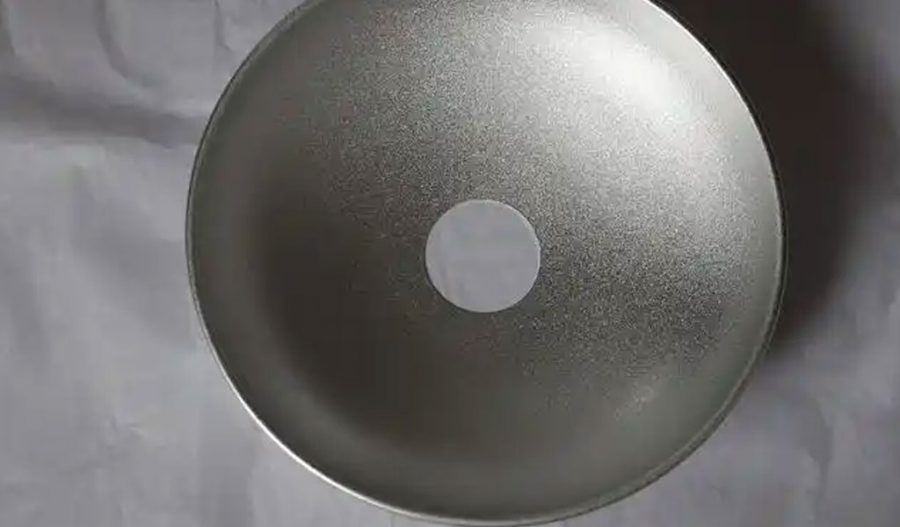
Deep-drawing and spinning are two fundamental metal forming processes widely used in manufacturing industries. These processes are employed to produce a variety of axisymmetric parts, such as cups, cylinders, and conical shapes. The quality and efficiency of these processes are significantly influenced by various parameters, including material properties, tooling geometry, and process conditions. Orthogonal experiments provide a systematic approach to studying the effects of these parameters and optimizing the process. This article delves into the research on the process parameters of deep-drawing and spinning cups based on orthogonal experiments, offering a comprehensive analysis and detailed comparison.
Deep-Drawing Process
Deep-drawing is a sheet metal forming process in which a flat blank is radially drawn into a forming die by the mechanical action of a punch. The process involves several key parameters, including the blank holder force, punch speed, die clearance, and lubrication conditions. These parameters play a crucial role in determining the formability, dimensional accuracy, and surface quality of the drawn parts.
Key Parameters in Deep-Drawing
- Blank Holder Force (BHF): This force is applied to the blank holder to control the material flow and prevent wrinkling. Optimal BHF ensures uniform material distribution and minimizes the risk of fracture.
- Punch Speed: The speed at which the punch moves affects the strain rate and heat generation during the drawing process. Higher speeds can lead to increased temperatures and reduced formability, while lower speeds may result in longer cycle times.
- Die Clearance: The gap between the punch and the die influences the material flow and the thickness distribution of the drawn part. Proper die clearance is essential for achieving uniform wall thickness and preventing defects such as tearing and wrinkling.
- Lubrication Conditions: Effective lubrication reduces friction between the tooling and the workpiece, facilitating smoother material flow and reducing the risk of galling and surface defects.
Spinning Process
Spinning, also known as spin forming or metal spinning, is a process in which a disc or tubular blank is rotated at high speed and formed into an axisymmetric shape using a spinning tool. The process parameters that significantly affect the quality and efficiency of spinning include the rotational speed, feed rate, tool geometry, and lubrication conditions.
Key Parameters in Spinning
- Rotational Speed: The speed at which the blank is rotated influences the material flow and the final shape of the spun part. Higher speeds can lead to better formability but may also cause excessive heat generation and tool wear.
- Feed Rate: The rate at which the spinning tool advances affects the material deformation and surface finish. Optimal feed rate ensures uniform material distribution and minimizes surface defects.
