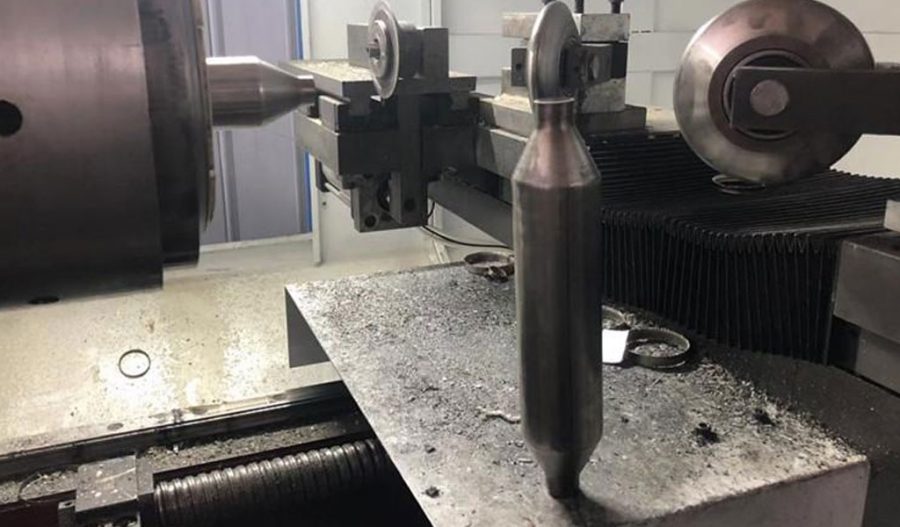
The U-shaped cross-section annular cavity spinning device represents a significant advancement in the field of textile manufacturing, particularly in the realm of spinning. This innovative device is designed to enhance the efficiency and quality of yarn production, addressing several challenges faced by traditional spinning methods. The following article delves into the intricacies of this device, its operational principles, advantages, and comparisons with other spinning technologies.
Introduction to Spinning
Spinning is a critical process in the textile industry, involving the conversion of fibers into yarn. Traditional spinning methods, such as ring spinning and rotor spinning, have been the backbone of yarn production for decades. However, these methods have limitations in terms of productivity, yarn quality, and energy consumption. The U-shaped cross-section annular cavity spinning device aims to overcome these limitations by introducing a novel approach to yarn formation.
Design and Operational Principles
The U-shaped cross-section annular cavity spinning device is characterized by its unique geometry, which plays a pivotal role in its functionality. The device consists of a U-shaped cavity that serves as the spinning chamber. This cavity is designed to create a controlled environment for fiber alignment and yarn formation. The key components of the device include:
- Fiber Feeding System: This system ensures a consistent supply of fibers to the spinning chamber. It is equipped with precision controls to maintain the optimal fiber density and orientation.
- Spinning Chamber: The U-shaped cavity acts as the spinning chamber, where fibers are aligned and twisted to form yarn. The chamber’s design facilitates uniform airflow, which is crucial for fiber alignment.
- Airflow Control System: This system regulates the airflow within the spinning chamber, ensuring that fibers are evenly distributed and aligned. The controlled airflow helps in achieving consistent yarn quality.
- Yarn Extraction Mechanism: Once the yarn is formed, it is extracted from the spinning chamber through a controlled process. This mechanism ensures that the yarn maintains its integrity and quality during extraction.
Advantages of the U-Shaped Cross-Section Annular Cavity Spinning Device
The U-shaped cross-section annular cavity spinning device offers several advantages over traditional spinning methods. These advantages include:
- Improved Yarn Quality: The controlled environment within the spinning chamber ensures that fibers are aligned and twisted uniformly, resulting in higher yarn quality.
- Increased Productivity: The device’s efficient design allows for higher spinning speeds, leading to increased productivity. This is particularly beneficial in large-scale textile manufacturing.
- Energy Efficiency: The optimized airflow control system reduces energy consumption, making the device more cost-effective compared to traditional spinning methods.
- Versatility: The device can handle a variety of fiber types, including natural and synthetic fibers. This versatility makes it suitable for a wide range of textile applications.
- Reduced Waste: The precise control over fiber alignment and yarn formation minimizes waste, contributing to a more sustainable manufacturing process.
