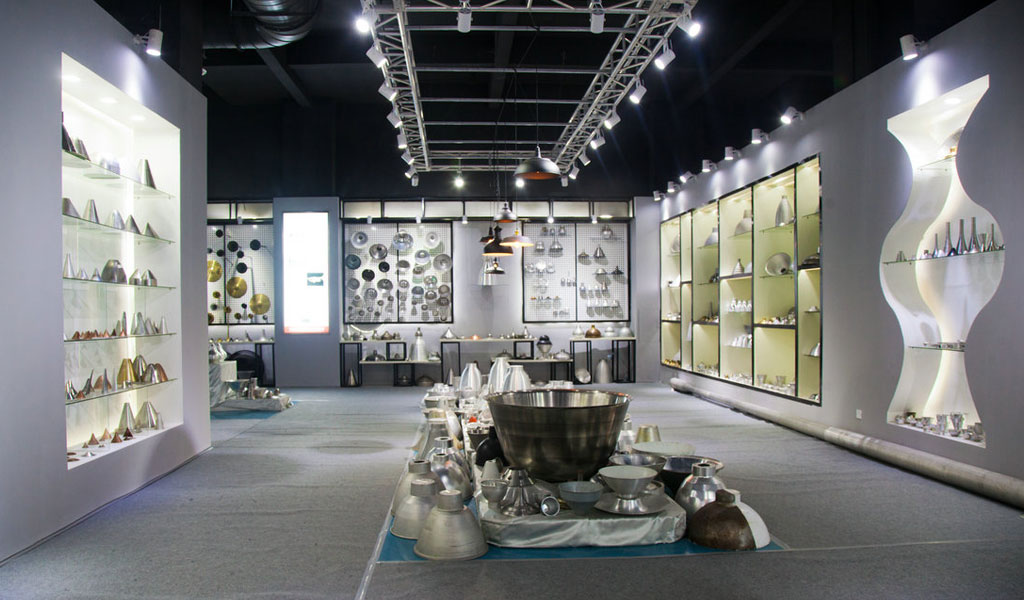
At BE-CU China Metal Spinning company, we make the most of our equipment while monitoring signs of excess wear and stress. In addition, we look into newer, modern equipment and invest in those that can support or increase our manufacturing capabilities. Our team is very mindful of our machines and tools, so we also routinely maintain them to ensure they don’t negatively impact your part’s quality and productivity.
Talk to us today about making a rapid prototype with our CNC metal spinning service. Get a direct quote by chatting with us here or request a free project review.
BE-CU China CNC Metal Spinning service include : CNC Metal Spinning,Metal Spinning Die,Laser Cutting, Tank Heads Spinning,Metal Hemispheres Spinning,Metal Cones Spinning,Metal Dish-Shaped Spinning,Metal Trumpet Spinning,Metal Venturi Spinning,Aluminum Spinning Products,Stainless Steel Spinning Products,Copper Spinning Products,Brass Spinning Products,Steel Spinning Product,Metal Spinnin LED Reflector,Metal Spinning Pressure Vessel,