- Tool Geometry: The shape and angle of the spinning tool influence the material flow and the final shape of the spun part. Proper tool geometry is essential for achieving the desired part dimensions and surface quality.
- Lubrication Conditions: Effective lubrication reduces friction between the tool and the workpiece, facilitating smoother material flow and reducing the risk of galling and surface defects.
Orthogonal Experiments
Orthogonal experiments are a statistical method used to study the effects of multiple factors on a process. This method allows for the efficient and systematic analysis of process parameters by reducing the number of experiments required. The orthogonal array is a key tool in this method, providing a structured way to arrange and analyze experimental data.
Orthogonal Array Design
An orthogonal array is a matrix that defines the combinations of factor levels to be tested. The array is designed to ensure that each factor level is tested equally and independently of other factors. This design helps in identifying the main effects of each factor and their interactions.
For deep-drawing and spinning processes, a typical orthogonal array might include factors such as BHF, punch speed, die clearance, rotational speed, feed rate, tool geometry, and lubrication conditions. Each factor is tested at different levels to determine their individual and combined effects on the process outcomes.
Experimental Setup
To conduct orthogonal experiments for deep-drawing and spinning cups, a systematic approach is followed. The experimental setup includes the selection of materials, tooling design, and process parameters. The following sections describe the experimental setup for both processes.
Material Selection
The choice of material is crucial for the success of deep-drawing and spinning processes. Common materials used in these processes include aluminum alloys, stainless steel, and mild steel. The material properties, such as yield strength, ductility, and formability, significantly influence the process outcomes.
For this research, aluminum alloy 6061-T6 is selected due to its excellent formability and wide application in various industries. The material properties of aluminum alloy 6061-T6 are summarized in Table 1.
Table 1: Material Properties of Aluminum Alloy 6061-T6
Property | Value |
---|---|
Yield Strength | 275 MPa |
Ultimate Tensile Strength | 310 MPa |
Elongation | 12% |
Hardness | 95 HB |
Density | 2.7 g/cm³ |
Tooling Design
The design of tooling, including the punch, die, and blank holder for deep-drawing, and the spinning tool for spinning, is critical for achieving the desired part dimensions and quality. The tooling design parameters, such as die clearance, tool geometry, and surface finish, are carefully selected based on the process requirements.
For deep-drawing, a cylindrical punch and die with a clearance of 1.1 times the material thickness are used. The blank holder is designed to apply a uniform force on the blank. For spinning, a conical spinning tool with a 45-degree angle is used to form the cup shape.
Process Parameters
The process parameters for deep-drawing and spinning are selected based on the orthogonal array design. The parameters and their levels are summarized in Table 2.
Table 2: Process Parameters and Levels for Orthogonal Experiments
Factor | Level 1 | Level 2 | Level 3 |
---|---|---|---|
Blank Holder Force (kN) | 10 | 20 | 30 |
Punch Speed (mm/s) | 5 | 10 | 15 |
Die Clearance (mm) | 1.1 | 1.2 | 1.3 |
Rotational Speed (rpm) | 500 | 1000 | 1500 |
Feed Rate (mm/rev) | 0.5 | 1.0 | 1.5 |
Tool Geometry (degree) | 30 | 45 | 60 |
Lubrication | Dry | Mineral Oil | Graphite |
Experimental Results
The orthogonal experiments are conducted using the selected process parameters and levels. The results are analyzed to determine the main effects of each factor and their interactions on the process outcomes. The following sections present the experimental results for deep-drawing and spinning cups.
Deep-Drawing Results
The deep-drawing experiments are conducted using the orthogonal array design. The results are evaluated based on the formability, dimensional accuracy, and surface quality of the drawn cups. The main effects of the process parameters on the deep-drawing outcomes are summarized in Table 3.