Comparison with Other Spinning Technologies
To understand the unique benefits of the U-shaped cross-section annular cavity spinning device, it is essential to compare it with other spinning technologies. The following table provides a detailed comparison:
Feature | Ring Spinning | Rotor Spinning | Air-Jet Spinning | U-Shaped Annular Cavity Spinning |
---|---|---|---|---|
Yarn Quality | High | Moderate | Moderate | High |
Productivity | Low to Moderate | High | High | Very High |
Energy Consumption | High | Moderate | Low | Low |
Fiber Versatility | Limited | Moderate | High | Very High |
Waste Generation | Moderate | High | Low | Very Low |
Maintenance | High | Moderate | Low | Low |
Cost | High | Moderate | Moderate | Moderate |
Detailed Analysis of Spinning Technologies
- Ring Spinning:
- Yarn Quality: Ring spinning produces high-quality yarn due to its precise control over fiber alignment and twisting.
- Productivity: The productivity is relatively low due to the mechanical limitations of the ring and traveler system.
- Energy Consumption: High energy consumption is a significant drawback, making it less cost-effective.
- Fiber Versatility: Limited to certain types of fibers, primarily natural fibers like cotton and wool.
- Waste Generation: Moderate waste generation due to the mechanical nature of the process.
- Maintenance: Requires frequent maintenance, leading to higher operational costs.
- Cost: High initial and operational costs.
- Rotor Spinning:
- Yarn Quality: Moderate yarn quality, suitable for coarser yarns.
- Productivity: High productivity due to the continuous spinning process.
- Energy Consumption: Moderate energy consumption, more efficient than ring spinning.
- Fiber Versatility: Moderate versatility, can handle a wider range of fibers compared to ring spinning.
- Waste Generation: High waste generation due to the nature of the rotor spinning process.
- Maintenance: Moderate maintenance requirements.
- Cost: Moderate initial and operational costs.
- Air-Jet Spinning:
- Yarn Quality: Moderate yarn quality, suitable for fine to medium yarns.
- Productivity: High productivity due to the efficient air-jet mechanism.
- Energy Consumption: Low energy consumption, making it more cost-effective.
- Fiber Versatility: High versatility, can handle a wide range of fibers.
- Waste Generation: Low waste generation due to the efficient use of fibers.
- Maintenance: Low maintenance requirements.
- Cost: Moderate initial and operational costs.
- U-Shaped Annular Cavity Spinning:
- Yarn Quality: High yarn quality due to the controlled environment and precise fiber alignment.
- Productivity: Very high productivity due to the efficient design and controlled airflow.
- Energy Consumption: Low energy consumption, making it highly cost-effective.
- Fiber Versatility: Very high versatility, can handle a wide range of natural and synthetic fibers.
- Waste Generation: Very low waste generation due to the precise control over fiber alignment and yarn formation.
- Maintenance: Low maintenance requirements.
- Cost: Moderate initial and operational costs.
Scientific Principles Behind the U-Shaped Annular Cavity Spinning Device
The scientific principles behind the U-shaped annular cavity spinning device are rooted in fluid dynamics and fiber mechanics. The key principles include:
- Fluid Dynamics: The controlled airflow within the spinning chamber is governed by the principles of fluid dynamics. The design of the U-shaped cavity ensures uniform airflow, which is crucial for fiber alignment and yarn formation. The airflow creates a vortex that helps in twisting the fibers into yarn.
- Fiber Mechanics: The mechanical properties of fibers, such as tensile strength and elasticity, play a significant role in yarn formation. The device’s design ensures that fibers are aligned and twisted in a manner that maximizes their mechanical properties, resulting in high-quality yarn.
- Thermodynamics: The energy efficiency of the device is governed by the principles of thermodynamics. The optimized airflow control system minimizes energy loss, making the device more cost-effective.
Applications and Future Prospects
The U-shaped cross-section annular cavity spinning device has a wide range of applications in the textile industry. Its versatility and efficiency make it suitable for various types of yarn production, including:
- Cotton Yarn: The device can produce high-quality cotton yarn, suitable for a variety of textile applications.
- Wool Yarn: The controlled environment within the spinning chamber makes it ideal for producing wool yarn, which requires precise fiber alignment.
- Synthetic Yarn: The device’s versatility allows it to handle synthetic fibers, such as polyester and nylon, making it suitable for a wide range of textile products.