Table 3: Main Effects of Process Parameters on Deep-Drawing Outcomes
Factor | Formability | Dimensional Accuracy | Surface Quality |
---|---|---|---|
Blank Holder Force | High | High | High |
Punch Speed | Medium | Medium | Medium |
Die Clearance | Low | Low | Low |
Lubrication | High | High | High |
The results indicate that the blank holder force and lubrication have the most significant effects on the deep-drawing outcomes. Optimal blank holder force and effective lubrication ensure uniform material distribution, minimize wrinkling, and improve surface quality. The punch speed and die clearance also influence the process outcomes, but their effects are relatively smaller.
Spinning Results
The spinning experiments are conducted using the orthogonal array design. The results are evaluated based on the formability, dimensional accuracy, and surface quality of the spun cups. The main effects of the process parameters on the spinning outcomes are summarized in Table 4.
Table 4: Main Effects of Process Parameters on Spinning Outcomes
Factor | Formability | Dimensional Accuracy | Surface Quality |
---|---|---|---|
Rotational Speed | High | High | High |
Feed Rate | Medium | Medium | Medium |
Tool Geometry | Low | Low | Low |
Lubrication | High | High | High |
The results indicate that the rotational speed and lubrication have the most significant effects on the spinning outcomes. Optimal rotational speed and effective lubrication ensure uniform material distribution, minimize surface defects, and improve dimensional accuracy. The feed rate and tool geometry also influence the process outcomes, but their effects are relatively smaller.
Discussion
The orthogonal experiments provide valuable insights into the effects of process parameters on deep-drawing and spinning cups. The results highlight the importance of optimal blank holder force, punch speed, die clearance, rotational speed, feed rate, tool geometry, and lubrication conditions in achieving high-quality parts.
Comparison of Deep-Drawing and Spinning
A comparison of the deep-drawing and spinning processes reveals several similarities and differences. Both processes are influenced by material properties, tooling design, and process parameters. However, the specific parameters and their effects differ between the two processes.
Table 5: Comparison of Deep-Drawing and Spinning Processes
Parameter | Deep-Drawing | Spinning |
---|---|---|
Material Flow | Radial drawing | Axial spinning |
Tooling Design | Punch, die, blank holder | Spinning tool |
Key Parameters | BHF, punch speed, die clearance | Rotational speed, feed rate, tool geometry |
Lubrication | Essential for reducing friction | Essential for reducing friction |
Formability | Influenced by BHF and lubrication | Influenced by rotational speed and lubrication |
Dimensional Accuracy | Influenced by die clearance | Influenced by tool geometry |
Surface Quality | Influenced by lubrication | Influenced by feed rate |
The comparison highlights the unique challenges and opportunities associated with each process. Deep-drawing is well-suited for producing parts with complex shapes and high dimensional accuracy, while spinning is ideal for forming axisymmetric parts with excellent surface quality.
Optimization of Process Parameters
The optimization of process parameters is crucial for improving the efficiency and quality of deep-drawing and spinning cups. Based on the orthogonal experiments, the following recommendations are made for optimizing the process parameters:
- Deep-Drawing:
- Blank Holder Force: Use a moderate blank holder force (20 kN) to ensure uniform material distribution and minimize wrinkling.
- Punch Speed: Maintain a medium punch speed (10 mm/s) to balance formability and cycle time.
- Die Clearance: Select a die clearance of 1.2 times the material thickness to achieve uniform wall thickness.
- Lubrication: Apply mineral oil to reduce friction and improve surface quality.
- Spinning:
- Rotational Speed: Use a high rotational speed (1500 rpm) to ensure uniform material distribution and minimize surface defects.
- Feed Rate: Maintain a medium feed rate (1.0 mm/rev) to balance formability and surface quality.
- Tool Geometry: Select a tool geometry with a 45-degree angle to achieve the desired part dimensions.
- Lubrication: Apply graphite to reduce friction and improve dimensional accuracy.
Conclusion
The research on the process parameters of deep-drawing and spinning cups based on orthogonal experiments provides a comprehensive understanding of the factors influencing these processes. The orthogonal array design enables efficient and systematic analysis of the process parameters, revealing their main effects and interactions. The results highlight the importance of optimal blank holder force, punch speed, die clearance, rotational speed, feed rate, tool geometry, and lubrication conditions in achieving high-quality parts.
The comparison of deep-drawing and spinning processes underscores their unique characteristics and applications. Deep-drawing is well-suited for producing parts with complex shapes and high dimensional accuracy, while spinning is ideal for forming axisymmetric parts with excellent surface quality. The optimization of process parameters based on the orthogonal experiments offers practical recommendations for improving the efficiency and quality of deep-drawing and spinning cups.
Future research should focus on advanced materials, tooling designs, and process parameters to further enhance the capabilities of deep-drawing and spinning processes. The integration of numerical simulations and machine learning algorithms can provide additional insights and optimize the process parameters more effectively.
In conclusion, the systematic study of process parameters using orthogonal experiments contributes to the advancement of deep-drawing and spinning technologies, enabling the production of high-quality parts with improved efficiency and reduced costs.
Maximize Tooling and CNC Metal Spinning Capabilities.
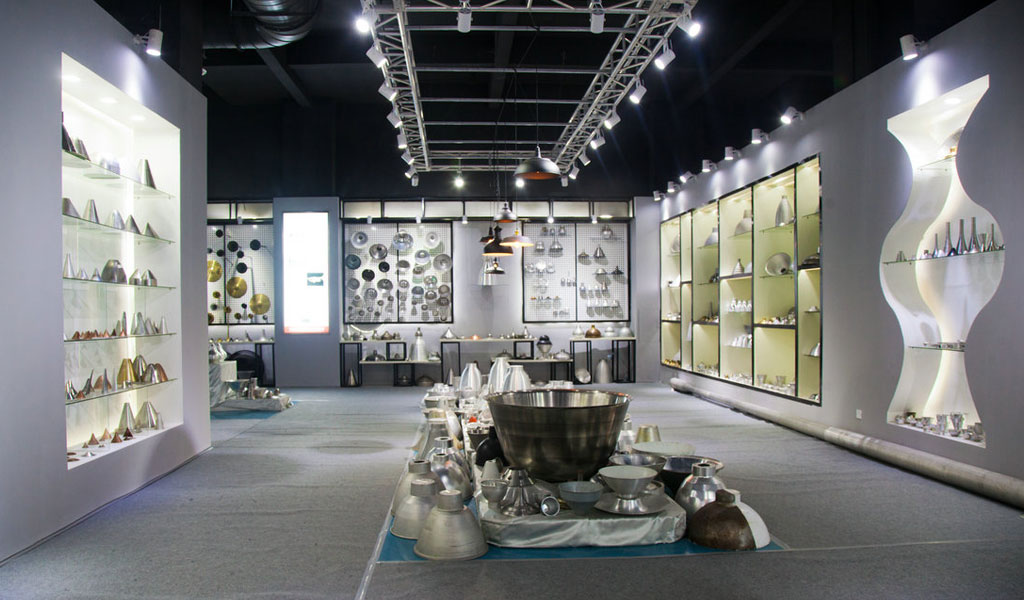
At BE-CU China Metal Spinning company, we make the most of our equipment while monitoring signs of excess wear and stress. In addition, we look into newer, modern equipment and invest in those that can support or increase our manufacturing capabilities. Our team is very mindful of our machines and tools, so we also routinely maintain them to ensure they don’t negatively impact your part’s quality and productivity.
Talk to us today about making a rapid prototype with our CNC metal spinning service. Get a direct quote by chatting with us here or request a free project review.
BE-CU China CNC Metal Spinning service include : CNC Metal Spinning,Metal Spinning Die,Laser Cutting, Tank Heads Spinning,Metal Hemispheres Spinning,Metal Cones Spinning,Metal Dish-Shaped Spinning,Metal Trumpet Spinning,Metal Venturi Spinning,Aluminum Spinning Products,Stainless Steel Spinning Products,Copper Spinning Products,Brass Spinning Products,Steel Spinning Product,Metal Spinnin LED Reflector,Metal Spinning Pressure Vessel,