- Blended Yarn: The device can produce blended yarns, combining different types of fibers to achieve desired properties.
The future prospects of the U-shaped cross-section annular cavity spinning device are promising. With advancements in technology and materials, the device can be further optimized for even higher productivity and energy efficiency. Research and development in this area are likely to focus on:
- Material Innovations: Developing new materials for the spinning chamber and airflow control system to enhance durability and efficiency.
- Automation: Incorporating advanced automation technologies to further streamline the spinning process and reduce human intervention.
- Sustainability: Exploring sustainable practices, such as the use of recycled fibers and renewable energy sources, to make the spinning process more environmentally friendly.
Conclusion
The U-shaped cross-section annular cavity spinning device represents a significant advancement in the field of textile manufacturing. Its unique design and operational principles offer numerous advantages over traditional spinning methods, including improved yarn quality, increased productivity, energy efficiency, versatility, and reduced waste. As the textile industry continues to evolve, the adoption of such innovative technologies will be crucial for meeting the growing demand for high-quality textile products while ensuring sustainability and cost-effectiveness. The future of spinning lies in the integration of advanced technologies and scientific principles, paving the way for a more efficient and sustainable textile industry.
Maximize Tooling and CNC Metal Spinning Capabilities.
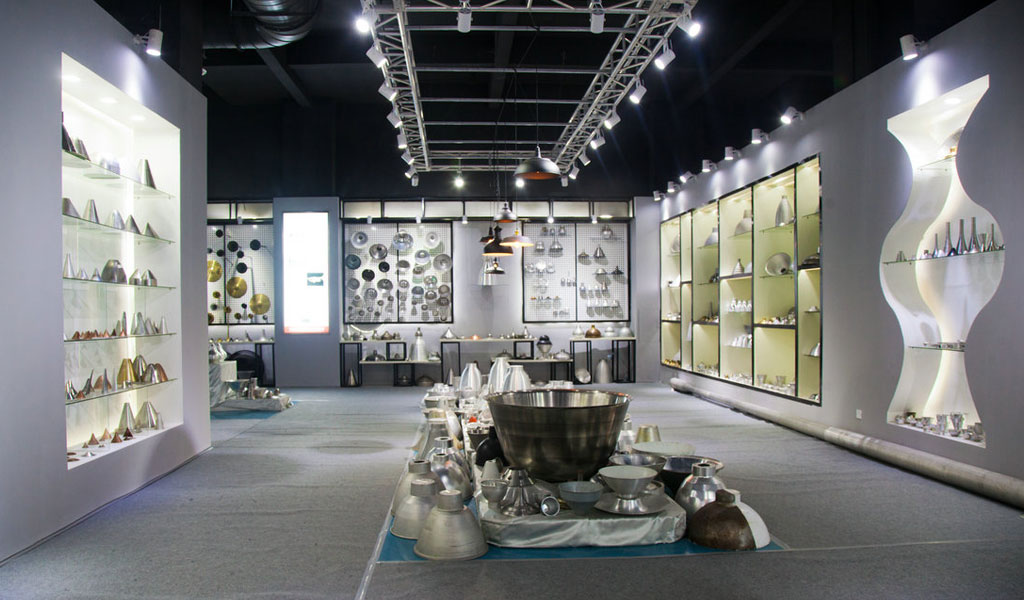
At BE-CU China Metal Spinning company, we make the most of our equipment while monitoring signs of excess wear and stress. In addition, we look into newer, modern equipment and invest in those that can support or increase our manufacturing capabilities. Our team is very mindful of our machines and tools, so we also routinely maintain them to ensure they don’t negatively impact your part’s quality and productivity.
Talk to us today about making a rapid prototype with our CNC metal spinning service. Get a direct quote by chatting with us here or request a free project review.
BE-CU China CNC Metal Spinning service include : CNC Metal Spinning,Metal Spinning Die,Laser Cutting, Tank Heads Spinning,Metal Hemispheres Spinning,Metal Cones Spinning,Metal Dish-Shaped Spinning,Metal Trumpet Spinning,Metal Venturi Spinning,Aluminum Spinning Products,Stainless Steel Spinning Products,Copper Spinning Products,Brass Spinning Products,Steel Spinning Product,Metal Spinnin LED Reflector,Metal Spinning Pressure Vessel,